3 мощных метода: как металлообработка формирует будущее твердосплавных кнопок
Карбид вольфрама кнопкиИзвестные своей исключительной твердостью и износостойкостью, они являются незаменимыми компонентами в различных отраслях промышленности - от горнодобывающей и строительной до нефте- и газодобычи. Но знаете ли вы, что процесс производства, в частности используемый метод ковки, может существенно повлиять на конечные свойства и характеристики этих важнейших компонентов? В этом подробном руководстве рассматриваются тонкости трех известных методов ковки - горячая ковка, холодная ковка и штамповка -раскрывает, как каждый метод формирует микроструктуру, прочность и общее качество кнопок из карбида вольфрама.
За пределами твердости: Почему ковка имеет значение для производства твердосплавных кнопок
Наука формообразования: Понимание воздействия ковки
- Уточнение микроструктуры: Процессы ковки, включающие контролируемую пластическую деформацию, улучшают зернистую структуру карбида вольфрама, повышая его прочность, вязкость и износостойкость.
- Контроль плотности и пористости: Ковка помогает устранить внутренние пустоты и пористость, в результате чего получаются более плотные и прочные твердосплавные кнопки, способные выдерживать экстремальные условия эксплуатации.
- Сложность и точность формы: Различные технологии ковки обеспечивают разную степень гибкости в достижении сложных форм и точных размеров, удовлетворяя конкретные требования к применению.
Вникая в детали: Горячая ковка, холодная ковка и свинчивание - объяснение
Тепло, давление и точность: Подробный обзор каждого метода
1. Горячая штамповка:
- Процесс: Нагрев заготовки из карбида вольфрама до высокой температуры (обычно выше температуры рекристаллизации) перед формованием с помощью сжимающих усилий в штампе.
- Преимущества:
- Требуется меньшее усилие ковки из-за снижения прочности материала при высоких температурах.
- Повышенная пластичность, позволяющая изменять форму и создавать сложные геометрические формы.
- Улучшенная текучесть и однородность зерен, повышающая механические свойства.
- Ограничения:
- Возможность окисления или обезуглероживания при высоких температурах, что требует контролируемой атмосферы или защитных покрытий.
- Более высокий расход энергии по сравнению с холодной ковкой.
- Может потребоваться дополнительная обработка для достижения окончательных допусков.
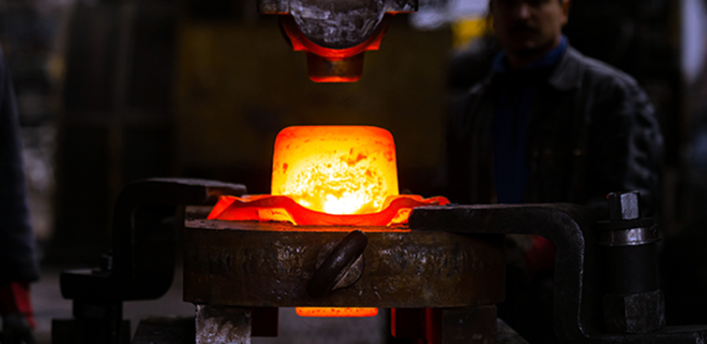
2. Холодная ковка:
- Процесс: Выполняется при комнатной или слегка повышенной температуре, с использованием высоких сжимающих усилий для придания формы преформе из карбида вольфрама в штампе.
- Преимущества:
- Повышенная прочность и твердость за счет упрочнения в процессе деформации.
- Отличная обработка поверхности и точность размеров, что часто снижает или исключает необходимость вторичной обработки.
- Более низкое потребление энергии по сравнению с горячей ковкой.
- Ограничения:
- Требуется большее усилие ковки из-за повышенной прочности материала при более низких температурах.
- Ограниченная формуемость, ограничивающая сложность достижимых форм.
- Может потребоваться отжиг для снятия внутренних напряжений, возникающих при холодной обработке.
3. Скручивание:
- Процесс: Специализированный процесс ковки, при котором стержень или труба из карбида вольфрама радиально сжимается и уменьшается в диаметре с помощью набора вращающихся штампов.
- Преимущества:
- Высокая производительность и эффективность, особенно для цилиндрических и симметричных форм.
- Отличная обработка поверхности и контроль размеров.
- Можно использовать для создания вытянутых форм с большим отношением длины к диаметру.
- Ограничения:
- Ограниченная гибкость формы, в основном подходит для деталей цилиндрической или близкой к сетке формы.
- Для сложных геометрических форм могут потребоваться дополнительные этапы обработки.
- Разработка и настройка инструмента может быть более сложной по сравнению с ковкой в открытом штампе.
Сравнение характеристик: Как методы ковки влияют на свойства твердосплавных баттонов
От структуры зерна до качества поверхности: Ключевые факторы дифференциации
Характеристика | Кнопки горячей штамповки | Кнопки холодной ковки | Закрепленные кнопки |
---|---|---|---|
Зерновая структура | Мелкие, однородные зерна благодаря рекристаллизации | Деформированные, удлиненные зерна в результате холодной обработки | Утонченная зерновая структура с направленным выравниванием |
Твердость (HV30) | 1400 – 1800 | 1600 – 2000 | 1500 – 1900 |
Прочность | Высокая прочность и ударопрочность | Очень высокая прочность и износостойкость | Отличное сочетание прочности и пластичности |
Отделка поверхности | Хорошо, но может потребоваться дополнительная обработка | Отличная обработка поверхности и точность размеров | Очень хорошая обработка поверхности с минимальными дефектами |
Сложность формы | Достигается высокая степень сложности формы | Ограничивается простыми формами | Преимущественно подходит для цилиндрических или близких к сетке деталей |
Стоимость | Умеренный | Высокая | От низкого до умеренного |
Применение в разных отраслях: В чем преимущества каждого типа кнопок
От бурения до износа деталей: Разнообразные варианты использования
- Горнодобывающая промышленность и строительство: Горячекованые твердосплавные кнопки широко используются в буровых коронках, режущих резцах и других инструментах, подвергающихся высокому ударному и абразивному износу.
