카바이드 플레이트 금형은 현대 제조업의 숨은 영웅입니다. 탁월한 강도, 내구성, 정밀성 덕분에 정밀 금형이 중요한 산업에서 없어서는 안 될 필수품입니다. 카바이드 플레이트가 왜 그렇게 필수적인지 궁금하거나 필요에 가장 적합한 옵션을 찾고 계신다면 잘 찾아오셨습니다. 인사이트, 비교, 전문가 팁으로 가득한 이 종합 가이드를 자세히 살펴보세요.
금형용 카바이드 플레이트는 무엇입니까?
다이용 카바이드 플레이트는 텅스텐 카바이드 분말과 바인더(주로 코발트 또는 니켈)를 혼합하여 만든 평평한 직사각형 소재입니다. 고온과 고압에서 소결하여 매우 단단하고 내마모성이 뛰어난 소재를 만듭니다. 간단히 말해, 이 플레이트는 극심한 스트레스, 열, 마모를 견딜 수 있도록 설계되어 금형 제작 공정에서 다른 재료를 성형하거나 절단하는 데 완벽합니다.
카바이드 플레이트는 다이의 '갑옷'이라고 생각하면 됩니다. 일반 강철 금형은 단단한 재료를 절단할 때 빠르게 마모되지만 카바이드는 인성이 뛰어나 공구 수명이 길고 성능이 향상됩니다. 스탬핑에서 압출에 이르기까지 다양한 용도로 사용되는 초경 플레이트는 전 세계 산업에 혁명을 일으켰습니다.
카바이드 플레이트의 주요 특징
- 경도: 텅스텐 카바이드는 경도가 다이아몬드에 이어 두 번째로 높습니다.
- 내마모성: 거친 환경을 견디면 더 오래 사용할 수 있습니다.
- 열 안정성: 극심한 더위 속에서도 무결성을 유지합니다.
- 내식성: 까다로운 환경에서 사용하기에 이상적입니다.
- 정확성: 일관되게 선명하고 깔끔한 커팅을 제공합니다.
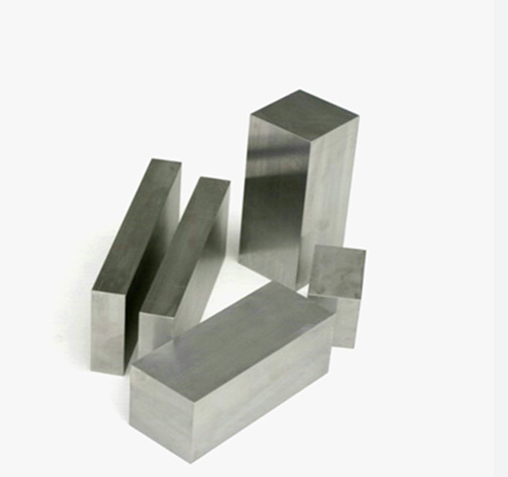
사용 상위 산업 카바이드 플레이트 다이용
카바이드 플레이트는 여러 산업에서 중요한 역할을 합니다. 다양한 분야에서 초경판의 고유한 특성을 어떻게 활용하는지 살펴보겠습니다.
1. 자동차 산업
자동차 업계에서는 정밀도가 가장 중요합니다. 카바이드 플레이트는 기어, 섀시 부품, 엔진 부품과 같은 부품을 스탬핑하고 절단하는 데 사용됩니다. 내구성이 뛰어나 다운타임을 최소화하고 일관된 품질을 보장합니다.
2. 항공우주 분야
항공기 제조업체의 경우 카바이드 플레이트는 가볍지만 내구성이 뛰어난 부품을 제작하는 데 필수적입니다. 티타늄 및 인코넬과 같은 이색 합금을 절단하는 데 필수적입니다.
3. 전자 제품 제조
작은 전자 부품은 정밀 가공이 필요합니다. 카바이드 플레이트는 회로 기판 및 기타 전자 부품에 복잡한 모양과 패턴을 만드는 데 도움이 됩니다.
