Понимание Твердосплавные инструменты
Твердосплавные инструменты изготавливаются из композитного материала, в котором частицы карбида вольфрама сочетаются с металлическим связующим, например кобальтом. Почему они являются фаворитами в отрасли? Вот почему:
- Износостойкость: Твердосплавные инструменты выдерживают абразивные нагрузки гораздо лучше, чем другие материалы, что делает их идеальными для резки, шлифовки и придания формы твердым материалам.
- Высокая прочность и жесткость: Они созданы для того, чтобы выдерживать большие нагрузки, не вытирая пота (и не ломаясь вообще).
- Термостойкость: Твердосплавные инструменты остаются холодными под давлением, сохраняя свою целостность даже при высоких температурах.
А теперь представьте, что у вас есть спортивный автомобиль с высокими техническими характеристиками. Разве вы не хотели бы поддерживать его в рабочем состоянии, чтобы пробег был максимальным? Тот же принцип применим и к твердосплавным инструментам. Правильное обслуживание гарантирует, что вы получите максимум от их невероятных возможностей.
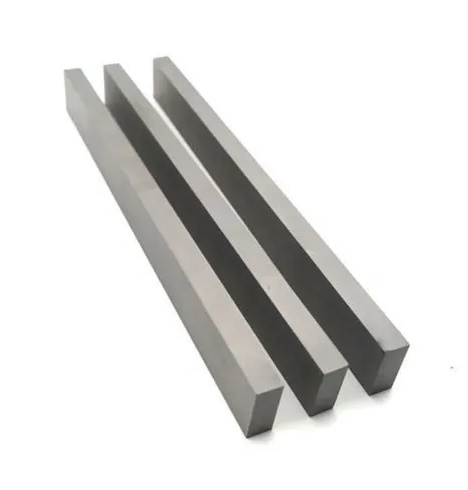
Основные советы по обслуживанию
Чтобы сохранить твёрдосплавные инструменты чтобы они работали как можно лучше, вот некоторые из них основные советы по обслуживанию вам следует:
Совет по обслуживанию | Описание |
---|---|
Регулярная уборка | Удаляйте мусор и налет после каждого использования, чтобы предотвратить коррозию и сохранить острые края. |
Осмотрите на предмет повреждений | Проверьте, нет ли сколов, трещин или износа до и после использования. Небольшие дефекты могут привести к большим проблемам. |
Используйте правильную смазку | Всегда используйте рекомендованные смазочные материалы для уменьшения трения и износа во время работы. |
Хранить в сухом месте | Влажность может привести к коррозии. Храните инструменты в контролируемой среде с низкой влажностью. |
Избегайте перегрева | Чрезмерный нагрев может разрушить структуру материала. При необходимости используйте системы охлаждения. |
Использование защитных покрытий | Рассмотрите инструменты с защитными покрытиями для повышения износостойкости и устойчивости к коррозии. |
Регулярно затачивайте лезвия | Тупые инструменты требуют больше усилий и снижают эффективность. Затачивайте их по мере необходимости, используя соответствующие инструменты. |
Подберите инструменты к материалам | Используйте подходящий твердосплавный инструмент для работы. Не допускайте несоответствия и не рискуйте повредить как инструмент, так и материал. |
Обращайтесь осторожно | Не роняйте инструменты и не подвергайте их излишним ударам, которые могут вызвать микротрещины. |
Следуйте рекомендациям производителя | Всегда соблюдайте рекомендации по уходу, предоставленные производителем. |
Общие ошибки, которых следует избегать
Даже самые лучшие инструменты могут выйти из строя, если за ними не ухаживать должным образом. Избегайте этих распространенных ошибок, чтобы продлить срок службы твердосплавных инструментов:
- Использование неправильного инструмента для работы: Вы когда-нибудь пробовали использовать отвертку в качестве стамески? Это рецепт катастрофы. То же самое относится и к твердосплавным инструментам. Используйте соответствующий тип для конкретного материала и задачи.
- Пренебрежение регулярными проверками: Небольшие трещины или сколы не кажутся большой проблемой, но они могут быстро перерасти в серьезный ущерб.
- Неправильная заточка: Использование неправильного шлифовального круга или техники может испортить режущую кромку инструмента.
- Не обращая внимания на смазку: Работа без надлежащей смазки приводит к чрезмерному нагреву и ускоряет износ.
- Плохая практика хранения: Если оставить инструменты во влажной или незащищенной среде, это приведет к появлению ржавчины и коррозии.
