왜 카바이드 로드 항공우주 합금에 이상적
이제 이야기의 주인공인 카바이드 로드에 대해 이야기해 보겠습니다. 가공 분야의 특수 작전 팀이라고 상상해 보세요. 이 드릴 비트는 일반적인 드릴 비트가 아니라 전투용으로 설계되었으며, 특히 가장 거친 항공우주 합금에 맞설 수 있도록 설계되었습니다.
이 막대에 사용되는 소재인 텅스텐 카바이드는 다이아몬드 다음으로 지구상에서 가장 단단한 물질 중 하나입니다. 텅스텐과 탄소를 초고온에서 혼합하여 매우 단단하고 내마모성이 뛰어난 화합물을 형성하여 만들어집니다.
하지만 무엇이 이들을 게임 체인저로 만들까요?
- 뛰어난 경도: 티타늄 및 인코넬과 같은 잘 녹지 않는 항공우주 합금을 절단하는 데 적합합니다.
- 내열성: 카바이드는 더 차갑고 더 오래 유지됩니다. 즉, 공구 마모가 적고 더 정밀한 절삭이 가능합니다.
- 치수 안정성: 카바이드 막대는 높은 응력에서도 챔피언처럼 모양을 유지합니다.
- 더 길어진 공구 수명: 초경 공구는 HSS(고속강)에 비해 최대 10배 더 오래 사용할 수 있습니다.
따라서 제트 엔진 블레이드를 정밀 밀링하거나 방열 브래킷을 보링 가공할 때 카바이드 봉은 단순히 살아남는 것이 아니라 번창합니다.
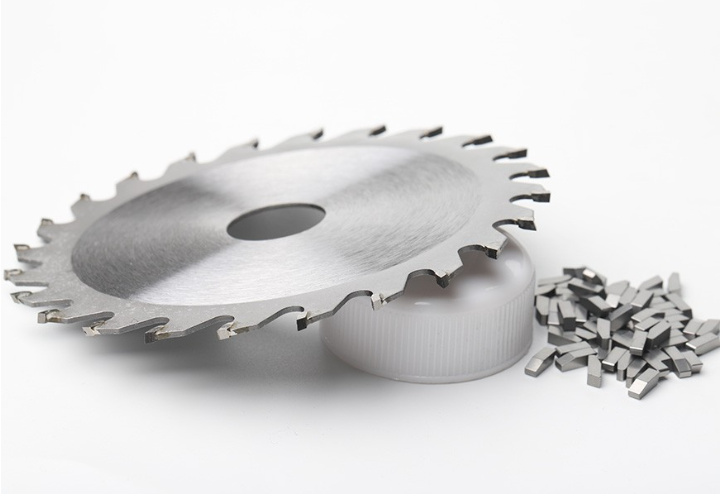
올바른 선택 카바이드 로드 항공우주 합금용
올바른 카바이드 막대를 선택하는 것은 단순히 선반에서 가장 단단한 막대를 고르는 것이 아닙니다. 합금, 가공 공정, 최종 목표를 파악하는 것이 중요합니다. 다음은 몇 가지 핵심 요소입니다:
1. 학년 구성
카바이드 막대는 코발트 함량과 입자 크기에 따라 다양한 등급으로 제공됩니다.
- 서브미크론 입자: 티타늄 및 니켈 합금의 고속 마감에 가장 적합합니다.
- 초미세 입자: 공차가 좁은 드릴링 및 밀링 작업에 적합합니다.
2. 코팅
코팅은 갑옷과 같다고 생각하세요. 코팅된 막대는 열과 산화에 대한 저항력이 더 뛰어납니다.
- TiAlN(질화 티타늄 알루미늄): 고속 건식 가공에 탁월합니다.
- TiCN(탄화 티타늄): 중단된 컷을 위한 더 견고한 코팅.
3. 애플리케이션 유형
- 드릴링: 강성을 높여서 휘어짐을 방지하세요.
- 밀링: 측면 응력을 견딜 수 있는 균형 잡힌 막대를 선택합니다.
- 선회: 진동 감쇠가 뛰어난 막대가 필요합니다.
4. 공차 및 직진성
항공우주 분야에서는 정밀도가 중요합니다. h6 이상의 공차를 가진 막대를 선택하세요. 차이가 있습니다.
항공우주 응용 분야에 사용되는 카바이드 로드용 특정 금속 분말 모델
여기서부터 괴상한 이야기가 시작됩니다. 이러한 특정 카바이드 분말 모델은 항공 우주 툴링의 중추입니다. 각각 고유한 기능을 제공합니다.
