Побеждая износ, по одной кнопке за раз: глубокое погружение в долговечность
В сложных условиях горнодобывающей, строительной и тяжелой промышленности, где царят абразивное и ударное воздействие, обычные материалы часто оказываются не на высоте. Заходите на сайт . твердый твёрдый сплав кнопки - Созданные для работы в экстремальных условиях, эти маленькие, но могучие компоненты переопределяют износостойкость, расширяя границы срока службы и производительности оборудования.
Данное руководство погружается в глубины твердосплавных кнопок, исследуя их тонкости, области применения и факторы, которые выделяют их в качестве оптимального решения для борьбы с износом.
Что такое твердосплавные кнопки?
Крошечные титаны выносливости: Разгадка состава и строения
Твердосплавные кнопки - это износостойкие детали, которые обычно припаиваются или привариваются к поверхности инструментов и оборудования, подвергающихся сильному абразивному износу, ударам и эрозии. В отличие от кнопок с твердосплавной сердцевиной и менее прочным внешним слоем, цельные твердосплавные кнопки полностью состоят из цементированного карбида - композитного материала, известного своей исключительной твердостью и износостойкостью.
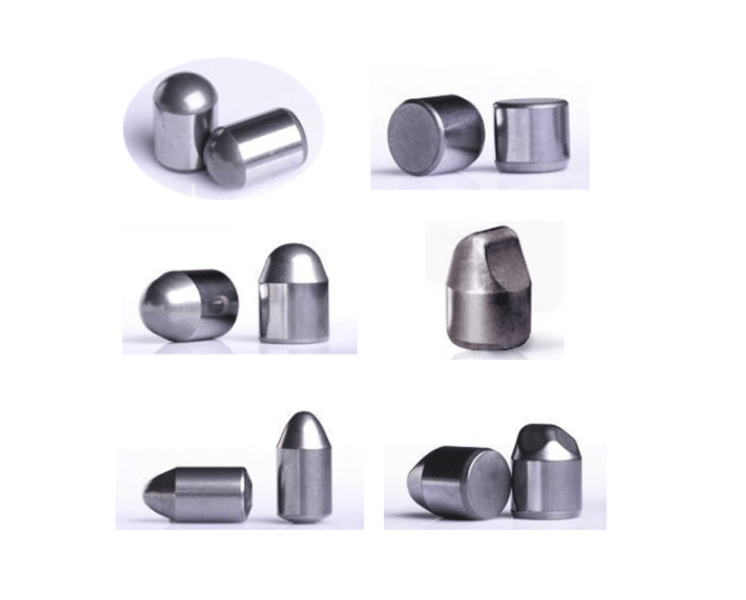
Сила цементированного карбида: Выигрышная комбинация твердости и прочности
Цементированный карбид, также известный как карбид вольфрама, создается с помощью процесса, называемого порошковой металлургией. Мелкодисперсный порошок карбида вольфрама, известного своей чрезвычайной твердостью, смешивается с металлическим связующим веществом, обычно кобальтом, а затем подвергается воздействию высоких температур и давления. В процессе спекания материалы сплавляются, образуя невероятно плотный и прочный композитный материал.
Принцип работы кнопок из твердого сплава
Standing Strong Against the Forces of Wear: Наука, стоящая за исключительной долговечностью
Замечательная износостойкость твердых твердосплавных кнопок обусловлена уникальными свойствами цементированного карбида:
- Экстремальная твердость: Карбид вольфрама, являющийся основным компонентом, обладает одной из самых высоких твердостей среди всех известных материалов, значительно превышающей твердость стали и других распространенных износостойких материалов. Эта исключительная твердость позволяет кнопкам выдерживать абразивный износ твердыми, острыми частицами.
- Высокая прочность на сжатие: Процесс спекания создает плотную, взаимосвязанную структуру внутри цементированного карбида, придавая ему исключительную прочность на сжатие. Это позволяет кнопкам выдерживать высокие ударные нагрузки без разрушения или деформации.
- Химическая стойкость: Цементированный карбид демонстрирует отличную устойчивость к коррозии и химическому воздействию, что делает его пригодным для использования в суровых условиях, где другие материалы поддаются разрушению.
Навигация по миру кнопок из твердого сплава: Типы, марки и области применения
Не все пуговицы созданы одинаковыми: Понимание нюансов разных классов
Твердосплавные кнопки выпускаются в широком диапазоне марок, каждая из которых предназначена для решения конкретных задач по износу и условий эксплуатации. Марка твердосплавной кнопки определяется такими факторами, как:
- Размер зерна: Размер частиц карбида вольфрама в цементированной карбидной матрице влияет на твердость и прочность. Более мелкие зерна обычно обеспечивают более высокую твердость и износостойкость, а более крупные зерна - повышенную вязкость и ударопрочность.
- Содержание кобальта: Процентное содержание кобальтовой связки в цементированном карбиде влияет на твердость, прочность и стоимость кнопки. Более высокое содержание кобальта обычно приводит к повышению вязкости и ударопрочности, но снижает твердость.
- Другие добавки: Производители могут включать другие добавки, такие как карбид титана или карбид тантала, для улучшения специфических свойств, таких как износостойкость, коррозионная стойкость или высокотемпературные характеристики.
