- 2 helical coolant holes carbide rod
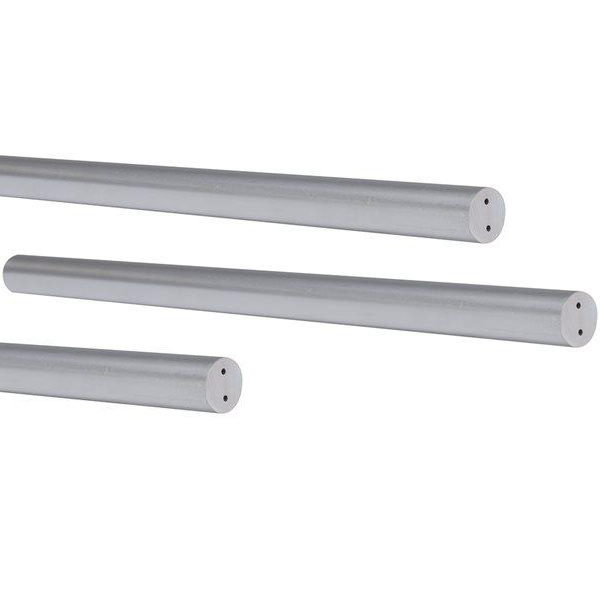
2 helical coolant holes carbide rod
Carbide rods with helical coolant holes greatly avoid the early wear and failure of the tungsten carbide tools during high-speed machiningby the coolant in helical holes to reduce the temperature evenly, widely used in cutting and machining applications. The helix angle determines the efficiency of chip evacuation during the cutting process, which is critical for preventing tool wear and damage to the workpiece.We supply 30°& 40°helix,and unground & ground carbide rods with twohelical cooling holes in varied grades. If you would like to learn more about our carbide grades, please click on the link below to browse the grade page.
A comprehensive standard selection of carbide rods with helical cooling holes in various dimensions is available in the below tables, but other sizes, tolerances & configurations also available on request.
Contact us if what you need is not shown here.
Introduction
A helical coolant holes carbide rod is a type of solid carbide rod that incorporates two helically-shaped coolant holes drilled along its length. These unique coolant holes are designed to optimize coolant flow and chip evacuation during machining operations. By providing improved cooling and efficient chip removal, these rods help to enhance tool life, reduce heat buildup, and improve overall machining performance. They are commonly used in high-speed machining and applications where effective cooling and chip control are critical.
Composition and Structure
Composition: The tungsten carbide particles make up the majority of the composition, providing the rod’s hardness and wear resistance. The binder material, such as cobalt or nickel, acts as a matrix that holds the tungsten carbide particles together.
Structure: The structure of a helical coolant holes carbide rod is typically dense and uniform due to the sintering process used during manufacturing. Sintering involves heating the green compact to a high temperature, allowing the tungsten carbide particles to bond together and form a solid structure. The helical coolant holes are precision-drilled along the length of the rod, creating a spiral pathway for coolant flow.
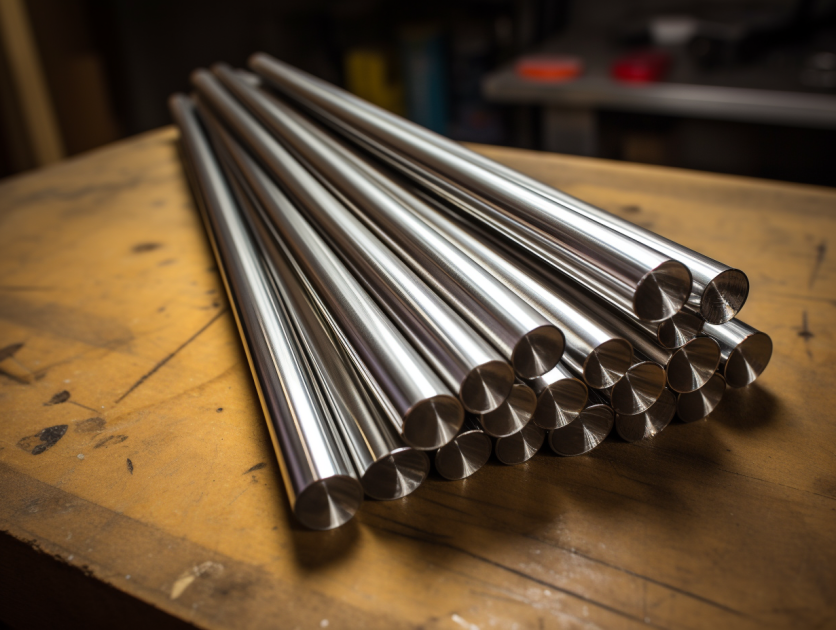
Efficient Coolant Flow
Enhanced flow ensures effective cooling at the cutting edge for improved machining performance.