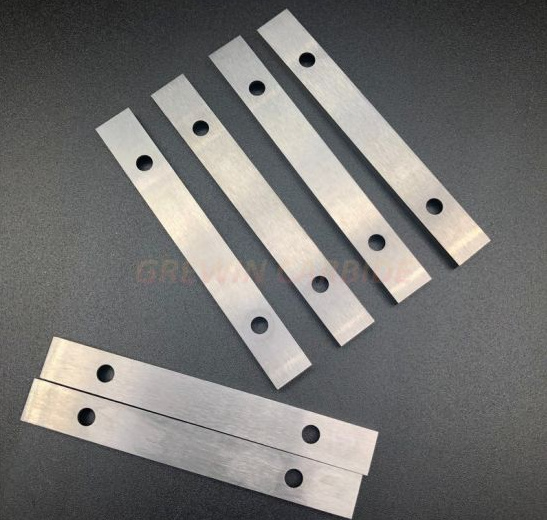
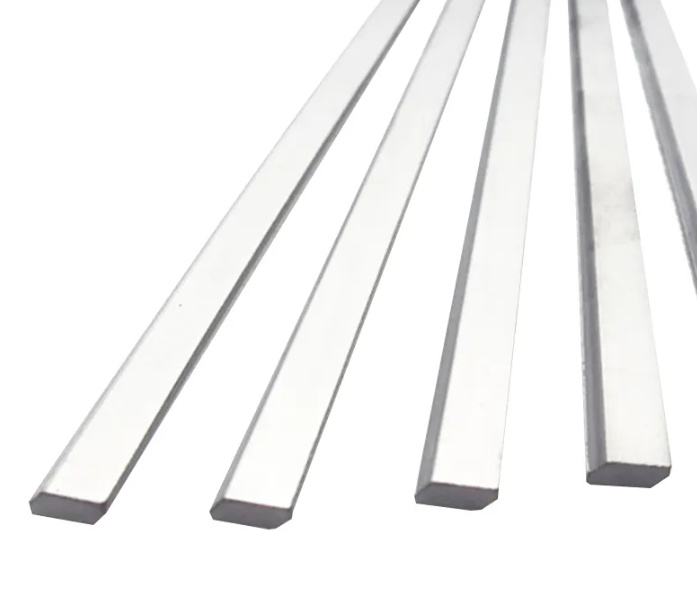
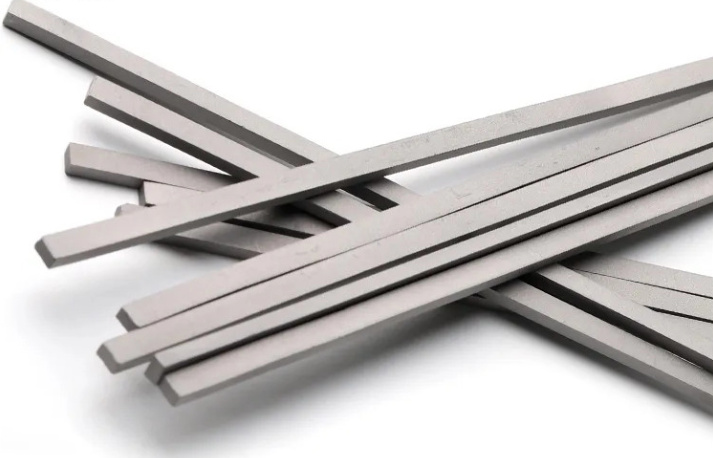
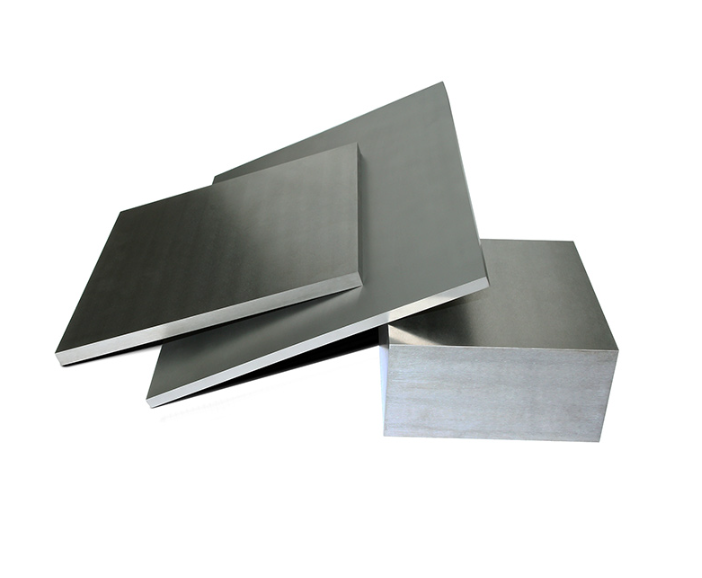
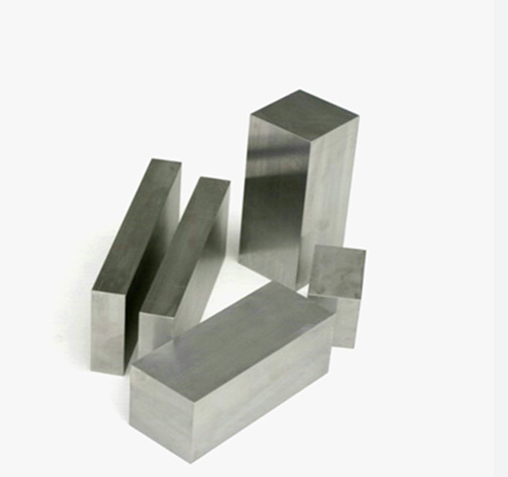

Рекомендуемые продукты и услуги
Когда речь идет о поддержании твёрдосплавные инструментыИнвестиции в правильные продукты могут иметь большое значение. Вот десять надежных моделей металлических порошков, которые стоит рассмотреть:
- Класс K10: Известна своей превосходной износостойкостью и прочностью, подходит для деревообрабатывающих инструментов.