파우더 모델 | 구성 세부 정보 | 최상의 용도 | 속성 |
---|---|---|---|
WC-Co 10% 서브마이크론 | 90% 텅스텐 카바이드, 10% 코발트 | 일반 항공우주 합금 절단 | 높은 내마모성, 우수한 인성 |
WC-Co 6% 울트라파인 | 94% WC, 6% Co | 티타늄 합금 마감 | 높은 가장자리 유지력, 미세한 표면 마감 |
WC-CoCr 12% | 88% WC, 10% Co, 2% Cr | 인코넬과 같은 고온 합금 | 향상된 내산화성 |
WC-Ni 15% | 85% 화장실, 15% 니켈 | 부식성 환경 | 높은 내식성 |
WC-TaC-Co | 탄탈 카바이드 및 코발트 함유 화장실 | 연마성 항공우주 복합재 | 높은 골절 인성 |
WC-CoTi 8% | 화장실, 코발트, 티타늄 | 중단된 컷 | 내충격성 |
WC-Co 5% 나노 그레인 | 나노 크기의 입자가 있는 화장실 | 초정밀 커팅 | 극한의 경도 |
WC-Co-V 12% | WC, 12% Co, 바나듐 | 다목적 항공 우주 가공 | 균형 잡힌 내마모성과 내구성 |
WC-Co-Al 8% | 화장실, 코발트, 알루미늄 | 고속 드릴링 | 열 안정성 |
WC-Co-Cr 10% 스프레이 건조 | 응집된 혼합 | 코팅된 공구 기판 | 고밀도, 균일한 입자 분포 |
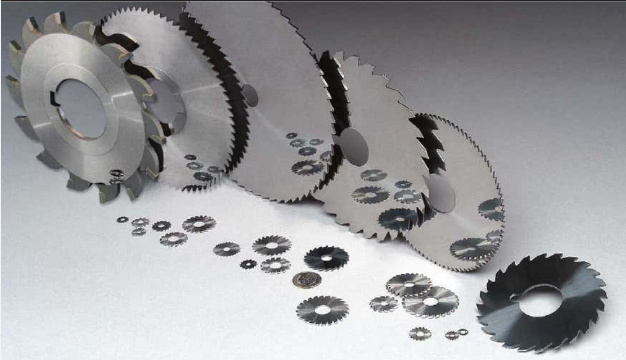
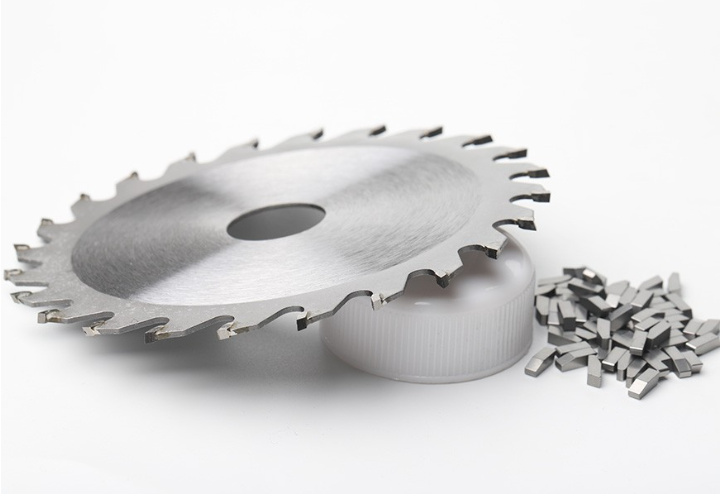
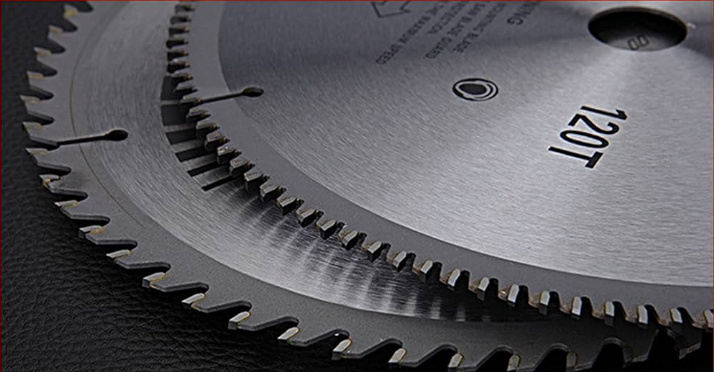
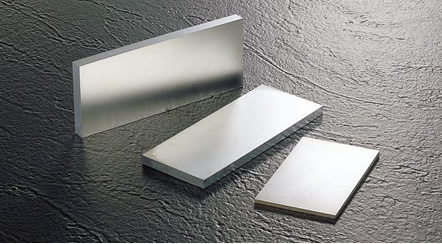
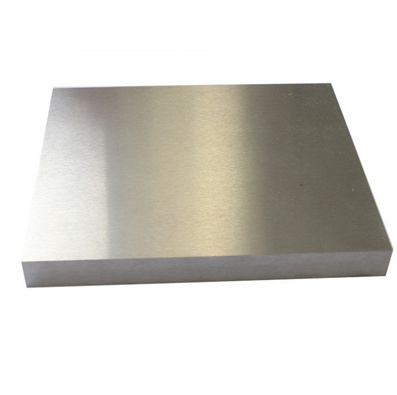
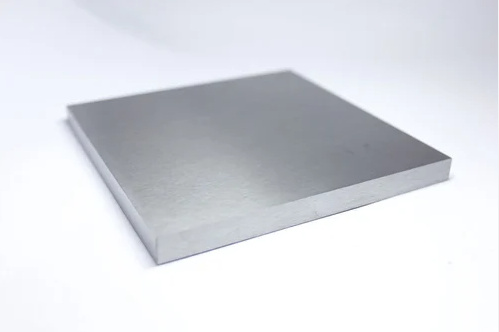
항공 우주 가공의 트렌드와 혁신
가공 기술은 멈춰 있지 않습니다. 항공우주 분야의 요구는 진화하고 있으며 도구도 진화하고 있습니다. 항공우주 산업을 형성하는 흥미로운 트렌드를 소개합니다:
혁신 | 설명 | 항공 우주 가공에 미치는 영향 |
---|---|---|
하이브리드 세라믹-카바이드 로드 | 카바이드 코어와 세라믹 레이어의 혼합 | 더 높은 온도 내성 |