Optimal Chip Evacuation
Helical holes facilitate smooth and efficient chip removal during machining operations.
Enhanced Cooling Capability
Improved coolant flow enables efficient heat dissipation, preventing tool overheating and prolonging tool life.
Extended Tool Life
Minimized wear and heat-related damage contribute to a longer lifespan and reduced tool replacement costs.
High Hardness and Wear Resistance
Durable and resistant to wear and abrasion for reliable performance in demanding applications.
Excellent Strength and Stability
Withstands high cutting forces without deformation, maintaining dimensional accuracy and stability.
Versatility in Machining
Suitable for various machining operations, including milling, turning, and drilling, offering flexibility in applications.
Improved Productivity
Enhanced cooling, chip evacuation, and tool life lead to increased efficiency, reduced downtime, and improved overall productivity.
Raw Material Selection
High-quality tungsten carbide powder and a binder material, typically cobalt or nickel, are carefully selected.
Mixing
The tungsten carbide powder and binder material are thoroughly mixed to create a homogeneous mixture.
Compacting
The mixed powder is compacted under high pressure to form a green compact, which roughly resembles the final rod shape.
Pre-Sintering
The green compact is subjected to pre-sintering at a temperature below the final sintering temperature.
Drilling Helical Coolant Holes
Precisely drill helical coolant holes in the pre-sintered green compact.
Sintering
Heat the pre-sintered compact to bond the tungsten carbide particles, forming a solid structure.
Shaping and Finishing
Machine the sintered rod to the desired shape, ensuring accurate coolant hole alignment.
Quality Control
Conduct inspections, measurements, and tests to ensure the rod meets specifications.
High-Speed Machining
The efficient coolant flow and chip evacuation provided by the helical coolant holes make 2 helical coolant holes carbide rods ideal for high-speed machining applications. They help to dissipate heat and maintain tool performance at elevated cutting speeds.
Aerospace Industry
The aerospace industry often requires precise and efficient machining of complex components. 2 helical coolant holes carbide rods are well-suited for this industry, as they enhance cooling and chip evacuation, allowing for improved accuracy and surface finish in aerospace parts manufacturing.
Automotive Industry
In automotive manufacturing, where high productivity and precision are crucial, 2 helical coolant holes carbide rods excel. They enable efficient cooling and chip removal during the production of automotive components, such as engine parts, transmission components, and brake system parts.
Mold and Die Making
The mold and die industry demands high accuracy and surface quality. 2 helical coolant holes carbide rods provide effective cooling and chip evacuation in the machining of intricate molds and dies. They contribute to improved dimensional precision and surface finish in mold and die production.
High-Speed Machining
The efficient coolant flow and chip evacuation provided by the helical coolant holes make 2 helical coolant holes carbide rods ideal for high-speed machining applications. They help to dissipate heat and maintain tool performance at elevated cutting speeds.
Aerospace Industry
The aerospace industry often requires precise and efficient machining of complex components. 2 helical coolant holes carbide rods are well-suited for this industry, as they enhance cooling and chip evacuation, allowing for improved accuracy and surface finish in aerospace parts manufacturing.
Automotive Industry
In automotive manufacturing, where high productivity and precision are crucial, 2 helical coolant holes carbide rods excel. They enable efficient cooling and chip removal during the production of automotive components, such as engine parts, transmission components, and brake system parts.
Mold and Die Making
The mold and die industry demands high accuracy and surface quality. 2 helical coolant holes carbide rods provide effective cooling and chip evacuation in the machining of intricate molds and dies. They contribute to improved dimensional precision and surface finish in mold and die production.
A 2 helical coolant holes carbide rod is a solid carbide rod with two helically-shaped coolant holes drilled along its length for enhanced coolant flow and chip evacuation during machining.
