소개 무모한 힘만이 통할 때
거대한 공작물과 까다로운 재료가 공구 기술의 한계를 시험하는 까다로운 중장비 가공의 세계에서는 가장 견고한 공구만이 살아남습니다. 입력 유형 D 카바이드 납땜 팁최고의 파워와 복원력으로 가장 까다로운 절삭 조건을 극복하도록 설계된 기계 가공 분야의 주력 제품입니다.
이 글에서는 초경 브레이징 팁의 고유한 특징과 장점, 그리고 최대 금속 제거와 흔들림 없는 신뢰성이 타협할 수 없는 조건일 때 이 팁을 선택하는 이유에 대해 자세히 살펴봅니다.
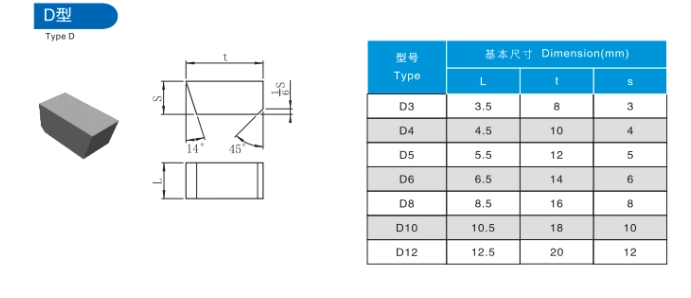
기계 가공의 헤비급: 가장 까다로운 응용 분야 해결
다른 도구가 흔들리는 경우, 타입 D 팁이 우선합니다.
고강도 가공 작업은 다음과 같은 특징이 있습니다:
- 높은 재료 제거율: 대량의 자료를 빠르고 효율적으로 제거합니다.
- 가공하기 어려운 재료: 기존 툴링이 빠르게 마모될 수 있는 거칠고 마모성이 있거나 고온의 합금으로 작업합니다.
- 익스트림 커팅 포스: 견고한 툴링 및 기계 설정이 필요한 상당한 절삭력을 생성합니다.
이러한 까다로운 조건에서는 뛰어난 카바이드 브레이징 팁이 필요합니다:
- 힘과 강인함: 헤비컷 작업 시 발생하는 엄청난 힘과 스트레스를 견뎌내야 합니다.
- 내마모성: 마모성 소재를 가공할 때 절삭날 무결성과 공구 수명을 유지합니다.
- 열 안정성: 고속 가공 시 발생하는 높은 온도에서도 변형을 방지하고 절삭날의 날카로움을 유지합니다.
타입 D 카바이드 브레이징 팁: 최대 금속 제거를 위해 제작
강인함과 내구성의 교향곡
타입 D 카바이드 브레이징 팁은 고강도 가공을 위해 특별히 제작되었으며, 그 특징이 뚜렷합니다:
- 중립 또는 약간 플러스 레이크 각도: 이 레이크 각도는 절삭날의 강도와 선명도 사이의 균형을 유지하여 제공합니다:
- 강력한 최첨단 기술: 중장비 가공에서 흔히 발생하는 높은 충격 하중과 중단된 절단을 견딜 수 있습니다.
- 효율적인 칩 흐름: 대량의 자재 제거 시 발생하는 큰 칩을 쉽게 제거할 수 있습니다.
- 큰 코 반경: 타입 D 팁의 노즈 반경이 더 넓습니다:
- 커팅 엣지 강도 증가: 절삭력을 더 넓은 영역에 분산시켜 칩핑이나 파손의 위험을 줄입니다.
- 더 높은 피드 속도에서 향상된 표면 마감: 주로 정삭용으로 알려져 있지는 않지만, 노즈 반경이 커서 중장비 가공에서 일반적으로 사용되는 높은 이송 속도에서도 허용 가능한 표면 정삭이 가능합니다.
- 견고한 카바이드 등급: 타입 D 팁은 코발트(Co) 함량이 높거나 탄탈륨(Ta) 또는 니오븀(Nb)과 같은 다른 원소를 첨가한 초경 카바이드 재종을 사용하는 경우가 많습니다. 이러한 등급은 다음을 제공합니다:
- 뛰어난 강도와 견고함: 고강도 가공에서 발생하는 극한의 힘을 견딜 수 있습니다.
- 높은 내마모성: 마모성 소재 가공 시 공구 수명 연장.
- 열 안정성: 고온에서도 최첨단 무결성을 유지합니다.
고강도 가공에서 타입 D 카바이드 브레이징 팁의 장점
가장 까다로운 컷을 통과하는 전력 공급
타입 D 카바이드 브레이징 팁의 견고한 설계와 재료 특성은 몇 가지 주요 이점을 제공합니다:
- 높은 재료 제거율: 강도와 인성이 뛰어나 공격적인 절삭 파라미터를 사용할 수 있어 생산성을 극대화하고 가공 시간을 단축할 수 있습니다.
- 까다로운 재료에서 연장된 공구 수명: 내마모성이 뛰어나 연마성 또는 고온 합금 가공 시에도 공구 수명이 연장됩니다.
