Обзор Твердосплавные кнопки
Carbide buttons, often referred to as cemented carbide buttons, are vital components used across various industries, particularly in mining, drilling, and cutting tools. These components are renowned for their incredible hardness, wear resistance, and ability to withstand high pressure, making them indispensable in challenging environments. But what exactly are carbide buttons, and why are they so critical in these applications?
Imagine you’re trying to cut through a piece of tough material like rock or steel. Regular tools just wouldn’t make the cut—literally. This is where carbide buttons come into play. They’re the heroes of the tough tasks, performing well where others would fail. In this article, we’ll explore everything you need to know about carbide buttons, from their types and applications to how you can select the right one for your specific needs. Let’s dive in!
What is a Carbide Button?
Carbide buttons are small, button-shaped components made from cemented carbide—a composite material composed of hard carbide particles bonded together by a metallic binder. Tungsten carbide (WC) is the most common type, known for its exceptional hardness and durability.
Why Are Carbide Buttons So Tough?
To put it simply, carbide buttons are as tough as nails—well, tougher actually. Tungsten carbide, the primary material used in these buttons, is nearly as hard as diamond. This means carbide buttons can cut through almost anything. But why is this toughness so important? In industries like mining or oil drilling, tools face extreme conditions—think high pressure, abrasion, and heat. Carbide buttons are built to withstand these conditions without breaking a sweat, making them invaluable for heavy-duty tasks.
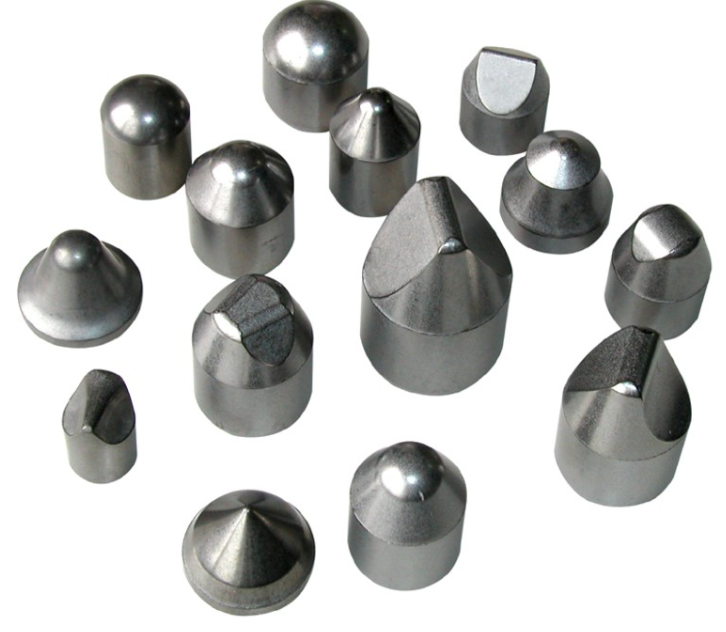
Типы твердосплавных кнопок
Carbide buttons come in various shapes, sizes, and compositions, each designed to suit different applications. Whether you’re drilling into soft rock or cutting through hard metal, there’s a carbide button tailored for the job. Here, we’ll break down the most common types.
Common Types of Carbide Buttons
Тип | Описание |
---|---|
Spherical Carbide Buttons | Spherical buttons are used for extremely hard formations. They offer excellent wear resistance and are designed to minimize the risk of breakage during drilling. |
Conical Carbide Buttons | Ideal for medium to hard formations, conical buttons provide a balance between penetration rate and durability. |
Flat Top Carbide Buttons | These are used in softer formations where high penetration rates are required. They wear faster than spherical buttons but are more cost-effective. |
Parabolic Carbide Buttons | Designed for both soft and hard formations, parabolic buttons offer a versatile solution, balancing wear resistance with cutting efficiency. |
Chisel Carbide Buttons | Chisel buttons are best for directional drilling and softer formations. They allow for precise control and high penetration rates. |
Hemispherical Carbide Buttons | These buttons are designed for tough drilling conditions and are ideal for hard, abrasive formations. |
Trapezoidal Carbide Buttons | Trapezoidal buttons provide a combination of wear resistance and impact toughness, suitable for hard formations. |
Pyramid Carbide Buttons | Best for breaking up extremely hard surfaces, pyramid buttons offer superior impact resistance. |
Bullet-Shaped Carbide Buttons | Bullet-shaped buttons are used for deep drilling in hard formations, offering excellent wear resistance and durability. |
Domed Carbide Buttons | These buttons are ideal for general-purpose drilling, offering a balance between toughness and wear resistance. |
As you can see, the shape and design of a carbide button play a crucial role in its performance. The right choice can mean the difference between a successful operation and a costly failure.
Applications of Carbide Buttons
Carbide buttons are the workhorses of numerous industries, employed in tasks that require extreme toughness and precision. Let’s explore the main applications where these mighty little components shine.
