Победа над износом с непревзойденной твердостью: Глубокое погружение в технологию твердосплавных кнопок
В мире тяжелой промышленности, где абразивный износ, удары и эрозия являются постоянными противниками, традиционные материалы часто оказываются не на высоте. Заходите на сайт . твёрдый сплав кнопки - Маленькие, но могучие воины, созданные, чтобы противостоять самым суровым условиям, продлевая срок службы оборудования и увеличивая производительность.
Это полное руководство погружает в увлекательный мир твердосплавных кнопок, исследуя их состав, применение, преимущества и факторы, которые делают их идеальным износостойким решением.
Что такое твердосплавные кнопки?
Крошечные титаны выносливости: Разгадка состава и строения
Твердосплавные кнопки - это износостойкие детали, обычно круглой или шестиугольной формы, которые стратегически прикрепляются к поверхности инструментов и оборудования, подверженных сильному износу. Они состоят из твердой, износостойкой сердцевины, обычно изготовленной из цементированного карбида (карбида вольфрама), окруженной более жесткой, ударопрочной матрицей, часто из стального сплава.
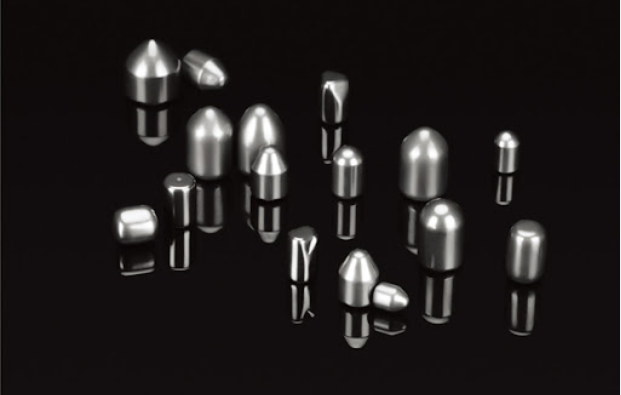
Наука, скрывающаяся за исключительной твердостью: Понимание цементированного карбида
Цементированный карбид, также известный как карбид вольфрама, - это композитный материал, известный своей исключительной твердостью, значительно превышающей твердость стали и многих других износостойких материалов. Он создается в процессе, называемом порошковой металлургией, где:
- Приготовление порошка: Мелкодисперсный порошок карбида вольфрама, известного своей чрезвычайной твердостью, смешивается с металлическим связующим, обычно кобальтом.
- Уплотнение: Порошковая смесь уплотняется под высоким давлением для придания нужной формы.
- Спекание: Спрессованная деталь нагревается до высокой температуры в контролируемой атмосфере, в результате чего связующее вещество расплавляется и сплавляет частицы карбида вольфрама вместе.
В результате спекания получается невероятно плотный и прочный композитный материал с исключительной износостойкостью.
Принцип работы твердосплавных кнопок
Стойкость против сил износа: Механизмы долговечности
Своей замечательной износостойкостью твердосплавные кнопки обязаны нескольким ключевым факторам:
- Экстремальная твердость: Сердечник из карбида вольфрама обладает одним из самых высоких уровней твердости среди всех известных материалов, что позволяет ему противостоять абразивному износу от твердых острых частиц.
- Высокая прочность на сжатие: Процесс спекания создает плотную, взаимосвязанную структуру внутри цементированного карбида, придавая ему исключительную прочность на сжатие, чтобы выдерживать высокие ударные нагрузки без разрушения или деформации.
- Прочная внешняя матрица: Окружающая стальная матрица обеспечивает дополнительную прочность и ударопрочность, предотвращая сколы или растрескивание твердосплавного сердечника в экстремальных условиях.
- Надежное крепление: Твердосплавные кнопки надежно крепятся к основному материалу, как правило, с помощью пайки или сварки, что обеспечивает их надежную фиксацию даже при сильных нагрузках и вибрациях.
Виды твердосплавных кнопок и их применение
Кнопка для каждой битвы: Изучение различных типов и их использования
Твердосплавные кнопки выпускаются в широком диапазоне типов, каждый из которых предназначен для решения конкретных задач по износу и условий эксплуатации. Некоторые распространенные типы включают:
- Круглые пуговицы: Наиболее распространенный тип, обеспечивающий хороший баланс износостойкости и ударопрочности. Используется в таких областях, как горнодобывающая промышленность, строительство и сельское хозяйство.
- Шестиугольные пуговицы: Обеспечивают повышенную износостойкость за счет большей площади поверхности. Часто используются в таких высокоабразивных областях, как бурение и дробление.
- Баллистические пуговицы: Разработаны для экстремальной ударопрочности, имеют округлую или коническую форму для отражения ударов. Используются в таких областях, как дробеструйная обработка и дробление.
- Пуговицы с шипами: Сочетание твердосплавного сердечника со стратегически расположенными шипами обеспечивает повышенное сцепление и износостойкость. Используются в таких областях, как снегоуборочная и землеройная техника.
Технические характеристики твердосплавных кнопок: Взгляд на основные характеристики
Характеристика | Описание |
---|---|
Тип | Различные варианты (круглые, шестиугольные, баллистические, шипованные) |
Материал сердцевины | Цементированный карбид (карбид вольфрама) |
Материал матрицы | Как правило, стальной сплав |
Твердость | Обычно варьируется от 85 до 95 HRA (шкала Роквелла A). |
Прочность на сжатие | Обычно превышает 6000 МПа (мегапаскалей) |
Размеры и формы | Доступен широкий диапазон размеров, форм и способов крепления (паяные, сварные) |
Оценки и стандарты | Существуют различные системы классификации, часто зависящие от производителя или отраслевых стандартов (например, ISO, ASTM). |
Применение: Где твердосплавные кнопки лучше
Победа над износом в требовательных отраслях: Обзор основных областей применения
Исключительная износостойкость, ударопрочность и долговечность твердосплавных кнопок делают их идеальными для широкого спектра применений, включая:
- Горное дело: Буровые инструменты, зубья ковша, изнашиваемые детали дробилок, желоба, бункеры.