The two helical coolant holes provide improved coolant flow, efficient heat dissipation, optimal chip evacuation, extended tool life, and enhanced machining performance.
Yes, the diameter and pitch of the helical coolant holes can be customized based on specific machining requirements and coolant flow needs.
2 helical coolant holes carbide rods are compatible with various coolant systems, including through-spindle coolant systems, external coolant supplies, or flood coolant systems.
Yes, these rods are versatile and can be used in various machining operations such as milling, turning, drilling, and high-speed machining where efficient coolant flow and chip evacuation are essential.
The improved coolant flow and efficient heat dissipation provided by the helical coolant holes help to reduce tool wear, minimize heat-related damage, and extend the lifespan of the carbide rod.
Regular cleaning and inspection of the helical coolant holes to ensure unobstructed coolant flow are important for optimal performance and longevity.
Yes, 2 helical coolant holes carbide rods are suitable for machining various materials such as steels, alloys, and non-ferrous metals, making them applicable in diverse industrial sectors.
These specialized carbide rods are available from reputable tooling suppliers, manufacturers, and distributors specializing in cutting tools and machining components.
Standard safety precautions for machining operations, such as wearing appropriate protective gear and following safe operating practices, should be followed when using 2 helical coolant holes carbide rods.
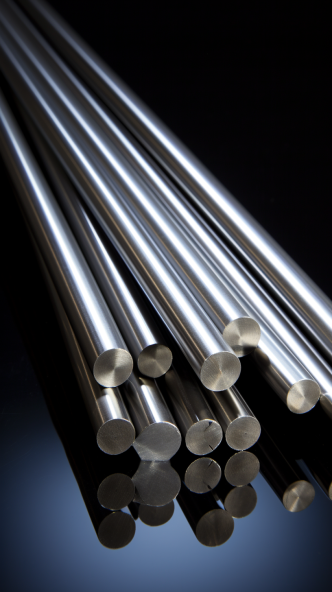
Data
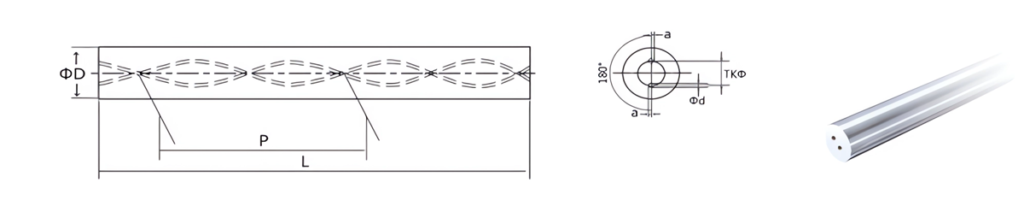
30° Helix 2 Helical Coolant Holes Carbide Rod Description
The 30° helix 2 helical coolant holes carbide rod is a specialized solid carbide rod with a 30-degree helical flute design and two helical coolant holes drilled along its length. This unique configuration offers improved chip evacuation, efficient coolant flow, and effective heat dissipation during machining operations. The 30° helix provides enhanced cutting action and stability, while the two helical coolant holes ensure optimal cooling and chip removal for extended tool life and improved machining performance. This carbide rod is suitable for various applications, including milling, drilling, and high-speed machining, where efficient coolant flow and chip evacuation are crucial.
