заточка твердосплавных пластин являются важнейшими инструментами в мире обработки, рассчитанными на долговечность и точность. Но даже самые прочные твердосплавные пластины нуждаются в заточке для поддержания их работоспособности. В этом подробном руководстве рассматриваются все тонкости заточки твердосплавных пластин - от понимания их состава до выбора правильного метода заточки. Независимо от того, являетесь ли вы опытным машинистом или только начинаете, это руководство расскажет вам обо всем, что необходимо знать.
Обзор заточки твердосплавных пластин
Твердосплавные вставки - это маленькие, но могучие детали, используемые в металлообработке и обладающие удивительной твердостью и износостойкостью. Эти пластины изготавливаются из комбинации карбида вольфрама и кобальта, что делает их невероятно прочными. Однако со временем они могут потерять свою кромку, что требует заточки для восстановления их режущих свойств.
Зачем затачивать твердосплавные пластины?
Заточка твердосплавных пластин имеет решающее значение для поддержания их эффективности и продления срока службы. Затупившиеся пластины могут привести к некачественным резам, повышенному износу инструмента и даже повреждению заготовки. Регулярная заточка гарантирует, что пластины останутся острыми, обеспечивая более чистые резы и повышая общую производительность.
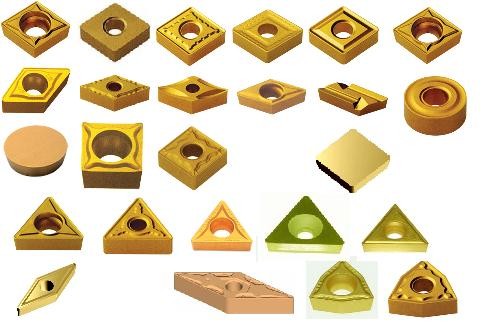
Виды заточки твердосплавных пластин
Твердосплавные вставки бывают разных типов, каждый из которых предназначен для определенных целей. Вот таблица с описанием некоторых распространенных типов твердосплавных вставок и их применения:
Тип вставки | Описание | Приложение |
---|---|---|
CNMG | Отрицательный угол наклона, двусторонний | Токарные и фрезерные работы |
TNMG | Треугольный, отрицательный угол наклона | Черновая и чистовая обработка |
SNMG | Квадрат, отрицательный угол наклона | Сильная черновая обработка |
DNMG | Алмазная форма, отрицательный угол наклона | Тонкая отделка |
WNMG | Тригон, отрицательный угол наклона | Средняя и тяжелая черновая обработка |
CCMT | Положительный угол наклона, односторонний | Финишная обработка и легкая резка |
DCMT | Алмазная форма, положительный угол наклона | Прецизионная отделка |
VBMT | Ромбическая форма, положительный угол наклона | Тонкая отделка и профилирование |
