In the world of high-precision machining, where tolerances are measured in microns and performance is paramount, solid carbide rods reign supreme. These engineered marvels, crafted from incredibly hard and wear-resistant tungsten carbide, form the backbone of countless cutting tools and wear parts that drive industries ranging from aerospace to medical.
But not all carbide rods are created equal. This comprehensive guide delves into the intricacies of four essential solid carbide rod types, each with unique features and advantages tailored to specific machining challenges:
- Straight Coolant Hole Carbide Rod
- 2 Straight Coolant Holes Carbide Rod
- 2 Helical Coolant Holes Carbide Rod
- End Chamfered Ground Carbide Rod
From understanding their distinct characteristics to exploring their diverse applications, this guide equips you with the knowledge to navigate the world of solid carbide rods and select the perfect type for your precision machining needs.
Overview: The Power of Precision in Your Hands
Solid carbide rods, unlike their steel counterparts, retain their hardness and strength even at extreme temperatures, making them ideal for high-speed machining operations where heat generation is a concern. Their exceptional wear resistance translates to longer tool life, reduced downtime, and ultimately, lower manufacturing costs.
The addition of coolant holes and other features further enhances their performance, enabling efficient chip evacuation, improved heat dissipation, and increased cutting speeds, pushing the boundaries of what’s possible in precision machining.
Detailed Introduction: Exploring the World of Solid Carbide Rods
What is a Solid Carbide Rod?
A solid carbide rod, as the name suggests, is a cylindrical rod made entirely of tungsten carbide, a cemented carbide material known for its exceptional hardness and wear resistance. These rods serve as the starting material for manufacturing a wide range of cutting tools and wear parts used in various industries.
Working Principle of Carbide Rods in Machining
Carbide rods, when machined into cutting tools, function based on the principle of shear deformation. The incredibly hard cutting edges of carbide tools, formed from the rod material, are able to cut through workpieces by exceeding the material’s shear strength. The geometry of the cutting tool, along with its cutting parameters, determines the efficiency and quality of the cut.
How are Solid Carbide Rods Used?
Solid carbide rods are typically machined into various cutting tools, including:
- End Mills: For shaping and profiling operations.
- Drills: For creating holes in various materials.
- Reamers: For enlarging and finishing existing holes.
- Custom Tools: Tailored to specific machining requirements.
How are Solid Carbide Rods Machined?
Machining carbide rods requires specialized equipment and techniques due to their extreme hardness. Diamond grinding wheels are commonly employed for shaping and finishing carbide rods. Precision grinding machines, often CNC-controlled, are used to achieve the tight tolerances and intricate geometries required for high-performance cutting tools.
Classifications and Types of Solid Carbide Rods
Solid carbide rods are categorized based on various factors, including:
- Carbide Grade: Determines the hardness, toughness, and wear resistance of the rod.
- Diameter and Length: Available in a wide range of standard and custom sizes.
- Coolant Hole Configuration: Straight, helical, or no coolant holes.
- Surface Finish: Ground, polished, or coated.
Market Trends in Solid Carbide Rods
The global demand for solid carbide rods is on the rise, driven by the increasing adoption of advanced manufacturing technologies, particularly in industries such as aerospace, automotive, and medical. The market is characterized by intense competition, with manufacturers constantly innovating to develop new carbide grades and tool designs that offer enhanced performance and cost-effectiveness.