Part No. | D/mm | L/mm | d/mm | TK/mm | Pitch | Tol. of D/mm | Tol. of L/mm | Tol. of d/mm | Tol. of TK/mm | Grade (click here) |
---|---|---|---|---|---|---|---|---|---|---|
RHUK03003300-2H0040-0170-01632 | 3.0 | 330 | 0.40 | 1.70 | 16.32 | +1.0/+0.6 | 0, +5 | ±0.10 | +0/-0.40 | TS710, TS610, TU412, TU409, TU406, TN209, TS715 |
RHUK04003300-2H0060-0220-02177 | 4.0 | 330 | 0.60 | 2.20 | 21.77 | +1.0/+0.6 | 0, +5 | ±0.10 | +0/-0.40 | TS710, TS610, TU412, TU409, TU406, TN209, TS715 |
RHUK05003300-2H0070-0260-02721 | 5.0 | 330 | 0.70 | 2.60 | 27.21 | +1.0/+0.6 | 0, +5 | ±0.10 | +0/-0.40 | TS710, TS610, TU412, TU409, TU406, TN209, TS715 |
RHUK06003300-2H0070-0260-03265 | 6.0 | 330 | 0.70 | 2.60 | 32.65 | +1.0/+0.6 | 0, +5 | ±0.10 | +0/-0.40 | TS710, TS610, TU412, TU409, TU406, TN209, TS715 |
RHUK07003300-2H0100-0370-03809 | 7.0 | 330 | 1.00 | 3.70 | 38.09 | +1.1/+0.7 | 0, +5 | ±0.15 | +0/-0.60 | TS710, TS610, TU412, TU409, TU406, TN209, TS715 |
RHUK08003300-2H0100-0400-04353 | 8.0 | 330 | 1.00 | 4.00 | 43.53 | +1.1/+0.7 | 0, +5 | ±0.15 | +0/-0.60 | TS710, TS610, TU412, TU409, TU406, TN209, TS715 |
RHUK09003300-2H0140-0480-04897 | 9.0 | 330 | 1.40 | 4.80 | 48.97 | +1.1/+0.7 | 0, +5 | ±0.15 | +0/-0.60 | TS710, TS610, TU412, TU409, TU406, TN209, TS715 |
RHUK10003300-2H0140-0480-05441 | 10.0 | 330 | 1.40 | 4.80 | 54.41 | +1.1/+0.7 | 0, +5 | ±0.15 | +0/-0.60 | TS710, TS610, TU412, TU409, TU406, TN209, TS715 |
RHUK11003300-2H0140-0530-05986 | 11.0 | 330 | 1.40 | 5.30 | 59.86 | +1.1/+0.7 | 0, +5 | ±0.15 | +0/-0.60 | TS710, TS610, TU412, TU409, TU406, TN209, TS715 |
RHUK12003300-2H0140-0625-06530 | 12.0 | 330 | 1.40 | 6.25 | 65.30 | +1.1/+0.7 | 0, +5 | ±0.15 | +0/-0.60 | TS710, TS610, TU412, TU409, TU406, TN209, TS715 |
RHUK13003300-2H0175-0650-07074 | 13.0 | 330 | 1.75 | 6.50 | 70.74 | +1.1/+0.7 | 0, +5 | ±0.20 | +0/-0.60 | TS710, TS610, TU412, TU409, TU406, TN209, TS715 |
RHUK14003300-2H0175-0710-07618 | 14.0 | 330 | 1.75 | 7.10 | 76.18 | +1.1/+0.7 | 0, +5 | ±0.20 | +0/-0.60 | TS710, TS610, TU412, TU409, TU406, TN209, TS715 |
RHUK14003300-2H0190-0670-07618 | 14.0 | 330 | 1.90 | 6.70 | 76.18 | +1.1/+0.7 | 0, +5 | ±0.20 | +0/-0.60 | TS710, TS610, TU412, TU409, TU406, TN209, TS715 |
RHUK15003300-2H0175-0770-08162 | 15.0 | 330 | 1.75 | 7.70 | 81.62 | +1.1/+0.7 | 0, +5 | ±0.20 | +0/-0.60 | TS710, TS610, TU412, TU409, TU406, TN209, TS715 |
RHUK16003300-2H0175-0830-08706 | 16.0 | 330 | 1.75 | 8.30 | 87.06 | +1.1/+0.7 | 0, +5 | ±0.20 | +0/-0.60 | TS710, TS610, TU412, TU409, TU406, TN209, TS715 |
RHUK16003300-2H0210-0800-08707 | 16.0 | 330 | 2.10 | 8.00 | 87.07 | +1.1/+0.7 | 0, +5 | ±0.20 | +0/-0.60 | TS710, TS610, TU412, TU409, TU406, TN209, TS715 |