- Класс P30: Идеально подходит для обработки стали с высокой ударопрочностью.
- Твердый сплав C2 Micrograin: Идеально подходит для работ, требующих острых краев и точности.
- Карбидный порошок C5: Отлично подходит для абразивных материалов и тяжелых работ.
- Вольфрамо-кобальтовый сплав: Обеспечивает исключительную прочность при выполнении работ с высокой нагрузкой.
- H10F: Превосходно подходит для высокоскоростной обработки с термической стабильностью.
- Композит WC-Co: Универсальная и долговечная марка общего назначения.
- ZK30UF: Ультрамелкое зерно для получения превосходной поверхности при высокоточной обработке.
- VK10: Сочетает в себе износостойкость и прочность для резки закаленных материалов.
- Класс S10: Предназначен для цветных материалов, таких как алюминий и пластик.
У каждой модели есть свои достоинства, поэтому обязательно подбирайте порошок в соответствии с вашими потребностями.
Предлагаемые методы и инструменты для шлифования
Шлифование твердосплавных инструментов - это и искусство, и наука. Использование правильного метода и оборудования обеспечивает точность и долговечность.
Метод измельчения | Описание |
---|---|
Алмазные шлифовальные круги | Высокоэффективны для обработки твердосплавных инструментов с минимальным износом. |
Кубический нитрид бора (CBN) | Идеально подходит для применений, требующих меньшего нагрева и высокой прочности. |
Мокрое измельчение | Уменьшает выделение тепла, предотвращая термическое повреждение инструментов. |
Колеса с мелкой зернистостью | Обеспечивает более гладкую поверхность и острые режущие кромки. |
Автоматические шлифовальные станки | Обеспечивает стабильные результаты при минимальных затратах ручного труда. |
Ручные шлифовальные машины | Пригодится для заточки в дороге, но для точности требует навыков. |
Алмазные диски с гальваническим покрытием | Идеально подходит для сложных форм и небольших инструментов. |
Многоосевые шлифовальные станки с ЧПУ | Высокоточное шлифование для сложных геометрических форм. |
Когда заменять или ремонтировать Твердосплавные инструменты
Как понять, когда нужно выкинуть полотенце и заменить твердосплавный инструмент? Все дело в балансе. Вот некоторые признаки, на которые следует обратить внимание:
- Чрезмерный износ: Если заточка не восстанавливает работоспособность, значит, пришло время для замены.
- Частые сколы или трещины: Постоянные повреждения могут указывать на то, что инструмент уже отслужил свой срок.
- Плохая производительность: Если качество обработки падает или инструменты требуют больше усилий, замена может быть более экономичной.
- Несовместимость материалов: Переход на более твердые или прочные материалы может потребовать модернизации инструмента.
В случае сомнений проконсультируйтесь со специалистом или ознакомьтесь с рекомендациями производителя.
Вопросы и ответы
Вопрос | Ответить |
---|---|
Как лучше всего чистить инструменты из твердого сплава? | Используйте мягкую щетку или ультразвуковой очиститель с мягким моющим средством, чтобы удалить мусор, не повредив поверхность. |
Можно ли самому затачивать твердосплавные инструменты? | Да, но для этого требуется соответствующее оборудование, например, алмазные шлифовальные круги, и твердая рука для точности. |
Как часто следует проверять инструменты? | Проводите быстрый осмотр перед и после каждого использования. Планируйте тщательный осмотр еженедельно или ежемесячно. |
Каков срок службы инструментов из твердого сплава? | При правильном уходе инструменты из твердого сплава могут прослужить в 10-20 раз дольше, чем стальные, в зависимости от условий эксплуатации. |
Стоит ли использовать инструменты из твердого сплава с покрытием? | Конечно! Такие покрытия, как TiN или AlTiN, повышают износостойкость и термостойкость. |
Как предотвратить сколы? | Обращайтесь с инструментами осторожно, не прилагайте чрезмерных усилий и следите за правильным выравниванием во время обработки. |
Все ли инструменты из твердого сплава требуют смазки? | Большинство так и делают. Правильная смазка минимизирует нагрев и уменьшает износ. Всегда проверяйте рекомендации производителя. |