제조, 금형 및 절삭 공구에서 카바이드 플레이트의 일반적인 응용 분야
카바이드 플레이트 는 중장비 작업, 절삭 공구, 금형 및 금형 제작, 마모 부품, 항공우주 정밀 부품에 필수적인 소재입니다. 타의 추종을 불허하는 경도, 열과 마모에 대한 저항성, 뛰어난 수명 덕분에 고성능 산업용 부품에 가장 많이 사용되는 소재입니다.
금형, 특히 사출 금형과 다이캐스팅 공구에서 카바이드 플레이트는 서비스 수명을 연장하고 유지보수로 인한 가동 중단 시간을 줄이는 데 도움이 됩니다. CNC 공구, 톱날 또는 선반 인서트와 같은 절삭 분야에서는 뜨거운 칼로 버터를 자르듯 금속을 절단합니다.
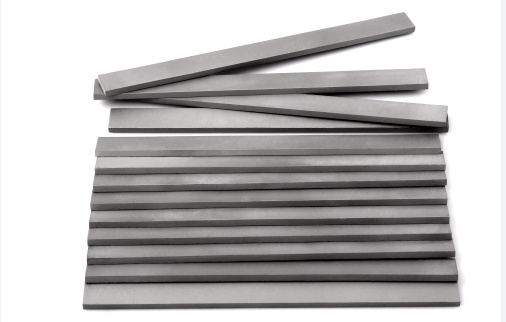
이란 무엇인가요? 카바이드 플레이트?
카바이드 플레이트는 주로 다음 재료로 만든 평평한 부품입니다. 텅스텐 카바이드(WC)를 코발트(Co)와 같은 바인더 금속과 혼합하는 경우가 많습니다. 이 화합물은 다음과 같은 물질을 만듭니다. 손톱보다 단단한-말 그대로입니다. 텅스텐 카바이드는 모스 척도에서 다이아몬드에 가까운 등급으로, 상업적으로 가장 단단한 소재 중 하나입니다.
진정한 마법은 이 플레이트가 제조되는 방식에서 비롯됩니다. 금속 분말(자세한 내용은 나중에 설명)을 엄청난 압력으로 압축한 다음 고온에서 소결합니다. 결과는? 밀도가 높고 거의 깨지지 않으며 산업 수준의 스트레스에도 끄떡없이 견딜 수 있는 플레이트가 탄생합니다.
디자인 최적화가 중요한 이유
카바이드 덩어리를 기계에 밀어 넣는 것만으로는 의도한 대로 절단할 수 없습니다. 설계 최적화는 카바이드 플레이트가 최고의 성능을 발휘할 수 있도록 하는 비결입니다.
카바이드 플레이트의 디자인을 최적화할 수 있습니다:
- 스트레스 상황에서 성능 향상
- 도구 수명 연장
- 장애율 및 칩핑 감소
- 제조 비용 절감
- 에너지 효율성 향상
최적화를 하지 않으면 포뮬러 1 엔진을 장바구니에 넣는 것과 같습니다. 물론 잠시 동안은 작동할지 모르지만 금방 망가지고 엄청난 리소스를 낭비하게 될 것입니다.
최적화를 통해 엔지니어는 카바이드 플레이트에 가장 적합한 모양, 구성, 두께 및 적용 방법을 결정할 수 있습니다. 여기에는 형상 조정, 분말 혼합 비율 조정, 바인더 분산 개선, 레이어 코팅 추가 등이 포함될 수 있습니다.