RHUK16003300-2H0250-0880-08706 | 16.0 | 330 | 2.50 | 8.80 | 87.06 | +1.1/+0.7 | 0, +5 | ±0.20 | +0/-0.60 | TS710, TS610, TU412, TU409, TU406, TN209, TS715 |
RHUK17003300-2H0175-0890-09250 | 17.0 | 330 | 1.75 | 8.90 | 92.5 | +1.1/+0.7 | 0, +5 | ±0.20 | +0/-0.80 | TS710, TS610, TU412, TU409, TU406, TN209, TS715 |
RHUK18003300-2H0200-0955-09795 | 18.0 | 330 | 2.00 | 9.55 | 97.95 | +1.1/+0.7 | 0, +5 | ±0.20 | +0/-0.80 | TS710, TS610, TU412, TU409, TU406, TN209, TS715 |
RHUK18003300-2H0280-0990-09795 | 18.0 | 330 | 2.80 | 9.90 | 97.95 | +1.1/+0.7 | 0, +5 | ±0.20 | +0/-0.80 | TS710, TS610, TU412, TU409, TU406, TN209, TS715 |
RHUK19003300-2H0200-1010-10339 | 19.0 | 330 | 2.00 | 10.10 | 103.39 | +1.1/+0.7 | 0, +5 | ±0.20 | +0/-0.80 | TS710, TS610, TU412, TU409, TU406, TN209, TS715 |
RHUK20003300-2H0200-1040-10883 | 20.0 | 330 | 2.00 | 10.40 | 108.83 | +1.1/+0.7 | 0, +5 | ±0.20 | +0/-0.80 | TS710, TS610, TU412, TU409, TU406, TN209, TS715 |
RHUK20003300-2H0250-1000-10883 | 20.0 | 330 | 2.50 | 10.00 | 108.83 | +1.1/+0.7 | 0, +5 | ±0.20 | +0/-0.80 | TS710, TS610, TU412, TU409, TU406, TN209, TS715 |
RHUK21003300-2H0200-1115-11427 | 21.0 | 330 | 2.00 | 11.15 | 114.27 | +1.1/+0.7 | 0, +5 | ±0.20 | +0/-0.80 | TS710, TS610, TU412, TU409, TU406, TN209, TS715 |
RHUK22003300-2H0200-1160-11971 | 22.0 | 330 | 2.00 | 11.60 | 119.71 | +1.1/+0.7 | 0, +5 | ±0.20 | +0/-0.80 | TS710, TS610, TU412, TU409, TU406, TN209, TS715 |
RHUK23003300-2H0200-1220-12515 | 23.0 | 330 | 2.00 | 12.20 | 125.15 | +1.1/+0.7 | 0, +5 | ±0.20 | +0/-0.80 | TS710, TS610, TU412, TU409, TU406, TN209, TS715 |
RHUK24003300-2H0200-1280-13059 | 24.0 | 330 | 2.00 | 12.80 | 130.59 | +1.1/+0.7 | 0, +5 | ±0.20 | +0/-0.80 | TS710, TS610, TU412, TU409, TU406, TN209, TS715 |
RHUK25003300-2H0200-1330-13603 | 25.0 | 330 | 2.00 | 13.30 | 136.03 | +1.2/+0.8 | 0, +5 | ±0.25 | +0/-1.00 | TS710, TS610, TU412, TU409, TU406, TN209, TS715 |
Part No. | D/mm | L/mm | d/mm | TK/mm | Pitch | Grade (click here) |
---|---|---|---|---|---|---|
RHU/GJ03003300-2H0040-0170-01632 | 3.0 | 330 | 0.40 | 1.70 | 16.32 | TN209, TU406, TU412, TS610, TU408, TU510, TU512A, TU512B, TS606, TS613, TM1512, TM2214 |
RHU/GJ04003300-2H0060-0220-02177 | 4.0 | 330 | 0.60 | 2.20 | 21.77 | TN209, TU406, TU412, TS610, TU408, TU510, TU512A, TU512B, TS606, TS613, TM1512, TM2214 |
RHU/GJ05003300-2H0070-0260-02721 | 5.0 | 330 | 0.70 | 2.60 | 27.21 | TN209, TU406, TU412, TS610, TU408, TU510, TU512A, TU512B, TS606, TS613, TM1512, TM2214 |
RHU/GJ06003300-2H0070-0260-03265 | 6.0 | 330 | 0.70 | 2.60 | 32.65 | TN209, TU406, TU412, TS610, TU408, TU510, TU512A, TU512B, TS606, TS613, TM1512, TM2214 |
