Introduction: Unlocking Versatility with 4 Flute End Mills
4 flute end mills are indispensable tools in the world of machining, renowned for their ability to deliver a balance of aggressive material removal and smooth surface finishes. Their four cutting edges, or flutes, provide increased stability and chip clearance, making them ideal for a wide range of applications across various industries. This comprehensive guide delves into the specifics of three key types of 4 flute end mills: Straight Shank Square End Mills, Straight Shank Long Flush End Mills, and Straight Shank Round End Mills, exploring their unique characteristics, applications, and advantages.
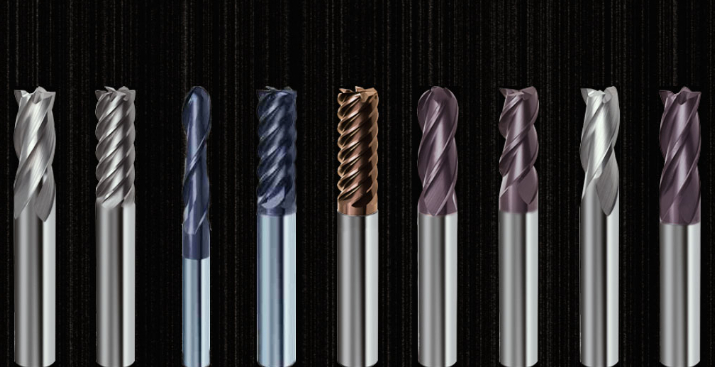
Understanding the Fundamentals: What is a 4 Flute End Mill?
Defining the Tool:
A 4 flute end mill is a rotary cutting tool featuring four helical cutting edges, or flutes, that spiral along its body. These flutes facilitate efficient material removal while channeling chips away from the cutting zone. The end mill’s design allows for both axial and lateral cutting, making it highly versatile for a multitude of machining operations.
Key Components of a 4 Flute End Mill:
- Cutting Edges: The four precisely ground edges, typically made from carbide or high-speed steel, are responsible for cutting the workpiece.
- Flutes: The helical grooves running along the body of the end mill provide pathways for chip evacuation. Four flutes offer a balance of chip removal, surface finish, and tool rigidity.
- Shank: The cylindrical portion of the end mill is secured in the tool holder of a milling machine.
- Body: The main section of the end mill houses the flutes and connects the shank to the cutting edges.
Exploring Three Essential Types of 4 Flute End Mills
1. Straight Shank Square End Mills: The Workhorse for General Machining
Straight shank square end mills are the most common type of 4 flute end mill, characterized by their square cutting profile and straight shank. They are highly versatile and widely used for a broad range of machining operations, including:
- Slotting and Pocketing: Creating rectangular slots and pockets in workpieces.
- Profiling: Machining contours and profiles on the edges of workpieces.
- Facing: Creating flat surfaces by removing material from the top face of a workpiece.
2. Straight Shank Long Flush End Mills: Reaching Deep with Precision
Straight shank long flush end mills, also known as long reach end mills, are specifically designed for machining deep cavities and features. They feature an extended cutting length and a reduced neck diameter, providing increased reach and rigidity for deep-cut applications. Key applications include:
- Deep Cavity Machining: Creating deep pockets, molds, and dies with precision.
- Mold Core Machining: Machining intricate details and features in mold cores.
- Aerospace Component Manufacturing: Producing complex parts with deep cavities and tight tolerances.
3. Straight Shank Round End Mills: Achieving Smooth Contours and Radii
Straight shank round end mills feature a rounded cutting profile, allowing for the creation of smooth contours, radii, and fillets. They are commonly used in applications where a smoother finish and reduced stress concentrations are desired, such as:
- Contour Machining: Creating smooth, flowing curves and profiles.
- Fillet and Radius Machining: Machining rounded corners and edges to reduce stress points.
- Mold Polishing: Finishing and polishing mold cavities to achieve a high-quality surface finish.
