효율성 극대화: 우수한 재료 제거 및 표면 마감을 위한 두 개의 플루트 엔드 밀
두 개의 플루트 엔드 밀 는 가공 분야에서 필수적인 도구로, 재료를 빠르게 제거하고 매끄러운 표면 마감을 만들어내는 능력으로 높이 평가받고 있습니다. 이 다용도 절삭 공구는 각각 특정 가공 작업에 맞게 다양한 구성으로 제공됩니다. 이 종합 가이드는 두 가지 대표적인 유형의 플루트 엔드밀에 초점을 맞춥니다: 스트레이트 생크 사각 엔드밀 그리고 스트레이트 섕크 볼 엔드 밀. 각 공구의 고유한 특성, 응용 분야, 장점, 가공 요구 사항에 적합한 공구를 선택하는 방법에 대해 자세히 알아보겠습니다.
둘의 힘 이해하기: 왜 두 개의 플루트 엔드 밀을 사용해야 할까요?
2개의 플루트 엔드 밀 는 뚜렷한 이점을 제공하는 두 개의 최첨단 디자인이 특징입니다:
- 효율적인 칩 배출: 절삭날 사이의 플루트 공간이 넓어 칩을 효율적으로 제거할 수 있으며, 특히 길고 끈적한 칩이 생성되는 알루미늄이나 플라스틱과 같은 부드러운 소재를 작업할 때 매우 중요합니다. 이렇게 효율적인 칩 흐름은 칩 재절단을 방지하고 표면 정삭을 개선하며 공구 수명을 연장합니다.
- 절단 속도 및 이송 속도 향상: 절삭날 접촉이 줄어들어 플루트가 더 많은 엔드밀에 비해 절삭 속도와 이송 속도가 더 빨라집니다. 이는 곧 가공 시간 단축과 생산성 향상으로 이어집니다.
- 낮은 절삭력: 두 개의 플루트 엔드밀은 소재에 맞물리는 절삭날 수가 적기 때문에 절삭력이 낮아 과도한 힘이 가해지면 뒤틀리거나 파손될 수 있는 얇거나 섬세한 공작물을 가공하는 데 적합합니다.
두 가지 유형, 서로 다른 용도: 사각 엔드밀과 볼 엔드밀
직선형 생크 사각 엔드밀: 평평한 표면과 날카로운 모서리의 달인: 사각 엔드밀
- 정의 기능: 평평한 바닥에 두 개의 날카로운 절단면이 있어 평평한 표면, 어깨, 슬롯 및 모서리가 날카로운 포켓을 만드는 데 이상적입니다.
- 애플리케이션: 정밀한 90도 각도가 필요한 밀링 작업 등에 널리 사용됩니다:
- 키홈 만들기: 샤프트 또는 허브에 슬롯을 가공하여 키를 수용함으로써 두 구성 요소 사이의 회전을 방지합니다.
- 가공 단계: 공작물에 계단식 피처를 만들면 다양한 레벨이나 플랫폼을 만드는 데 자주 사용됩니다.
- 에지 프로파일링: 모서리가 날카로운 공작물 외부의 직선 모서리와 프로파일을 절단합니다.
- 페이스 밀링: 공작물 상단을 밀링하여 평평한 표면을 만듭니다.
- 플런지 밀링: 공작물을 똑바로 잘라 깊은 슬롯이나 포켓을 만듭니다.
스트레이트 생크 볼 엔드 밀: 윤곽과 부드러운 전환 조각하기
- 정의 기능: 반구형 커팅 팁으로 윤곽이 있는 표면, 필렛, 반경 및 서로 다른 피처 간의 부드러운 전환을 만들 수 있습니다.
- 애플리케이션: 다음과 같이 매끄럽고 흐르는 표면이 필요한 응용 프로그램에서 Excel:
- 몰드 제작: 사출 성형, 블로우 성형 및 기타 성형 공정에 사용되는 금형에 복잡한 캐비티, 디테일 및 매끄러운 표면을 생성합니다.
- 다이 싱킹: 스탬핑, 성형 및 기타 금속 성형 작업에 사용되는 금형에 캐비티와 디테일을 가공합니다.
- 윤곽 밀링: 미리 정의된 경로를 따라 복잡한 3D 모양과 윤곽을 가공합니다.
- 필렛 및 반지름 만들기: 모서리와 모서리를 둥글게 가공하여 응력 집중을 줄이고 부품의 강도를 향상시킵니다.
