Introduction: Defying Wear, Delivering Durability
In industries where abrasion, impact, and extreme conditions are daily challenges, wear-resistant 카바이드 플레이트 blanks emerge as unsung heroes. These robust plates, meticulously engineered from cemented carbide, provide exceptional protection for critical components, extending their lifespan and minimizing costly downtime.
This comprehensive guide delves into the world of wear-resistant carbide plate blanks, exploring their properties, manufacturing processes, diverse applications, and the advantages of partnering with a trusted supplier like TRUER.
Wear-Resistant Carbide Plate Blanks: The Shield Against Abrasion
Understanding the Power of Tungsten Carbide
Wear-resistant carbide plate blanks are pre-sintered or fully sintered plates composed primarily of tungsten carbide (WC) particles, renowned for their exceptional hardness, bonded together by a metallic binder, typically cobalt (Co). This unique composition grants these plates unparalleled resistance to wear, making them ideal for applications where surfaces are subjected to constant friction, abrasion, or impact.
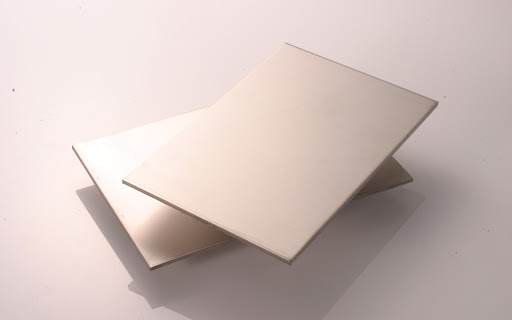
The Making of a Wear-Resistant Champion
From Powder to Plate: The Manufacturing Process
The creation of wear-resistant carbide plate blanks involves a carefully controlled multi-step process:
- 파우더 준비: Tungsten carbide (WC) powder and a binder metal powder, usually cobalt (Co), are precisely mixed in specific ratios to achieve the desired material properties. Other elements, such as tantalum (Ta), niobium (Nb), or titanium (Ti), may be added to enhance specific characteristics like wear resistance or corrosion resistance.
- 누릅니다: The powder mixture is then pressed into the desired plate shape using high-pressure dies. The applied pressure compacts the powder, forming a “green” (unsintered) plate with sufficient strength for handling.
- Presintering (Optional): Some manufacturers employ a presintering step, where the green plates undergo a controlled heating process in a furnace. This imparts additional green strength and prepares the plates for final sintering.
- 소결: The presintered or green plates are subjected to extremely high temperatures (typically between 1350°C and 1500°C) in a controlled atmosphere furnace. This process, known as liquid-phase sintering, fuses the WC particles together through the molten binder phase, resulting in a dense, incredibly hard material.
- 마무리: After sintering, the plates may undergo various finishing operations, such as grinding, lapping, or polishing, to achieve the desired dimensions, surface finish, and flatness.
Decoding the Properties: What Makes Carbide Plates Wear-Resistant?
Table 1: Typical Properties of Wear-Resistant Carbide Plate Blanks
속성 | 설명 | 일반적인 값 |
---|---|---|
경도(HRA) | 들여쓰기 및 긁힘에 대한 내성 | 88-95 |
가로 파열 강도(TRS) | 굽힘 힘을 견디는 능력 | 1200 – 2500 MPa |
압축 강도 | Resistance to crushing forces | 4000 - 6000 MPa |
밀도 | 단위 부피당 질량 | 13.5 – 15.0 g/cm³ |
Coefficient of Friction | Resistance to sliding against other materials | 0.1 – 0.3 (depending on mating material) |
내식성 | Ability to withstand chemical attack | Excellent in most environments |
Applications: Where Wear-Resistance Reigns Supreme
A World of Applications, From Mining to Manufacturing
The exceptional wear resistance of carbide plate blanks makes them indispensable across a wide range of industries and applications:
- 광업 및 건설: Carbide plates protect critical components in mining equipment, such as chutes, hoppers, buckets, and cutting edges, from the abrasive forces of rocks, ores, and other harsh materials.
- 석유 및 가스: The extreme pressures and abrasive environments encountered in oil and gas exploration and production demand wear-resistant components. Carbide plates are used in drilling equipment, valves, pumps, and other critical parts to ensure longevity and reliability.
- 발전: Wear-resistant carbide plates are vital in power plants, protecting components in coal pulverizers, ash handling systems, and other areas prone to wear from abrasive particles.
