Обзор
Твердый сплав Торцевые фрезы, предназначенные для обработки цветных металлов, отличаются высокой эффективностью и точностью. Эти передовые инструменты разработаны с учетом уникальных свойств цветных материалов, таких как алюминий, медь, латунь и титан, обеспечивая высокое качество обработки и увеличенный срок службы инструмента. В этом блоге мы рассмотрим особенности твердосплавных концевых фрез для цветных металлов, включая их определение, принципы работы, применение, производственные процессы, классификацию, тенденции рынка, области применения и многое другое. Кроме того, мы воспользуемся таблицей для сравнения различных типов и выделим преимущества и недостатки этих инструментов.
Подробное введение
Что такое твердосплавная концевая фреза для цветных металлов?
Твердосплавная торцевая фреза по цветным металлам - это режущий инструмент из карбида вольфрама, специально разработанный для обработки цветных материалов. Цветные металлы, не содержащие железа, обладают уникальными свойствами, которые требуют специализированных инструментов для эффективной и точной резки. Эти торцевые фрезы разработаны для обеспечения исключительной производительности, уменьшения износа инструмента и повышения качества готовой продукции.
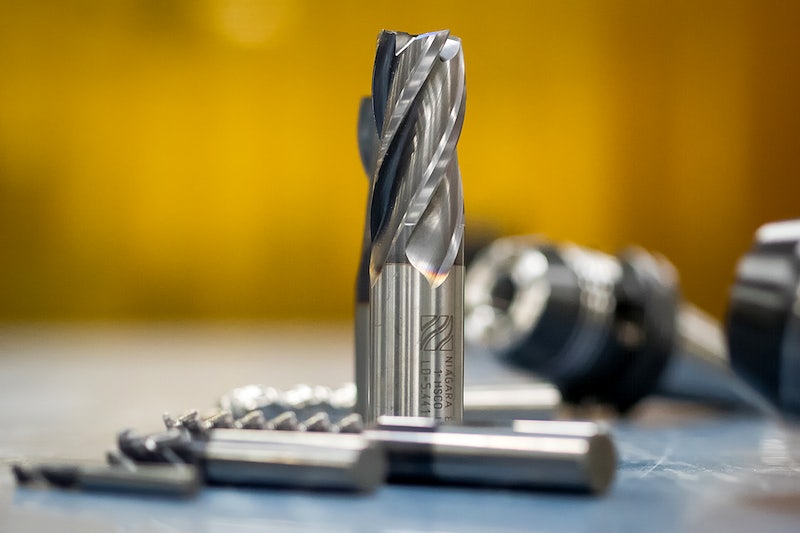
Как работает твердосплавная концевая фреза для цветных металлов?
Работа твердосплавной торцевой фрезы по цветным металлам основана на ее режущих кромках и свойствах твердого сплава. Карбид вольфрама обладает невероятной твердостью и износостойкостью, что позволяет торцевым фрезам сохранять остроту режущих кромок даже при высоких температурах и длительном использовании. Конструкция торцевой фрезы, включая количество канавок и угол наклона спирали, оптимизирована для эффективного отвода стружки и минимального отклонения инструмента, что обеспечивает плавные и точные резы.
Как использовать твердосплавную концевую фрезу для обработки цветных металлов
Использование твердосплавной торцевой фрезы для обработки цветных металлов включает в себя следующие шаги:
- Настройка машины: Убедитесь, что фрезерный станок правильно откалиброван, а заготовка надежно зажата.
- Выбор инструмента: Выберите подходящую твердосплавную концевую фрезу в зависимости от конкретного материала цветного металла и желаемой чистоты обработки.
- Скорость и подача: Установите правильную скорость вращения шпинделя и скорость подачи в соответствии с обрабатываемым материалом.
- Использование охлаждающей жидкости: Нанесите охлаждающую жидкость, чтобы уменьшить накопление тепла и продлить срок службы инструмента.
- Мониторинг: Постоянный мониторинг процесса фрезерования для корректировки параметров по мере необходимости и обеспечения оптимальной производительности.
Как производятся твердосплавные концевые фрезы для цветных металлов?
Процесс изготовления твердосплавных концевых фрез для цветных металлов включает в себя несколько точных этапов:
- Подготовка порошка: Порошок карбида вольфрама смешивается со связующим веществом, обычно кобальтом.