- 복잡한 표면 마무리하기: 곡면이나 윤곽이 있는 표면을 매끄럽고 미적으로 보기 좋게 마감할 수 있습니다.
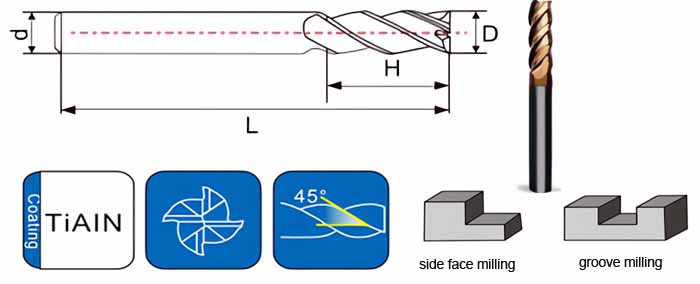
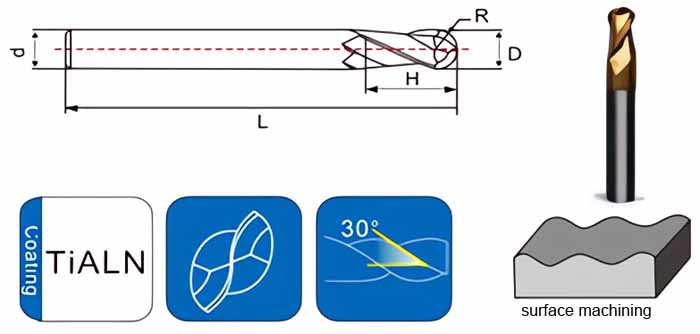
디자인 해부하기: 두 개의 플루트 엔드밀의 해부학
주요 구성 요소와 그 기능:
- 최첨단: 엔드밀의 주변부에 위치한 두 개의 정밀하게 연마된 모서리는 재료 제거를 담당합니다. 형상과 날카로움은 절삭 성능과 표면 조도에 직접적인 영향을 미칩니다.
- 플루트: 엔드밀의 몸체를 따라 나선형 홈이 있어 가공 중 칩 배출을 위한 경로를 제공합니다. 두 개의 플루트 엔드밀은 플루트 공간이 더 넓어 칩 흐름을 개선합니다.
- Shank: 밀링 머신의 공구 홀더에 단단히 고정되어 있는 엔드밀의 원통형 부분입니다. 직선형 생크는 수동 밀링 머신과 일부 CNC 기계에 일반적으로 사용됩니다.
- Body: 엔드밀의 주요 부분은 일반적으로 경도, 내마모성 및 날카로운 절삭 날을 유지하는 능력을 위해 솔리드 카바이드로 제작됩니다.
- 전체 길이(OAL): 절삭날 끝에서 생크 끝까지 엔드밀의 총 길이입니다.
- 절단 지름: 엔드밀의 절단 부분의 직경으로, 절단 폭을 결정합니다.
원자재에서 정밀 공구까지: 제조 공정
변화의 여정:
- 카바이드 블랭크 준비: 이 공정은 일반적으로 분말 야금을 통해 생산되는 원통형 카바이드 블랭크로 시작됩니다. 블랭크의 치수는 최종 엔드밀 치수보다 약간 큽니다.
- 연삭 작업: 다이아몬드 연삭 휠을 사용하는 정밀 연삭기는 카바이드 블랭크를 원하는 엔드밀 형상으로 성형하는 데 사용됩니다. 여기에는 절삭날, 플루트, 생크 및 전체 치수를 만드는 작업이 포함됩니다.
- 코팅 애플리케이션: 공구 수명, 경도 및 성능을 향상시키기 위해 화학 기상 증착(CVD) 또는 물리적 기상 증착(PVD)과 같은 기술을 사용하여 엔드밀에 TiN, TiCN 또는 AlTiN과 같은 다양한 코팅을 적용할 수 있습니다.
- 품질 관리 및 검사: 엔드밀이 엄격한 치수 공차, 표면 마감 요구 사항 및 성능 표준을 충족하도록 제조 공정 전반에 걸쳐 엄격한 품질 관리 조치를 취합니다.
두 개의 플루트 엔드밀이 작동 중입니다: 다양한 응용 분야
항공우주에서 자동차까지, 그리고 그 너머까지:
- 몰드 제작: 사출 성형, 블로우 성형 및 기타 성형 공정에 사용되는 금형에 복잡한 캐비티, 디테일 및 매끄러운 표면을 생성합니다. 볼 엔드 밀은 윤곽이 있는 금형 피처를 만드는 데 탁월합니다.