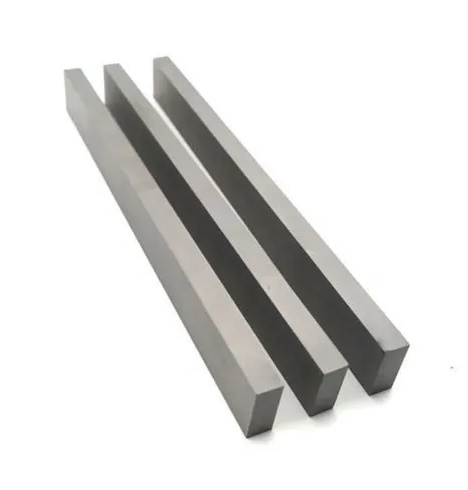
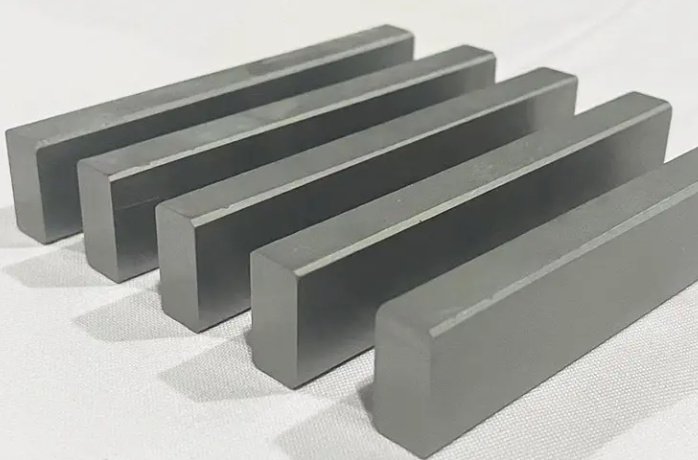
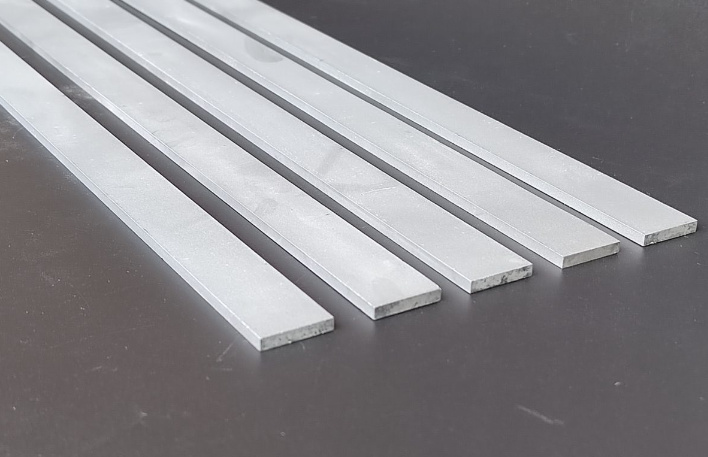
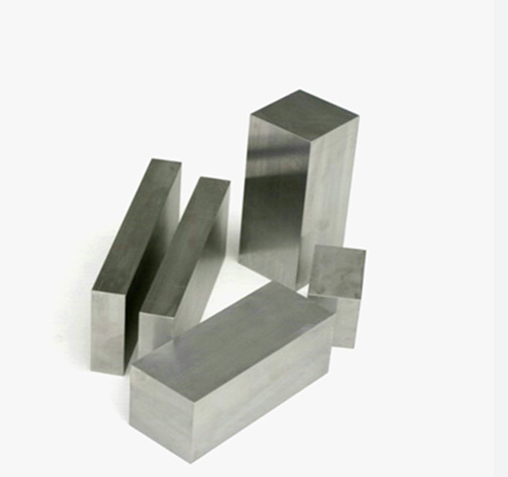

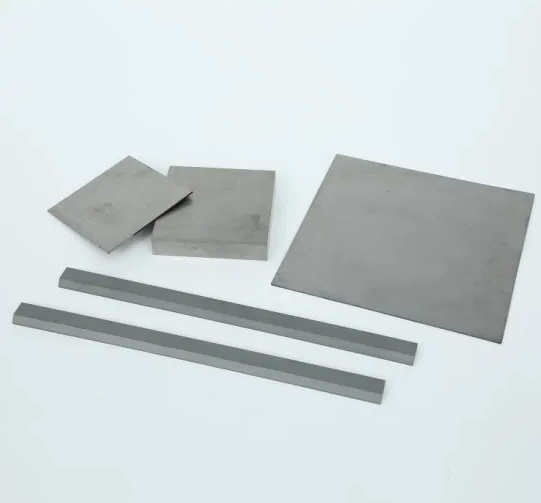
카바이드 플레이트 설계 최적화의 핵심 요소
아래 표는 각 항목의 핵심 파라미터와 이들이 카바이드 플레이트 성능에 미치는 영향.
