소개 소개: 용서할 수 없는 것을 정복하다: 내구성과 성능의 만남
극한의 온도와 마모성 재료가 공구를 한계까지 밀어붙이는 까다로운 금속 절삭 영역에서는 가장 견고한 제품만이 살아남습니다. 입력 타입 K 카바이드 브레이징 팁가장 혹독한 절삭 조건을 견디면서도 뛰어난 성능과 공구 수명을 제공하도록 설계된 헤비 듀티 챔피언입니다.
이 글에서는 초경 브레이징 팁의 고유한 특성과 장점, 그리고 가장 까다로운 가공 과제를 해결하기 위해 초경 팁을 선택하는 이유를 살펴봅니다.
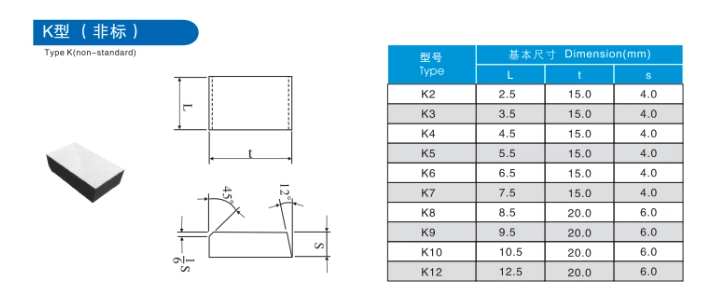
극한의 절단 조건에 대한 도전: 열과 마모와의 싸움
가공의 한계를 뛰어넘다:
특정 가공 작업에는 절삭 공구의 성능을 빠르게 저하시킬 수 있는 극한의 조건이 수반됩니다:
- 고온: 절삭 영역에서 마찰과 칩 형성으로 인해 발생하는 고온은 절삭 날을 연화시켜 공구의 빠른 마모와 정확도 저하로 이어질 수 있습니다.
- 연마재: 주철, 고실리콘 알루미늄, 섬유 강화 플라스틱과 같은 마모성 소재를 가공하면 절삭 날에 상당한 마모가 발생하여 공구 수명이 단축되고 표면 조도가 저하됩니다.
- 중단된 컷: 불규칙한 모양이나 표면이 끊어진 부품을 가공할 때 발생하는 끊어진 절삭은 절삭 공구에 충격 하중과 열 순환이 가해져 칩핑과 파손의 위험을 증가시킵니다.
타입 K 카바이드 브레이징 팁: 강도와 내구성을 위한 단조
내구성과 성능의 해부학:
K형 카바이드 브레이징 팁은 극한의 절단 조건에서도 견딜 수 있도록 특별히 제작되었으며, 다음과 같은 특징이 있습니다:
- 견고한 카바이드 등급: 타입 K 팁은 극한의 온도와 마모 조건에서 높은 인성과 마모, 칩핑, 파손에 대한 내성을 위해 특별히 제조된 카바이드 재종을 사용합니다.
- 포지티브 레이크 각도: 타입 K 팁의 플러스 경사각은 절삭력과 열 발생을 줄여 까다로운 응용 분야에서 칩 흐름을 개선하고 공구 수명을 연장합니다.
- 강력한 브레이징 조인트: 카바이드 팁은 고온과 충격 하중을 견디는 특수 브레이징 합금을 사용하여 공구 생크에 단단히 브레이징되어 가장 까다로운 작업에서도 팁의 무결성을 보장합니다.
K형 카바이드 브레이징 팁이 극한 조건에서 탁월한 10가지 이유
자신감을 가지고 용서할 수 없는 것을 정복하세요:
타입 K 카바이드 브레이징 팁의 견고한 구조와 재료 특성은 몇 가지 주요 이점을 제공합니다:
- 탁월한 내마모성: 견고한 카바이드 재종과 플러스 레이크 각도는 연마재와 고온으로 인한 마모를 최소화하여 공구 수명을 크게 연장합니다.
- 높은 고온 경도: K타입 팁은 고온에서도 경도와 최첨단 무결성을 유지하여 까다로운 애플리케이션에서 일관된 성능과 정확성을 보장합니다.
- 칩핑 및 파손에 대한 내성: 견고한 카바이드 재종과 강력한 브레이징 조인트로 인해 타입 K 팁은 중단 절삭에서 발생하는 충격 하중과 열 순환을 견딜 수 있습니다.
- 향상된 칩 제어: 포지티브 레이크 각도는 효율적인 칩 흐름을 촉진하여 열 축적을 줄이고 공구와 공작물 모두를 손상시킬 수 있는 칩 용접을 방지합니다.
- 절단력 감소: 플러스 레이크 각도와 날카로운 절삭날은 절삭력을 최소화하여 공구, 공작 기계 및 공작물에 가해지는 스트레스를 줄여줍니다.
- 향상된 표면 마감: K타입 팁은 주로 마감용으로 설계되지는 않았지만, 특히 다른 팁 형상이 어려움을 겪는 까다로운 소재에서 놀라울 정도로 우수한 표면 마감을 구현할 수 있습니다.
- 까다로운 애플리케이션에서의 활용성: 타입 K 팁은 황삭, 반정삭, 까다로운 재료의 중단 절삭 등 다양한 고강도 가공 작업에 적합합니다.
- 까다로운 환경에서의 비용 효율성: 타입 K 팁이 제공하는 공구 수명 연장과 가동 중단 시간 감소는 특히 공구 마모가 주요 관심사인 애플리케이션에서 전반적인 비용 절감에 기여합니다.