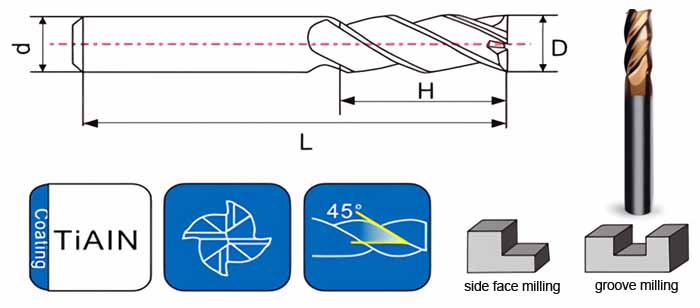
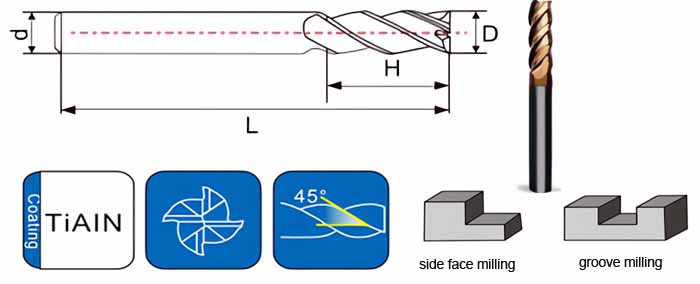

Comparative Analysis: Understanding the Differences
Feature | Straight Shank Square End Mill | Straight Shank Long Flush End Mill | Straight Shank Round End Mill |
---|---|---|---|
Cutting Profile | Square | Square | Round |
Shank Type | Straight | Straight | Straight |
Overall Length | Standard | Extended | Standard |
Neck Diameter | Standard | Reduced | Standard |
Applications | General machining, slotting, pocketing, profiling, facing | Deep cavity machining, mold core machining, aerospace components | Contour machining, fillet and radius machining, mold polishing |
Advantages | Versatile, widely available, cost-effective | Increased reach, enhanced rigidity for deep cuts | Smooth contours, reduced stress concentrations |
Limitations | Limited reach for deep cavities | Can be prone to deflection with excessive overhang | Not suitable for square corners or sharp edges |
Applications Across Industries: The Versatility of 4 Flute End Mills
Meeting Diverse Machining Needs:
- Aerospace: Manufacturing complex components with tight tolerances, such as engine parts, turbine blades, and structural elements.
- Automotive: Producing engine blocks, cylinder heads, transmission parts, and other critical components requiring precision and durability.
- Medical Device Manufacturing: Creating implants, surgical instruments, and other medical devices with high precision and biocompatibility.
- Mold Making: Machining intricate mold cavities, cores, and details for various industries, including plastics, die casting, and injection molding.
- General Machining: Widely used in machine shops and manufacturing facilities for a variety of tasks, including prototyping, repair, and custom fabrication.
Choosing the Right 4 Flute End Mill: Key Considerations
Factors Influencing Tool Selection:
- Material Being Machined: Different materials require end mills with specific properties, such as hardness, wear resistance, and coating.
- Type of Machining Operation: The specific machining operation, such as slotting, pocketing, or profiling, will dictate the appropriate end mill geometry.
- Depth of Cut: For deep cavities, long reach end mills are essential to provide the necessary reach and rigidity.
- Surface Finish Requirements: Choose an end mill with the appropriate number of flutes and geometry to achieve the desired surface finish.
- Machine Tool Capabilities: Consider the spindle speed, horsepower, and rigidity of the milling machine to ensure compatibility with the chosen end mill.
Why Choose TRUER for Your 4 Flute End Mill Needs?
Partnering with a Leader in Precision Tooling:
- Uncompromising Quality: TRUER maintains rigorous quality control measures throughout the manufacturing process, ensuring exceptional tool performance and longevity.
- Application-Specific Expertise: Our team of experienced engineers can guide you in selecting the optimal 4 flute end mill for your specific application, maximizing efficiency and results.
- Competitive Pricing and Timely Delivery: TRUER offers competitive pricing and strives to deliver orders promptly, minimizing downtime and maximizing your productivity.
Frequently Asked Questions: Addressing Your 4 Flute End Mill Queries
1. What are the primary advantages of using a 4 flute end mill compared to a 2 flute end mill?
4 flute end mills offer increased stability, improved chip evacuation, and generally smoother surface finishes compared to 2 flute end mills. This makes them well-suited for a wider range of materials and machining operations, particularly when higher cutting forces are involved.
2. When would I choose a straight shank square end mill over a straight shank round end mill?
Choose a straight shank square end mill for general machining operations where you need to create square corners, slots, or pockets. Opt for a straight shank round end mill when machining contours, radii, or fillets, as their rounded cutting profile produces smoother finishes and reduces stress concentrations.
3. What is the significance of the reduced neck diameter on a straight shank long flush end mill?
The reduced neck diameter on a straight shank long flush end mill allows for increased reach into deep cavities while maintaining rigidity. This design minimizes tool deflection and vibration, improving accuracy and surface finish in deep-cut applications.
4. What are some common signs of wear on a 4 flute end mill, and how can I extend tool life?
Common wear signs include increased cutting forces, poor surface finish, excessive heat generation, and chipping or breakage of the cutting edges. To extend tool life, use appropriate cutting parameters, apply coolant effectively, maintain a rigid setup, and avoid excessive tool deflection.
5. What factors should I consider when choosing the material and coating for my 4 flute end mill?
Consider the material being machined, the type of machining operation, and the desired tool life. Carbide end mills are generally more expensive but offer superior hardness, wear resistance, and high-temperature performance. HSS end mills are more cost-effective and suitable for machining softer materials. Coatings like TiN, TiCN, and AlTiN can further enhance tool life, hardness, and performance.
Want to buy a great quality 4 flute end mills at the right price? Click here.