Автомобильная промышленность стремится к инновациям и постоянно ищет материалы, которые повышают производительность, эффективность и долговечность. Заходите на сайт . карбид вольфрама заготовки - невероятно твердые, износостойкие компоненты, которые служат основой для широкого спектра важнейших автомобильных деталей. Данное подробное руководство погружает в многогранный мир заготовок из карбида вольфрама, исследуя их свойства, области применения в автомобильном секторе и факторы, способствующие их растущему внедрению.
Что такое заготовки из карбида вольфрама?
Основа долговечности: Непревзойденная твердость и износостойкость
Заготовки из карбида вольфрама представляют собой предварительно спеченные детали, имеющие форму, близкую к сетке, состоящие из частиц карбида вольфрама, соединенных металлическим связующим, обычно кобальтом. Этот уникальный состав придает исключительную твердость и износостойкость, превосходящую даже самые прочные стали.
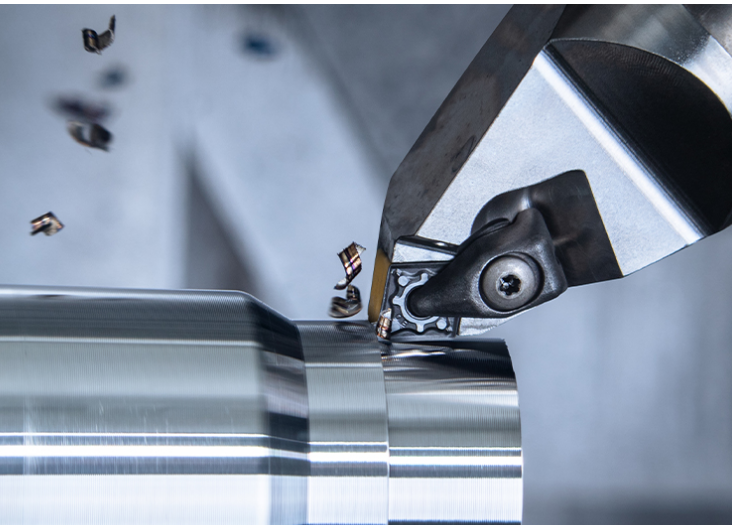
Свойства заготовок из карбида вольфрама: Для самых требовательных областей применения
Таблица 1: Основные свойства заготовок из карбида вольфрама для автомобильной промышленности
Недвижимость | Описание | Преимущества в автомобильной промышленности |
---|---|---|
Высокая твердость | Измеряет устойчивость к вдавливанию и царапинам. Карбид вольфрама входит в число самых твердых материалов. | Позволяет компонентам выдерживать экстремальный износ, продлевая срок службы и сокращая объем технического обслуживания. |
Отличная износостойкость | Противостоит потере материала из-за трения, истирания или эрозии. | Очень важна для деталей, подверженных постоянному трению, таких как компоненты двигателя и режущие инструменты. |
Высокая прочность на сжатие | Выдерживает большие сжимающие усилия без деформации и разрушения. | Незаменимы для деталей, подвергающихся значительному давлению, таких как подшипники и седла клапанов. |
Хорошая коррозионная стойкость | Устойчив к разрушению под воздействием химикатов, влаги и агрессивных сред. | Обеспечивает долговечность в сложных автомобильных условиях, особенно под капотом. |
Высокая горячая твердость | Сохраняет твердость и прочность при повышенных температурах. | Критически важен для компонентов, работающих при высоких температурах, таких как детали двигателей и выхлопных систем. |
Применение в автомобильной промышленности: Где долговечность сочетается с производительностью
Заготовки из карбида вольфрама играют важнейшую роль в широком спектре автомобильных применений, включая:
- Компоненты двигателя: Седла клапанов, направляющие клапанов, топливные форсунки и поршневые кольца выигрывают от чрезвычайной износостойкости и высокотемпературных характеристик карбида вольфрама.
- Трансмиссионные системы: В шестернях, подшипниках и кольцах синхронизаторов используется карбид вольфрама, который выдерживает высокие нагрузки, трение и износ, обеспечивая плавную и эффективную передачу мощности.
- Тормозные системы: Тормозные колодки, тормозные диски и компоненты ABS используют твердость и износостойкость карбида вольфрама для улучшения тормозных характеристик и продления срока службы.
- Рулевое управление и подвеска: Компоненты рулевого управления, втулки подвески и ступичные подшипники получают преимущества от прочности и износостойкости карбида вольфрама, обеспечивая точность управления и длительный срок службы.
- Производственное оборудование: Режущие инструменты, штампы и быстроизнашивающиеся детали, используемые в автомобилестроении, благодаря исключительной твердости карбида вольфрама используются для обработки и придания формы различным компонентам.
Тенденции и движущие силы рынка: Повышение спроса на долговечность
Несколько факторов способствуют росту использования заготовок из карбида вольфрама в автомобильной промышленности:
- Фокус на топливной эффективности: Более легкие автомобили с более эффективными двигателями требуют прочных компонентов, способных выдерживать повышенные нагрузки и рабочие температуры.
- Жесткие нормы выбросов: Передовые технологии двигателей и системы контроля выбросов требуют применения прочных материалов, таких как карбид вольфрама, для работы при повышенном давлении и температуре сгорания.
- Спрос на долговечность автомобилей: Потребители ожидают, что автомобили прослужат дольше, что обуславливает потребность в компонентах с исключительной износостойкостью и увеличенным сроком службы.