주요 디자인 고려 사항과 그 영향
팩터 | 중요한 이유 | 최적화 전략 |
---|---|---|
판재 두께 및 치수 | 어셈블리의 응력 저항 및 피팅에 영향을 미칩니다. | 부하 분포 및 애플리케이션 지오메트리와 크기 일치 |
파우더 구성 | 경도, 인성, 내식성에 영향을 미칩니다. | 여러 파우더 블렌딩, WC와 바인더 함량 균형 맞추기 |
소결 조건 | 입자 크기, 다공성 및 결합에 영향을 미칩니다. | 시간/온도 균형 최적화, 압력 소결 사용 |
코팅 또는 표면 처리 | 마모, 마찰, 부식 감소 | PVD, CVD 코팅 적용, 윤활 또는 부식 방지 마감 추가 |
기하학 및 도형 | 부하 분배 및 절단 효율 결정 | 응력 분포를 위한 FEM 시뮬레이션을 통한 설계 |
냉각 및 열 관리 | 열 스트레스를 받는 공구 수명에 미치는 영향 | 냉각수 채널 또는 방열 레이어 통합 |
애플리케이션별 부하 | 피로 수명 및 골절 지점 결정 | 실제 기계 부하 시나리오 모델링 |
입자 크기 제어 | 입자가 작을수록 강도가 높아지고 입자가 클수록 인성이 높아집니다. | 우선순위인 강도 대 내충격성을 기준으로 입자 크기 선택 |
바인더 상 균질성 | 분산 불량으로 인한 약점 및 균열 발생 | 고에너지 볼 밀링 및 균일한 소결 기술 사용 |
인서트/툴과의 호환성 | 잘 맞지 않으면 잡음, 정렬 불량 또는 공구 파손의 원인이 됩니다. | 완벽한 결합 형상을 위한 공구 설계와 조정 |
최적화된 사례 연구 및 적용 사례 카바이드 플레이트 디자인
고속 CNC 가공 공구 제조업체
독일의 한 공구 회사는 선반 공구에 표준 텅스텐 카바이드 플레이트를 사용했습니다. 하지만 공구 마모율이 빠르게 증가하는 것을 발견했습니다. 이 회사는 미세한 WC 입자 구조, 코발트 바인더 및 TiAlN 코팅이 적용된 최적화된 카바이드 플레이트 설계로 전환했습니다. 결과는? 공구 수명이 40% 증가하고 절삭 속도가 25% 향상되었습니다.
자동차 부품용 몰드 베이스 공급업체
아시아의 한 금형 제조업체는 스탬핑 다이 베이스에서 조기 고장을 경험했습니다. FEM 시뮬레이션 분석과 공급업체와의 협업을 통해 레이어 복합 구조의 맞춤형 초경판을 구현했습니다. 새로운 설계는 균열을 방지하고 공구 수명을 2배로 연장했습니다.
초경판용 설계 소프트웨어, 시뮬레이션 기술 및 협력 공급업체 선정
카바이드 플레이트 설계의 디지털 시대에 오신 것을 환영합니다. 이제 추측과 작별하고 정밀도와 인사하세요. 오늘날 엔지니어들은 첨단 CAD/CAM 소프트웨어, 유한 요소법(FEM) 시뮬레이션및 머티리얼 프로퍼티 데이터베이스 를 사용하여 디자인을 생산에 적용하기 전에 가상으로 테스트할 수 있습니다.
인기 도구 포함:
- 오토데스크 퓨전 360 - CAD/CAM과 제너레이티브 디자인을 결합하여 레이아웃을 최적화합니다.
- 앤시스 메카니컬/컴솔 멀티피직스 - 열, 구조 및 피로 시뮬레이션에 이상적입니다.
- JMatPro 및 Thermo-Calc - 온도/압력 하에서 위상 다이어그램 및 재료 거동을 모델링하는 데 사용됩니다.
협업의 힘을 과소평가하지 마세요. 전문 파트너와의 파트너십 분말 야금 공급업체 그리고 코팅 제공업체 큰 차이를 만들 수 있습니다. 신뢰할 수 있는 파트너가 올바른 파우더 블렌드를 선택하고 열처리 일정을 제안하며 맞춤형 소결 프로그램을 공동 개발할 수 있도록 도와드립니다.
