Почему "Разрезание Твердосплавный стержень Сложно?
Резать твердосплавные стержни - все равно что пытаться прорезать алмаз ножом для масла: да, это так сложно. Карбид, особенно карбид вольфрама, невероятно твердый и хрупкий. Он создан для того, чтобы выдерживать интенсивный износ, что делает его рок-звездой в промышленности.
Основная проблема заключается в том, что карбид плохо сочетается с традиционными режущими инструментами. Стандартные инструменты часто быстро изнашиваются или не выдерживают высокого давления и тепла, возникающих в процессе резки. Поэтому выбор правильного метода и оборудования - это не просто совет, а необходимость.
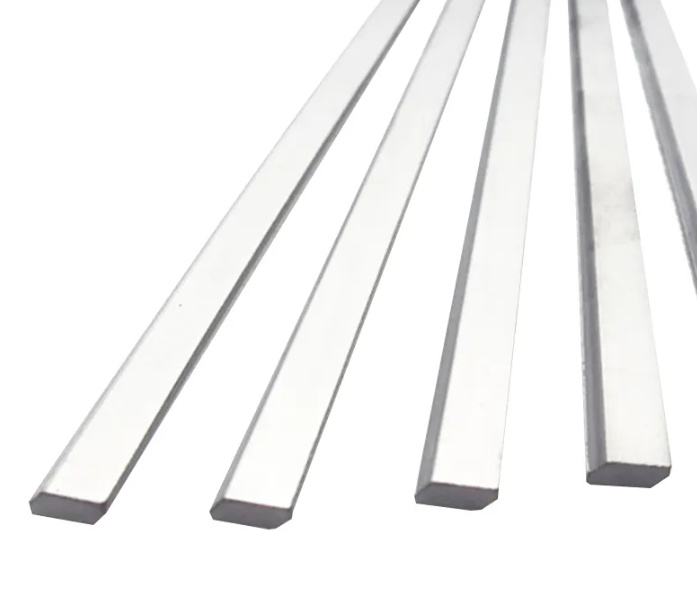
Свойства Твердосплавные стержни
Прежде чем перейти к технике нарезки, давайте поговорим о химии и физике. Твердосплавные стержни обычно изготавливаются из карбида вольфрама (WC), смешанного со связующим веществом, таким как кобальт (Co). Эта смесь придает им уникальное сочетание чрезвычайной твердости, высокой температуры плавления, устойчивости к истиранию и деформации.
Вот несколько объектов, которые выделяются на фоне других:
- Твердость: Около 1600-2200 HV (твердость по Виккерсу)
- Прочность на сжатие: До 7000 МПа
- Теплопроводность: 70-100 Вт/м-К
- Модуль упругости: 530-700 ГПа
- Вязкость разрушения: Относительно низкие (4-15 МПа-м½), поэтому легко растрескиваются
Эти свойства фантастически важны для работы инструмента, но являются головной болью при обработке. Твердость может погубить инструмент, в то время как хрупкость требует легкого прикосновения и лазерной точности.
Распространенные методы резки твердосплавных стержней
Давайте поговорим о тактике. Резка твердого сплава - это не универсальная операция. Существует множество способов, и каждый из них имеет свои плюсы и минусы в зависимости от того, чего вы хотите добиться.