RHU/GJ07003300-2H0100-0370-03809 | 7.0 | 330 | 1.00 | 3.70 | 38.09 | TN209, TU406, TU412, TS610, TU408, TU510, TU512A, TU512B, TS606, TS613, TM1512, TM2214 |
RHU/GJ08003300-2H0100-0400-04353 | 8.0 | 330 | 1.00 | 4.00 | 43.53 | TN209, TU406, TU412, TS610, TU408, TU510, TU512A, TU512B, TS606, TS613, TM1512, TM2214 |
RHU/GJ09003300-2H0140-0480-04897 | 9.0 | 330 | 1.40 | 4.80 | 48.97 | TN209, TU406, TU412, TS610, TU408, TU510, TU512A, TU512B, TS606, TS613, TM1512, TM2214 |
RHU/GJ10003300-2H0140-0480-05441 | 10.0 | 330 | 1.40 | 4.80 | 54.41 | TN209, TU406, TU412, TS610, TU408, TU510, TU512A, TU512B, TS606, TS613, TM1512, TM2214 |
RHU/GJ11003300-2H0140-0530-05986 | 11.0 | 330 | 1.40 | 5.30 | 59.86 | TN209, TU406, TU412, TS610, TU408, TU510, TU512A, TU512B, TS606, TS613, TM1512, TM2214 |
RHU/GJ12003300-2H0140-0625-06530 | 12.0 | 330 | 1.40 | 6.25 | 65.30 | TN209, TU406, TU412, TS610, TU408, TU510, TU512A, TU512B, TS606, TS613, TM1512, TM2214 |
RHU/GJ13003300-2H0175-0650-07074 | 13.0 | 330 | 1.75 | 6.50 | 70.74 | TN209, TU406, TU412, TS610, TU408, TU510, TU512A, TU512B, TS606, TS613, TM1512, TM2214 |
RHU/GJ14003300-2H0175-0710-07618 | 14.0 | 330 | 1.75 | 7.10 | 76.18 | TN209, TU406, TU412, TS610, TU408, TU510, TU512A, TU512B, TS606, TS613, TM1512, TM2214 |
RHU/GJ15003300-2H0175-0770-08162 | 15.0 | 330 | 1.75 | 7.70 | 81.62 | TN209, TU406, TU412, TS610, TU408, TU510, TU512A, TU512B, TS606, TS613, TM1512, TM2214 |
RHU/GJ16003300-2H0175-0830-08706 | 16.0 | 330 | 1.75 | 8.30 | 87.06 | TN209, TU406, TU412, TS610, TU408, TU510, TU512A, TU512B, TS606, TS613, TM1512, TM2214 |
RHU/GJ17003300-2H0175-0890-09250 | 17.0 | 330 | 1.75 | 8.90 | 92.50 | TN209, TU406, TU412, TS610, TU408, TU510, TU512A, TU512B, TS606, TS613, TM1512, TM2214 |
RHU/GJ18003300-2H0200-0955-09795 | 18.0 | 330 | 2.00 | 9.55 | 97.95 | TN209, TU406, TU412, TS610, TU408, TU510, TU512A, TU512B, TS606, TS613, TM1512, TM2214 |
RHU/GJ19003300-2H0200-1010-10339 | 19.0 | 330 | 2.00 | 10.10 | 103.39 | TN209, TU406, TU412, TS610, TU408, TU510, TU512A, TU512B, TS606, TS613, TM1512, TM2214 |
RHU/GJ20003300-2H0200-1040-10883 | 20.0 | 330 | 2.00 | 10.40 | 108.83 | TN209, TU406, TU412, TS610, TU408, TU510, TU512A, TU512B, TS606, TS613, TM1512, TM2214 |
RHU/GJ21003300-2H0200-1115-11427 | 21.0 | 330 | 2.00 | 11.15 | 114.27 | TN209, TU406, TU412, TS610, TU408, TU510, TU512A, TU512B, TS606, TS613, TM1512, TM2214 |
RHU/GJ22003300-2H0200-1160-11971 | 22.0 | 330 | 2.00 | 11.60 | 119.71 | TN209, TU406, TU412, TS610, TU408, TU510, TU512A, TU512B, TS606, TS613, TM1512, TM2214 |
RHU/GJ23003300-2H0200-1220-12515 | 23.0 | 330 | 2.00 | 12.20 | 125.15 | TN209, TU406, TU412, TS610, TU408, TU510, TU512A, TU512B, TS606, TS613, TM1512, TM2214 |
