В быстро меняющемся мире современного производства, где точность и скорость имеют первостепенное значение, многофланцевые твёрдый сплав Торцевые фрезы стали незаменимыми инструментами для достижения исключительных результатов. Эти передовые инструменты с несколькими режущими кромками и прочной твердосплавной конструкцией обеспечивают непревзойденную скорость съема материала, превосходную чистоту поверхности и длительный срок службы инструмента. В этом подробном руководстве вы узнаете о тонкостях применения многозаходных твердосплавных концевых фрез, их конструкции, областях применения и преимуществах выбора надежного поставщика, такого как TRUER.
Что такое многолезвийные твердосплавные концевые фрезы?
Твердосплавные концевые фрезы с несколькими фрезами - это вращающиеся режущие инструменты, специально разработанные для высокоскоростной обработки. Они имеют несколько режущих кромок, или флейт, обычно от двух до восьми и более, расположенных по окружности режущего конца инструмента. Эти канавки в сочетании с исключительной твердостью и износостойкостью твердого сплава позволяют торцевым фрезам с несколькими канавками быстро и эффективно удалять материал, создавая точные и сложные формы в широком диапазоне материалов.
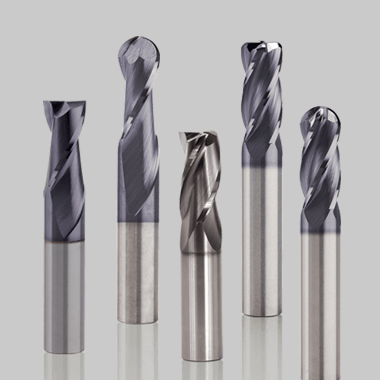
Анатомия высокопроизводительного инструмента: Дизайн и особенности
Многозаходные твердосплавные торцевые фрезы имеют несколько ключевых особенностей, которые способствуют их исключительной производительности:
- Номер флейты: Количество канавок существенно влияет на характеристики резания инструмента. Большее количество фрез, как правило, обеспечивает более высокую скорость съема материала и более гладкую поверхность, но может потребовать увеличения скорости вращения шпинделя и мощности.
- Угол спирали: Угол наклона спиралей по отношению к оси инструмента влияет на отвод стружки и силу резания. Большие углы спирали способствуют эффективному удалению стружки, а меньшие углы обеспечивают повышенную прочность режущей кромки.
- Геометрия флейты: Форма и конструкция фрез, включая угол наклона, угол зазора и стружколомающие элементы, оптимизированы для конкретных материалов и условий резания.
- Твердый сплав: Выбор подходящей марки твердого сплава, основанный на таких факторах, как твердость, прочность и износостойкость, имеет решающее значение для обеспечения оптимального срока службы и производительности инструмента.
- Покрытия: Современные покрытия, такие как TiN, TiAlN и DLC, могут еще больше повысить износостойкость, уменьшить трение и увеличить срок службы инструмента, особенно при высокотемпературной или абразивной обработке.
Классификация режущего мастерства: Типы многофланцевых торцевых фрез
Многогранные твердосплавные концевые фрезы выпускаются в различных конфигурациях для удовлетворения разнообразных требований к обработке:
Тип концевой мельницы | Характеристики | Приложения |
---|---|---|
Квадратные концевые фрезы | Плоский режущий конец, углы 90 градусов | Фрезерование общего назначения, пазование, прорезка карманов |
Торцевые фрезы с шаровым наконечником | Полусферический режущий конец | Контурное фрезерование, 3D-профилирование, гладкие поверхности |
Угловые радиусные торцевые фрезы | Скругленные углы с определенным радиусом | Обработка кромок, снятие фасок, обработка филе |
Торцевые фрезы для черновой обработки | Агрессивная геометрия флейты, большой зазор для стружки | Быстрый съем материала, черновая обработка |
Финишные концевые фрезы | Тонкая геометрия флейты, высокие углы спирали | Тонкая обработка, гладкая поверхность, точное контурирование |
Таблица 1: Типы многофланцевых торцевых фрез
Применение в различных отраслях промышленности: Где точность сочетается с универсальностью
Исключительная производительность и универсальность многозаходных твердосплавных торцевых фрез сделали их незаменимым инструментом в самых разных отраслях промышленности:
- Аэрокосмическая промышленность: Обработка сложных авиационных компонентов, деталей двигателей и элементов конструкций из высокопрочных сплавов.
