Важность Твердосплавные пластины в сложных приложениях
Начнем с простой истины: когда речь идет о самых жестких и требовательных условиях эксплуатации в таких отраслях, как аэрокосмическая, автомобильная, нефтегазовая и горнодобывающая, твёрдосплавные пластины являются бесспорными чемпионами. Думайте о них как о бронированных рыцарях мира материалов - прочных, твердых и почти неразрушимых.
Почему они так важны? Потому что эти тарелки, особенно те, что сделаны из карбид вольфрамаОни способны выдерживать интенсивный износ, давление и температуру. Будь то резка высокопрочных сплавов или защита поверхностей в условиях сильных ударов, твердосплавные пластины гарантируют, что инструменты и компоненты прослужат дольше, будут работать интенсивнее и лучше.
И это не просто маркетинговый ход. Согласно отчету компании Global Market Insights, в рынок карбида вольфрама Только к 2030 году ожидается, что объем продаж превысит $27 миллиардов. Очевидно, что речь идет о материалах, которые имеют огромное значение в реальных приложениях.
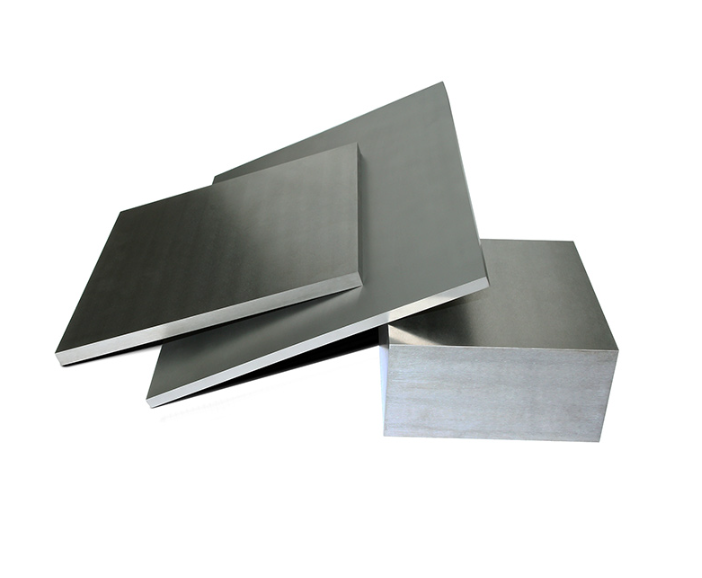
Что такое Твердосплавная пластина?
Итак, что именно это твердосплавная пластина?
В двух словах, твердосплавная пластина - это композитный материал, изготовленный путем связывание карбидов металлов (обычно карбида вольфрама) с металлическим связующим веществомобычно кобальт или никель. Полученный материал обладает уникальным сочетанием твердость (до 9 по шкале Мооса!), износостойкость и прочность.
Давайте разберемся в этом:
- Карбид вольфрама: Сверхтвердый керамический состав.
- Кобальт/никелевое связующее: Держит все вместе, как клей, и придает прочность.
- Производственный процесс: Обычно включает в себя порошковую металлургию и спекание.
Вы получаете материал, который тверже стали, почти такой же прочный, как алмазы, и создан для работы в самых суровых промышленных условиях. Они используются в режущие инструменты, быстроизнашивающиеся детали, штампы, пуансоны и защитные экраны.
Трудности при склеивании твердосплавных пластин
Вот тут-то и возникают сложности. Какими бы замечательными ни были твердосплавные пластины, связывание их с другими материалами - это не просто прогулка по парку.
Почему? Из-за них:
- Высокая твердость: Они нелегко деформируются, что означает, что клеи или металлы "сцепляются" с ними с трудом.
- Несоответствие теплового расширения: Они расширяются и сжимаются с разной скоростью по сравнению со сталью или алюминием.
- Хрупкость: Несмотря на свою твердость, они могут растрескаться под нагрузкой, если не приклеены должным образом.
На самом деле, многие производители в конечном итоге имеют дело с расслоение, растрескивание под напряжением или снижение эксплуатационных характеристик из-за некачественных методов склеивания.