1. EDM (электроэрозионная обработка)
- Лучшее для: Сложные разрезы и жесткие допуски
- Плюсы: Отсутствие механических напряжений, отличная обработка поверхности
- Cons: Медленный процесс, высокая стоимость
2. Шлифование алмазным кругом
- Лучшее для: Крупносерийное производство
- Плюсы: Высокоточная, долговечная оснастка
- Cons: Дорогостоящее оборудование, высокая стоимость обслуживания
3. Лазерная резка
- Лучшее для: Сложные геометрии и микрорезы
- Плюсы: Бесконтактный, сверхточный
- Cons: Риск термического повреждения, дорогостоящая настройка
4. Гидроабразивная резка
- Лучшее для: Термочувствительные материалы
- Плюсы: Отсутствие теплового эффекта, экологичность
- Cons: Более низкая точность, более грубая отделка
5. Пиление алмазными дисками
- Лучшее для: Прямые срезы на коротких стержнях
- Плюсы: Экономичность, простота настройки
- Cons: Ограничивается менее сложными дизайнами
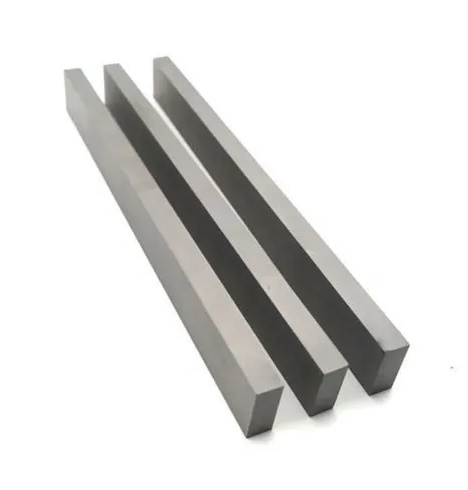
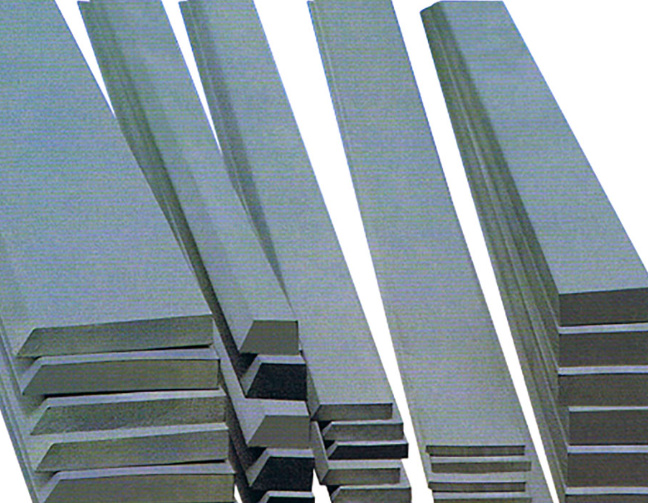
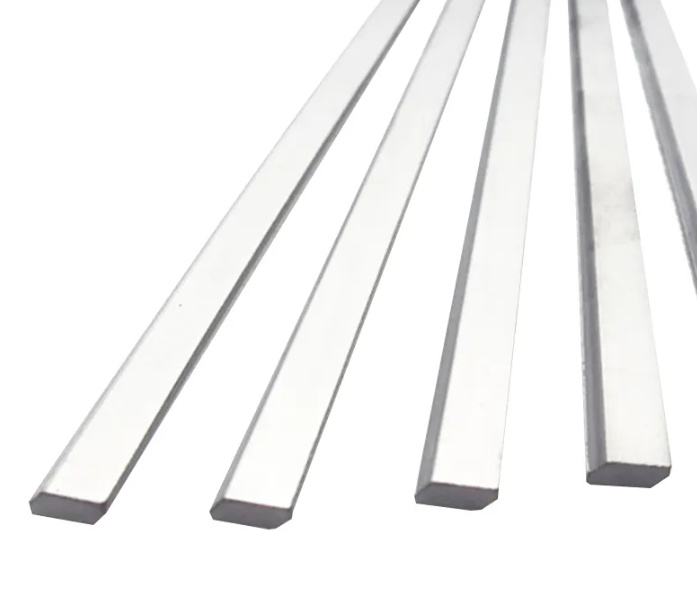
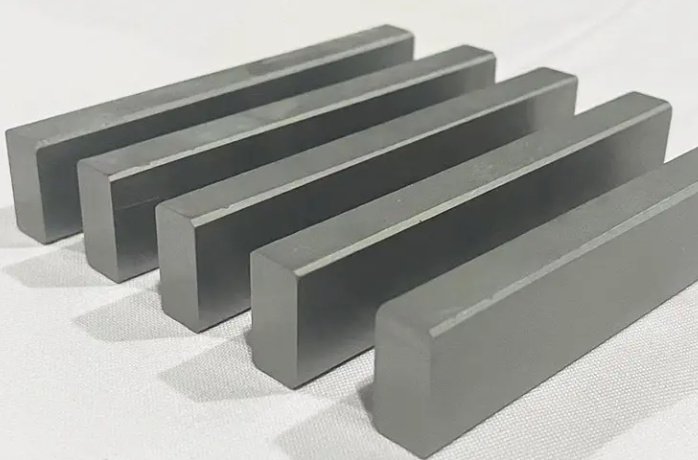
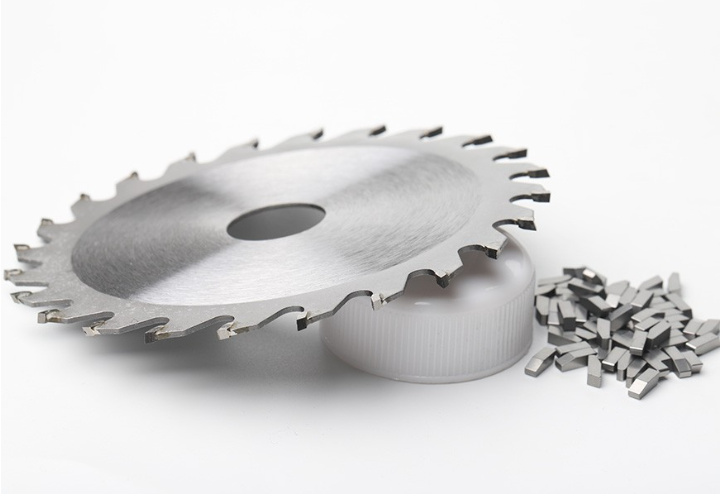
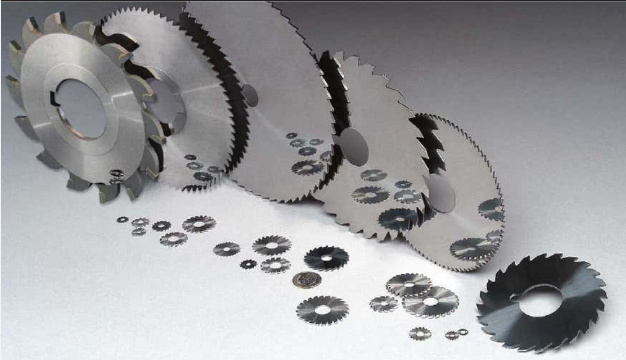
Лучшие практики для резки Твердосплавные стержни
Метод резки | Лучший пример использования | Прецизионный уровень | Срок службы инструмента | Скорость | Отделка поверхности |
---|---|---|---|---|---|
EDM | Сложные формы, жесткие допуски | Очень высокий | Длинный (зависит от электрода) | Медленный | Отличный |
Шлифование алмазным кругом | Крупносерийное производство | Высокая | Длинный | Быстрый | Отличный |
Лазерная резка | Тонкие стержни, сложные узоры | Очень высокий | Средний | Средний | Хороший |
