정밀도와 속도가 가장 중요한 현대 제조업의 급변하는 세계에서 멀티 플루트 카바이드 엔드밀은 탁월한 결과를 얻기 위한 필수 도구로 부상했습니다. 다중 절삭날과 견고한 카바이드 구조를 갖춘 이 최첨단 공구는 탁월한 재료 제거율, 우수한 표면 조도, 연장된 공구 수명을 제공합니다. 이 포괄적인 가이드에서는 멀티 플루트 카바이드 엔드밀의 설계, 적용 분야 및 TRUER와 같은 신뢰할 수 있는 공급업체를 선택할 때의 이점을 살펴보면서 복잡한 멀티 플루트 카바이드 엔드밀에 대해 자세히 설명합니다.
멀티 플루트 카바이드 엔드밀이란?
멀티 플루트 카바이드 엔드밀은 고속 가공 작업을 위해 특별히 설계된 회전식 절삭 공구입니다. 일반적으로 2개에서 8개 이상에 이르는 여러 개의 절삭날, 즉 플루트가 공구의 절삭 끝 둘레에 배열되어 있습니다. 이러한 플루트는 카바이드의 탁월한 경도 및 내마모성과 결합하여 멀티 플루트 엔드밀이 재료를 빠르고 효율적으로 제거하여 다양한 재료에서 정밀하고 복잡한 형상을 생성할 수 있도록 합니다.
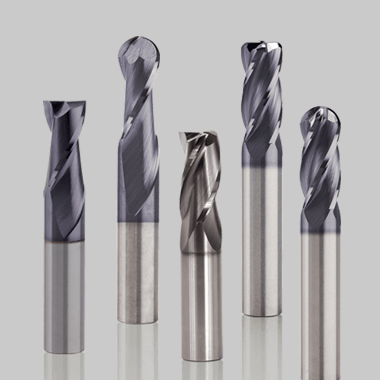
고성능 도구의 해부학: 디자인 및 기능
멀티 플루트 카바이드 엔드밀은 뛰어난 성능에 기여하는 몇 가지 주요 기능으로 설계되었습니다:
- 플루트 번호: 플루트의 수는 공구의 절삭 특성에 큰 영향을 미칩니다. 일반적으로 플루트가 많을수록 재료 제거율이 높아지고 표면 정삭이 부드러워지지만 스핀들 속도와 동력이 증가해야 할 수 있습니다.
- 나선 각도: 공구 축에 대한 플루트의 각도는 칩 배출 및 절삭력에 영향을 미칩니다. 나선 각도가 높을수록 칩을 효율적으로 제거할 수 있고, 각도가 낮을수록 절삭날 강도가 증가합니다.
- 플루트 지오메트리: 레이크 각도, 이격 각도, 칩 브레이커 기능 등 플루트의 모양과 디자인은 특정 재료와 절단 조건에 최적화되어 있습니다.
- 카바이드 등급: 최적의 공구 수명과 성능을 보장하려면 경도, 인성 및 내마모성과 같은 요소를 기준으로 적절한 초경 재종을 선택하는 것이 중요합니다.
- 코팅: 특히 고온 또는 마모성 가공 분야에서 TiN, TiAlN, DLC와 같은 고급 코팅은 내마모성을 더욱 향상시키고 마찰을 줄이며 공구 수명을 개선할 수 있습니다.
절삭력 분류하기: 멀티 플루트 엔드밀의 종류
멀티 플루트 카바이드 엔드밀은 다양한 가공 요구 사항에 맞게 다양한 구성으로 제공됩니다:
엔드밀 유형 | 특징 | 애플리케이션 |
---|---|---|
사각 엔드밀 | 평평한 절단면, 90도 모서리 | 범용 밀링, 슬롯 가공, 포켓 가공 |
볼 노즈 엔드밀 | 반구형 커팅 엔드 | 윤곽 밀링, 3D 프로파일링, 매끄러운 표면 마감 |
코너 반경 엔드밀 | 특정 반경의 둥근 모서리 | 가장자리 블렌딩, 모따기, 필렛 가공 |
황삭 엔드밀 | 공격적인 플루트 형상, 넓은 칩 간극 | 신속한 재료 제거, 황삭 작업 |
마감 엔드밀 | 미세한 플루트 형상, 높은 나선형 각도 | 섬세한 마감, 매끄러운 표면 마감, 정밀한 컨투어링 |
표 1: 일반적인 멀티 플루트 엔드밀 유형
산업 전반의 애플리케이션: 정밀성과 다목적성이 만나는 곳
멀티 플루트 카바이드 엔드밀의 뛰어난 성능과 다용도성으로 인해 다양한 산업 분야에서 없어서는 안 될 도구가 되었습니다:
- 항공우주: 고강도 합금으로 복잡한 항공기 부품, 엔진 부품 및 구조 요소를 가공합니다.
