개요
카바이드 톱 팁 are crucial components in cutting tools, defining the efficiency, precision, and durability of saw blades. The geometry and design of these tips play a critical role in their cutting performance and wear resistance. This blog delves into the intricate details of carbide saw tip design, exploring how various geometric factors influence their functionality. Whether you’re in woodworking, metalworking, or another industry that relies on precision cutting, understanding these factors can significantly enhance your tool performance and longevity.
자세한 소개
카바이드 톱 팁이란?
Carbide saw tips are small, hard components attached to the teeth of saw blades. They are made from tungsten carbide, a material known for its hardness and wear resistance. These tips enable saw blades to cut through various materials with high precision and minimal wear. The design and geometry of these tips are meticulously engineered to optimize performance.
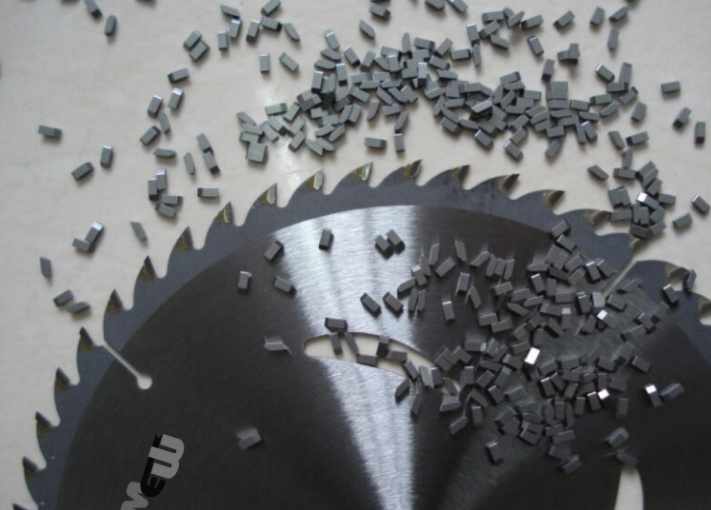
How Does Geometry Affect Cutting Performance?
The geometry of a carbide saw tip includes its shape, angle, and edge configuration. These factors collectively determine how effectively the tip can cut through a material. Key geometric aspects include:
- Tip Shape: The overall shape of the tip affects how it interacts with the material. Common shapes include flat, trapezoidal, and round tips, each offering different cutting characteristics.
- 레이크 각도: The rake angle is the angle between the face of the tip and the material being cut. Positive rake angles make cutting easier and require less force, while negative rake angles provide greater strength and durability.
- 클리어런스 각도: This is the angle between the back of the tip and the material, which helps prevent the tip from rubbing against the material, reducing friction and heat generation.
- 가장자리 반경: The sharpness of the cutting edge, defined by its radius, affects the ease of cutting and the quality of the finish. Sharper edges provide cleaner cuts but may wear out faster.
Key Geometric Factors and Their Impact
Tip Shape and Profile
The shape and profile of a carbide saw tip determine its cutting efficiency and the type of cut it can achieve. Here are some common shapes and their impacts:
- Flat Tips: Provide a smooth and continuous cut, ideal for fine finishes.
- Trapezoidal Tips: Offer a balance between sharpness and durability, suitable for general-purpose cutting.
- 라운드 팁: Enhance tip strength and durability, making them ideal for cutting harder materials.
레이크 각도
The rake angle significantly influences cutting ease and tool life:
- 포지티브 레이크 각도: Reduces cutting force and energy consumption, improving cutting efficiency. It is suitable for softer materials like wood and plastics.
- 네거티브 레이크 각도: Increases the strength and durability of the tip, making it ideal for cutting hard and abrasive materials like metals.
클리어런스 각도
The clearance angle helps in reducing friction and heat buildup:
- Large Clearance Angle: Minimizes friction and heat, extending tool life. It is beneficial for high-speed cutting applications.
- Small Clearance Angle: Provides greater support to the cutting edge, enhancing durability but may increase friction and heat.
가장자리 반경
The edge radius affects the quality of the cut and wear resistance:
- Sharp Edge: Provides clean and precise cuts but wears out faster.
- Blunt Edge: Increases durability and wear resistance, suitable for rough cutting applications.
How to Optimize Design for Wear Resistance?
Wear resistance is crucial for the longevity of carbide saw tips. Optimizing design involves balancing sharpness and durability. Key considerations include:
- 머티리얼 구성: Using high-quality tungsten carbide with appropriate binder materials enhances wear resistance.
- 코팅: Applying advanced coatings like titanium nitride (TiN) or diamond-like carbon (DLC) reduces wear and extends tool life.
- 팁 지오메트리: Selecting the appropriate rake angle, clearance angle, and edge radius for specific materials and cutting conditions ensures optimal wear resistance.
