카바이드 인서트 는 놀라울 정도로 단순해 보일 수 있지만, 겉보기에는 절삭 성능을 최적화하도록 세심하게 설계된 복잡한 기하학적 구조와 디자인의 세계가 숨겨져 있습니다. 이러한 기하학적 특징이 가공 결과에 어떤 영향을 미치는지 이해하는 것이 작업에 적합한 초경 인서트를 선택하고 탁월한 결과를 얻기 위한 핵심입니다.
이 블로그 게시물에서는 다음과 같은 흥미로운 관계를 살펴봅니다. 카바이드 인서트 지오메트리 및 절단 성능, 탐색 7가지 핵심 디자인 요소 가공 결과에 미치는 영향
1. 레이크 각도: 칩 흐름과 절삭력에 미치는 영향
초경 인서트의 레이크면(칩을 향하는 표면)과 공작물에 수직인 선 사이에서 측정되는 레이크 각도는 칩 형성 및 절삭력에 중요한 역할을 합니다.
- 포지티브 레이크 각도: 칩 흐름이 용이하여 절삭력을 줄이고 동력을 덜 필요로 합니다. 부드러운 소재를 가공하거나 미세한 표면 마감을 구현하는 데 이상적입니다.
- 네거티브 레이크 각도: 더 강력한 절삭날을 제공하여 단단한 재료 가공이나 내충격성이 중요한 절삭 가공에 더 적합합니다. 그러나 음의 경사각은 더 높은 절삭력을 생성합니다.
2. 이격 각도: 마찰 및 열 축적 방지
카바이드 인서트의 측면면(가공된 표면을 향한 표면)과 공작물 접선 사이에 형성되는 안전각은 공구와 공작물 사이에 적절한 간격을 확보하여 마찰과 과도한 열 발생을 방지합니다.
- 더 넓은 클리어런스 각도: 마찰과 열 축적을 줄여 칩 용접이 발생하기 쉬운 연성 또는 연성 소재를 가공할 때 특히 유용합니다.
- 더 작은 간격 각도: 단단한 소재를 가공하거나 고강도 절삭 작업 시 절삭날 지지력을 강화하여 공구 수명을 연장합니다.
3. 칩 브레이커 지오메트리: 칩 형성 및 배출 제어하기
칩 브레이커는 카바이드 인서트의 레이크면에 통합된 홈 또는 스텝으로, 칩 형성을 제어하고 절삭 영역에서 칩 흐름을 유도하는 데 매우 중요합니다.
- 넓고 얕은 칩브레이커: 연성 소재를 빠른 절삭 속도로 가공하는 데 이상적인 짧고 말린 칩의 형성을 촉진합니다.
- 좁고 깊은 칩브레이커: 더 두껍고 좁은 칩을 생성하여 더 단단한 재료를 가공하거나 칩 제어가 중요한 황삭 가공에 적합합니다.
4. 절삭날 준비: 엣지 강도 및 표면 마감에 미치는 영향
카바이드 인서트의 절삭 날은 다양한 방법으로 준비할 수 있으며, 각각 절삭 날 강도, 표면 마감 및 공구 수명에 영향을 미칩니다.
- 연마된 엣지: 매우 날카롭고 광택이 나는 가장자리를 만들어 미세한 표면 마감과 엄격한 허용 오차를 달성하는 데 이상적입니다. 그러나 연마된 모서리는 더 섬세하고 깨지기 쉽습니다.
- 모서리가 깎인 가장자리: 절삭 날을 강화하여 특히 마모성 소재를 가공할 때나 중단된 절삭 중에 칩핑의 위험을 줄입니다.
- 둥근 모서리: 가장자리 강도와 표면 마감의 균형이 잘 잡혀 있어 다양한 가공 분야에 적합합니다.
5. 코너 반경: 강도와 선명도의 균형
모서리 반경, 즉 갈퀴와 측면 면이 교차하는 부분의 둥근 모서리는 인서트의 강도, 선명도 및 다양한 절단 조건을 처리하는 능력에 영향을 미칩니다.
- 날카로운 모서리(작은 반경): 가장 날카로운 절삭 날을 제공하여 엄격한 공차와 복잡한 형상을 구현하는 데 이상적입니다. 그러나 날카로운 모서리는 칩핑에 더 취약합니다.
- 둥근 모서리(큰 반경): 강도와 칩핑에 대한 저항력이 향상되어 무거운 절삭 작업이나 단단한 재료를 가공할 때 특히 유용합니다.
6. 삽입 두께: 공구 강성 및 안정성 결정
카바이드 인서트의 두께는 절삭력에 따른 강성과 처짐에 대한 저항에 영향을 미칩니다.
- 더 두꺼운 인서트: 무거운 절삭 작업이나 편향이 정확도에 영향을 미칠 수 있는 대형 공작물 가공에 필수적인 강성과 안정성을 제공합니다.
- 더 얇은 인서트: 절삭 저항이 적어 전력 소비를 줄이고 섬세한 부품을 가공하거나 더 작고 덜 강력한 기계를 사용할 때 적합합니다.