RCMT | Круглый, положительный угол наклона | Контурирование и профилирование |
APKT | Прямоугольная форма, положительный угол наклона | Фрезерование |
Применение Заточка твердосплавных пластин
Заточка твердосплавных пластин необходима для различных процессов обработки. Для разных областей применения требуются различные типы пластин и методы заточки:
Приложение | Тип вставки | Техника заточки |
---|---|---|
Развернуть | КНМГ, ТНМГ, ДНМГ | Хонингование, шлифование |
Фрезерование | APKT, RCMT | Шлифование алмазным кругом |
Бурение | CCMT, DCMT | Хонингование алмазной пастой |
Профилирование | VBMT, RCMT | Ручная заточка алмазными камнями |
Черновая обработка | SNMG, WNMG | Шлифование кругами CBN |
Свойства материалов твердосплавных вставок
Понимание свойств материала твердосплавных пластин имеет решающее значение для выбора правильного метода заточки. Вот описание основных свойств:
Недвижимость | Описание |
---|---|
Твердость | Очень жесткие, обычно 85-92 HRA |
Жесткость | Высокая прочность, устойчивость к поломкам |
Износостойкость | Отличная износостойкость благодаря карбидному составу |
Термическая стабильность | Сохраняет твердость при высоких температурах |
Химическая стойкость | Устойчивость к коррозии и химическим реакциям |
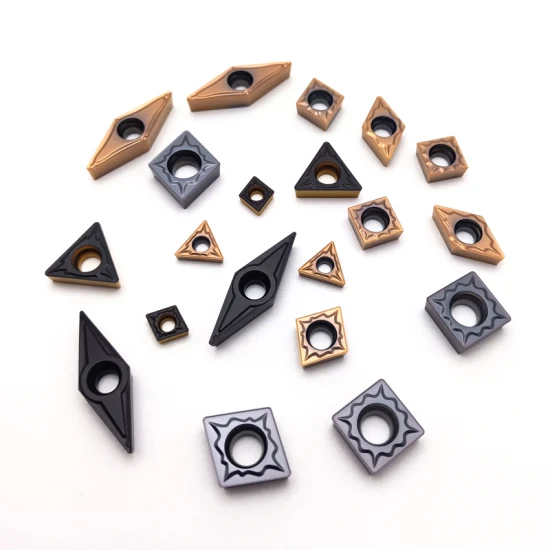
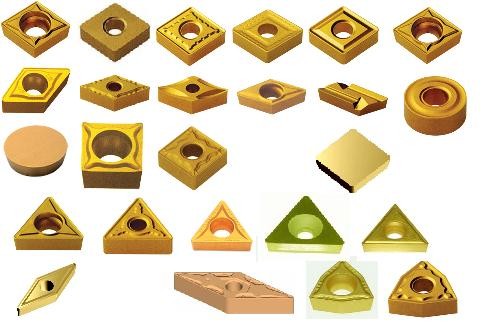
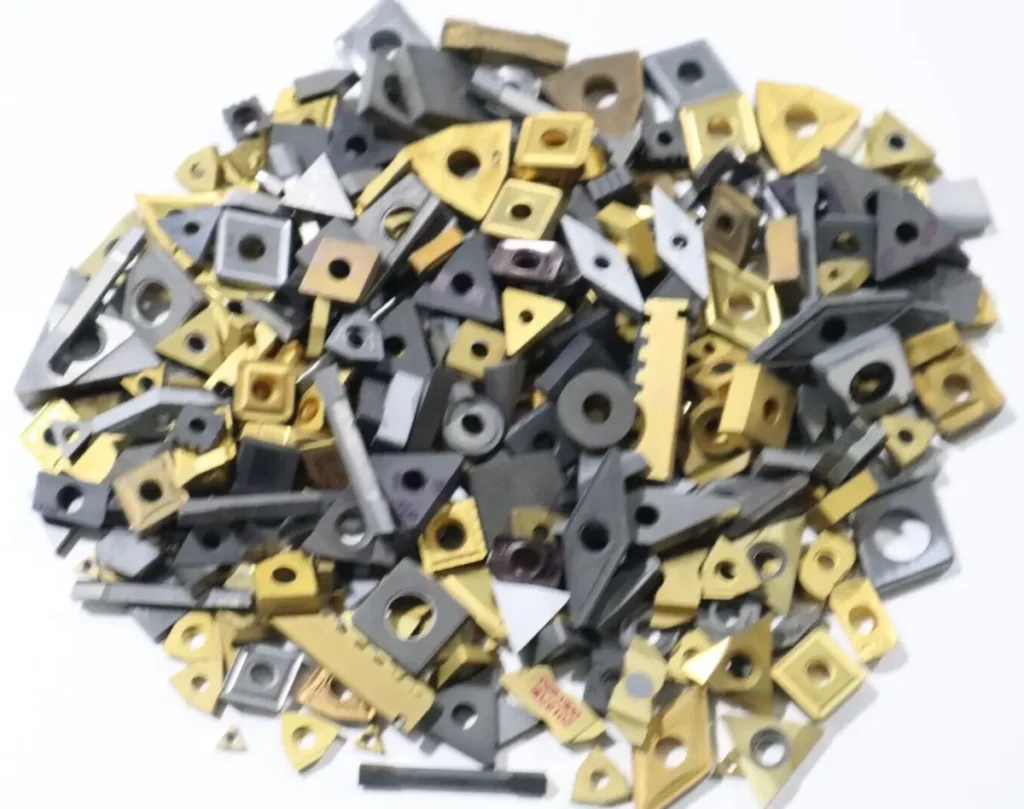
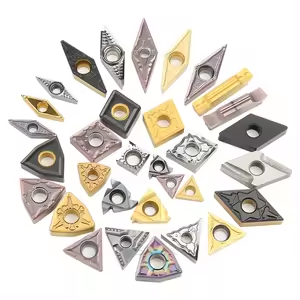
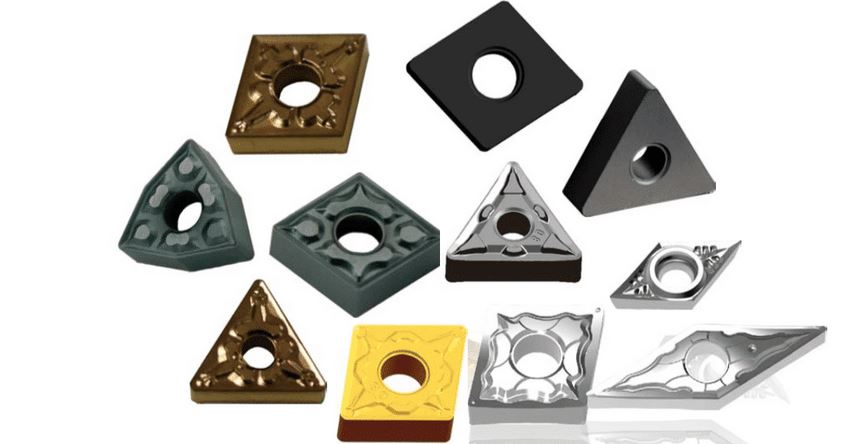
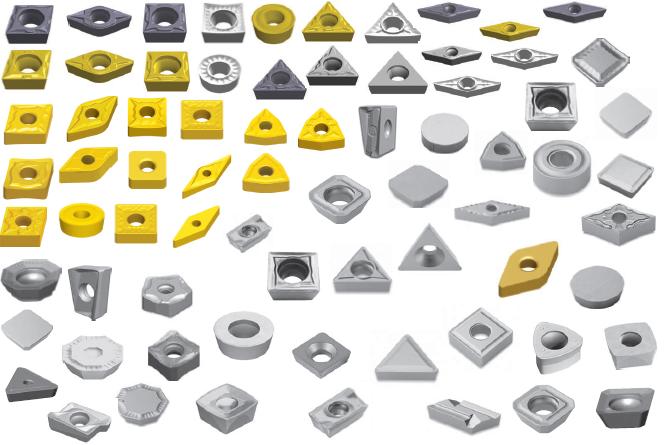
Состав, свойства и характеристики
Твердосплавные вставки состоят в основном из карбида вольфрама и кобальта, каждый из которых вносит свой вклад в их уникальные характеристики:
Компонент | Роль | Характеристики |
---|---|---|
Карбид вольфрама | Обеспечивает твердость | Чрезвычайно твердый и износостойкий |
Кобальт | Действует как связующее вещество | Повышает прочность и долговечность |
Карбид титана | Дополнительное дополнение | Повышает твердость и износостойкость |
Карбид тантала | Дополнительное дополнение | Повышает прочность и термостойкость |
Твердость, прочность и износостойкость
Твердосплавные вставки известны своей впечатляющей твердостью, прочностью и износостойкостью. Вот сравнение этих свойств:
Недвижимость | Описание |
---|---|
Твердость | От 85 до 92 HRA, что делает их одним из самых твердых материалов. |