RHU/GJ24003300-2H0200-1280-13059 | 24.0 | 330 | 2.00 | 12.80 | 130.59 | TN209, TU406, TU412, TS610, TU408, TU510, TU512A, TU512B, TS606, TS613, TM1512, TM2214 |
RHU/GJ25003300-2H0200-1330-13603 | 25.0 | 330 | 2.00 | 13.30 | 136.03 | TN209, TU406, TU412, TS610, TU408, TU510, TU512A, TU512B, TS606, TS613, TM1512, TM2214 |
40° Helix 2 Helical Coolant Holes Carbide Rod Description
The 40° helix 2 helical coolant holes carbide rod is a specialized solid carbide rod featuring a 40-degree helical flute design and two helical coolant holes drilled along its length. This configuration offers enhanced chip evacuation, efficient coolant flow, and effective heat dissipation during machining operations. The 40° helix provides improved cutting action and stability, while the two helical coolant holes ensure optimal cooling and chip removal for extended tool life and enhanced machining performance. This carbide rod is well-suited for various applications, including milling, drilling, and high-speed machining, where efficient coolant flow and chip evacuation are critical for achieving superior results.
Unground & Ground Data
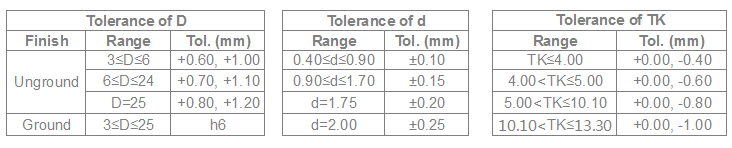
Part No. | D/mm | L/mm | d/mm | TK/mm | Pitch | Grade (click here) |
---|---|---|---|---|---|---|
RHU/GJ06003300-2H0050-0220-02246 | 6.0 | 330 | 0.50 | 2.20 | 22.46 | TN209, TU406, TU412, TS610, TU408, TU510, TU512A, TU512B, TS606, TS613, TM1512, TM2214 |
RHU/GJ08003300-2H0065-0270-02995 | 8.0 | 330 | 0.65 | 2.70 | 29.95 | TN209, TU406, TU412, TS610, TU408, TU510, TU512A, TU512B, TS606, TS613, TM1512, TM2214 |
RHU/GJ10003300-2H0080-0350-03744 | 10.0 | 330 | 0.80 | 3.50 | 37.44 | TN209, TU406, TU412, TS610, TU408, TU510, TU512A, TU512B, TS606, TS613, TM1512, TM2214 |
RHU/GJ12003300-2H0090-0420-04493 | 12.0 | 330 | 0.90 | 4.20 | 44.93 | TN209, TU406, TU412, TS610, TU408, TU510, TU512A, TU512B, TS606, TS613, TM1512, TM2214 |
RHU/GJ14003300-2H0100-0470-05242 | 14.0 | 330 | 1.00 | 4.70 | 52.42 | TN209, TU406, TU412, TS610, TU408, TU510, TU512A, TU512B, TS606, TS613, TM1512, TM2214 |
RHU/GJ16003300-2H0120-0550-05990 | 16.0 | 330 | 1.20 | 5.50 | 59.90 | TN209, TU406, TU412, TS610, TU408, TU510, TU512A, TU512B, TS606, TS613, TM1512, TM2214 |
RHU/GJ18003300-2H0140-0630-06739 | 18.0 | 330 | 1.40 | 6.30 | 67.39 | TN209, TU406, TU412, TS610, TU408, TU510, TU512A, TU512B, TS606, TS613, TM1512, TM2214 |
RHU/GJ20003300-2H0150-0710-07488 | 20.0 | 330 | 1.50 | 7.10 | 74.88 | TN209, TU406, TU412, TS610, TU408, TU510, TU512A, TU512B, TS606, TS613, TM1512, TM2214 |
- Contact
Our team is ready to provide support
Truer Carbide is committed to providing efficient solutions to problems. Each team member has the expertise and experience to quickly understand and meet your needs.