- 항공우주: 항공우주 부품용 알루미늄 및 티타늄과 같은 경량의 고강도 합금을 가공할 때는 볼 엔드 밀이 제공하는 정밀하고 매끄러운 마감이 필요한 경우가 많습니다.
- 자동차: 엔진 부품, 변속기 부품 및 정밀한 공차와 매끄러운 마감이 필요한 기타 자동차 부품을 생산하며, 종종 사각 및 볼 엔드 밀을 모두 사용합니다.
- 의료 기기 제조: 높은 정밀도, 매끄러운 표면, 생체 적합성이 요구되는 복잡한 의료용 임플란트, 수술 기구 및 장치를 제작합니다. 볼 엔드 밀은 복잡한 형상을 만들 수 있는 능력 때문에 선호되는 경우가 많습니다.
- 일반 가공 및 프로토타입 제작: 다양한 산업 분야에서 프로토타입, 고정구, 지그 및 기타 가공 부품 제작에 사용되며, 사각 및 볼 엔드 밀 모두 원하는 형상에 따라 응용 분야를 찾을 수 있습니다.
TRUER: 프리미엄 투 플루트 엔드밀을 위한 신뢰할 수 있는 파트너
품질과 성능에 대한 확고한 약속:
- 정밀 엔지니어링: 트루어의 두 가지 플루트 엔드밀은 뛰어난 정확도, 반복성 및 긴 공구 수명을 제공하도록 세심하게 설계되어 정밀한 절삭과 일관된 성능을 보장합니다.
- 프리미엄 카바이드 등급: 당사는 경도, 인성 및 내마모성을 고려하여 엄선된 최고 품질의 초경 소재만을 공급하여 공구 수명을 연장하고 최적의 성능을 보장합니다.
- 애플리케이션별 전문성: 당사의 숙련된 엔지니어 팀은 고객이 선택 프로세스를 탐색하고 특정 가공 요구 사항에 이상적인 투 플루트 엔드밀을 정확히 찾아낼 수 있도록 전문적인 지침을 제공합니다.
- 사용자 지정 기능: TRUER는 가장 까다롭고 특수한 애플리케이션 요구 사항까지 충족하는 맞춤형 엔지니어링 솔루션을 전문적으로 제작합니다. 여기에는 정확한 사양에 맞게 형상, 코팅 및 크기를 조정하는 것이 포함됩니다.
트루어와 경쟁사 비교: 두 플루트 엔드밀 공급업체의 비교 분석
가공 요구 사항에 적합한 파트너 선택하기:
공급업체 | 위치 | 가격 범위(개당, 대략적인 가격) | 스페셜티 |
---|---|---|---|
TRUER | 중국 | $15 – $150+ | 타협하지 않는 품질, 애플리케이션별 설계, 경쟁력 있는 가격, 탁월한 고객 지원 |
나이아가라 커터 | 미국 | $18 – $180+ | 혁신과 품질로 유명한 고성능 엔드밀의 광범위한 제품군 |
잉거솔 절삭 공구 | 미국 | $16 – $160+ | 엔드밀, 드릴, 리머 등 생산성과 신뢰성에 중점을 둔 다양한 절삭 공구 제품군 |
케나메탈 | 미국 | $20 – $200+ | 금속 가공 솔루션 분야의 글로벌 리더로서 광범위한 절삭 공구 및 툴링 시스템을 제공합니다. |
참고: 두 개의 플루트 엔드밀 가격은 엔드밀 크기, 유형, 재질, 코팅, 주문 수량 등 다양한 요인에 의해 영향을 받습니다. 비교를 위해 항상 여러 공급업체에 견적을 요청하는 것이 좋습니다. 좋은 품질의 두 개의 플루트 엔드 밀을 적절한 가격에 구매하고 싶으신가요? 클릭 여기..
