소개 야수 길들이기: 주철의 정밀 가공
주철은 인상적인 강도와 비용 효율성으로 수많은 산업 분야에서 최고의 자리를 차지하고 있습니다. 하지만 이 견고한 소재를 가공할 때는 마모성이 강하고 딱딱하고 불연속적인 칩을 형성하는 경향이 있어 고유한 어려움이 있습니다. 입력 유형 G 카바이드 납땜 팁주철 가공의 복잡성을 극복하도록 설계된 특수 공구로 뛰어난 성능, 공구 수명 및 표면 마감을 제공합니다.
이 기사에서는 주철 부품을 가공할 때 정밀도와 효율성을 달성하기 위해 이 팁이 선택되는 이유와 고유한 특성, 장점에 대해 알아보고 타입 G 카바이드 브레이징 팁의 세계를 탐구합니다.
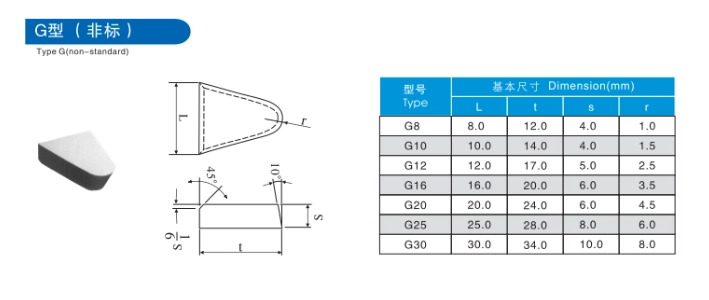
주철의 도전: 마모, 열 및 칩 형성
까다로운 가공의 지형 탐색하기:
주철 가공은 기존 절삭 공구의 성능을 빠르게 저하시킬 수 있는 세 가지 문제를 안고 있습니다:
- 높은 내마모성: 주철 매트릭스 내에 흑연 조각이 존재하면 본질적으로 마모성이 있는 재료가 생성되어 공구 마모가 가속화되고 절삭날의 날카로움이 감소합니다.
- 열 발생: 주철의 연마성 때문에 가공 중에 상당한 열이 발생하여 공구 마모를 유발하고 치수 정확도에 영향을 미칠 수 있습니다.
- 불연속적인 칩 형성: 주철의 부서지기 쉬운 특성으로 인해 작고 불연속적인 칩이 형성되어 절삭 영역에 갇혀 마찰, 열 축적, 공구 손상 가능성이 높아질 수 있습니다.
타입 G 카바이드 브레이징 팁: 주철 숙달을 위한 설계
내마모성 및 칩 제어의 해부학:
타입 G 카바이드 브레이징 팁은 주철 가공의 문제를 해결하기 위해 특별히 설계되었으며, 다음과 같은 특징이 있습니다:
- 견고한 카바이드 등급: 타입 G 팁은 인성과 내마모성이 강화된 카바이드 재종을 사용하여 주철의 열악한 절삭 환경을 견딜 수 있습니다.
- 날카로운 커팅 엣지: 주철 가공에서 효율적인 칩 형성과 열 발생 최소화를 위해서는 날카로운 절삭날을 유지하는 것이 중요합니다. 타입 G 팁은 깔끔한 전단 작업을 용이하게 하기 위해 날카롭고 양의 레이크 각도를 특징으로 하는 경우가 많습니다.
- 칩 제어 기능: 많은 타입 G 팁에는 주철에서 발생하는 길고 끈적끈적한 칩을 잘게 부수도록 설계된 칩 브레이커 또는 칩 제어 지오메트리가 통합되어 있습니다. 이러한 기능은 효율적인 칩 배출을 촉진하고 열 축적을 줄이며 칩 용접을 방지합니다.
G타입 카바이드 브레이징 팁이 주철 가공에 탁월한 7가지 이유
자신감을 가지고 도전과제를 정복하세요:
G타입 카바이드 브레이징 팁의 특수 설계와 재료 특성은 몇 가지 주요 이점으로 이어집니다:
- 탁월한 내마모성: 견고한 카바이드 재종과 날카로운 절삭날은 주철 가공 시 발생하는 높은 연마 마모를 견딜 수 있어 공구 수명을 크게 연장시킵니다.
- 효율적인 칩 제어: 칩 브레이커 형상과 양의 경사각은 효율적인 칩 형성 및 배출을 촉진하여 열 축적을 줄이고 칩 용접을 방지하며 표면 조도를 향상시킵니다.
- 표면 마감 개선: 날카로운 절삭날, 효율적인 칩 제어, 절삭력 감소의 조합으로 타입 G 팁은 주철의 표면 마감이 놀라울 정도로 우수하여 2차 마감 작업이 필요 없는 경우가 많습니다.
- 절단력 감소: 날카로운 절삭날과 양의 경사각이 절삭력을 최소화하여 공구, 공작 기계 및 공작물에 가해지는 스트레스를 줄여줍니다.
- 생산성 향상: 공구 수명 연장, 가동 중단 시간 감소, 더 빠른 절삭 속도 및 이송 능력은 생산성 향상과 사이클 시간 단축에 기여합니다.
- 까다로운 애플리케이션에서의 비용 효율성: 타입 G 팁이 제공하는 향상된 공구 수명과 생산성 향상은 특히 대량 주철 가공 작업에서 상당한 비용 절감으로 이어집니다.
