경도를 넘어서: 최적화된 카바이드 버튼 설계의 비밀을 밝히다
까다로운 내마모성 부품의 세계에서, 카바이드 버튼 는 뛰어난 내구성으로 유명합니다. 하지만 지오메트리 및 디자인 성능과 수명을 극대화하는 데 중요한 역할을 하는 작지만 강력한 구성 요소는 무엇일까요?
이 포괄적인 가이드는 카바이드 버튼 모양, 애플리케이션 요구 사항 및 내마모성 간의 흥미로운 상호 작용을 자세히 설명하여 성능을 최적화하고 장비 수명을 연장하는 정보에 입각한 결정을 내릴 수 있도록 지원합니다.
지오메트리가 중요한 이유: 영향력 이해
눈에 보이는 것 그 이상: 형태가 착용 행동에 미치는 영향
카바이드 재종 자체는 경도 및 인성과 같은 기본적인 특성을 결정하지만, 버튼의 형상은 이러한 특성이 실제 성능으로 변환되는 방식에 큰 영향을 미칩니다. 그 이유는 다음과 같습니다:
- 스트레스 분산: 카바이드 버튼의 모양은 충격, 마모 및 기타 마모 메커니즘으로 인한 응력이 표면 전체에 분산되는 방식에 영향을 미칩니다. 이 분포를 최적화하면 응력 집중을 최소화하고 치핑, 균열 또는 조기 마모의 위험을 줄일 수 있습니다.
- 머티리얼 흐름: 마모성 소재를 사용하는 애플리케이션에서 버튼의 형상은 이러한 소재의 흐름과 표면과의 상호 작용 방식에 영향을 미칠 수 있습니다. 전략적인 형상은 재료의 처짐을 촉진하여 직접적인 마모를 줄이고 버튼 수명을 연장할 수 있습니다.
- 셀프 샤프닝: 일부 버튼 디자인에는 버튼이 마모됨에 따라 자동으로 연마되는 기능이 포함되어 있습니다. 이렇게 하면 절단 또는 연삭 효율을 더 오랫동안 유지하여 교체로 인한 가동 중단 시간을 줄일 수 있습니다.
- 부착 강도: 버튼의 형상은 기본 소재에 대한 부착 강도와 신뢰성에도 영향을 미칩니다. 적절한 디자인은 안전한 결합을 보장하여 버튼 분실을 방지하고 마모 수명을 극대화합니다.
주요 기하학적 특징과 그 효과
버튼 디자인의 구성 요소 자세히 살펴보기
- 얼굴 모양: 마모 표면에 닿는 버튼의 노출된 면의 모양이 매우 중요합니다. 일반적인 모양은 다음과 같습니다:
- 라운드: 다용도로 활용 가능하며 내마모성이 우수합니다.
- 육각형: 더 나은 마모 분포를 위해 표면적을 넓히고 셀프 샤프닝을 향상시킬 수 있습니다.
- 탄도: 극한의 내충격성을 위해 설계되어 암석 파쇄와 같은 용도로 자주 사용됩니다.
- 원뿔형: 드릴링이나 토공 작업과 같은 작업에서 자재 흐름을 촉진하고 막힘을 줄입니다.
- 얼굴 프로필: 버튼의 얼굴 윤곽은 평평하거나 오목하거나 볼록할 수 있으며, 각각 착용 동작에 영향을 미칩니다:
- Flat: 고른 마모 분포를 제공하지만 강한 충격을 받으면 칩핑에 더 취약할 수 있습니다.
- Concave: 셀프 샤프닝을 강화하고 절단 또는 드릴링 작업에서 재료 침투력을 향상시킬 수 있습니다.
- 볼록: 충격과 마모에 대한 저항력이 향상되지만 절단 효율이 다소 떨어질 수 있습니다.
- 섕크 디자인: 섕크는 버튼의 기본 소재에 내장되어 고정 기능을 제공하는 부분입니다:
- 스트레이트 섕크: 간단하고 비용 효율적이며 마모와 충격이 중간 정도인 애플리케이션에 적합합니다.
- 카운터보어 생크: 표면적이 넓어져 부착력이 강해져 잡아당기는 힘에 대한 저항력이 향상됩니다.
