Building a Stronger Tomorrow: Road Breaking, Rotary Drilling, Rolling, and TBM Tips Buttons Explained
From towering skyscrapers to intricate underground tunnels, construction projects demand tools and materials that can withstand immense pressure and relentless wear. Tungsten carbide buttons have emerged as indispensable components in this demanding industry, offering unparalleled hardness and durability. This guide delves into four key types of carbide buttons—road breaking, rotary drilling, rolling, and TBM tips—unveiling their unique characteristics and how they contribute to building a stronger, more resilient future.
Why Tungsten Carbide Buttons Are the Backbone of Construction
Beyond Ordinary Wear Parts: Understanding the Value Proposition
- Exceptional Hardness: Tungsten carbide, a composite material renowned for its extreme hardness, forms the core of these tungsten carbide buttons, enabling them to resist wear and tear even under the most demanding construction conditions.
- Impact and Abrasion Resistance: Construction sites are rife with impact, shock, and abrasive forces. Tungsten carbide buttons are engineered to withstand these challenges, ensuring longevity and minimizing downtime.
- Versatility in Application: From breaking through solid rock to drilling precise holes, each type of tungsten carbide button is specifically designed to excel in its respective application, optimizing efficiency and performance.
Decoding the Designs: Road Breaking, Rotary Drilling, Rolling, and TBM Tips Buttons
Shape and Function: How Design Influences Performance
1. Road Breaking Buttons:
- Characteristics: These tungsten carbide buttons typically feature a robust, blunt, or hemispherical shape designed to withstand high-impact forces.
- Advantages: Excel in breaking and crushing concrete, asphalt, and rock during demolition and road construction projects.
- Ideal For: Hydraulic breakers, impact hammers, and other heavy-duty demolition equipment.
2. Rotary Drilling Buttons:
- Characteristics: These tungsten carbide buttons come in various shapes, including conical, parabolic, and chisel-shaped, optimized for efficient drilling.
- Advantages: Provide fast drilling rates and precise hole formation in a range of materials, including rock, concrete, and asphalt.
- Ideal For: Drilling rigs, core drilling machines, and other rotary drilling applications.
3. Rolling Buttons:
- Characteristics: These tungsten carbide buttons feature a smooth, spherical surface designed for rolling and crushing action.
- Advantages: Provide excellent wear resistance in applications involving grinding, milling, and crushing of construction materials.
- Ideal For: Ball mills, rod mills, and other material processing equipment.
4. TBM Tips Buttons:
- Characteristics: These tungsten carbide buttons are specifically designed for use in Tunnel Boring Machines (TBMs), often featuring complex geometries and cutting edges.
- Advantages: Offer a balance of penetration, wear resistance, and durability for efficient tunnel excavation in various ground conditions.
- Ideal For: Tunnel boring machines used in infrastructure projects, mining, and other underground construction applications.