나노 코팅 도구 | 다층 나노 코팅(예: AlTiN) | 공구 수명 연장, 마모 감소 |
스마트 머시닝 센서 | 공구 홀더에 내장된 센서 | 실시간 피드백 및 착용 추적 |
3D 프린팅 카바이드 인서트 | 복잡한 지오메트리를 추가 | 맞춤형 모양, 재료 낭비 감소 |
극저온 가공 | 냉각에 사용되는 LN2 | 깔끔한 절삭, 연장된 공구 수명 |
공구 경로 최적화 AI | AI가 생성하는 최적의 절단 경로 | 시간 절약, 표면 마감 개선 |
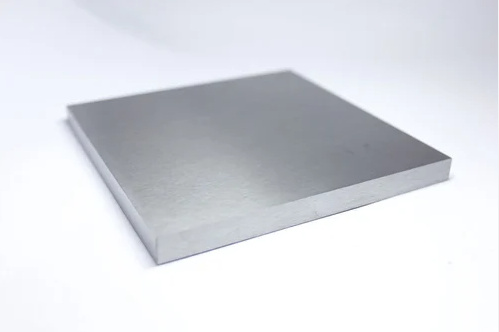
자주 묻는 질문
질문 | 답변 |
---|---|
카바이드 막대는 무엇으로 만들어지나요? | 대부분 텅스텐 카바이드와 코발트가 사용되며, 특수한 특성을 위해 크롬이나 탄탈륨과 같은 첨가제를 사용하는 경우도 있습니다. |
고속 강철(HSS)보다 더 나은가요? | 예, 특히 기계 가공이 어려운 항공우주 합금의 경우 더욱 그렇습니다. 더 오래 지속되고, 더 날카롭게 유지되며, 열에 더 잘 견딥니다. |
티타늄에 카바이드 막대를 사용할 수 있나요? | 물론이죠. 최상의 결과를 얻으려면 TiAlN과 같은 올바른 코팅이 적용된 미세 입자 또는 서브미크론 입자를 사용하세요. |
가장 큰 단점은 무엇인가요? | 강철에 비해 부서지기 쉬우므로 부적절한 취급이나 극심한 진동은 칩핑을 유발할 수 있습니다. |
올바른 것을 선택하려면 어떻게 해야 하나요? | 재료, 절단 속도, 환경, 기계 유형 등 사용 분야를 고려하세요. 그런 다음 입자 크기, 구성 및 코팅과 일치시킵니다. |
일반적인 수명은 어떻게 되나요? | 사용법에 따라 다르지만 카바이드 도구는 기존 도구보다 3배에서 10배 더 오래 사용할 수 있습니다. |
코팅이 필요한가요? | 항상 그런 것은 아니지만 코팅은 특히 고속 또는 건식 가공에서 성능을 크게 향상시킵니다. |
어떤 종류의 유지 관리가 필요하나요? | 도구를 깨끗하게 유지하고, 마모를 모니터링하며, 마모나 산화를 방지하기 위해 적절하게 보관하세요. |
카바이드 공구를 연마할 수 있나요? | 예, 하지만 다이아몬드 연삭 도구와 정밀 기계가 필요합니다. |
상위 공급업체는 누구인가요? | 케나메탈, 샌드빅, 세라티짓, 미쓰비시, 세코 등의 브랜드가 품질과 혁신으로 시장을 선도하고 있습니다. |