- 더브테일 생크: 풀아웃에 대한 저항력이 뛰어나 충격이 큰 애플리케이션에 이상적입니다.
- 버튼 크기: 버튼이 클수록 일반적으로 마모량이 많고 더 큰 충격에도 견딜 수 있지만, 침투력이 떨어지거나 더 견고한 부착 방법이 필요할 수 있습니다. 작은 버튼은 복잡한 표면에서 더 나은 윤곽을 제공하며 마모율이 낮은 애플리케이션에 더 비용 효율적일 수 있습니다.
- 간격 및 배열: 마모 표면의 카바이드 버튼의 간격과 배열도 성능에 영향을 미칩니다. 고려해야 할 요소는 다음과 같습니다:
- 착용 패턴: 기존 착용 패턴을 분석하면 버튼 배치를 최적화하여 보호 기능을 극대화할 수 있습니다.
- 머티리얼 흐름: 버튼의 간격을 전략적으로 배치하면 효율적인 자료 흐름을 촉진하고 막힘을 최소화할 수 있습니다.
- 영향력 분산: 여러 버튼에 충격력을 고르게 분산시키면 개별 버튼의 고장 위험을 줄일 수 있습니다.
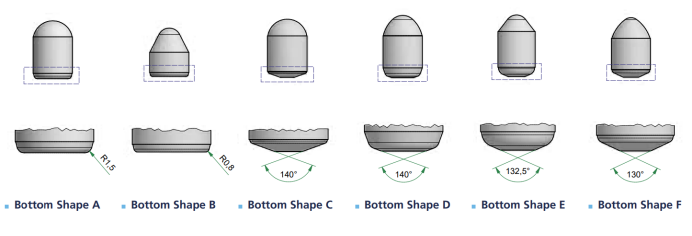
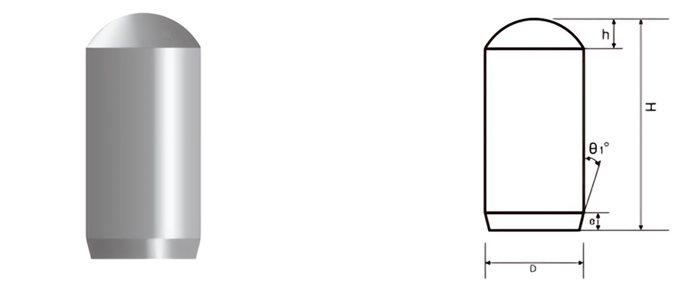
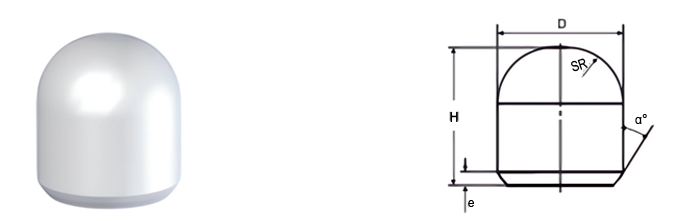
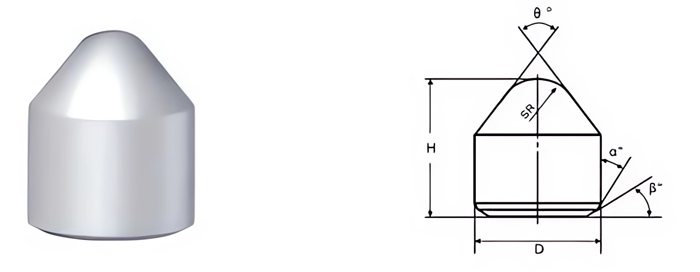
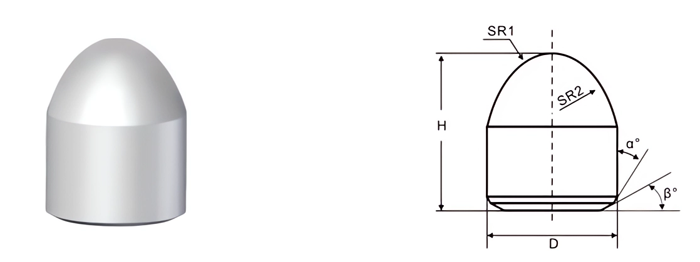
지오메트리를 애플리케이션에 맞추기: 완벽한 핏 찾기
특정 산업을 위한 성능 최적화를 위한 가이드
애플리케이션 | 주요 과제 | 권장 지오메트리 기능 |
---|---|---|
채굴(드릴링) | 마모, 충격, 암석 파편화 | 원추형 또는 탄도형 페이스 모양, 카운터보어 또는 더브테일 생크가 있어 안전하게 부착 가능 |
건설(도로 밀링) | 높은 마모, 골재에 의한 충격 | 육각형 또는 원형 얼굴 모양, 평면 또는 오목한 얼굴 프로파일로 셀프 샤프닝 가능 |
농업(경작) | 토양 및 암석에 의한 마모, 내충격성 | 원형 또는 원뿔형 표면 모양, 다양한 토양 조건에서 안전하게 부착할 수 있는 적당한 생크 깊이 |
재활용(파쇄) | 내충격성, 다양한 소재로 인한 마모 | 탄도 또는 강력하게 강화된 원형 페이스 형태, 견고한 섕크 디자인으로 안전하게 부착 가능 |
기본을 넘어서: 고급 디자인 고려 사항