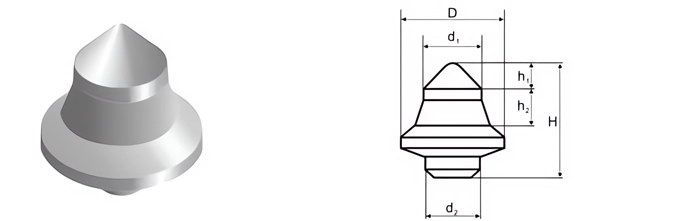
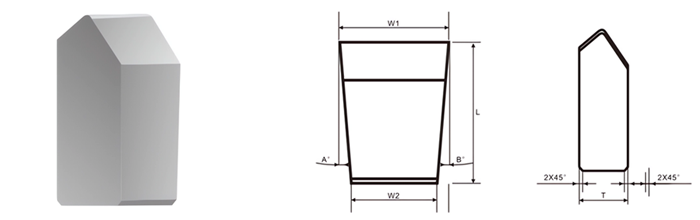
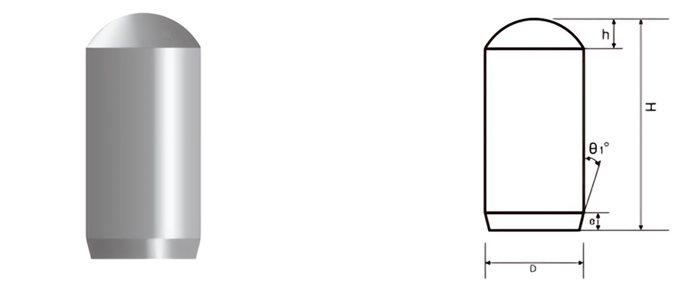
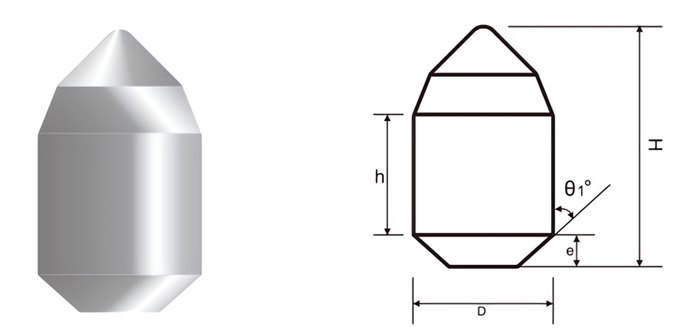
Technical Specifications: A Comparative Look at Button Properties
From Composition to Standards: Key Data Points
Feature | Road Breaking Buttons | Rotary Drilling Buttons | Rolling Buttons | TBM Tips Buttons |
---|---|---|---|---|
Type | Road Breaking | Rotary Drilling | Rolling | TBM Tips |
Composition | Tungsten Carbide (WC) with Cobalt (Co) or Nickel (Ni) binder | Tungsten Carbide (WC) with Cobalt (Co) or Nickel (Ni) binder | Tungsten Carbide (WC) with Cobalt (Co) or Nickel (Ni) binder | Tungsten Carbide (WC) with Cobalt (Co) or Nickel (Ni) binder |
Hardness (HV30) | 1400 – 1800 | 1500 – 1900 | 1450 – 1850 | 1600 – 2000 |
Transverse Rupture Strength (N/mm²) | 1800 – 2500 | 1900 – 2600 | 1850 – 2550 | 2000 – 2800 |
Impact Resistance | Excellent | Very Good | Good | Excellent |
Wear Resistance | Excellent in high-impact applications | Very good in penetration and cutting applications | Good balance of wear and penetration resistance | Excellent in abrasive and high-pressure environments |
Sizes and Shapes | Various diameters and shapes available | Various diameters, tip angles, and geometries available | Various diameters available | Customized shapes and sizes based on TBM design |
Grades and Standards | Meet ISO, ASTM, and other relevant industry standards | Meet ISO, ASTM, and other relevant industry standards | Meet ISO, ASTM, and other relevant industry standards | Meet ISO, ASTM, and other relevant industry standards |
Applications in Construction: Where Each Button Type Shines
From Demolition to Tunnel Boring: A Range of Use Cases
- Demolition and Road Construction: Road breaking buttons are essential for breaking concrete structures, asphalt pavements, and rock during demolition and road construction projects.
- Foundation Drilling: Rotary drilling buttons are used in foundation drilling rigs to create holes for piles, piers, and other foundation elements.
- Material Processing: Rolling buttons are used in ball mills and other grinding equipment to crush and process aggregates, cement, and other construction materials.
- Tunnel Excavation: TBM tips buttons play a critical role in tunnel boring machines, excavating tunnels for transportation, water management, and other infrastructure projects.
Comparative Analysis: TRUER vs. Industry Leaders
Navigating the Market: A Side-by-Side Comparison
Supplier | Country | Price Range (per piece) | Specialties |
---|---|---|---|
TRUER | China | $12 – $60+ | Custom-engineered solutions, rapid prototyping, exceptional customer support |
Element Six | UK | $18 – $75+ | Advanced material science, high-performance carbide grades for extreme wear applications |
Kennametal | USA | $15 – $65+ | Wide range of standard and custom button designs, extensive industry experience |
Sandvik Coromant | Sweden | $16 – $80+ | Innovative tooling solutions, focus on sustainability and performance optimization |
Note: Prices are approximate and can vary significantly based on button size, geometry, grade, quantity, and other factors.If you want to purchase affordable, corrosion-resistant and durable carbide buttons, click here.