- Разведка нефти и газа: Твердосплавные кнопки, изготовленные методом холодной ковки, предпочтительны для скважинных буровых инструментов, где первостепенное значение имеют высокая твердость и износостойкость.
- Металлообработка и механическая обработка: Твердосплавные кнопки Swaged находят применение в износостойких деталях, режущих пластинах и инструментальных компонентах, требующих высокой точности размеров и гладких поверхностей.
TRUER: ваш партнер в области точной ковки
Удовлетворение потребностей промышленности: Сравнительный анализ
Поставщик | Страна | Диапазон цен (за штуку) | Специальности |
---|---|---|---|
TRUER | Китай | $10 – $50+ | Индивидуальные решения для ковки, передовой опыт в области материалов, возможности быстрого создания прототипов |
Элемент шесть | ВЕЛИКОБРИТАНИЯ | $15 – $60+ | Высокопроизводительные марки твердого сплава, специализированные технологии ковки для сложных условий эксплуатации |
Kennametal | США | $12 – $55+ | Широкий ассортимент стандартных и нестандартных кованых кнопок, большой опыт работы в отрасли |
Sandvik Coromant | Швеция | $14 – $70+ | Инновационные процессы ковки, ориентация на устойчивое развитие и оптимизацию производительности |
Примечание: Цены являются приблизительными и могут значительно отличаться в зависимости от размера пуговицы, геометрии, сорта, количества и других факторов.
Взвешивая плюсы и минусы: сравнительный анализ методов ковки
Принятие обоснованных решений: Преимущества и ограничения
Метод ковки | Преимущества | Ограничения |
---|---|---|
Горячая штамповка | - Более низкие усилия при ковке<br> - Повышенная пластичность<br> - Улучшенный поток зерна | - Потенциал к окислению<br> - Повышенное энергопотребление<br> - Может потребоваться вторичная обработка |
Холодная ковка | - Повышенная прочность и твердость<br> - Отличная обработка поверхности<br> - Низкое потребление энергии | - Повышенное усилие ковки<br> - Ограниченная формуемость<br> - Может потребоваться отжиг |
Свертывание | - Высокие производственные показатели<br> - Отличный контроль размеров<br> - Подходит для продолговатых форм | - Ограниченная гибкость формы<br> - Может потребоваться вторичная обработка<br> - Сложная оснастка |
За пределами основ: Факторы, влияющие на результаты ковки
Оптимизация производительности кнопок: Основные соображения
- Свойства материала: Состав, размер зерна и исходные свойства порошка карбида вольфрама влияют на его кузнечную способность и конечные характеристики пуговицы.
- Параметры ковки: Температура, давление, скорость деформации и конструкция штампа играют важнейшую роль в определении микроструктуры, плотности и общего качества кованых пуговиц.
- Термообработка: Послештамповочная термическая обработка, например отжиг или снятие напряжения, может еще больше изменить механические свойства и стабильность размеров твердосплавных кнопок.
Часто задаваемые вопросы: Ответы на ваши вопросы о ковке
1. Как выбрать наиболее подходящий метод ковки для конкретного применения кнопки из карбида вольфрама?
Оптимальный метод ковки зависит от таких факторов, как желаемая форма кнопки, требуемые механические свойства, объем производства и стоимость. Наши технические специалисты могут предоставить индивидуальные рекомендации, исходя из ваших конкретных потребностей.
2. Какие основные меры контроля качества применяются в процессе ковки для обеспечения постоянного качества пуговиц?
На протяжении всего процесса ковки применяются строгие меры контроля качества, включая проверку сырья, мониторинг параметров ковки в процессе производства, проверку размеров, испытания на твердость и микроструктурный анализ.
3. Может ли компания TRUER предоставить кованые кнопки из карбида вольфрама со специальной обработкой поверхности или покрытием?
Да, мы предлагаем ряд видов обработки поверхности, таких как полировка, шлифовка и нанесение покрытий, чтобы еще больше повысить производительность и долговечность наших кованых кнопок в сложных условиях эксплуатации.
4. Каково типичное время выполнения заказа на заказ кованых кнопок из карбида вольфрама от TRUER?
Сроки выполнения индивидуальных заказов зависят от таких факторов, как сложность конструкции, используемый метод ковки, требуемое количество и текущие производственные мощности. Свяжитесь с нашим отделом продаж для получения индивидуального предложения и оценки времени выполнения заказа. Для получения дополнительной информации, пожалуйста, нажмите здесь.
5. Предлагает ли компания TRUER техническую поддержку или консультационные услуги, связанные с разработкой и оптимизацией кованых кнопок из карбида вольфрама?
Да, наша команда опытных инженеров предоставляет всестороннюю техническую поддержку, включая рекомендации по выбору материалов, оптимизацию конструкции, помощь в создании прототипов и устранении неполадок, чтобы обеспечить ваш успех.