Гидроабразивная резка | Термочувствительные приложения | Средний | Длинный | Средний | Ярмарка |
Пиление алмазными дисками | Быстрые прямые резы, короткие стержни | Средний | Средний | Быстрый | Хороший |
Рекомендуемое оборудование и инструменты
Вы же не принесете ложку на бой на мечах, верно? То же самое относится и к резке твердого сплава. Вам нужно правильное снаряжение:
- Прецизионные алмазные отрезные станки - Обеспечивает низкую вибрацию и высокую точность резки.
- Проволочно-вырезные станки - Идеально подходит для сложных работ с высокими допусками.
- Лазерные резаки с системами охлаждения - Сдерживает тепловую деформацию.
- Гидроабразивные фрезы с абразивами - Отлично подходит для выполнения задач, чувствительных к температуре.
- Высококачественные алмазные лезвия - Необходим для обеспечения долговечности и целостности поверхности.
Такие бренды, как AccuteX, Обработка GF, и Содик производят системы EDM мирового класса, в то время как TRUMPF и Амада доминирует в технологиях лазерной резки.
Как избежать поломки кромки при резке твердосплавных стержней
Думайте о карбиде как о стекле - он не гнется, а ломается. Поэтому, если вы торопите процесс или оказываете неравномерное давление, защелкаИ вот он, ваш первозданный край.
Чтобы все было гладко:
- Используйте острые инструменты с алмазным покрытием для уменьшения вибрации.
- Прочно закрепите стержень но без применения чрезмерной силы.
- Используйте охлаждающие жидкости чтобы свести к минимуму накопление тепла.
- Резать постепенно а не за один агрессивный проход.
Терпение - ваш лучший друг. Все дело в утонченности, а не в грубой силе.