Прочность | Высокая прочность на сжатие, устойчивость к деформации |
Износостойкость | Превосходная износостойкость, идеально подходит для высокоскоростной обработки |
Технические характеристики, размеры, форма и стандарты
Твердосплавные вставки имеют различные формы и размеры, соответствуют промышленным стандартам для обеспечения стабильной работы:
Спецификация | Подробности |
---|---|
Размеры | Распространенные размеры: вставки 1/4″, 1/2″, 3/4″. |
Формы | Квадратные, треугольные, ромбовидные, круглые, ромбические |
Стандарты | Стандарты ISO, ANSI и DIN обеспечивают совместимость и качество |
Поставщики и ценовая политика
Выбор правильного поставщика имеет решающее значение для получения высококачественных твердосплавных пластин. Вот список некоторых авторитетных поставщиков и их ценовая политика:
Поставщик | Расположение | Диапазон цен |
---|---|---|
Sandvik Coromant | Глобальная | $5 - $20 за вставку |
Kennametal | Глобальная | $10 - $30 за вставку |
ИСКАР | Глобальная | $8 - $25 за вставку |
Mitsubishi Materials | Глобальная | $12 - $35 за вставку |
Sumitomo Electric | Глобальная | $15 - $40 за вставку |
Выбор правильного Заточка твердосплавных пластин
Выбор правильного метода заточки зависит от различных факторов, включая тип пластины, обрабатываемый материал и желаемое качество обработки. Вот руководство, которое поможет вам выбрать подходящие твердосплавные вставки для заточки:
Фактор | Рассмотрение | Рекомендуемый метод заточки |
---|---|---|
Тип вставки | Положительный и отрицательный рейк | Шлифование алмазным кругом для отрицательной граблины, хонингование алмазной пастой для положительной граблины |
Материал | Твердость и прочность | Для более твердых материалов требуются алмазные круги, для более мягких материалов можно использовать круги CBN |
Желаемая отделка | Грубая обработка против отделки | Для финишной обработки требуется более тонкое хонингование, для черновой - более грубое шлифование. |
Преимущества и ограничения
Понимание преимуществ и недостатков заточки твердосплавных пластин поможет вам принять взвешенное решение:
Аспект | Преимущества | Ограничения |
---|---|---|
Производительность | Сохраняет эффективность резания, продлевает срок службы инструмента | Требует точной техники, может отнимать много времени |