- Строительство: Дорожные фрезы, асфальтовые фрезы, бетоноломы, оборудование для сноса зданий.
- Сельское хозяйство: Почвообрабатывающие орудия, компоненты для обработки почвы, быстроизнашивающиеся детали для сельскохозяйственной техники.
- Переработка: Молотки для шредеров, изнашиваемые детали для дробилок, компоненты для обработки материалов.
- Нефть и газ: Буровые долота, скважинные инструменты, быстроизнашивающиеся детали для насосов и клапанов.
Сравнение поставщиков твердосплавных кнопок
Навигация по рынку: Сравнительный взгляд на ведущих поставщиков
Поставщик | Расположение | Диапазон цен (за штуку) | Специальности |
---|---|---|---|
Боарт Лонгиер | Австралия | $10 – $60+ | Буровые инструменты и быстроизнашивающиеся детали для горнодобывающей промышленности и строительства |
Корпорация ЭСКО | США | $8 – $50+ | Инструменты для обработки грунта и быстроизнашивающиеся детали для строительства и горнодобывающей промышленности |
Atlas Copco | Швеция | $12 – $70+ | Буровое оборудование и быстроизнашивающиеся детали для горнодобывающей промышленности, строительства и инфраструктуры |
Примечание: Цены являются приблизительными и могут значительно отличаться в зависимости от размера пуговицы, сорта, заказанного количества и других факторов.
Преимущества и недостатки твердосплавных кнопок
Взвешивание плюсов и минусов: сбалансированная перспектива
Преимущества | Недостатки |
---|---|
Исключительная износостойкость | Более высокая первоначальная стоимость по сравнению с некоторыми альтернативами |
Высокая ударопрочность | Может быть хрупким при определенных условиях воздействия |
Универсальность для различных применений | Для правильного крепления могут потребоваться специальные методы пайки или сварки |
Длительный срок службы, сокращение времени обслуживания и простоев | Производительность зависит от правильного выбора сорта и условий эксплуатации |
За пределами основ: Интересные факты о твердосплавных кнопках
- От лампочек до защиты от износа: В основе исключительной твердости твердосплавных кнопок лежит тот же материал, что и в нитях накаливания ламп - вольфрам.
- Глобальный рынок: Мировой рынок твердосплавных кнопок является значительным и растущим, что обусловлено увеличением спроса со стороны таких отраслей, как горнодобывающая промышленность, строительство и развитие инфраструктуры.
- Непрерывные инновации: Производители постоянно исследуют и разрабатывают новые марки твердого сплава, конструкции кнопок и способы крепления, чтобы еще больше повысить производительность, срок службы и возможности применения.
Почему TRUER выбирает твердосплавные пуговицы?
Компания TRUER является надежным партнером в предоставлении высокопроизводительных решений для твердосплавных кнопок. Мы предлагаем:
- Бескомпромиссное качество: Мы поставляем наши твердосплавные кнопки от авторитетных производителей, известных своими строгими мерами контроля качества, что обеспечивает стабильную производительность и надежность.
- Индивидуальные решения: Наша команда экспертов тесно сотрудничает с клиентами, чтобы понять их конкретные требования к применению и рекомендовать оптимальную марку твердого сплава, конструкцию кнопки и способ крепления.
- Конкурентные цены: Мы стремимся обеспечить конкурентоспособные цены без ущерба для качества, гарантируя нашим клиентам наилучшее соотношение цены и качества.
- Исключительная поддержка клиентов: Наша приверженность удовлетворению потребностей клиентов выходит за пределы точки продажи. Мы предлагаем техническую поддержку, руководство и помощь, чтобы наши клиенты максимально увеличили производительность и срок службы твердосплавных кнопок.
Часто задаваемые вопросы о твердосплавных кнопках
1. Как выбрать подходящую марку твердого сплава для моей задачи?
Оптимальная марка зависит от конкретных механизмов износа, обрабатываемых материалов и условий эксплуатации. Для получения индивидуальных рекомендаций рекомендуется проконсультироваться с поставщиком твердосплавных кнопок или экспертом по материаловедению.
2. Какие существуют различные способы крепления твердосплавных кнопок?
К распространенным методам крепления относятся пайка и сварка. Пайка предполагает использование присадочного металла для соединения кнопки с основным материалом, в то время как сварка использует тепло и давление для скрепления материалов.
3. Как продлить срок службы твердосплавных кнопок?
Правильное обращение, хранение, очистка и обслуживание, а также оптимизация рабочих параметров могут значительно продлить срок службы кнопок.
4. Какие существуют альтернативы твердосплавным кнопкам для защиты от износа?
Альтернативой могут служить твердые наплавочные сплавы, керамические плитки и полиуретановые покрытия. Однако твердосплавные кнопки часто обеспечивают более высокую износостойкость, ударопрочность и общий срок службы в сложных условиях эксплуатации.
5. Где я могу найти надежного поставщика твердосплавных кнопок?
TRUER является надежным источником высококачественных твердосплавных кнопок. Свяжитесь с нами сегодня, чтобы обсудить ваши конкретные требования и изучить наш широкий спектр решений.