- Metalworking and Forming: Carbide plate blanks are used to create dies, punches, and wear plates in metal forming operations, ensuring precise tolerances and extended tool life.
- Recycling and Waste Management: The abrasive nature of recycled materials makes wear-resistant carbide plates essential for protecting components in shredders, crushers, and other recycling equipment.
Comparing Carbide Plate Blank Suppliers: A Global Perspective
Table 2: Comparison of Wear-Resistant Carbide Plate Blank Suppliers
공급업체 | 위치 | Price Range (per kg, USD) | 스페셜티 |
---|---|---|---|
케나메탈 | 미국 | $80 – $250+ | Wide range of carbide grades, large plate sizes, precision grinding capabilities |
샌드빅 코로만트 | 스웨덴 | $90 – $280+ | Advanced carbide grades, specialized coatings for extreme wear applications |
엘리먼트 식스 | 영국, 글로벌 | $100 – $300+ | Expertise in polycrystalline diamond (PCD) and tungsten carbide solutions for extreme wear |
세라티짓 | 룩셈부르크 | $70 – $220+ | Cost-effective solutions, standard and custom carbide grades, global manufacturing presence |
Tungaloy | 일본 | $85 – $260+ | High-performance carbide grades, tight tolerances, expertise in precision machining |
TRUER | 중국 | $65 – $200+ | High-quality, cost-effective carbide plate blanks; Expertise in geological mining products; Vertically integrated manufacturing with advanced pressing and sintering technology for superior density and wear resistance |
참고: Prices are approximate and can vary significantly based on plate size, grade, quantity, tolerances, surface finish requirements, and other factors.
장점과 한계: 장단점 비교
Table 3: Advantages and Limitations of Wear-Resistant Carbide Plate Blanks
장점 | 제한 사항 |
---|---|
탁월한 내마모성: Significantly extends the lifespan of components subjected to abrasion, erosion, and impact, reducing downtime and maintenance costs | 깨지기 쉬운 자연: Carbide’s high hardness also makes it inherently brittle, making it susceptible to chipping or fracturing under high impact or shock loads |
High Hardness and Strength: Maintains structural integrity and dimensional accuracy even under extreme pressures and abrasive conditions | 비용: Carbide plate blanks typically have a higher initial cost compared to wear-resistant steels or other materials |
다용도성: Available in various grades, sizes, and shapes to meet diverse application requirements | 가공 과제: Machining carbide requires specialized equipment, tooling, and expertise due to its hardness and abrasive nature |
The TRUER Difference: Why Choose Us for Your Wear-Fighting Needs?
- 타협하지 않는 품질: At TRUER, quality is at the forefront of everything we do. We maintain rigorous quality control measures throughout our manufacturing process to ensure that every wear-resistant carbide plate blank meets or exceeds your expectations.
- 수직적 통합: Our vertically integrated manufacturing process, from powder processing to final finishing, allows us to control every aspect of production, ensuring consistent quality and competitive pricing.
- 기술 전문성: Our team of experienced engineers possesses deep knowledge of carbide materials and applications. We work closely with you to understand your specific needs and recommend the optimal carbide grade and plate design for your application.
- 고객 중심 접근 방식: We are committed to providing exceptional customer service and support. Our dedicated team is always available to answer your questions, provide technical assistance, and ensure your complete satisfaction.
Frequently Asked Questions (FAQ)
Addressing Your Wear-Related Concerns
1. What is the typical lifespan of a wear-resistant carbide plate blank?
The lifespan of a carbide plate blank depends on various factors, including the application’s severity, the material being handled, and the operating environment. However, carbide plates typically last 5 to 10 times longer than wear-resistant steels in comparable applications.
2. What is the largest carbide plate size that you can manufacture?
We have the capability to manufacture carbide plates up to 1500 mm x 600 mm in size, with thicknesses ranging from 3 mm to 50 mm.
3. Can you provide carbide plates with custom shapes or hole patterns?
Yes, we offer custom machining services to create carbide plates with specific shapes, hole patterns, and other features to meet your unique application requirements.
4. What is the best way to attach carbide plates to my components?
Carbide plates can be attached using various methods, including brazing, welding, mechanical fastening, or adhesive bonding. The optimal method depends on the specific application and the materials involved.
5. How do I choose the right carbide grade for my wear application?
Selecting the appropriate carbide grade is crucial for optimal performance and longevity. Factors to consider include the type and severity of wear, operating temperature, impact resistance requirements, and corrosion resistance needs. Our engineering team can assist you in selecting the ideal grade for your specific application.