Стоимость | Экономичность по сравнению с заменой вставок | Первоначальные инвестиции в заточное оборудование |
Универсальность | Может использоваться для различных процессов обработки | Ограничено типом имеющегося заточного оборудования |
Техники заточки: Как выбрать правильный метод
Выбор правильного метода заточки имеет решающее значение для поддержания работоспособности твердосплавных пластин. Здесь подробно рассматриваются некоторые распространенные методы заточки и их применение:
Заточка алмазными камнями
Хонингование алмазными камнями - это точный метод, идеально подходящий для финишной обработки и профилирования. Этот метод предполагает ручное хонингование вставки алмазным камнем с мелкой зернистостью, обеспечивая острую кромку без снятия большого количества материала.
Шлифование с помощью кругов CBN
Круги CBN (Cubic Boron Nitride) отлично подходят для черновой обработки и снятия тяжелого материала. В этом методе круг CBN используется для шлифовки вставки, обеспечивая острую кромку и сохраняя геометрию вставки.
Шлифование алмазным кругом
Шлифование алмазным кругом - это универсальный метод, подходящий как для черновой, так и для чистовой обработки. Этот метод предполагает использование алмазного круга для шлифовки вставки, обеспечивая острую и прочную кромку.
Хонингование алмазной пастой
Хонингование алмазной пастой - это метод тонкой настройки, идеально подходящий для достижения зеркального блеска. Эта техника включает в себя нанесение алмазной пасты на хонинговальный инструмент и тщательное хонингование вставки, обеспечивающее бритвенную остроту кромки.
Заточка твердосплавных пластин: Пошаговое руководство
Заточка твердосплавных пластин требует точности и правильных инструментов. Вот пошаговое руководство, которое поможет вам начать работу:
- Соберите инструменты: Убедитесь, что у вас есть необходимые инструменты для заточки, включая алмазные камни, круги CBN и хонинговальную пасту.
- Очистите вставку: Удалите любой мусор или налет на вставке с помощью мягкой щетки и чистящего раствора.
- Закрепите вставку: Поместите вставку в надежное крепление, чтобы предотвратить ее перемещение во время заточки.
- Выберите метод повышения резкости: Выберите подходящий метод заточки в зависимости от типа вставки и желаемой чистоты.
- Заточка вставки: Осторожно заточите вставку, сохраняя постоянное давление и угол наклона.
