엣지 준비가 중요한 이유 카바이드 플레이트
무딘 칼로 토마토를 썰어본 적이 있나요? 그 끌림, 그 눈물. 이제 수천 RPM으로 작동하며 단단한 금속을 자르는 산업용 공구를 상상해 보세요. 그 가장자리는 제로 오류의 여지가 없습니다. 모든 미크론이 중요한 카바이드 플레이트 가장자리 준비의 세계에 오신 것을 환영합니다.
모서리 준비는 단순히 끝을 연마하는 것이 아니라 일관된 성능, 긴 공구 수명, 정밀한 작업의 비결입니다. 제대로 수행하면 칩핑을 최소화하고 미세 골절을 줄이며 마모에 대한 저항력을 높일 수 있습니다. 경주용 자동차를 튜닝하는 것과 같다고 생각하면 됩니다. 미세 조정이 없으면 마력은 의미가 없습니다.
항공우주 및 자동차부터 광업 및 금속 성형에 이르기까지 카바이드 플레이트는 숨은 영웅입니다. 하지만 모서리에 결함이 있으면 전체 생산 라인에 문제가 생깁니다. 예산이 감당할 수 있는 속도보다 더 빨리 공구를 소진할 수 있습니다.
그렇군요, 엣지 준비는 매우 중요합니다.
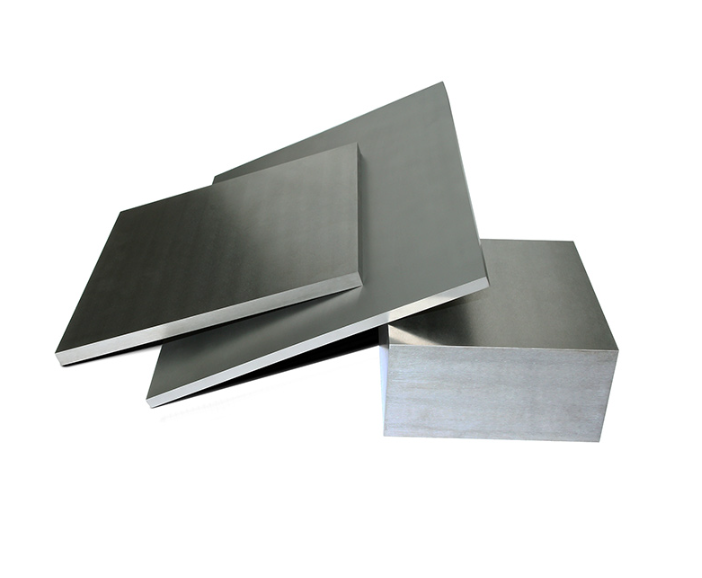
카바이드 플레이트의 일반적인 모서리 준비 기술
여기에는 정답이 없습니다. 올바른 기술은 애플리케이션, 기본 재료 및 성능 사양에 따라 다릅니다. 다음은 가장 많이 사용되는 방법에 대한 안내입니다.
1. 호닝(가장자리 래디얼링)
가장자리에 미니 마사지를 해준다고 상상해 보세요. 호닝은 날카로운 모서리를 둥글게 다듬어 부서짐을 줄여줍니다. 갈라짐이 적고 견고한 절삭날을 원할 때 이상적입니다.
2. 그라인딩
연삭은 재료를 공격적으로 제거하며 일반적으로 대량 모서리 성형에 사용됩니다. 다이아몬드 휠이나 CBN 공구를 사용하면 카바이드에 적합하지만 열 응력으로 인해 잘못하면 위험할 수도 있습니다.
3. 모따기
모따기는 가장자리에 평평한 각진 표면을 만듭니다. 이는 삽입을 유도하고 응력 집중을 줄이는 데 사용됩니다. 가장자리에 절벽이 아닌 '경사로'를 만든다고 생각하면 됩니다.
4. 랩핑
연마 슬러리를 사용하여 미세한 버를 제거하는 초미세 연마로 스파 트리트먼트입니다. 좋은 상태에서 완벽한 상태로 끌어올릴 수 있는 마지막 터치입니다.
5. EDM(방전 가공)
복잡한 형상에 적합한 EDM은 전기 스파크를 사용하여 재료를 기화시킵니다. 하지만 열의 영향을 받는 영역이 남기 때문에 2차 준비가 필요할 수 있습니다.