- 생산성 향상: 공구 수명 저하 없이 더 높은 절삭 속도와 이송을 견딜 수 있는 능력은 생산성 향상과 사이클 시간 단축으로 이어집니다.
- 도구 고장 위험 감소: 타입 K 팁의 견고한 구조와 내마모성은 공구 고장의 위험을 최소화하여 공정 안정성을 높이고 불량률을 낮춥니다.
타입 K 카바이드 브레이징 팁의 적용 분야
내구성과 성능이 융합된 곳:
타입 K 카바이드 브레이징 팁은 가장 까다로운 가공 과제를 해결하기 위한 최고의 선택입니다:
- 경화강 가공: 높은 열경도와 내마모성으로 절삭 공구가 까다롭기로 악명 높은 경화강 가공에 이상적입니다.
- 연마재 절단: 타입 K 팁은 주철, 고실리콘 알루미늄, 섬유 강화 플라스틱과 같이 다른 팁 형상이 빨리 마모되는 마모성 소재 가공에 탁월합니다.
- 절단 작업 중단: 칩핑과 파손에 강해 밀링 슬롯, 포켓 및 기타 불규칙한 모양의 피처와 같은 중단된 절삭 작업에 적합합니다.
올바른 유형의 K 카바이드 브레이징 팁 선택하기: 고려해야 할 요소
극한 조건에 맞는 도구 선택 최적화:
최적의 K형 카바이드 브레이징 팁을 선택하려면 여러 가지 요소를 신중하게 고려해야 합니다:
- 공작물 재질: 재료의 경도, 마모성 및 열적 특성은 적절한 카바이드 등급과 코팅을 결정하는 데 중요한 요소입니다.
- 절단 조건: 절단 속도, 이송, 절단 깊이, 절단 중단 여부 등 절단 조건의 심각도는 팁 선택에 영향을 미칩니다.
- 머신 툴 기능: 공작 기계의 강성과 출력은 달성 가능한 절삭 파라미터와 적절한 팁 크기 및 형상 선택에 영향을 미칠 수 있습니다.
타입 K 카바이드 브레이징 팁 선택: 간단한 가이드
선택 과정을 돕기 위해 다양한 타입 K 팁 형상에 대한 일반적인 적용 사례와 고려 사항을 요약한 표를 소개합니다:
타입 K 팁 지오메트리 | 일반적인 애플리케이션 | 주요 고려 사항 |
---|---|---|
포지티브 레이크 각도의 정사각형 인서트 | 범용 황삭, 헤비 듀티 밀링 | 다양한 애플리케이션에 적합한 강도와 칩 흐름의 균형을 제공합니다. |
포지티브 레이크 각도의 삼각형 인서트 | 플런지 밀링, 램핑, 모서리 가공 | 공격적인 절단 및 절삭 작업을 위한 강력한 절삭날 제공 |
칩브레이커 지오메트리의 원형 인서트 | 연속 절단, 칩 제어 개선 | 향상된 칩 제어 기능을 제공하고 연속 절단 작업에서 절삭력을 줄입니다. |
타입 K 카바이드 브레이징 팁에 대해 자주 묻는 질문
Q1: 캔 타입 K 카바이드 브레이징 팁를 사용하여 작업을 마무리할 수 있나요?
A1: 주로 황삭 및 고강도 가공용으로 설계되었지만, 타입 K 팁은 다른 팁 형상이 어려움을 겪는 까다로운 재료에서도 놀라울 정도로 우수한 표면 마감을 얻을 수 있습니다. 그러나 최적의 표면 마감을 위해서는 일반적으로 마감 작업을 위해 특별히 설계된 팁을 사용하는 것이 좋습니다.
Q2: 타입 K 카바이드 브레이징 팁의 마모 징후는 무엇인가요?
A2: 일반적인 마모 징후로는 절삭날의 측면 마모, 레이크 면의 크레이터 마모, 절삭날의 치핑 또는 파손 등이 있습니다. 극한의 절삭 조건에서 마모는 치수 정확도 저하, 표면 조도 저하 또는 절삭력 증가로 나타날 수 있습니다.
Q3: 타입 K 카바이드 브레이징 팁을 사용할 때 공구 수명을 최대화하려면 어떻게 해야 합니까?
A3: 핵심 요소에는 적용 분야에 적합한 팁 형상과 재종 선택, 절삭 파라미터 최적화(재료의 가공성 및 공작 기계의 성능 고려), 적절한 절삭유 도포 보장, 견고한 기계 설정 유지 등이 있습니다.
Q4: 사각형 인서트와 삼각형 인서트 타입 K 팁의 차이점은 무엇인가요?
A4: 양의 경사각을 가진 사각 인서트는 범용 황삭 및 고강도 밀링에 적합한 강도와 칩 흐름의 균형을 제공하며, 양의 경사각을 가진 삼각형 인서트는 공격적인 절삭 및 절입 작업에 적합한 강력한 절삭 날을 제공합니다.
Q5: 원형 인서트 타입 K 팁은 언제 선택해야 하나요?
A5: 칩 브레이커 형상의 원형 인서트는 정사각형 또는 삼각형 인서트에 비해 칩 제어 기능이 향상되고 절삭력이 감소하므로 연속 절삭 작업에 선호되는 경우가 많습니다.