- 유한 요소 분석(FEA): 정교한 컴퓨터 시뮬레이션을 통해 다양한 작동 조건에서 응력 분포와 마모 패턴을 모델링하여 고도로 최적화된 버튼 디자인을 구현할 수 있습니다.
- 사용자 지정 디자인: 고유한 마모 문제가 있는 특수 애플리케이션의 경우, 성능 요구 사항에 정확하게 부합하는 맞춤형 버튼 디자인을 만들 수 있습니다.
- 웨어러블 모니터링 및 분석: 카바이드 버튼의 마모 패턴을 정기적으로 모니터링하면 형상을 더욱 최적화하고 수명을 연장하는 데 유용한 인사이트를 얻을 수 있습니다.
자주 묻는 질문:
1. 육각 카바이드 버튼 사용의 주요 장점은 무엇인가요?
육각형 버튼은 원형 버튼에 비해 표면적이 넓어 마모 분포를 개선하고 자체 연마를 촉진할 수 있습니다.
2. 영향력이 큰 애플리케이션에서 버튼 크기는 성능에 어떤 영향을 미치나요?
버튼이 클수록 일반적으로 마모량이 많고 더 큰 충격에도 견딜 수 있습니다. 그러나 이탈을 방지하기 위해 더 견고한 부착 방법이 필요할 수 있습니다.
3. 마모 표면에 카바이드 버튼을 배치할 때 적절한 간격이 중요한 이유는 무엇인가요?
적절한 간격은 마모가 고르게 분포되도록 하고, 효율적인 재료 흐름을 촉진하며, 특히 연마재와 관련된 응용 분야에서 막힘을 방지하는 데 도움이 됩니다.
4. 드릴링 및 파쇄 용도에 동일한 카바이드 버튼 형상을 사용할 수 있나요?
일부 버튼 모양은 다용도로 사용할 수 있지만, 일반적으로 사용 목적에 맞게 특별히 설계된 형상을 선택하는 것이 좋습니다. 예를 들어, 드릴링과 분쇄는 서로 다른 마모 메커니즘과 힘의 방향을 수반합니다.
5. 특정 애플리케이션에 맞는 최적의 카바이드 버튼 형상을 결정하려면 어떻게 해야 하나요?
마모 분야에 경험이 풍부한 카바이드 버튼 공급업체 또는 재료 엔지니어와 상담하는 것이 좋습니다. 마모 메커니즘, 가공되는 재료, 작동 조건 등의 요소를 고려하여 고객의 특정 요구 사항을 평가하여 가장 적합한 버튼 형상과 등급을 추천할 수 있습니다.
결론 카바이드 버튼의 잠재력을 최대한 활용하기
지오메트리와 디자인이 다음 사항에 미치는 중대한 영향 이해 카바이드 버튼 성능은 마모 수명을 극대화하고 가동 중단 시간을 줄이며 전반적인 효율성을 최적화하는 데 매우 중요합니다. 애플리케이션의 특정 과제를 신중하게 고려하고 지식이 풍부한 공급업체와 협력하면 이러한 내구성 부품의 잠재력을 최대한 활용하고 귀중한 장비의 수명을 연장할 수 있습니다.