7. 코팅 기술: 내마모성 및 성능 향상
카바이드 인서트는 내마모성을 높이고 마찰을 줄이며 전반적인 절단 성능을 향상시키기 위해 얇고 단단한 재료로 코팅되는 경우가 많습니다.
- 질화 티타늄(TiN): 경도를 높이고 마찰을 줄이며 내산화성을 향상시키는 다용도 코팅으로 다양한 가공 분야에 적합합니다.
- 티타늄 카보나이트(TiCN): TiN보다 훨씬 뛰어난 경도와 내마모성을 제공하여 연마성 소재를 가공하거나 고속 작업 시 특히 효과적입니다.
- 알루미늄 산화물(Al2O3): 내열성과 내마모성이 뛰어나 고온 합금 가공이나 건식 가공 작업에 이상적입니다.
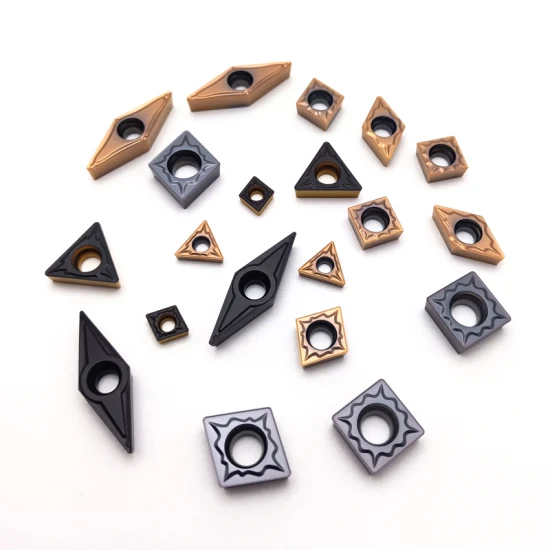
카바이드 인서트 형상: 빠른 참조 가이드
기능 | 설명 | 절단 성능에 미치는 영향 |
---|---|---|
레이크 각도 | 레이크 면과 수직선 사이의 각도 | 칩 흐름, 절삭력 및 표면 마감에 영향을 미칩니다. |
클리어런스 각도 | 측면 면과 공작물 접선 사이의 각도 | 마찰 방지, 열 축적 제어 |
칩브레이커 | 레이크 면의 홈 또는 계단 | 칩 형성 및 배출 제어 |
최첨단 준비 | 연마, 모따기 또는 둥글게 다듬기 | 모서리 강도, 표면 마감 및 공구 수명에 영향을 미칩니다. |
모서리 반경 | 레이크와 측면 교차점의 둥근 모서리 | 강도와 선명함의 균형 |
삽입 두께 | 인서트의 전체 두께 | 공구 강성 및 안정성 결정 |
코팅 | 얇고 단단한 소재를 표면에 적용 | 내마모성 향상, 마찰 감소, 성능 향상 |
자주 묻는 질문: 초경 인서트 기하학 관련 질문 해결하기
1. 내 애플리케이션에 적합한 경사각은 어떻게 선택하나요?
적절한 경사각 선택은 가공할 소재와 원하는 절삭 조건에 따라 달라집니다. 부드러운 소재와 정삭 작업에는 일반적으로 양의 경사각을 사용하는 것이 유리하지만, 단단한 소재와 황삭 작업에는 종종 음의 경사각이 필요합니다.
2. 가공에서 칩 제어의 중요성은 무엇인가요?
효과적인 칩 제어는 일관된 절삭 성능을 유지하고, 공작물이나 공구를 손상시킬 수 있는 칩 축적을 방지하며, 작업자의 안전을 보장하는 데 매우 중요합니다. 적절하게 설계된 칩 브레이커는 칩 흐름을 절삭 영역에서 멀어지게 하는 데 중요한 역할을 합니다.
3. 모서리가 뾰족한 인서트와 둥근 모서리 인서트는 언제 사용해야 하나요?
날카로운 모서리 인서트는 엄격한 공차와 복잡한 형상을 구현하는 데 이상적이지만 치핑에 더 취약합니다. 둥근 모서리 인서트는 강도가 높으며 무거운 절삭 작업이나 단단한 재료를 가공할 때 더 적합합니다.
4. 코팅 카바이드 인서트를 사용하면 어떤 이점이 있나요?
코팅 카바이드 인서트 는 내마모성 증가, 마찰 감소, 내열성 향상, 절삭 성능 향상 등 다양한 이점을 제공합니다. 다양한 코팅은 특정 가공 응용 분야와 재료에 맞게 맞춤화됩니다.
5. 인서트 두께는 공구 강성에 어떤 영향을 미칩니까?
인서트가 두꺼울수록 절삭력에 따른 강성과 휨에 대한 저항력이 커지는 반면, 인서트가 얇을수록 절삭 저항력이 떨어집니다. 적절한 인서트 두께를 선택하는 것은 가공 작업, 공작물 크기 및 기계 성능에 따라 달라집니다.