6. 워터젯 및 레이저 커팅(사전 준비)
정밀한 가장자리 준비가 시작되기 전에 셰이핑의 첫 단계로 자주 사용됩니다. 이렇게 하면 거칠고 딱딱한 가장자리가 남을 수 있으므로 반드시 다듬어야 합니다.
다음용 도구 및 장비 카바이드 플레이트 엣지 준비
카바이드 모서리를 제대로 만들려면 몇 가지 중요한 하드웨어가 필요합니다. 라인업은 다음과 같습니다:
1. CNC 연삭기
적응형 제어 기능이 있는 고속 스핀들은 반복 가능한 정밀도를 보장합니다. ANCA, Walter, Rollomatic과 같은 브랜드가 이곳을 지배하고 있습니다.
2. 엣지 준비 기계(브러시 및 미디어 유형)
연마 브러시, 미디어 흐름 또는 미세 연마 제트를 사용하는 자동화된 시스템. EdgePrep™ 시스템 또는 브러시 연구 도구를 생각해 보세요.
3. 초음파 연마기
고주파 진동을 사용하여 가장자리를 미세 조정합니다. 허용 오차가 좁은 경우에 적합합니다.
4. 래핑 및 연마 테이블
최종 마무리에 이상적입니다. 연마 슬러리가 있는 회전판을 사용하여 유리와 같은 광택을 얻습니다.
5. 현미경 및 프로파일 측정 도구
측정이 중요합니다. 레이저 프로파일로미터, 주사전자현미경, 광학 현미경은 정밀한 준비를 보장합니다.
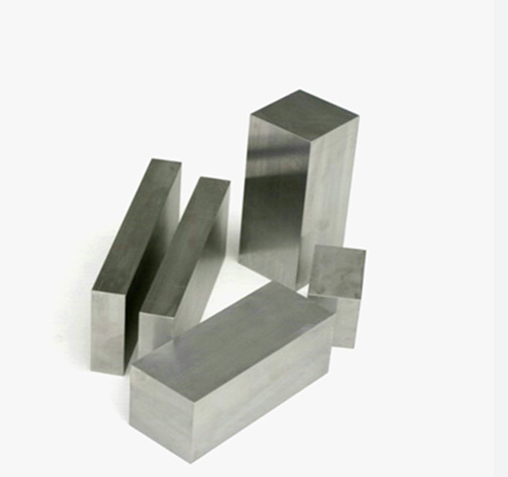

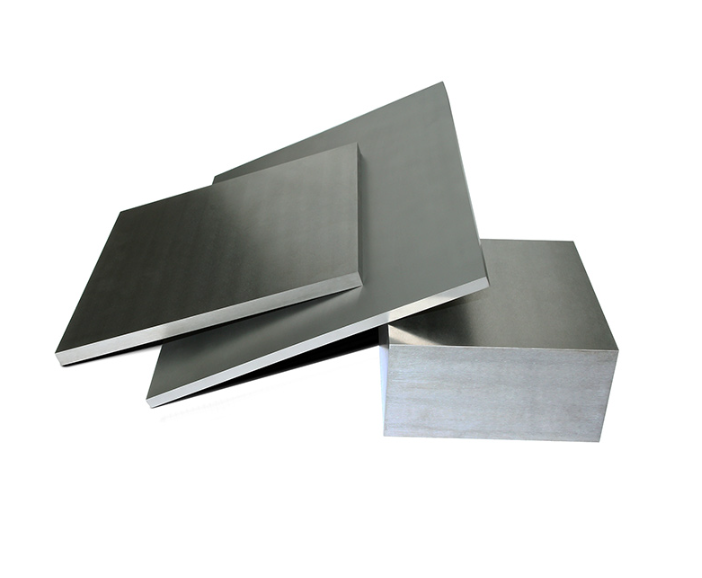
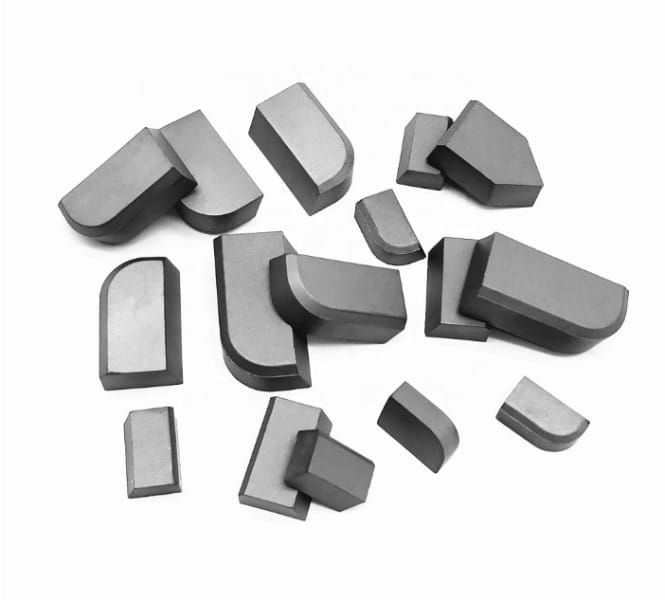