- Компактирование: Порошковая смесь прессуется в нужную форму с помощью пресс-формы.
- Агломерация: Спрессованная форма нагревается в печи для спекания, частицы скрепляются между собой и образуют цельную заготовку твердосплавного концевого сверла.
- Шлифование флейты: Флейты затачиваются в заготовке с помощью специализированных шлифовальных кругов.
- Покрытие: Для повышения производительности на торцевую фрезу может быть нанесено покрытие из таких материалов, как нитрид титана (TiN) или алмазоподобный углерод (DLC).
- Контроль качества: Каждая торцевая фреза проходит тщательное тестирование на соответствие требуемым характеристикам.
Классификация твердосплавных концевых фрез для цветных металлов
Твердосплавные концевые фрезы для цветных металлов можно классифицировать по различным критериям:
- Количество флейт: Обычно от 2 до 4, оптимизированных для удаления стружки.
- Покрытие: Варианты: без покрытия, с TiN-покрытием, с DLC-покрытием и т.д.
- Геометрия торца: Плоский конец, шаровой конец, угловой радиусный конец и т.д.
- Угол спирали: Угол наклона флейты относительно оси концевой фрезы, обычно от 30° до 45°.
- Приложение: Общепромышленная, чистовая, черновая, высокоскоростная обработка и т.д.
Тенденции рынка
Рынок твердосплавных концевых фрез для цветных металлов расширяется, что обусловлено развитием производственных технологий и растущим спросом на высокоточную обработку. Основные тенденции включают:
- Все более широкое применение в аэрокосмической и автомобильной промышленности: Спрос на высокопроизводительные материалы требует применения современных режущих инструментов.
- Технологические инновации: Разработка новых покрытий и геометрии для повышения производительности.
- Усилия по обеспечению устойчивости: Фокус на экологически чистых производственных процессах и переработке твердосплавных материалов.
Подробная информация о продукте
Ниже приведена таблица с основной информацией о твердосплавных концевых фрезах для цветных металлов, включая их типы, компоненты, свойства, характеристики, спецификации, размеры, марки и стандарты.
Тип | Компонент | Свойства | Характеристики | Технические характеристики | Размеры | Классы | Стандарты |
---|---|---|---|---|---|---|---|
Стандартный твердый сплав | WC-Co | Высокая твердость, износостойкость | Многочисленные флейты, гладкие срезы | Разное | 1 мм-20 мм диаметр | ISO K10-K30 | ISO, ANSI |
Твердый сплав с покрытием TiN | WC-Co + TiN | Повышенная износостойкость, низкое трение | Покрытие TiN, высокоскоростная обработка | Настраиваемый | Различные длины и диаметры | ISO K15-K40 | ISO, ANSI |
Твердый сплав с покрытием DLC | WC-Co + DLC | Превосходная термостойкость, долговечность | DLC-покрытие, высокотемпературные применения | Настраиваемый | Разное | ISO K20-K35 | ISO, ANSI |
Твердый сплав с шариковым наконечником | WC-Co | Высокая точность, гладкая отделка | Геометрия с шаровым наконечником, несколько флейт | Настраиваемый | 1 мм-20 мм диаметр | ISO K25-K40 | ISO, ANSI |
Применение твердосплавных концевых фрез для обработки цветных металлов
Твердосплавные концевые фрезы для цветных металлов - это универсальные инструменты, используемые в различных отраслях промышленности и сферах применения. Вот некоторые ключевые области применения:
- Аэрокосмическая промышленность: Прецизионное фрезерование сложных деталей, обработка алюминиевых сплавов и титана.
- Автомобильная промышленность: Производство деталей двигателя, компонентов трансмиссии и легких деталей шасси.
- Медицинская промышленность: Обработка хирургических инструментов, стоматологических компонентов и имплантатов из цветных металлов.
- Производство инструментов и штампов: Создание пресс-форм, штампов и прецизионных инструментов.
- Электронная промышленность: Фрезерование печатных плат, алюминиевых и медных корпусов и разъемов.
- Общее производство: Высокоскоростная обработка различных цветных материалов, включая алюминий, латунь и медь.