4. 공구 및 금형 산업
이 산업은 플라스틱, 금속 및 복합재와 같은 재료를 성형하기 위한 금형과 금형을 만드는 데 카바이드 플레이트에 크게 의존합니다.
5. 석유 및 가스
드릴링 작업의 열악한 조건을 견디는 초경 플레이트는 극한의 경도와 내마모성이 요구되는 공구에 사용됩니다.
금형 적용을 위한 카바이드 플레이트의 5가지 주요 이점
이점 | 설명 |
---|---|
탁월한 내구성 | 마모와 손상을 견뎌내 교체 빈도를 줄여줍니다. |
정밀 성능 | 중요도가 높은 애플리케이션에 일관된 품질을 보장합니다. |
비용 효율적 | 수명이 길어지면 장기적으로 비용이 절감됩니다. |
내열성 | 금속 성형과 같은 고온 애플리케이션에 이상적입니다. |
다용도성 | 다양한 재료와 산업에 적합합니다. |
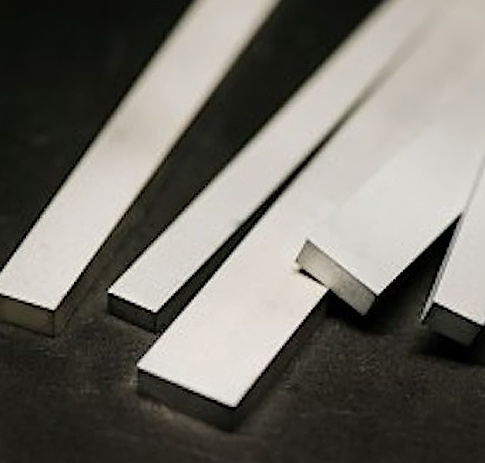
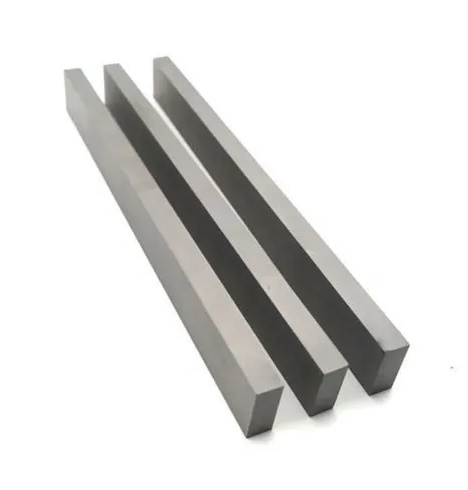
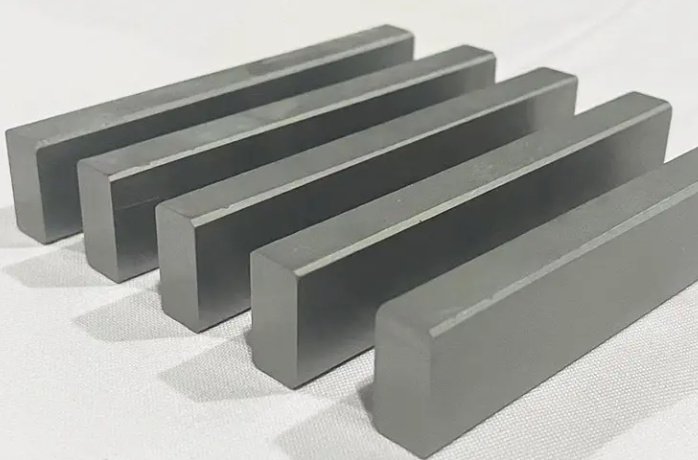
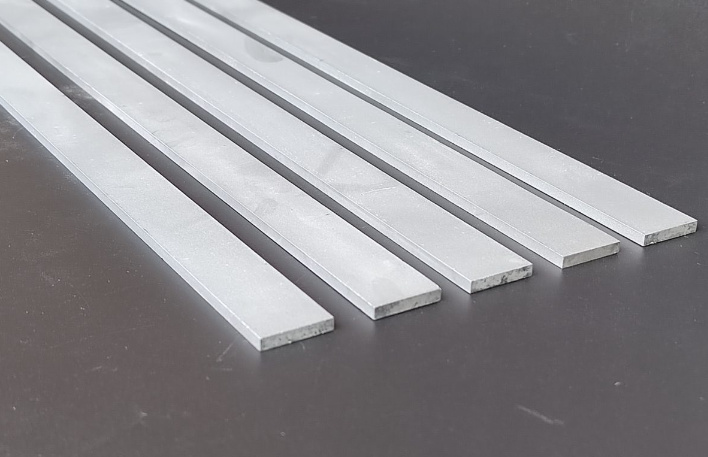
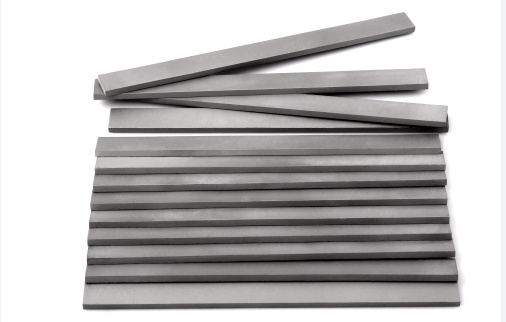
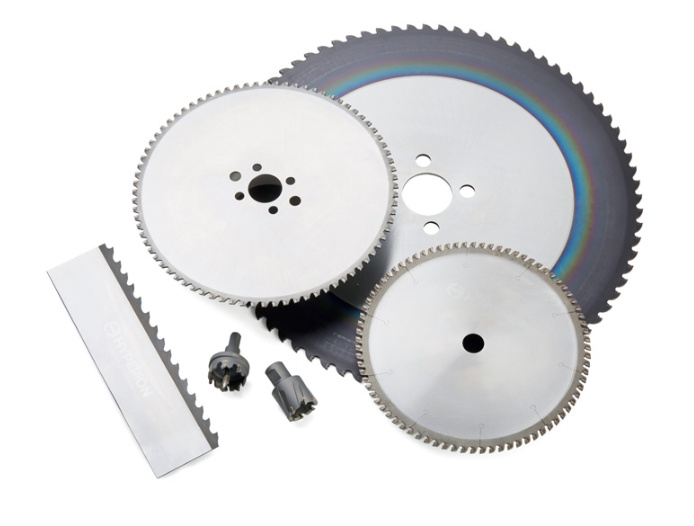