Unveiling the 4 Essential Solid Carbide Rod Types: A Comparative Analysis
Feature | Solid Carbide Rod | 1 Straight Coolant Hole | 2 Straight Coolant Holes | 2 Helical Coolant Holes | 1 End Chamfered Ground |
---|---|---|---|---|---|
Image | |||||
Description | A solid cylindrical rod made of tungsten carbide. | A solid carbide rod with a single straight coolant hole running through its center. | A solid carbide rod with two parallel straight coolant holes. | A solid carbide rod with two helical coolant holes for enhanced chip evacuation. | A solid carbide rod with one end chamfered and precision ground for accurate tool length setting. |
Coolant Flow | None | Through-tool coolant | Through-tool coolant | Through-tool coolant | None |
Chip Evacuation | Limited | Improved | Further improved | Superior | Limited |
Applications | General purpose machining, wear parts | Drilling, reaming, milling | Deep hole drilling, high-volume machining | High-performance machining, difficult-to-machine materials | Tool bit blanks, custom tool fabrication |
Advantages | Cost-effective, versatile | Enhanced chip removal, improved cooling | Balanced coolant flow, increased rigidity | Optimal chip removal, higher cutting speeds | Precise tool length, reduced setup time |
Limitations | Chip evacuation can be challenging | Single coolant hole may limit coolant flow | Helical holes can weaken the rod’s structure | More expensive than straight coolant holes | Not suitable for through-tool coolant applications |
Table 1: A Comparative Analysis of 4 Essential Solid Carbide Rod Types
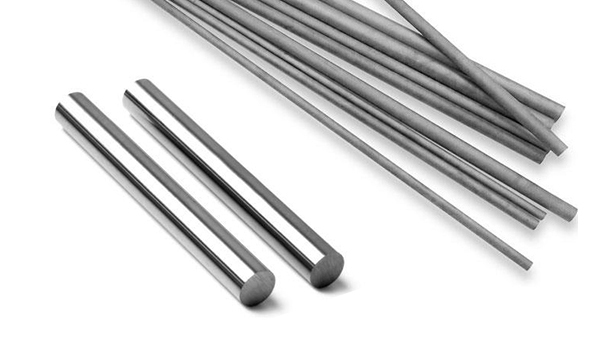
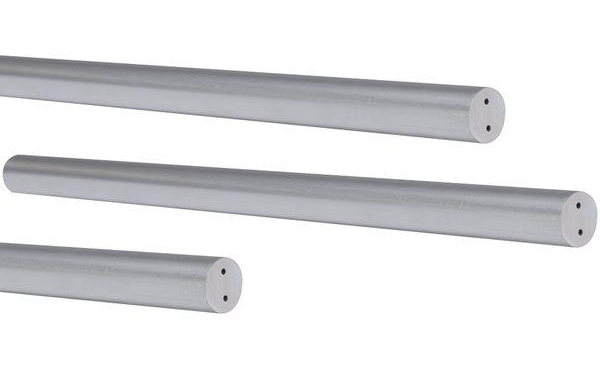
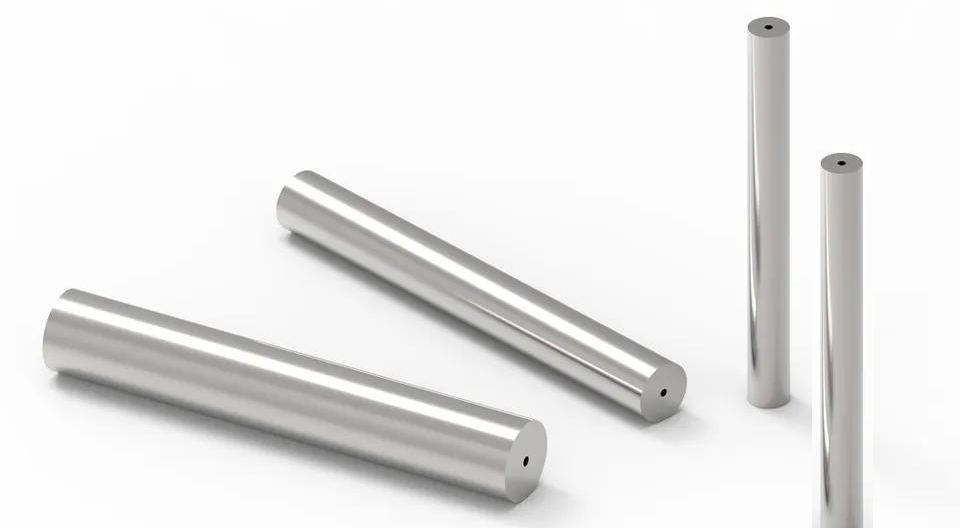
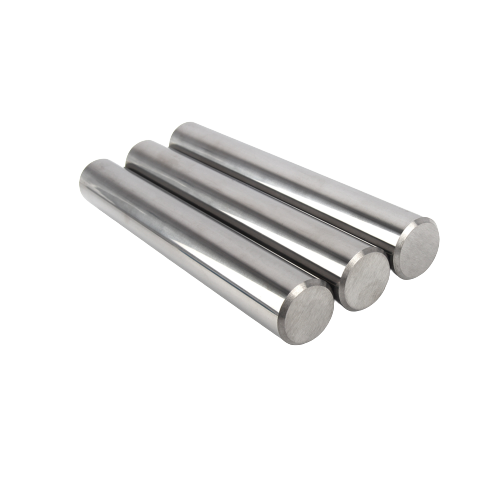
Applications: Where Precision Reigns Supreme
The versatility of solid carbide rods is reflected in their diverse applications across numerous industries:
- Aerospace: Manufacturing of engine components, turbine blades, and structural parts.