- Осмотрите край: Проверьте остроту и равномерность края вставки. При необходимости повторите процесс.
- Чистить и хранить: Снова очистите вставку и храните ее в безопасном месте во избежание повреждений.
Сравнение методов заточки: Что лучше?
Различные методы заточки имеют свои преимущества и ограничения. Вот сравнение, которое поможет вам выбрать лучший метод для ваших нужд:
Метод | Преимущества | Ограничения |
---|---|---|
Алмазные камни | Точные, идеально подходят для отделки | Требует времени, требует навыков |
Колеса CBN | Эффективный, хорошо подходит для черновой обработки | При неаккуратном использовании может быть удалено слишком много материала |
Шлифование алмазным кругом | Универсальный, прочный край | Требуется специализированное оборудование |
Хонингование алмазной пастой | Тонкая отделка, острый край | Лучше всего подходит для небольших корректировок, но не для серьезного повышения резкости |
Советы по обслуживанию при заточке твердосплавных пластин
Правильный уход имеет решающее значение для обеспечения долговечности и производительности твердосплавных пластин. Вот несколько советов, которые помогут сохранить ваши пластины в отличной форме:
- Регулярная уборка: Регулярно очищайте вставки от мусора и налета.
- Правильное хранение: Храните вкладыши в сухом, надежном месте во избежание повреждений.
- Своевременная заточка: Затачивайте пластины, как только заметите снижение производительности, чтобы избежать чрезмерного износа.
- Используйте качественные инструменты: Для достижения наилучших результатов приобретите высококачественные инструменты для заточки.
- Износ монитора: Следите за степенью износа пластин и соответственно корректируйте технику заточки.
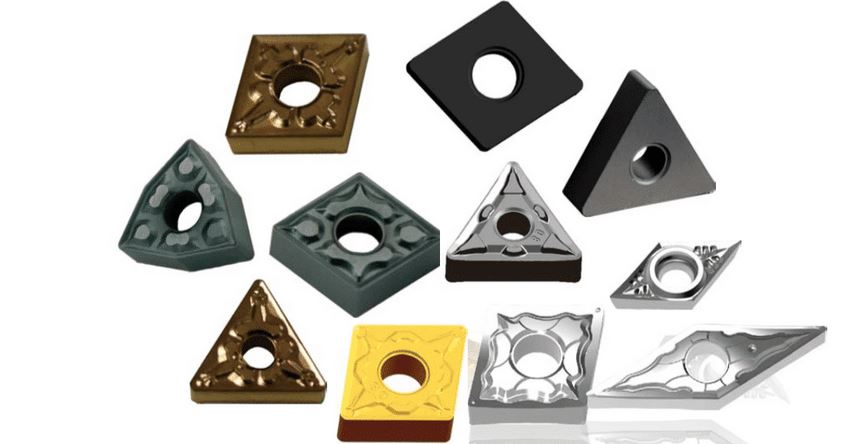
ЧАСТО ЗАДАВАЕМЫЕ ВОПРОСЫ
Вопрос | Ответить |
---|---|
Для чего используются твердосплавные вставки? | Твердосплавные пластины используются в механической обработке для резки, точения, фрезерования и сверления различных материалов. |
Как часто следует затачивать твердосплавные пластины? | Это зависит от области применения и материала, но, как правило, когда вы заметите снижение производительности. |
Могу ли я сам заточить твердосплавные пластины? | Да, при наличии необходимых инструментов и техники вы можете самостоятельно затачивать твердосплавные пластины. |
Каков наилучший метод заточки твердосплавных пластин? | Лучший метод зависит от типа вставки и области применения, но шлифование алмазным кругом - универсальный и эффективный вариант. |
Почему твердосплавные пластины нуждаются в заточке? | Заточка сохраняет эффективность резания, продлевает срок службы инструмента и обеспечивает высокое качество обработки. |
Заключение
Затачивание твердосплавных пластин является необходимым навыком для любого машиниста. Понимая различные типы вставок, их применение и лучшие методы заточки, вы сможете обеспечить остроту и эффективность ваших инструментов. Будь то заточка алмазными брусками или шлифовка кругами CBN, правильный подход позволит вашим пластинам работать наилучшим образом.