최고를 선택하는 방법 카바이드 플레이트 다이 요구사항에 맞는
올바른 카바이드 플레이트를 선택하는 것은 단순히 첫눈에 보이는 것을 고르는 것이 아닙니다. 특정 요구 사항을 이해하고 이를 적합한 소재와 일치시키는 것이 중요합니다. 다음은 몇 가지 주요 고려 사항입니다:
1. 재료 구성
카바이드 플레이트는 텅스텐 카바이드 함량과 바인더 재료에 따라 다양한 등급으로 제공됩니다. 높은 정밀도와 내마모성을 원한다면 텅스텐 카바이드 함량이 높은 플레이트(90% 이상)를 선택하세요.
2. 신청 요건
절단, 스탬핑 또는 압출을 하시나요? 공정마다 다른 등급이 필요합니다. 충격이 큰 애플리케이션의 경우 인성이 높은 플레이트가 필수적입니다.
3. 플레이트 두께 및 크기
플레이트의 치수가 툴링 설정과 일치하는지 확인하세요. 플레이트의 크기가 너무 크거나 작으면 비효율적이거나 장비가 손상될 수 있습니다.
4. 표면 마감
광택 마감 처리된 플레이트는 특히 정밀 애플리케이션에서 마찰을 줄이고 성능을 향상시킵니다.
5. 예산 대 성능
카바이드 플레이트는 투자가 필요하지만 내구성이 뛰어나 초기 비용을 정당화할 수 있는 경우가 많습니다. 초기 비용 대비 장기적인 이점을 비교해 보세요.