Manufacturing Process and its Influence on Geometry
The manufacturing process of carbide saw tips also affects their geometry and performance. The key steps include:
- 분말 혼합: 텅스텐 카바이드 분말은 금속 바인더(보통 코발트)와 혼합됩니다.
- 누르기: The mixture is pressed into shape using high-pressure molds, defining the tip’s geometry.
- 소결: 압착된 형상은 소결로에서 고온으로 가열되어 카바이드 입자를 서로 결합합니다.
- 그라인딩: The sintered tips are ground to precise dimensions and sharpened, affecting the edge radius and overall geometry.
- 브레이징: The finished tips are brazed onto the saw blade’s body, ensuring a secure and durable attachment.
Table: Geometric Factors and Their Impact on Cutting Performance
Geometric Factor | 설명 | Impact on Cutting Performance | 내마모성에 미치는 영향 |
---|---|---|---|
Tip Shape | Overall shape of the tip | Determines cutting characteristics and efficiency | Affects durability based on material hardness |
레이크 각도 | Angle between the tip face and material | Positive angles reduce cutting force; negative angles enhance strength | Positive angles may wear faster; negative angles increase durability |
클리어런스 각도 | Angle between tip back and material | Large angles reduce friction and heat | Small angles provide greater edge support |
가장자리 반경 | Sharpness of the cutting edge | Sharper edges provide cleaner cuts | Blunter edges enhance wear resistance |
설명: This table summarizes the geometric factors of carbide saw tips, their descriptions, and their impacts on cutting performance and wear resistance. Understanding these factors helps in selecting the right tip design for specific applications.
애플리케이션
Carbide saw tips are used in various industries and applications, each benefiting from specific geometric designs. Here are some key applications:
- 목공:
- 경목과 연목 자르기.
- 정밀 가구 및 캐비닛.
- 목재 표면을 정교하게 마감합니다.
- 금속 가공:
- 알루미늄과 구리 같은 비철금속을 절단합니다.
- 스테인리스 스틸과 같은 단단한 금속 가공.
- 금속 부품 및 구조물 제작.
- 플라스틱 절단:
- 플라스틱 시트와 부품을 자르고 성형합니다.
- 정밀한 치수의 플라스틱 제품 제조.
- 건설:
- 콘크리트, 벽돌 및 기타 건축 자재 절단.
- 건물 구성 요소 제작.
- 자동차 산업:
- 자동차 부품 및 구성 요소 제조.
- 금속 및 플라스틱 부품 절단 및 가공.
- 항공우주:
- 항공우주 재료의 정밀 절단.
- 항공기 부품 제작.
- 가구 제조:
- 목재 및 금속 가구 부품을 절단하고 성형합니다.
- 가구 표면의 미세한 마감 처리.
장단점 표
Table: Advantages and Limitations of Different Geometric Designs
측면 | Flat Tips | Trapezoidal Tips | 라운드 팁 |
---|---|---|---|
절단 효율성 | High for smooth and continuous cuts | Balanced for general-purpose cutting | Moderate, suitable for hard materials |
내구성 | 보통 | 높음 | 매우 높음 |
정밀도 | 매우 높음 | 높음 | 보통 |
내마모성 | 보통 | 높음 | 매우 높음 |
애플리케이션 | Fine woodworking and finishing | 범용 커팅 | Cutting hard and abrasive materials |
설명: This table compares the advantages and limitations of different geometric designs of carbide saw tips. Each design offers unique benefits and is suitable for specific applications and materials.
FAQs: Addressing Your Carbide Saw Tip Geometry Queries
1. What is the best rake angle for cutting hardwood?
A slightly negative rake angle (around -5 to -10 degrees) is generally recommended for hardwoods to provide a good balance of cutting performance and wear resistance.
2. How does the gullet design affect chip evacuation?
더 넓고 깊은 홈통은 연목이나 플라스틱과 같이 큰 칩을 생성하는 재료를 절단할 때 필수적인 칩 제거 공간을 더 많이 제공합니다.
3. What is the purpose of a chipbreaker?
Chipbreakers help break chips into smaller pieces, preventing them from clogging the gullet and reducing heat buildup, which can extend tool life.
4. How do coatings improve carbide saw tip performance?
Coatings like TiN or AlTiN increase hardness, reduce friction, and improve heat resistance, leading to longer tool life and improved cutting performance.
5. Where can I find information on the specific geometry of my saw blade’s carbide tips?
TRUER provides detailed information on the tip geometry, including rake angle, clearance angle, and other features. This information can be found on the blade’s packaging or in the product details page.
카바이드 팁 톱 팁을 좋은 가격에 구매하고 싶으신가요? 클릭하세요 여기.