- 신뢰성 및 예측 가능성: 견고한 구조로 예기치 않은 도구 고장의 위험을 최소화하여 일관된 성능과 예측 가능한 결과를 보장합니다.
- 고강도 애플리케이션에서의 활용성: 타입 D 팁은 밀링, 터닝, 보링, 그루브 가공 등 다양한 고강도 가공 작업에 적합합니다.
타입 D 카바이드 브레이징 팁의 적용 분야
최고의 성능과 내구성을 자랑하는 곳
타입 D 카바이드 브레이징 팁은 다른 공구가 부족한 고강도 가공 분야에서 탁월한 성능을 발휘합니다:
- 러프닝 작업: 밀링 및 선삭 작업에서 많은 양의 재료를 빠르게 제거합니다.
- 고온 합금 가공: 인코넬, 티타늄, 스테인리스 스틸과 같이 높은 절삭 온도를 발생시키는 재료로 작업합니다.
- 연마재 절단: 주철, 경화강 및 기존 툴링이 빠르게 마모될 수 있는 기타 소재를 가공합니다.
- 심한 중단 컷: 공구가 반복적으로 공작물에 들어갔다가 나오는 밀링과 같은 작업에서 발생하는 충격 하중과 변동하는 힘을 견딜 수 있습니다.
올바른 타입 D 카바이드 브레이징 팁 선택하기: 고려해야 할 요소
극한 조건에 맞는 툴링 선택 최적화
최적의 타입 D 카바이드 브레이징 팁을 선택하려면 신중하게 평가해야 합니다:
- 공작물 재질: 재료의 경도, 마모성 및 열적 특성은 적절한 카바이드 등급과 코팅을 결정하는 데 중요한 요소입니다.
- 가공 작업: 거친 밀링, 고온 합금의 선삭 또는 대구경 보링과 같은 특정 고강도 작업은 팁 형상과 크기 선택에 영향을 미칩니다.
- 절단 매개변수: 원하는 절삭 속도, 이송 속도, 절삭 깊이는 절삭력과 온도에 직접적인 영향을 미치기 때문에 팁 선택에 중요한 역할을 합니다.
- 머신 툴 기능: 공작 기계의 강성과 출력에 따라 팁 크기와 절단 매개변수의 선택이 제한될 수 있습니다.
타입 D 카바이드 브레이징 팁 선택: 간단한 가이드
선택 과정을 돕기 위해 다양한 타입 D 팁 형상에 대한 일반적인 적용 사례와 고려 사항을 요약한 표를 소개합니다:
타입 D 팁 지오메트리 | 일반적인 애플리케이션 | 주요 고려 사항 |
---|---|---|
하이 포지티브 인서트 | 고속 밀링, 거친 선삭 | 강도와 칩 흐름의 균형이 잘 잡혀 있습니다. |
이중 네거티브 삽입 | 고강도 선삭, 중단 절단 | 최대 강도와 칩핑 저항성 제공 |
버튼 삽입 | 견고한 보링, 깊은 홈 가공 | 넓은 절단 깊이를 위한 최대 지지력과 강성 제공 |
타입 D 카바이드 브레이징 팁에 대해 자주 묻는 질문
Q1: 타입 D 카바이드 브레이징 팁을 마감 작업에 사용할 수 있습니까?
A1: 미세한 표면 마감에는 적합하지 않지만, 표면 마감 요구 사항이 덜 엄격한 일부 고강도 작업의 마감 절단에는 타입 D 팁을 사용할 수 있습니다.
Q2: 타입 D 카바이드 브레이징 팁의 마모 징후는 무엇인가요?
A2: 일반적인 마모 징후로는 절삭날의 측면 마모, 갈퀴면의 크레이터, 고온으로 인한 절삭날의 소성 변형 등이 있습니다.
Q3: 고강도 가공에서 타입 D 카바이드 브레이징 팁의 공구 수명을 최대화하려면 어떻게 해야 합니까?
A3: 핵심 요소로는 응용 분야에 적합한 팁 형상과 재종 선택, 절삭 파라미터 최적화(재료 제거율과 공구 수명 간 균형), 고압 절삭유 시스템 사용, 견고한 기계 설정 등이 있습니다.
Q4: 고양성 인서트와 이중 음성 인서트 타입 D 팁의 차이점은 무엇인가요?
A4: 하이 포지티브 인서트는 효율적인 칩 흐름과 고속 이송 밀링 응용 분야를 위해 설계되었으며, 이중 네거티브 인서트는 고강도 선삭 및 중단된 절삭 작업에서 칩핑에 대한 저항성과 강도를 극대화합니다.
Q5: 버튼 인서트 타입 D 팁은 언제 선택해야 하나요?
A5: 버튼 인서트는 공구 처짐을 방지하고 정확한 홀 직경 또는 홈 치수를 보장하기 위해 최대의 지지력과 강성이 필요한 고강도 보링 및 깊은 홈 가공에 가장 적합한 선택입니다.