- Automotive: Production of engine components, transmission gears, and bearings.
- Medical: Creation of surgical instruments, implants, and dental tools.
- Moldmaking: Fabrication of molds for plastic injection molding, die casting, and other processes.
- Energy: Drilling and machining components for oil and gas exploration and power generation.
- Electronics: Micro-machining of electronic components and circuit boards.
Advantages and Limitations: Weighing the Pros and Cons
Feature | Advantages | Limitations |
---|---|---|
Hardness and Wear Resistance | Exceptional hardness and wear resistance, leading to longer tool life and improved cutting performance. | Can be brittle and prone to chipping under impact or high-vibration conditions. |
High-Temperature Stability | Retains hardness and strength at elevated temperatures, enabling high-speed machining operations. | Machining carbide requires specialized equipment and expertise due to its extreme hardness. |
Corrosion Resistance | Highly resistant to corrosion and chemical attack, suitable for use in harsh environments. | Can be more expensive than other tool materials, such as high-speed steel. |
Table 2: Advantages and Limitations of Solid Carbide Rods
Related Insights: Expanding the Carbide Horizon
- The Importance of Carbide Grade Selection: Choosing the right carbide grade is crucial for optimizing tool performance and longevity. Factors to consider include the material being machined, cutting speed, feed rate, and required surface finish.
- The Role of Coatings in Carbide Tool Performance: Coatings, such as TiN, TiAlN, and diamond-like carbon (DLC), can further enhance the wear resistance, lubricity, and oxidation resistance of carbide tools.
- Advancements in Carbide Rod Manufacturing: Innovations in powder metallurgy and sintering processes are leading to the development of new carbide grades with improved properties, such as finer grain structures and increased toughness.
FAQs: Addressing Your Carbide Rod Queries
1. What is the primary difference between solid carbide rods and carbide inserts?
Solid carbide rods are used to manufacture entire cutting tools, while carbide inserts are indexable cutting edges that are attached to tool holders. Solid carbide tools offer greater rigidity and are typically used for high-precision applications, while carbide inserts provide versatility and cost-effectiveness.
2. How do I choose the right coolant hole configuration for my application?
The choice of coolant hole configuration depends on the machining operation, material being cut, and desired chip evacuation. Straight coolant holes are suitable for general-purpose machining, while helical holes excel in high-performance applications where chip removal is critical.
3. Can I regrind or resharpen solid carbide tools?
Yes, solid carbide tools can be reground or resharpened multiple times, extending their lifespan and reducing tooling costs. However, it’s essential to use specialized grinding equipment and techniques to avoid damaging the carbide.
4. What are the safety precautions for handling solid carbide rods and tools?
Carbide is extremely hard and can shatter upon impact. Always wear safety glasses, gloves, and appropriate clothing when handling carbide. Use caution when machining carbide, as chips can be extremely sharp and hot.
5. Where can I source high-quality solid carbide rods?
Reputable carbide rod manufacturers and suppliers can provide high-quality products that meet your specific requirements. When selecting a supplier, consider factors such as experience, quality certifications, and customer support.
Want to buy cheap tungsten carbide rods at good prices? please click here.