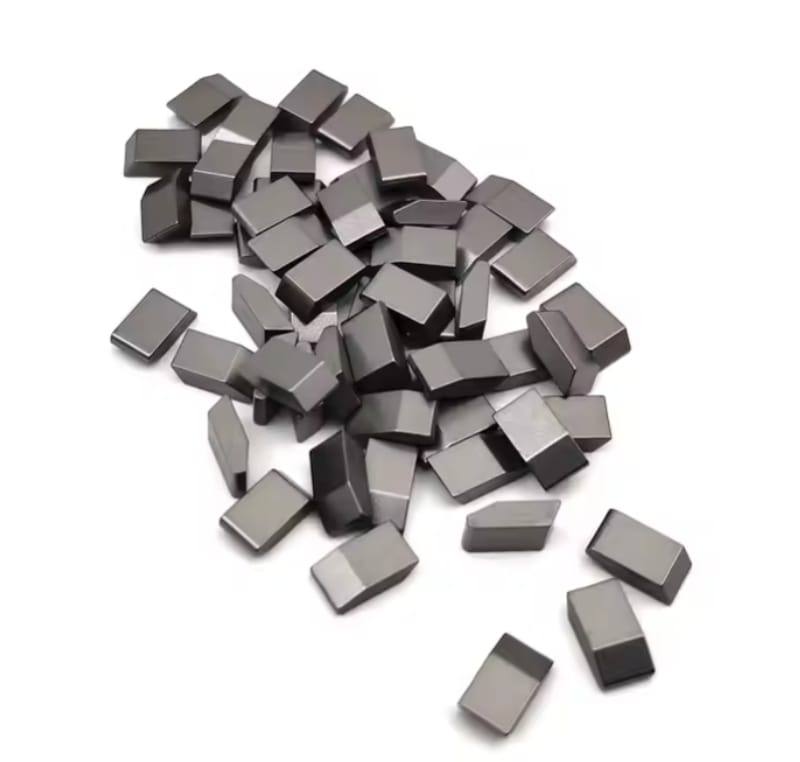
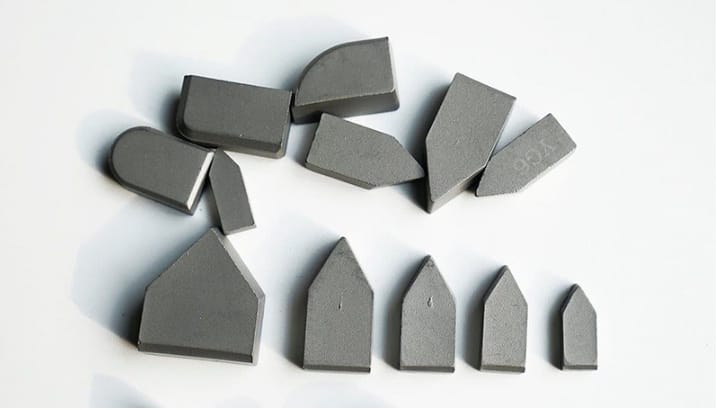
카바이드 플레이트 모서리 준비를 위한 모범 사례 및 팁
팁/베스트 프랙티스 | 설명 | 중요한 이유 |
---|---|---|
일관된 압력 유지 | 준비 중 압력을 표준화하여 고르지 않은 가장자리를 방지합니다. | 공구 잡음 및 고르지 않은 마모 방지 |
냉각수 또는 윤활유 사용 | 열 손상을 줄이기 위한 연삭 또는 랩핑 중 | 미세 균열을 최소화하고 카바이드 무결성을 보존합니다. |
에지 형상을 애플리케이션에 맞추기 | 정삭용은 날카롭게, 황삭용은 둥글게 | 효율성 및 기대 수명 향상 |
현미경으로 자주 검사하기 | SEM 또는 광학 도구를 사용한 정기 점검 | 결함 조기 발견, 비용 절감 |
올바른 연마재 선택 | 카바이드용 다이아몬드, 산화 알루미늄 피하기 | 경도와 광택 유지 |
가능한 경우 자동화 | CNC와 로봇 공학을 사용하여 사람의 실수를 방지하세요. | 반복성과 생산성 제공 |
모든 준비 단계 후 청소 | 다음 단계에서 파편이 표면에 박힐 수 있습니다. | 오염 및 표면 아래 결함 방지 |
품질 관리 및 테스트 카바이드 플레이트 엣지 준비
뿐만 아니라 외모. 카바이드 엣지 준비의 품질 관리는 압력 하에서 성능을 파헤칩니다. 지금 얘기 중입니다:
- 표면 무결성 분석: SEM(주사 전자 현미경)을 사용하여 미세 균열을 감지합니다.