- Автомобиль: Производство блоков цилиндров, головок блока цилиндров, компонентов трансмиссии и других важных автомобильных деталей.
- Медицинские приборы: Создание сложных имплантатов, хирургических инструментов и медицинского оборудования с высокой точностью и биосовместимостью.
- Изготовление пресс-форм: Производство пресс-форм и штампов для различных отраслей промышленности, включая литье пластмасс, резины и металла.
- Общее производство: Широкий спектр применения, включая создание прототипов, изготовление приспособлений и общие задачи обработки.
Взвешивание преимуществ и недостатков
Преимущества многолезвийных твердосплавных концевых фрез:
- Высокие скорости съема материала: Несколько режущих кромок обеспечивают быстрое и эффективное удаление материала.
- Улучшенная отделка поверхности: Большее количество рифлей позволяет получить более гладкую поверхность, что снижает или исключает необходимость во вторичной обработке.
- Увеличенный срок службы инструмента: Исключительная твердость и износостойкость карбида продлевают срок службы инструмента, сокращая время простоя и расходы на оснастку.
- Повышенная универсальность: Выпускаются в широком диапазоне размеров, геометрии и покрытий для решения различных задач обработки.
Ограничения:
- Более высокая первоначальная стоимость: По сравнению с концевыми фрезами из быстрорежущей стали, твердосплавные концевые фрезы обычно имеют более высокую начальную стоимость.
- Эвакуация чипов: Эффективное удаление стружки имеет решающее значение для предотвращения повторного срезания стружки и повреждения инструмента, что требует правильного применения СОЖ и соблюдения параметров обработки.
- Хрупкость: Твердость карбида делает его более хрупким, чем быстрорежущая сталь, что требует осторожного обращения и обработки для предотвращения поломки.
Таблица 3: Преимущества и ограничения многолезвийных твердосплавных концевых фрез
Преимущество TRUER: Почему выбирают нас?
- Непоколебимая приверженность качеству: Мы используем только самые высококачественные твёрдосплавные материалы и применяют строгие меры контроля качества на протяжении всего производственного процесса.
- Опыт применения: Наша команда опытных инженеров предоставляет квалифицированные рекомендации по выбору оптимальной торцевой фрезы для ваших конкретных задач обработки.
- Передовые технологии: Мы используем передовые технологии производства и методы прецизионной шлифовки для изготовления концевых фрез с исключительной точностью и производительностью.
- Решения, ориентированные на клиента: Мы стремимся понять ваши уникальные задачи и предложить индивидуальные решения, превосходящие ожидания.
Вопросы и ответы: Ответы на вопросы о многофланцевых торцевых фрезах
1. Как выбрать правильное количество флейт для моей задачи?
Оптимальное количество фрез зависит от таких факторов, как обрабатываемый материал, желаемая чистота поверхности и доступная мощность шпинделя. Большее количество фрез обычно обеспечивает более гладкую поверхность и более высокую скорость съема материала, но требует увеличения скорости и мощности шпинделя.
2. Какое значение имеет угол спирали на многофланцевой торцевой фрезе?
Угол спирали влияет на отвод стружки и силу резания. Большие углы спирали способствуют эффективному отводу стружки, а меньшие углы обеспечивают повышенную прочность режущей кромки.
3. Как предотвратить повторное срезание стружки при использовании многофрезерной торцевой фрезы?
Эффективный отвод стружки имеет решающее значение. Обеспечьте правильное применение СОЖ, используйте соответствующие параметры обработки и используйте концевые фрезы со стружколомом для облегчения удаления стружки.
4. Каковы признаки износа многофланцевой торцевой фрезы и когда ее следует заменить?
Признаками износа являются сколы или износ режущих кромок, увеличение силы резания, плохое качество поверхности, изменение звука или вибрации при обработке. Замените торцевую фрезу при появлении любого из этих признаков, чтобы предотвратить повреждение инструмента или дефекты заготовки.
5. Можете ли вы предоставить многозаходные торцевые фрезы на заказ для удовлетворения моих специфических требований к обработке?
Да, мы специализируемся на предоставлении решений по изготовлению инструмента на заказ. Свяжитесь с нами, сообщив свои конкретные требования, и наша команда инженеров будет работать в тесном сотрудничестве с вами, чтобы разработать и изготовить идеальную торцевую фрезу для вашего применения.