Common Applications of Carbide Buttons
Приложение | Промышленность | Функция |
---|---|---|
Rock Drilling | Добыча | Carbide buttons are used in drill bits for rock drilling, providing durability and wear resistance. |
Бурение нефтяных и газовых скважин | Нефть и газ | In oil and gas drilling, carbide buttons help drill through tough rock formations. |
Металлорежущий инструмент | Производство | Used in cutting tools, carbide buttons offer precision and longevity in metalworking. |
Road Construction | Строительство | In road construction, carbide buttons are used in the cutting tools for asphalt and concrete. |
Snow Plows | Municipal Maintenance | Carbide buttons are embedded in snow plow blades to enhance wear resistance when clearing roads. |
Деревообработка | Carpentry | Used in cutting tools, carbide buttons provide sharp edges that last longer than steel alternatives. |
Forestry Equipment | Лесное хозяйство | Carbide buttons are used in cutting tools for forestry to ensure durability and sharpness. |
Сельскохозяйственная техника | Сельское хозяйство | In agricultural machinery, carbide buttons are used in tillage equipment for better soil penetration. |
Wear Parts in Heavy Machinery | Тяжелое оборудование | Carbide buttons enhance the wear resistance of components in heavy machinery. |
Defense Applications | Оборона | Used in armor-piercing ammunition, carbide buttons provide penetration and durability. |
From drilling to cutting, the versatility of carbide buttons makes them an indispensable part of many industries. Their ability to maintain performance under extreme conditions is unmatched by other materials.