- 가장자리 반경 측정: 레이저 기반 도구는 미크론 이하의 정밀도까지 측정합니다.
- 경도 테스트: 미세 경도 테스터는 열처리로 인해 카바이드가 약화되지 않았는지 확인합니다.
- 현장 시뮬레이션 테스트: 테스트 리그에서 마모 및 하중 조건을 시뮬레이션하여 실제 내구성을 확인합니다.
여기서 QC에 실패하면 가장자리 불량, 불량품 발생, 심지어 라인에서 공작물 손상이 발생할 수 있습니다. 기본적으로 이 단계를 건너뛰면 안 됩니다!
카바이드 판재 모서리 준비의 응용 분야 및 산업 사례
카바이드 플레이트는 단순한 실험실의 호기심이 아닙니다. 어디서나 업계에서. 완벽한 엣지 준비는 여기서 빛을 발합니다:
1. 항공우주
터빈 블레이드 가공은 엄청난 RPM에서 가장자리 안정성이 요구됩니다. 준비가 잘못되었다고요? 치명적인 고장이 발생할 수 있습니다.
2. 자동차
정밀 펀칭 금형과 절삭 공구는 경화 카바이드 모서리에 의존합니다. 작은 결함도 대량 생산에서는 큰 결함을 유발할 수 있습니다.
3. 금속 스탬핑 및 성형
모서리는 매우 중요합니다. 굴곡이 있고 스트레스를 완화하는 가장자리가 부서지기 쉬운 가장자리보다 더 나은 성능을 발휘합니다.
4. 석유 및 가스
다운홀 공구에서 완벽한 모서리를 가진 카바이드 인서트는 극한의 압력과 마모를 견뎌냅니다.
5. 전자 제품 제조
미세 공차 모서리가 있는 다이 컷 도구는 정밀 회로를 제작하는 데 사용됩니다.
금속 분말 모델 사용 분야 카바이드 플레이트: 비교 및 설명
금속 분말 모델 | 설명 | 사용 사례 | 장점 | 단점 |
---|---|---|---|---|
WC-Co (10% Co) | 10% 코발트 바인더를 사용한 클래식 텅스텐 카바이드 | 범용 절삭 공구 | 강력하고 균형 잡힌 성능 | 중간 수준의 내식성 |
WC-Co(6% Co) | 낮은 코발트 함량, 높은 경도 | 마감 공구, 마모 부품 | 더 단단한 가장자리, 더 강한 내마모성 | 충격에 덜 견딤 |
WC-Ni | 코발트 대신 니켈 바인더 | 해양 또는 식품 도구와 같은 부식성 환경 | 부식 방지 | 코발트보다 약한 결합력 |
WC-TiC-Co | 내열성 강화를 위한 티타늄 카바이드 첨가제 | 항공 우주와 같은 고온 애플리케이션 | 고온 강도 | 비싸고, 준비하기 더 어렵습니다. |
WC-TaC-Co | 탄탈 카바이드로 인성 향상 | 무거운 충격 도구 | 주기적인 부하에도 강함 | 낮은 내마모성 |