장단점 비교: 두 가지 플루트 엔드 밀의 장점과 한계
정보에 입각한 가공 결정 내리기: 균형 잡힌 관점
기능 | 장점 | 제한 사항 |
---|---|---|
효율적인 칩 배출 | - 플루트 공간이 넓어 특히 부드러운 소재에서 칩 제거가 용이합니다.<br> - 칩 재절삭 감소로 표면 조도 개선 및 공구 수명 연장 | - 칩 패킹이 문제가 될 수 있는 더 작은 칩을 생산하는 더 단단한 재료에서는 그다지 효과적이지 않습니다. |
절단 속도 및 이송 속도 향상 | - 절삭 날 수가 적을수록 절삭 속도와 이송 속도가 빨라져 생산성이 향상됩니다.<br> - 절삭 시간 단축은 전체 가공 비용 절감으로 이어질 수 있습니다. | - 특히 더 단단한 소재의 경우 플루트가 많은 엔드밀에 비해 표면 마감이 거칠어질 수 있습니다. |
낮은 절삭력 | - 과도한 힘이 가해지면 뒤틀리거나 파손될 수 있는 얇거나 섬세한 공작물 가공에 적합합니다.<br> - 공구 편향을 줄여 정확도 향상 | - 플루트가 더 많은 엔드밀만큼 견고하지 않아 고강도 황삭 작업에는 적합하지 않습니다. |
더 깊이 알아보기: 두 개의 플루트 엔드 밀에 대한 흥미로운 인사이트
기본을 넘어서:
- 센터 커팅과 비센터 커팅: 두 개의 플루트 엔드밀은 중심 절삭 또는 비중심 절삭이 가능합니다. 중심 절삭 엔드밀은 절삭날이 공구의 중심까지 연장되어 있어 공작물에 직접 절삭할 수 있습니다. 비중심 절삭 엔드밀은 절단을 시작하기 위해 미리 드릴링된 구멍 또는 램핑 기술이 필요합니다.
- 나선 각도: 플루트의 나선 각도는 칩 배출 및 절단 작용에 영향을 미칩니다. 나선 각도가 높을수록 칩을 적극적으로 제거할 수 있고, 나선 각도가 낮을수록 절단은 부드러워지지만 칩 배출 효율은 떨어집니다.
- 런아웃 및 균형: 엔드밀 런아웃과 균형은 정확도, 표면 정삭 및 공구 수명에 매우 중요합니다. 런아웃은 공구 회전의 편심이나 흔들림을 의미하며, 불균형은 진동과 조기 마모를 유발할 수 있습니다. 고품질 엔드밀은 런아웃을 최소화하고 적절한 균형을 유지하도록 제조됩니다.
자주 묻는 질문: 두 가지 플루트 엔드밀 관련 질문 해결하기
1. 플루트가 2개인 엔드밀을 사용하면 플루트가 더 많은 엔드밀에 비해 어떤 주요 이점이 있나요?
두 개의 플루트 엔드밀은 특히 부드러운 소재에서 효율적인 칩 배출에 탁월하며 절삭날 접촉이 줄어들어 절삭 속도와 이송 속도를 높일 수 있습니다. 이는 가공 시간 단축과 생산성 향상으로 이어집니다.
2. 직선형 생크 볼 엔드밀보다 직선형 생크 사각 엔드밀을 선택하는 경우는 언제인가요?
평평한 표면, 숄더, 슬롯 또는 날카로운 90도 모서리가 있는 포켓을 만들어야 하는 경우 직선형 생크 사각 엔드밀을 선택하십시오. 매끄럽고 윤곽이 있는 표면, 필렛, 반경 또는 피처 사이의 부드러운 전환이 필요한 경우 볼 엔드밀을 선택하십시오.
3. 황삭 작업에 두 개의 플루트 엔드밀을 사용할 수 있나요?
두 개의 플루트 엔드밀은 가벼운 황삭, 특히 부드러운 소재에 사용할 수 있지만, 일반적으로 정삭 작업이나 가벼운 절삭에 더 적합합니다. 무거운 황삭 작업에는 더 많은 플루트가 있고 더 견고한 디자인의 엔드밀을 사용하는 것이 좋습니다.
4. 2개의 플루트 엔드밀의 일반적인 마모 징후는 무엇이며 공구 수명을 연장하려면 어떻게 해야 하나요?
일반적인 마모 징후로는 절삭력 증가, 표면 정삭 불량, 과도한 열 발생, 절삭날의 칩핑 또는 파손 등이 있습니다. 공구 수명을 연장하려면 적절한 절삭 파라미터를 사용하고, 절삭유를 효과적으로 도포하고, 단단한 설정을 유지하고, 과도한 공구 편향을 피해야 합니다.
5. 두 개의 플루트 엔드밀에서 코팅의 중요성은 무엇인가요?
코팅은 공구 수명, 경도 및 성능을 향상시킵니다. TiN은 다용도 범용 코팅이며, TiCN은 경도와 내마모성을 높이고, AlTiN은 고열 응용 분야에서 탁월한 성능을 발휘합니다. 가공할 재료와 원하는 공구 수명에 따라 코팅을 선택하세요.