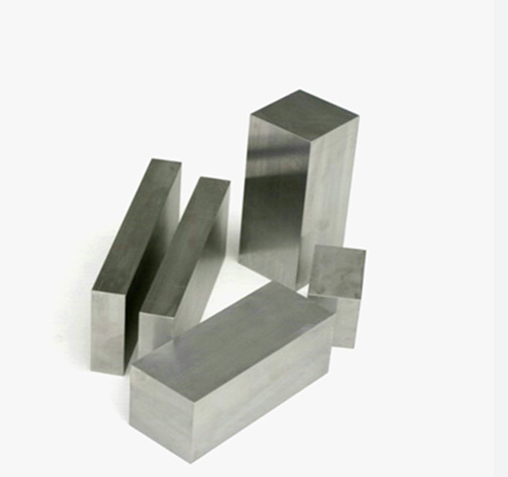
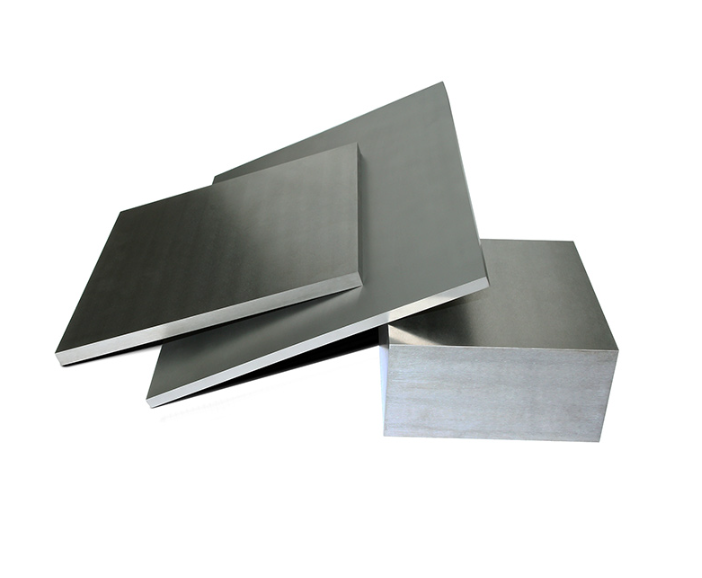

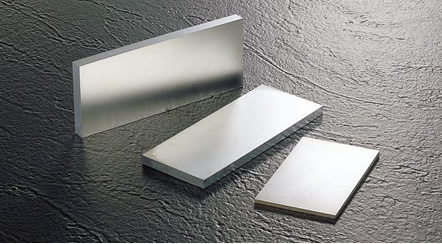
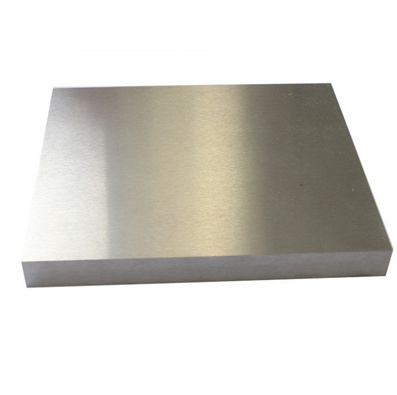
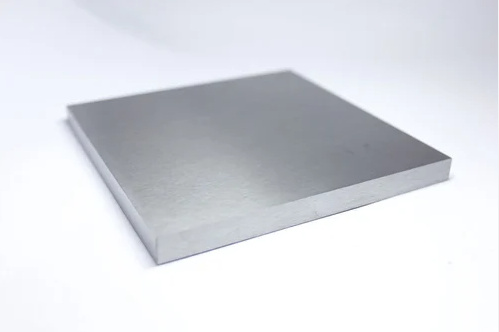
Эффективные техники скрепления для Твердосплавные пластины
Ниже приведена подробная таблица наиболее эффективных методов склеивания твердосплавных пластин, в которой сравниваются различные параметры для быстрого понимания.
Обзор методов склеивания твердосплавных пластин
Техника склеивания | Прочность сцепления | Термическое сопротивление | Стоимость | Общее использование | Преимущества | Недостатки |
---|---|---|---|---|---|---|
Пайка | Высокая | Умеренный | Умеренный | Режущие инструменты | Прочные суставы | Требует высоких температур |
Диффузионное связывание | Очень высокий | Высокая | Высокая | Аэрокосмическая промышленность | Не требуется шпатлевка | Затраты времени |
Клеевое соединение | Средний | От низкого до умеренного | Низкий | Прототипирование | Простой процесс | Более слабые облигации |
Механическое крепление | От низкого до среднего | Высокая | Низкий | Временные исправления | Реверсивный | Менее прочный |
Лазерная сварка | Очень высокий | Очень высокий | Очень высокий | Прецизионные инструменты | Точность и чистота | Дорогая установка |
Агломерация | Высокая | Высокая | Умеренный | Инструментальные вставки | Однородная связь | Требуются специальные инструменты |
Лучшие практики для сложных применений с использованием твердосплавных пластин
Итак, у вас есть твердосплавная пластина. Вы знаете, что она прочная, и хотите, чтобы она прослужила долго. Как сделать так, чтобы она выполняла свою работу правильно?
Вот некоторые проверенные в боях передовые методы:
- Подготовка поверхности - это все: Перед склеиванием очищайте, пескоструйно обрабатывайте или травите поверхности. Даже микроскопические загрязнения могут испортить соединение.
- Выберите подходящего агента по облигациям: Для работы в высокотемпературных средах используйте пайку или лазерную сварку. Для создания прототипов отлично подойдут клеи.
- Помните о тепловом расширении: Используйте эластичные клеи или слои для снятия напряжения для предотвращения растрескивания.
- Дизайн для облигаций: Если вы знаете, что будете приклеивать пластину, спроектируйте корпус или опорную конструкцию таким образом, чтобы равномерно распределять нагрузку.
- Тестировать, тестировать и еще раз тестировать: Перед запуском в производство проведите испытания на термоциклирование, вибрацию и стресс.