금형용 카바이드 플레이트의 미래
기술 발전에 따라 카바이드 플레이트는 점점 더 좋아지고 있습니다. 적층 제조 및 나노 구조 탄화물과 같은 새로운 제조 기술로 인해 카바이드 플레이트의 특성이 향상되고 있습니다.
- 향상된 내마모성: 나노 기술을 통해 경도와 내마모성이 훨씬 뛰어난 카바이드 플레이트의 생산이 가능해졌습니다.
- 지속 가능한 관행: 텅스텐 카바이드를 재활용하여 환경 발자국을 줄이려는 노력이 증가하고 있습니다.
- 맞춤형 솔루션: 고급 CNC 가공을 통해 제조업체는 특정 요구 사항에 맞는 카바이드 플레이트를 제작할 수 있습니다.
향후 10년 동안 정밀 제조의 중요성이 점점 더 커짐에 따라 초경 판재가 더 많은 산업 분야를 지배할 것으로 예상됩니다.
의 장점과 한계 비교 카바이드 플레이트 다이용
측면 | 장점 | 제한 사항 |
---|---|---|
경도 | 매우 단단하고 마모와 변형에 강합니다. | 극심한 충격에 약해질 수 있습니다. |
비용 | 내구성으로 인한 장기적인 비용 절감. | 강철 대체재에 비해 초기 비용이 높습니다. |
열 안정성 | 높은 열에서도 잘 작동합니다. | 가공을 위한 특수 장비가 필요합니다. |
내식성 | 열악한 환경에서도 탁월한 성능을 발휘합니다. | 극한 환경에서는 보호 코팅이 필요할 수 있습니다. |
사용자 지정 기능 | 다양한 등급과 크기로 제공됩니다. | 부드러운 소재에 비해 유연성이 제한적입니다. |
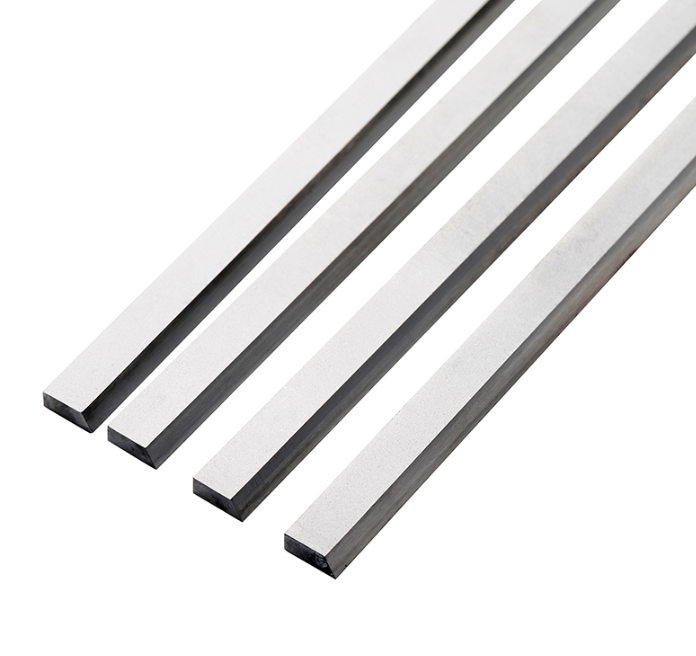
자주 묻는 질문
질문 | 답변 |
---|---|
카바이드 플레이트의 수명은 어떻게 되나요? | 사용법에 따라 강판보다 5~10배 더 오래 사용할 수 있습니다. |
카바이드 플레이트는 재활용이 가능한가요? | 예, 텅스텐 카바이드는 재활용하여 새 제품에 재사용할 수 있습니다. |
카바이드 플레이트는 어떻게 관리하나요? | 정기적으로 청소하고 심한 충격을 피하면 수명을 연장할 수 있습니다. |
카바이드 플레이트는 모든 재료에 사용할 수 있나요? | 예, 하지만 등급은 처리 중인 자료와 일치해야 합니다. |
텅스텐 카바이드와 강철의 차이점은 무엇인가요? | 텅스텐 카바이드는 훨씬 더 단단하고 내마모성이 뛰어납니다. |