Advantages and Limitations: Weighing the Trade-offs
Making Informed Decisions: A Balanced View of Each Button Type
Button Type | Advantages | Limitations |
---|---|---|
Road Breaking | – Exceptional impact resistance<br> – Effective for breaking hard materials like concrete and rock | – Not suitable for precision drilling or cutting<br> – Can generate significant noise and vibration |
Rotary Drilling | – Fast drilling rates<br> – Precise hole formation | – Can wear down quickly in extremely hard or abrasive formations<br> – Button selection critical for optimal performance |
Rolling | – Excellent wear resistance in grinding and crushing applications<br> – Contributes to efficient material processing | – Not suitable for cutting or drilling applications<br> – Button size and hardness must be matched to the material being processed |
TBM Tips | – High penetration rates in various ground conditions<br> – Designed for continuous operation in demanding tunneling environments | – Can be expensive due to complex designs and specialized materials<br> – Button replacement can be time-consuming |
Beyond the Basics: Factors Influencing Button Performance and Longevity
Maximizing ROI: Key Considerations
- Material Selection: Choosing the right carbide grade is crucial, considering the hardness of the material being worked on, impact resistance requirements, and potential abrasive wear.
- Button Attachment: Proper brazing or welding techniques are essential for a secure bond between the button and the tool, preventing premature button loss.
- Operating Conditions: Factors like temperature, pressure, and the presence of water or other fluids can impact button performance and lifespan.
Why Choose TRUER?
Your Partner in Construction Efficiency:
TRUER goes beyond supplying tungsten carbide buttons. We are your dedicated partner in optimizing construction operations. Here’s why industry leaders choose TRUER:
- Uncompromising Quality: We source the highest-grade tungsten carbide and employ rigorous quality control measures throughout our manufacturing process.
- Customization Expertise: Our team of engineers thrives on developing innovative, custom-engineered tungsten carbide button solutions tailored to your unique construction challenges.
- Rapid Prototyping and Production: We understand the critical role of speed in the construction industry. Our agile processes enable us to deliver prototypes and production runs efficiently.
- Exceptional Customer Support: We’re with you every step of the way, providing expert technical guidance and support to ensure your success.
Frequently Asked Questions: Addressing Your Construction Button Queries
1. How do I determine the best tungsten carbide button type for my specific construction application?
The optimal tungsten carbide button type depends on factors like the material being worked on, the type of equipment used, and the desired balance between penetration and wear resistance. Consulting with our technical experts is recommended for personalized guidance.
2. What are the typical wear patterns observed in different button types, and how can I identify when replacement is needed?
Wear patterns vary depending on the button type and operating conditions. Common signs of wear include flattening or chipping of road breaking buttons, blunting or breakage of rotary drilling buttons, and general erosion of the button surface. Regular inspection and replacement based on established wear limits are crucial.
3. Can TRUER provide tungsten carbide buttons with specialized coatings for enhanced wear or corrosion resistance in demanding construction environments?
Yes, we offer a range of surface treatments and coatings that can further enhance the performance and longevity of our tungsten carbide buttons in the presence of abrasive materials, corrosive agents, and other challenging conditions.
4. What is the typical lead time for ordering custom tungsten carbide buttons from TRUER?
Lead times for custom orders vary depending on the complexity of the design and the quantity required. Contact our sales team for a personalized quote and lead time estimate.
5. Does TRUER offer on-site technical support or training related to the use and maintenance of your tungsten carbide buttons in construction applications?
We provide comprehensive technical support, including on-site consultations, training programs, and troubleshooting assistance, to ensure you get the most out of our products and optimize your construction operations.