10가지 이상의 특정 금속 분말 모델에 사용됨 카바이드 플레이트 프로덕션
괴짜가 되어 봅시다. 다음은 다음과 같습니다. 가장 일반적으로 사용되는 12가지 금속 분말 모델 카바이드 플레이트의 경우 설명과 함께 제공됩니다:
파우더 모델 | 주요 용도 | 속성 | 장점 | 최상의 대상 |
---|---|---|---|---|
WC-10Co | 표준 도구 제작 | 단단하고 적당한 인성 | 균형 잡힌 내마모성 | 일반 가공 |
WC-6Co | 마무리 도구 | 더 높은 경도 | 엣지 유지력 향상 | 고속 도구 |
WC-Ni | 부식이 발생하기 쉬운 영역 | 코발트 프리 | 비자기성, 부식 방지 | 화학 및 식품 가공 |
WC-TiC-Co | 연마 애플리케이션 | 강화된 경도 | 내마모성 우수 | 채굴 및 드릴링 도구 |
WC-12Co | 내충격성 | 높은 인성 | 충격 흡수 | 단조 금형 |
WC-Cr3C2-Ni | 고온 설정 | 열 저항 | 뜨거운 상태에서도 경도 유지 | 항공 우주 터빈 |
WC-Co+VC(바나듐) | 균열 저항 | 곡물 정제 첨가제 | 골절 인성 향상 | 박판 및 인서트 |
WC-Co-TaC | 사용자 지정 블렌드 | 높은 강도 및 가장자리 내구성 | 균형 잡힌 성능 | 밀 커터 |
WC-Co-Mo | 실험 도구 | 몰리브덴 바인더 | 세밀한 입자 구조 | 마이크로 드릴 |
WC-NiCr | 열악한 환경 | 높은 내식성 및 내마모성 | 비코발트 옵션 | 석유 및 가스 툴링 |
WC-Co-Al | 경량 요구 사항 | 약간의 무게 감소 | 강점과의 트레이드 오프 | 경금속 성형 |
WC-Co-ZrC | 극한의 마모 | ZrC로 강화 | 탁월한 내마모성 | 건식 가공 |
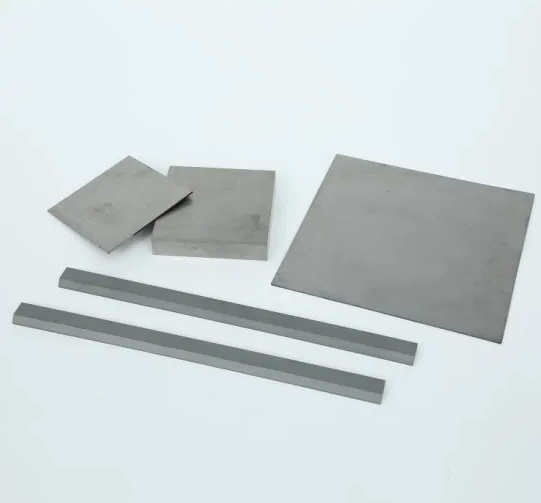
자주 묻는 질문
질문 | 답변 |
---|---|
일반적으로 사용하기에 이상적인 카바이드 구성은 무엇인가요? | WC-10Co는 대부분의 용도에 가장 적합한 경도와 인성의 균형으로 널리 알려져 있습니다. |
코팅은 카바이드 플레이트를 어떻게 개선하나요? | TiAlN 또는 DLC와 같은 코팅은 마찰, 마모, 열 축적을 줄여 수명을 연장합니다. |
가장 큰 디자인 실수는 무엇인가요? | 부하 시 열팽창 및 기계적 응력을 고려하지 않습니다. 항상 먼저 시뮬레이션하세요. |
카바이드 플레이트를 재사용하거나 재연마할 수 있나요? | 예, 많은 플레이트는 다시 연마하거나 재코팅할 수 있지만 원래의 무결성이 손상되지 않도록 해야 합니다. |
코발트는 항상 필요한가요? | 부식이 발생하기 쉬운 환경이나 건강상의 문제를 해결하기 위해 No-Ni 및 NiCr을 대체할 수 있습니다. |
시뮬레이션에 가장 적합한 소프트웨어는 무엇인가요? | 특히 열 및 기계적 하중을 고려한 물리적 시뮬레이션의 표준은 ANSYS와 COMSOL입니다. |
올바른 공급업체를 선택하려면 어떻게 해야 하나요? | 파우더, 디자인, 소결, 코팅 등 전체 스펙트럼을 지원하는 파트너를 찾아보세요. |
친환경 카바이드 옵션이 있나요? | 예, 제조업체는 재활용 화장실 및 저탄소 대체품을 실험하고 있습니다. |