- 자동차: 엔진 블록, 실린더 헤드, 변속기 부품 및 기타 중요한 자동차 부품을 제조합니다.
- 의료 기기: 높은 정밀도와 생체 적합성을 갖춘 복잡한 임플란트, 수술 기구 및 의료 장비를 제작합니다.
- 몰드 제작: 플라스틱, 고무, 금속 주조 등 다양한 산업 분야의 금형과 금형을 생산합니다.
- 일반 제조: 프로토타이핑, 픽스처 제작, 일반 가공 작업 등 다양한 분야에 활용할 수 있습니다.
장점과 한계 비교
멀티 플루트 카바이드 엔드밀의 장점:
- 높은 재료 제거율: 여러 개의 절삭 날이 있어 빠르고 효율적으로 재료를 제거할 수 있습니다.
- 향상된 표면 마감: 플루트가 많을수록 표면 마감이 더 매끄러워져 2차 마감 작업의 필요성을 줄이거나 없앨 수 있습니다.
- 향상된 툴 수명: 초경의 뛰어난 경도와 내마모성은 공구 수명을 연장하여 가동 중지 시간과 공구 비용을 줄여줍니다.
- 향상된 활용성: 다양한 가공 분야에 맞게 다양한 크기, 형상 및 코팅으로 제공됩니다.
제한 사항:
- 더 높은 초기 비용: 초경 엔드밀은 고속 스틸 엔드밀에 비해 일반적으로 초기 비용이 더 높습니다.
- 칩 대피: 칩 재절삭 및 공구 손상을 방지하려면 칩을 효과적으로 제거하는 것이 중요하며, 이를 위해서는 적절한 절삭유 도포와 가공 파라미터가 필요합니다.
- 취성: 초경은 경도가 높아 고속강보다 부서지기 쉬우므로 파손을 방지하기 위해 세심한 취급과 가공이 필요합니다.
표 3: 멀티 플루트 카바이드 엔드밀의 장점과 한계
트루어의 장점: 왜 당사를 선택해야 할까요?
- 품질에 대한 확고한 약속: 최고 등급의 카바이드 재료 제조 공정 전반에 걸쳐 엄격한 품질 관리 조치를 취하고 있습니다.
- 애플리케이션 전문성: 당사의 숙련된 엔지니어 팀은 고객의 특정 가공 요구 사항에 맞는 최적의 엔드밀을 선택할 수 있도록 전문적인 지침을 제공합니다.
- 최첨단 기술: 당사는 첨단 제조 기술과 정밀 연삭 기술을 활용하여 탁월한 정확도와 성능을 갖춘 엔드밀을 생산합니다.
- 고객 중심 솔루션: 당사는 고객의 고유한 과제를 이해하고 기대를 뛰어넘는 맞춤형 솔루션을 제공하기 위해 최선을 다하고 있습니다.
자주 묻는 질문: 멀티 플루트 엔드밀 쿼리 해결하기
1. 내 애플리케이션에 적합한 플루트 개수를 선택하려면 어떻게 해야 하나요?
최적의 플루트 수는 가공되는 소재, 원하는 표면 정삭, 사용 가능한 스핀들 출력 등의 요인에 따라 달라집니다. 일반적으로 플루트가 많을수록 더 매끄러운 마감과 더 높은 재료 제거율을 제공하지만 스핀들 속도와 동력이 증가합니다.
2. 멀티 플루트 엔드밀에서 나선 각도의 의미는 무엇인가요?
나선 각도는 칩 배출 및 절삭력에 영향을 미칩니다. 나선 각도가 높을수록 칩을 효율적으로 제거할 수 있고, 각도가 낮을수록 절삭날의 강도가 높아집니다.
3. 멀티 플루트 엔드밀을 사용할 때 칩 재절단을 방지하려면 어떻게 해야 하나요?
효과적인 칩 배출이 중요합니다. 적절한 절삭유 도포, 적절한 가공 파라미터 사용, 칩 제거를 용이하게 하는 칩 브레이커 기능이 있는 엔드밀을 고려해야 합니다.
4. 멀티 플루트 엔드밀의 마모 징후는 무엇이며 언제 교체해야 하나요?
마모 징후로는 절삭날이 부서지거나 마모된 경우, 절삭력 증가, 표면 정삭 불량, 가공 중 소리나 진동이 변하는 경우 등이 있습니다. 이러한 징후가 나타나면 엔드밀을 교체하여 공구 손상이나 공작물 결함을 방지하세요.
5. 특정 가공 요구 사항을 충족하는 맞춤형 멀티 플루트 엔드밀을 제공할 수 있나요?
예, 당사는 맞춤형 툴링 솔루션을 전문적으로 제공합니다. 구체적인 요구 사항을 알려주시면 엔지니어링 팀이 고객과 긴밀히 협력하여 고객의 애플리케이션에 가장 적합한 엔드밀을 설계하고 제조해 드립니다.