Преимущества и недостатки твердосплавных концевых фрез для цветных металлов
Ниже приведена таблица с описанием плюсов и минусов твердосплавных концевых фрез для обработки цветных металлов:
Аспект | Преимущества | Недостатки |
---|---|---|
Долговечность | Высокая износостойкость, долгий срок службы | Более высокая первоначальная стоимость по сравнению со стандартными концевыми фрезами |
Производительность | Превосходная эффективность резки, точность | Требуется умелое обращение и точная настройка |
Персонализация | Подстраивается под конкретные потребности, доступны различные геометрические формы | Более длительное время выполнения индивидуальных заказов |
Свойства материала | Исключительная твердость, термическая стабильность | Ограниченная гибкость в некоторых областях применения |
Похожие темы
Инновации в технологии торцевых мельниц
Последние достижения в области технологии торцевых фрез включают разработку гибридных торцевых фрез, сочетающих в себе преимущества нескольких материалов и покрытий. Эти инновации направлены на дальнейшее повышение производительности резания, срока службы инструмента и универсальности в различных областях обработки.
Устойчивое развитие производства концевых мельниц
Промышленность по производству концевых фрез уделяет все больше внимания вопросам экологичности. Усилия включают переработку твердосплавных материалов, снижение энергопотребления и разработку экологичных покрытий. Такие методы не только приносят пользу окружающей среде, но и повышают общую эффективность производственного процесса.
Будущие тенденции в производстве фрезерных инструментов
Будущее фрезерных инструментов, в том числе твердосплавных концевых фрез для цветных металлов, выглядит многообещающим благодаря постоянным исследованиям новых материалов и технологий производства. Ожидается, что такие тенденции, как аддитивное производство, интеграция "умных" материалов и использование искусственного интеллекта при проектировании и оптимизации инструментов, будут способствовать развитию отрасли.
ЧАСТО ЗАДАВАЕМЫЕ ВОПРОСЫ
Вопрос 1: Какие факторы следует учитывать при выборе твердосплавной торцевой фрезы для цветных металлов?
A1: При выборе твердосплавной концевой фрезы для цветных металлов учитывайте особенности обрабатываемого материала, желаемую чистоту поверхности, количество канавок, покрытие и геометрию торца. Кроме того, убедитесь, что инструмент совместим с вашим фрезерным станком и конкретными требованиями к применению.
Вопрос 2: Как количество канавок влияет на производительность концевой фрезы из твердого сплава для цветных металлов?
A2: Количество канавок влияет на производительность резания и скорость съема материала. Меньшее количество канавок обеспечивает лучший отвод стружки, что важно для цветных металлов, которые склонны к образованию длинной стружки. Однако большее количество канавок обеспечивает более гладкое резание и лучшую чистовую обработку. Выбор зависит от конкретного материала и операции фрезерования.
Вопрос 3: Можно ли использовать твердосплавные концевые фрезы для цветных металлов для высокоскоростной обработки?
A3: Да, твердосплавные концевые фрезы для цветных металлов хорошо подходят для высокоскоростной обработки благодаря своей высокой твердости, износостойкости и термостойкости. Покрытия, такие как TiN и DLC, еще больше повышают их производительность при высокоскоростной и высокотемпературной обработке, что делает их идеальным решением для сложных задач.
Вопрос 4: Какие методы технического обслуживания рекомендуются для твердосплавных концевых фрез для цветных металлов?
A4: Правильное обслуживание твердосплавных концевых фрез включает регулярный осмотр на предмет износа и повреждений, очистку для удаления мусора и налета, заточку при необходимости и хранение в сухом прохладном месте. Использование соответствующих смазочно-охлаждающих жидкостей и обеспечение правильных параметров обработки также помогают продлить срок службы инструмента.
Q5: Как определить подходящее покрытие для моей твердосплавной концевой фрезы для цветных металлов?
A5: Выбор подходящего покрытия зависит от обрабатываемого цветного материала и конкретных требований к применению. Покрытия TiN подходят для обработки общего назначения, в то время как покрытия DLC обеспечивают превосходную тепло- и износостойкость для высокоскоростных и высокотемпературных применений. Консультация с поставщиком поможет вам выбрать оптимальное покрытие для оптимизации производительности и срока службы инструмента.
Хотите купить Твердосплавная торцевая фреза по хорошей цене? Пожалуйста, нажмите здесь.