Модели металлических порошков для склеивания (10 лучших с описанием)
Давайте разберемся с техникой. Вот десять специальные модели металлических порошков обычно используется при склеивании твёрдосплавные пластиныОсобенно при пайке и диффузионном соединении.
Модель металлического порошка | Основной металл | Пример использования | Температура плавления (приблизительно) | Основные характеристики |
---|---|---|---|---|
BNi-2 | Никель | Пайка | 960°C | Коррозионная стойкость, хорошая текучесть |
BAg-7 | Серебро | Пайка | 780°C | Низкотемпературное соединение, хорошая пластичность |
Cusil | Медь/серебро | Пайка | 780°C | Высокая прочность, теплопроводность |
Амдри 105 | Никель | Диффузия | >1000°C | Устойчивость к окислению |
Metco 443 | Кобальт | Пайка | 1050°C | Жесткость и термостойкость |
AMDRY 962 | На основе никеля | Пайка | 1080°C | Самотечная, вакуумная среда |
Никробраз 30 | Никель | Пайка | 1050°C | Идеально подходит для соединения твердого сплава со сталью |
Oerlikon S-F 001 | Серебро/медь | Пайка | 790°C | Хорошая смачиваемость, тонкий поток |
Brazetec 4906 | Серебро | Пайка | 700°C | Низкое плавление, легкое нанесение |
Колмоной 88 | Никель-хром | Наплавка | 1100°C | Износостойкие накладки |
Тематические исследования и применение в реальном мире (факультативно)
Представьте, что вы производите буровые долота для нефтяных вышек. Одна компания протестировала паяные по сравнению со спекаемыми вольфрам твёрдосплавные пластины в смоделированных условиях. Угадайте, что? Агломерационные блоки прослужили 25% длиннее и показал 30% меньше микротрещин.
Другой производитель аэрокосмических деталей перешел от традиционной пайки к лазерная сваркаснижая количество отказов на 40% благодаря более точному управлению и меньшим тепловым искажениям. Реальные результаты, реальная экономия.
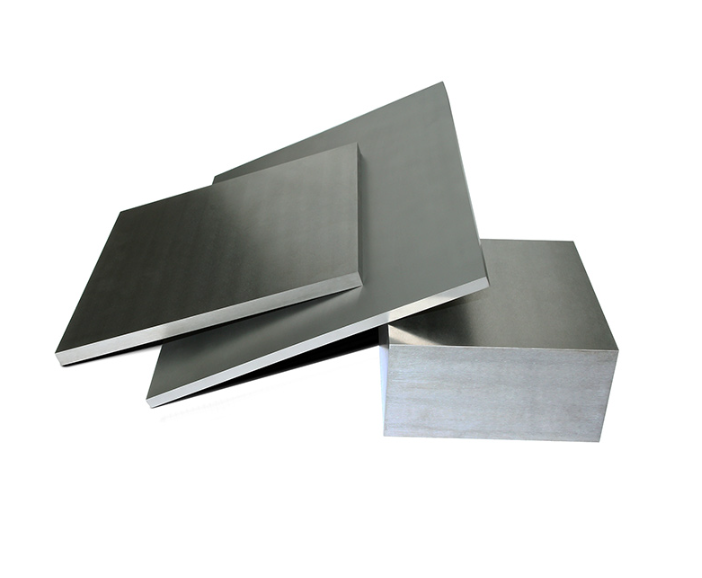
ЧАСТО ЗАДАВАЕМЫЕ ВОПРОСЫ
Вопрос | Ответить |
---|---|
Какой самый надежный метод склеивания твердосплавных пластин? | Диффузионное склеивание или лазерная сварка благодаря адгезии на атомном уровне. |
Можно ли использовать клей или эпоксидную смолу для склеивания твердосплавных пластин? | Да, для применения при низких нагрузках и температурах, например, при создании прототипов. |
Какой метод наиболее экономичен? | Пайка - прочный вариант среднего класса. |
Нужна ли специальная обработка поверхности твердосплавных пластин перед склеиванием? | Безусловно. Пескоструйная обработка или химическое травление помогают повысить прочность соединения. |
Как предотвратить растрескивание после склеивания? | Используйте слои для снятия напряжения или эластичные клеящие вещества. |
Можно ли приклеить карбид к алюминию или титану? | Да, но используйте соответствующие прослойки или выбирайте совместимые клеи. |
Что произойдет, если метод склеивания окажется неудачным? | Компонент может расслаиваться, трескаться или полностью выйти из строя в процессе эксплуатации. |
Существуют ли экологически безопасные методы склеивания? | Клеи и лазерная сварка дают меньше отходов по сравнению с пайкой с использованием флюса. |
В каких отраслях промышленности больше всего используется соединение твердосплавных пластин? | Аэрокосмическая, автомобильная, горнодобывающая, нефтегазовая и оборонная промышленность. |
Каков типичный срок службы компонентов из твердого сплава? | Зависит от области применения, но часто в 5-10 раз дольше, чем детали из нетвердого сплава. |