- Рост числа электромобилей (EV): Электромобили представляют собой уникальные задачи и возможности для материаловедения. Свойства карбида вольфрама позволяют использовать его для различных компонентов EV, включая электродвигатели, аккумуляторные системы и силовую электронику.
Сравнение поставщиков: Навигация по рынку заготовок из карбида вольфрама
Таблица 2: Ведущие поставщики заготовок из карбида вольфрама для автомобильной промышленности
Поставщик | Расположение | Диапазон цен (USD/кг) | Специальности |
---|---|---|---|
Kennametal | США | $80 – $250+ | Широкий ассортимент марок твердых сплавов, индивидуальные рецептуры, технический опыт |
Sandvik Coromant | Швеция | $90 – $280+ | Высокопроизводительные марки твердого сплава, прецизионная обработка, поддержка в применении |
Элемент шесть | Великобритания, Глобальный | $100 – $300+ | Передовые твердосплавные материалы, специализированные марки для сложных условий эксплуатации |
Ceratizit | Люксембург | $75 – $230+ | Экономически эффективные решения, широкий ассортимент стандартных марок, глобальное присутствие |
TRUER | Китай | $70 – $220+ | Высококачественные заготовки из твердого сплава, конкурентоспособные цены, быстрые сроки выполнения индивидуальных заказов |
Примечание: Цены являются приблизительными и зависят от сорта, размера, количества и рыночных условий.
Преимущества и ограничения: Сбалансированный взгляд на производительность
Таблица 3: Плюсы и минусы использования заготовок из карбида вольфрама в автомобильной промышленности
Преимущества | Ограничения |
---|---|
Исключительная долговечность и износостойкость: Значительно увеличивает срок службы компонентов, снижает потребность в обслуживании и повышает надежность. | Высокая начальная стоимость: Заготовки из карбида вольфрама обычно дороже стальных аналогов. |
Улучшенная производительность и эффективность: Повышает эффективность работы двигателя, оптимизирует передачу мощности и улучшает тормозные характеристики. | Хрупкая натура: Восприимчивость к сколам и разрушению при сильных ударных нагрузках. |
Уменьшенный вес и размер: Позволяет использовать более компактные и легкие компоненты без ущерба для прочности и долговечности. | Задачи механической обработки: Требуются специальные технологии и оборудование для обработки из-за высокой твердости. |
За гранью пустоты: Факторы, влияющие на производительность и долголетие
Реализация всего потенциала заготовок из карбида вольфрама в автомобильной промышленности выходит за рамки выбора материала. К ключевым моментам относятся:
- Выбор класса: Выбор подходящей марки твердого сплава в зависимости от конкретных требований к применению, таких как износостойкость, ударопрочность и коррозионная стойкость.
- Технологии нанесения покрытий: Нанесение специализированных покрытий позволяет дополнительно повысить износостойкость, уменьшить трение и улучшить эксплуатационные характеристики в сложных условиях.
- Оптимизация дизайна: Проектирование компонентов с использованием уникальных свойств карбида вольфрама с учетом таких факторов, как распределение напряжений, характер износа и тепловое расширение.
Почему вы выбираете TRUER для своих потребностей в заготовках из карбида вольфрама?
Компания TRUER является ведущим поставщиком высококачественных заготовок из карбида вольфрама, предлагая:
- Непоколебимая приверженность качеству: TRUER использует высококачественное сырье и строгие меры контроля качества на протяжении всего производственного процесса, чтобы обеспечить стабильную производительность и надежность.
- Техническая экспертиза: Команда опытных инженеров TRUER обладает глубокими знаниями о марках твердых сплавов, их применении и методах обработки, обеспечивая ценную поддержку и руководство.
- Конкурентные цены: Эффективная работа и клиентоориентированный подход позволяют TRUER предлагать конкурентоспособные цены без ущерба для качества.
- Быстрые сроки выполнения заказа: Компания TRUER понимает важность своевременной доставки и стремится обеспечить быстрые сроки выполнения заказов, в том числе и индивидуальных.
Вопросы и ответы: Ответы на вопросы о заготовках из карбида вольфрама
1. Какой сорт карбида вольфрама лучше всего подходит для моего конкретного автомобильного применения?
Выбор оптимальной марки зависит от таких факторов, как условия эксплуатации, механизмы износа и требуемые свойства. Технические специалисты TRUER могут порекомендовать наиболее подходящую марку, исходя из ваших конкретных потребностей.
2. Можно ли наносить покрытие на заготовки из карбида вольфрама для улучшения их свойств?
Да, различные покрытия, такие как CVD (химическое осаждение из паровой фазы) и PVD (физическое осаждение из паровой фазы), могут дополнительно повысить износостойкость, уменьшить трение и улучшить эксплуатационные характеристики в сложных условиях.
3. Какие ключевые моменты необходимо учитывать при обработке заготовок из карбида вольфрама?
Обработка карбида вольфрама требует специального оборудования, инструмента и опыта из-за его чрезвычайной твердости. Компания TRUER может предоставить рекомендации по параметрам обработки и передовым методам.
4. Как обеспечить качество и постоянство заготовок из карбида вольфрама?
TRUER применяет строгие меры контроля качества на протяжении всего производственного процесса, включая анализ материалов, проверку размеров и тестирование характеристик.
5. Предлагает ли компания TRUER индивидуальные решения по изготовлению заготовок из карбида вольфрама?
Да, компания TRUER специализируется на предоставлении индивидуальных решений, отвечающих конкретным требованиям. Их команда может разработать и изготовить заготовки для решения уникальных задач.