- 주철 가공의 다양성: 타입 G 팁은 황삭, 정삭, 선삭, 밀링, 드릴링, 보링 등 다양한 주철 가공 작업에 적합합니다.
타입 G 카바이드 브레이징 팁의 응용 분야
주철 가공에서 정밀도와 효율성이 만나는 지점:
타입 G 카바이드 브레이징 팁은 다양한 주철 가공 응용 분야에 가장 적합한 선택입니다:
- 자동차 산업: 엔진 블록, 실린더 헤드, 변속기 케이스 및 주철의 강도와 비용 효율성이 매우 중요한 기타 부품을 가공합니다.
- 중장비 제조: 건설 장비, 농기계, 광산 장비의 기어, 하우징 및 기타 핵심 부품을 생산합니다.
- 펌프 및 밸브 제조: 펌프 하우징, 밸브 본체 및 유체 흐름과 압력 억제가 중요한 기타 구성 요소에 복잡한 특징과 매끄러운 표면을 만듭니다.
올바른 유형의 G 카바이드 브레이징 팁 선택하기: 고려해야 할 요소
주철 숙달을 위한 툴 선택 최적화:
최적의 G타입 카바이드 브레이징 팁을 선택하려면 몇 가지 요소를 신중하게 고려해야 합니다:
- 주철 유형: 주철의 등급에 따라 경도, 강도, 기계 가공성이 달라져 카바이드 등급과 코팅의 선택에 영향을 미칩니다.
- 가공 작업: 황삭, 정삭, 선삭, 밀링, 드릴링 또는 보링과 같은 특정 가공 작업은 팁 형상, 크기 및 칩 브레이커 설계의 선택에 영향을 미칩니다.
- 절단 조건: 원하는 절단 속도, 이송, 절단 깊이 및 중단된 절단의 존재 여부가 팁 선택에 영향을 미칩니다.
- 머신 툴 기능: 공작 기계의 강성과 출력은 달성 가능한 절삭 파라미터와 적절한 팁 크기 및 형상 선택에 영향을 미칠 수 있습니다.
타입 G 카바이드 브레이징 팁 선택: 간단한 가이드
선택 과정을 돕기 위해 다양한 유형 G 팁 형상에 대한 일반적인 적용 사례와 고려 사항을 요약한 표를 소개합니다:
유형 G 팁 지오메트리 | 일반적인 애플리케이션 | 주요 고려 사항 |
---|---|---|
칩브레이커가 있는 원형 인서트 | 범용 터닝, 페이싱 및 보링 | 우수한 칩 컨트롤과 선명도와 강도의 균형을 제공합니다. |
칩브레이커가 있는 정사각형 삽입 | 밀링, 숄더 밀링 및 슬롯 가공 | 강력한 절삭날과 중단된 절삭을 위한 우수한 칩 배출 기능 제공 |
포지티브 레이크가 있는 삼각형 인서트 | 플런지 밀링, 램핑 및 챔퍼링 | 공격적인 절삭 및 절입 작업을 위한 강력한 절삭날 제공 |
타입 G 카바이드 브레이징 팁에 대해 자주 묻는 질문
Q1: 캔 타입 G 카바이드 브레이징 팁 주철 이외의 소재를 가공하는 데 사용할 수 있나요?
A1: 주철용으로 특별히 설계되었지만, 타입 G 팁은 다른 재료, 특히 연성 주철 및 압축 흑연 주철과 같은 유사한 특성을 가진 재료를 가공하는 데 사용할 수 있습니다. 그러나 특정 재료와 절삭 조건에 따라 성능이 달라질 수 있습니다.
Q2: G타입 카바이드 브레이징 팁의 마모 징후는 무엇인가요?
A2: 일반적인 마모 징후로는 절삭날의 측면 마모, 레이크면의 크레이터 마모, 절삭날의 치핑 또는 둥글어짐 등이 있습니다. 주철 가공에서 마모는 표면 조도 저하, 절삭력 증가 또는 칩 형성의 변화로 나타날 수 있습니다.
Q3: 타입 G 카바이드 브레이징 팁으로 주철을 가공할 때 공구 수명을 최대화하려면 어떻게 해야 합니까?
A3: 핵심 요소에는 적용 분야에 적합한 팁 형상과 재종 선택, 절삭 파라미터 최적화(주철 재종 및 공작 기계의 성능 고려), 적절한 절삭유 도포 보장, 견고한 기계 설정 유지 등이 있습니다.
Q4: 타입 G 카바이드 브레이징 팁에서 칩브레이커의 역할은 무엇인가요?
A4: 칩 브레이커는 주철에서 발생하는 길고 끈적한 칩을 잘게 부수도록 설계되어 효율적인 칩 배출을 촉진하고 열 축적을 줄이며 공구와 공작물 모두를 손상시킬 수 있는 칩 용접을 방지합니다.
Q5: 주철 가공을 위해 원형 인서트와 사각형 인서트 타입 G 팁을 언제 선택해야 합니까?
A5: 주철의 범용 선삭, 면삭 및 보링 작업에는 칩브레이커가 있는 원형 인서트가 선호되는 반면, 중단 절삭이 일반적인 밀링, 숄더 밀링 및 슬롯 가공 작업에는 칩브레이커가 있는 정사각형 인서트가 더 적합합니다.