Как разрезать тонкие стержни без деформации при резке твердосплавных стержней
Резать тонкие твердосплавные стержни - все равно что пытаться расщепить зубочистку самурайским мечом. супер легко испортить.
Вот как не сбиться с пути:
- Полностью поддерживайте стержень по всей длине для предотвращения изгиба.
- Используйте алмазные круги с мелкой зернистостью для аккуратных и точных разрезов.
- Идите медленно и уверенно с подачей и избегайте бокового давления.
- Рассмотрите возможность использования лазера или электроэрозионной обработки если вам нужна сверхточная точность.
Конкретные модели металлических порошков для Твердосплавные стержни (С описанием)
Модель порошка | Состав | Размер зерна | Приложения | Сильные стороны |
---|---|---|---|---|
WC-Co APT 88/12 | 88% WC, 12% Co | 0,8 мкм | Сверла, развертки | Высокая износостойкость |
WC-Co H10F | 90% WC, 10% Co | 0,6 мкм | Режущие инструменты | Высокая твердость |
WC-Co K20 | 93% WC, 7% Co | 1,0 мкм | Горные инструменты | Прочность + износостойкость |
WC-Co K30 | 94% WC, 6% Co | 1,2 мкм | Концевые фрезы | Превосходное сохранение кромки |
WC-Co H13A | 87% WC, 13% Co | 1,6 мкм | Инструменты для тяжелых условий эксплуатации | Устойчивость к ударам |
WC-Ni | 85% WC, 15% Ni | 1,0 мкм | Коррозионные среды | Коррозионная стойкость |
WC-Co Ultra Fine | 92% WC, 8% Co | 0,4 мкм | Прецизионные детали | Наибольшая твердость |
WC-TiC-Co | WC + TiC + Co | 1,2 мкм | Аэрокосмические детали | Термическая стабильность |
WC-Co C2 | 94% WC, 6% Co | 1,1 мкм | Инструменты для штамповки | Качество обработки поверхности |
WC-Co C10 | 90% WC, 10% Co | 0,7 мкм | Микроинструменты | Резкость по краям |
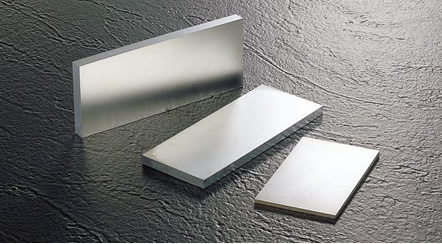
ЧАСТО ЗАДАВАЕМЫЕ ВОПРОСЫ
Вопрос | Ответить |
---|---|
Как лучше всего резать твердосплавные стержни в домашних условиях? | Используйте алмазный пильный диск и работайте медленно. Не допускайте перегрева и всегда надевайте защиту. |
Можно ли резать твердосплавные стержни лазером без образования трещин? | Да, но только в системах высокого класса, которые хорошо контролируют нагрев. В противном случае существует риск образования трещин. |
Почему твердосплавные стержни скалываются по краям? | Обычно это происходит из-за неправильного зажима, неравномерного давления или тупого инструмента. |
Эффективна ли гидроабразивная резка для твердосплавных стержней? | Это работает, особенно если вы хотите избежать нагрева. Только не ожидайте супергладкого покрытия. |
Какой металлический порошок лучше всего подходит для прецизионных твердосплавных инструментов? | WC-Co Ultra Fine за превосходную твердость и мелкую зернистость. |
Какие средства защиты необходимы при резке твердого сплава? | Защита глаз, перчатки и системы пылеудаления, чтобы избежать вдыхания мелких частиц. |
Можно ли использовать EDM для всех твердосплавных стержней? | В основном, да. Только убедитесь, что стержень не слишком токопроводящий, если используете определенные связующие. |
Нужна ли охлаждающая жидкость при резке твердого сплава? | Да! Охлаждающая жидкость снижает нагрев и значительно продлевает срок службы инструмента. |
Как долго служат алмазные лезвия при резке твердого сплава? | Зависит от качества и условий использования, но обычно в 10-20 раз дольше, чем стандартные лезвия. |
Существуют ли портативные инструменты для резки твердого сплава? | Для специализированного использования предлагаются компактные алмазные пилы и мини-электроэрозионные станки. |