서브마이크론 WC-Co | 가장자리 유지를 위한 초미세 입자 | 마이크로 드릴, PCB 툴링 | 탁월한 엣지 선명도 | 생산 비용 증가 |
나노 입자 WC-Co | 서브미크론보다 더 미세한 입자 크기 | 고정밀 의료 도구 | 탁월한 내마모성 | 매우 비싸다 |
Cr3C2 강화 화장실 | 내마모성 및 내산화성을 위한 크롬 카바이드 보강재 | 채굴, 시추 | 산화 및 부식 방지 | 더 부서지기 쉬울 수 있습니다. |
WC-Co-Cr | 강도와 내식성을 위한 3중 바인더 단계 | 석유 및 가스, 해양 산업 | 뛰어난 멀티 역할 내구성 | 연마 및 연마가 더 어렵습니다. |
Fe 기반 서멧 | 철 기반 매트릭스를 사용한 저렴한 대안 | 비용에 민감한 산업용 툴링 | 경제적이고 괜찮은 성능 | 전반적인 경도 감소 |
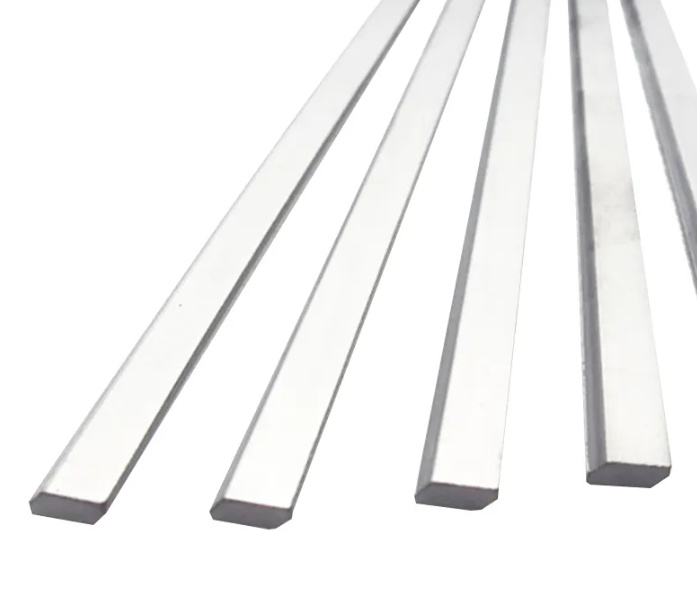
자주 묻는 질문
질문 | 답변 |
---|---|
카바이드 공구에 이상적인 모서리 반경은 얼마입니까? | 용도에 따라 다르지만 일반적으로 정삭 공구의 경우 15~25µm, 황삭 공구의 경우 최대 100µm가 일반적입니다. |
카바이드 플레이트를 수작업으로 준비할 수 있나요? | 기술적으로는 맞지만 일관성이 없고 산업 정밀도에는 적합하지 않습니다. |
에지 프리프가 공구 수명에 큰 영향을 미치는 이유는 무엇일까요? | 준비 상태가 좋지 않으면 스트레스 라이저가 발생하여 균열, 칩이 생기고 하중을 받으면 마모가 빨라집니다. |
엣지 준비 품질은 어떻게 측정하나요? | 레이저 프로파일 측정, SEM 및 경도 테스트를 사용합니다. 반복성과 반경 제어가 핵심입니다. |
연마보다 연삭이 더 낫나요? | 연마는 미세한 마무리를 위해 더 좋으며, 연삭은 모양을 만드는 데 필요합니다. 상황에 따라 다릅니다! |
마모된 카바이드 엣지를 다시 준비할 수 있나요? | 예, 하지만 마모로 인해 구조가 손상되지 않은 경우에만 해당됩니다. 다시 준비하면 공구 수명이 연장될 수 있습니다. |
엣지 준비가 가장 어려운 소재는 무엇인가요? | 나노 입자 탄화물과 TiC 강화 합금은 매우 단단하며 특수 공구가 필요합니다. |
코발트 바인더는 독성이 있나요? | 코발트는 분말 형태로 위험할 수 있습니다. 취급 시 적절한 PPE와 환기가 중요합니다. |
연삭 시 냉각 유체가 중요합니까? | 당연하죠. 과열을 방지하고 구조적 무결성을 보존합니다. |
가장 큰 엣지 준비 실수는 무엇인가요? | 가장자리를 과도하게 연마하거나 과열하여 미세 골절이 발생하는 경우. |