Технические характеристики кнопок из твердого сплава: Взгляд на основные характеристики
Характеристика | Описание |
---|---|
Тип | Твердый карбид |
Материал | Цементированный карбид (карбид вольфрама) |
Твердость | Обычно варьируется от 88 до 95 HRA (шкала Роквелла A). |
Прочность при поперечном разрыве (TRS) | Мера сопротивления материала изгибу и разрушению; зависит от марки. |
Прочность на сжатие | Обычно превышает 6000 МПа (мегапаскалей) |
Коррозионная стойкость | Превосходная устойчивость к большинству химикатов и агрессивным средам |
Размеры и формы | Выпускаются в широком диапазоне размеров, форм (круглые, шестигранные, баллистические) и способов крепления (паяные, сварные) |
Оценки и стандарты | Существуют различные системы классификации, часто зависящие от производителя или отраслевых стандартов (например, ISO, ASTM). |
Области применения: Где кнопки из твердого сплава занимают первое место
Победа над износом в требовательных отраслях: Обзор основных областей применения
Исключительная износостойкость, ударопрочность и долговечность кнопок из твердого сплава делают их идеальными для широкого спектра применений, включая:
- Добыча и выемка грунта: Буровой инструмент, зубья ковша, режущие кромки, изнашиваемые пластины и другие компоненты, используемые в горнодобывающем и землеройном оборудовании.
- Строительство и снос: Дорожные фрезы, асфальтовые фрезы, бетоноломы и оборудование для сноса зданий.
- Сельское хозяйство: Почвообрабатывающие орудия, компоненты для обработки почвы и быстроизнашивающиеся детали для сельскохозяйственной техники.
- Переработка: Молотки шредеров, изнашиваемые детали дробилок и другие компоненты, используемые в оборудовании для переработки отходов.
- Обработка материалов: Желоба, бункеры, циклоны и другие подверженные износу компоненты систем обработки материалов.
Сравнение поставщиков твердосплавных кнопок
Навигация по рынку: Сравнительный взгляд на ведущих поставщиков
Поставщик | Расположение | Диапазон цен (за штуку) | Специальности |
---|---|---|---|
Sandvik Coromant | Швеция | $5 – $50+ | Широкий ассортимент марок и геометрий; специализированные решения для конкретных областей применения |
TRUER | Китай | $4 – $40+ | Инновационные конструкции кнопок; особое внимание уделяется оптимизации производительности и анализу износа |
Элемент шесть | ВЕЛИКОБРИТАНИЯ | $6 – $60+ | Высокопроизводительные марки для экстремального износа; опыт работы с материалами на основе алмазов |
Примечание: Цены являются приблизительными и могут значительно отличаться в зависимости от размера пуговицы, сорта, заказанного количества и других факторов.
Преимущества и недостатки кнопок из твердого сплава
Взвешивание плюсов и минусов: сбалансированная перспектива
Преимущества | Недостатки |
---|---|
Исключительная износостойкость | Более высокая первоначальная стоимость по сравнению с некоторыми альтернативами |
Высокая ударопрочность | Может быть хрупким при определенных условиях воздействия |
Отличная коррозионная стойкость | Для правильного крепления могут потребоваться специальные методы пайки или сварки |
Длительный срок службы, сокращение времени обслуживания и простоев | Не подходит для всех областей применения; производительность зависит от правильного выбора марки и условий эксплуатации |
За пределами основ: Интересные факты о кнопках из твердого карбида
- От лампочек до защиты от износа: Тот же материал, что используется в нитях накаливания ламп, вольфрам, лежит в основе исключительной твердости твердых карбидных кнопок.
- Глобальный рынок: Мировой рынок твердосплавных кнопок является значительным и растущим, что обусловлено увеличением спроса со стороны таких отраслей, как горнодобывающая промышленность, строительство и развитие инфраструктуры.
- Непрерывные инновации: Производители постоянно исследуют и разрабатывают новые марки твердого сплава, конструкции кнопок и способы крепления, чтобы еще больше повысить производительность, срок службы и возможности применения.
Часто задаваемые вопросы о кнопках из твердого сплава
1. Как выбрать подходящую марку твердого сплава для моей задачи?
Оптимальный класс зависит от конкретных механизмов износа, обрабатываемых материалов и условий эксплуатации. Проконсультируйтесь с твёрдосплавная кнопка Для получения индивидуальных рекомендаций рекомендуется обратиться к поставщику или эксперту по материаловедению.
2. Какие существуют различные способы крепления кнопок из твердого сплава?
К распространенным методам крепления относятся пайка и сварка. Пайка предполагает использование присадочного металла для соединения кнопки с основным материалом, в то время как сварка использует тепло и давление для скрепления материалов.
3. Как продлить срок службы кнопок из твердого сплава?
Правильное обращение, хранение, очистка и обслуживание, а также оптимизация рабочих параметров могут значительно продлить срок службы кнопок.
4. Какие существуют альтернативы кнопкам из твердого сплава для защиты от износа?
Альтернативой могут служить наплавочные сплавы, керамические плитки и полиуретановые покрытия. Однако кнопки из твердого сплава часто обеспечивают более высокую износостойкость, ударопрочность и общий срок службы в сложных условиях эксплуатации.
5. Где я могу найти надежного поставщика кнопок из твердого сплава?
[Название вашей компании] является надежным источником высококачественных кнопок из твердого сплава. Свяжитесь с нами сегодня, чтобы обсудить ваши конкретные требования и изучить наш широкий спектр решений.