Свойства материалов Твердосплавные кнопки
Carbide buttons are not just hard—they possess a unique combination of properties that make them suitable for tough applications. Let’s break down what makes these components stand out.
Основные свойства материала
Недвижимость | Описание |
---|---|
Твердость | Carbide buttons are extremely hard, usually between 85-95 HRA, making them ideal for cutting, drilling, and wear-resistant applications. |
Жесткость | Despite their hardness, carbide buttons are tough, able to withstand high impact forces without shattering. |
Износостойкость | They exhibit excellent wear resistance, extending the life of tools and reducing downtime. |
Прочность на сжатие | Carbide buttons can withstand extremely high compressive forces, crucial for drilling and cutting in tough materials. |
Термическая стабильность | Carbide buttons maintain their properties at high temperatures, which is essential in applications involving intense heat, such as metal cutting or rock drilling. |
Коррозионная стойкость | They resist corrosion better than many other metals, increasing their longevity in harsh environments. |
Хрупкость | While carbide buttons are tough, they can be brittle under certain conditions, such as when subjected to tensile stress. |
These properties make carbide buttons incredibly reliable for demanding applications. However, understanding these properties is key to selecting the right carbide button for your specific needs.
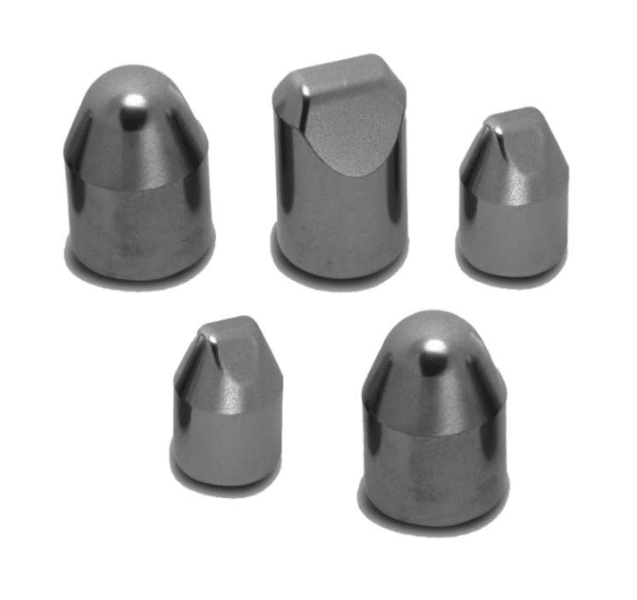
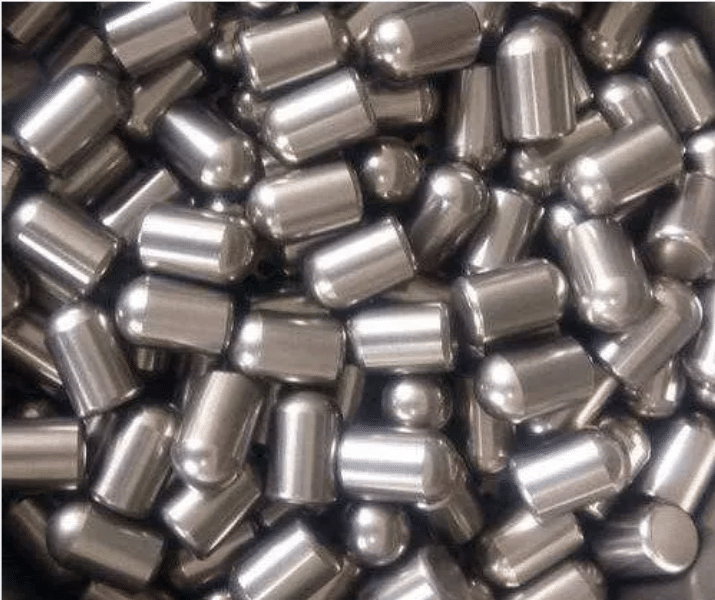
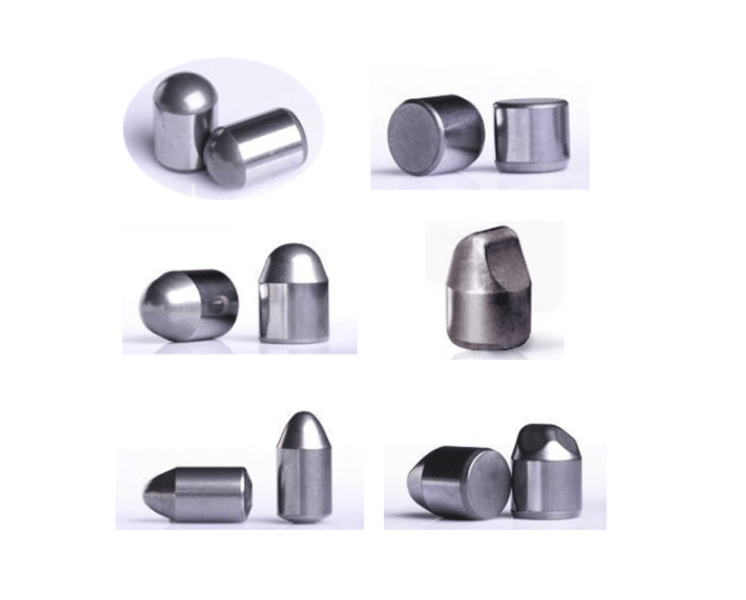
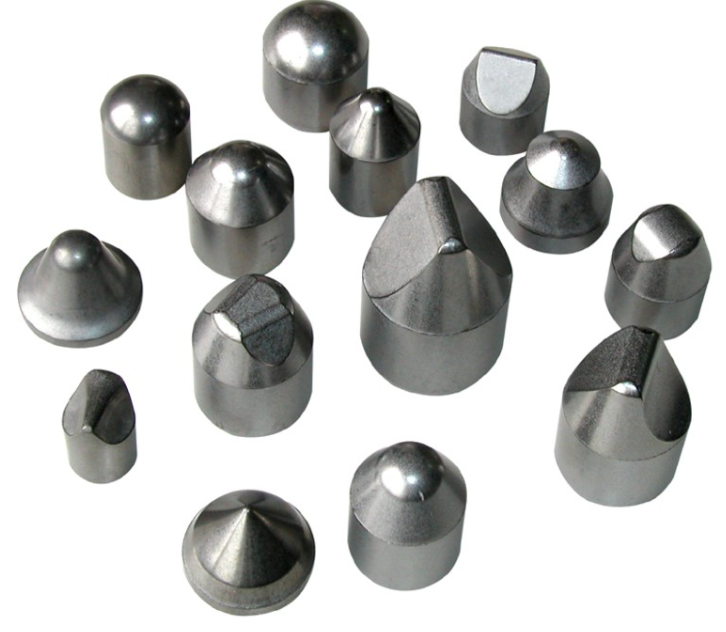
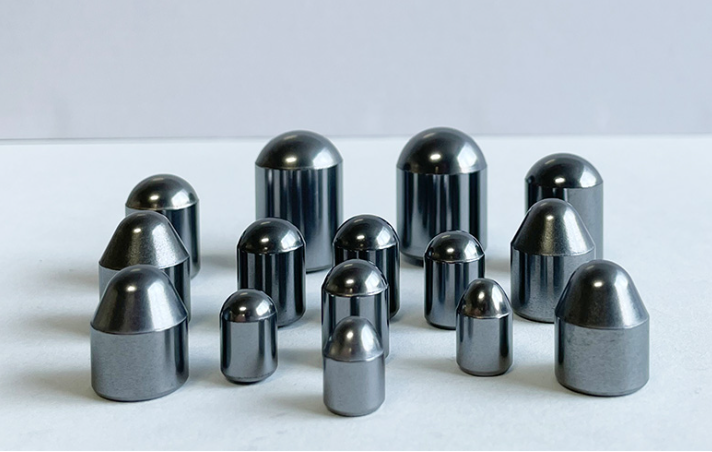
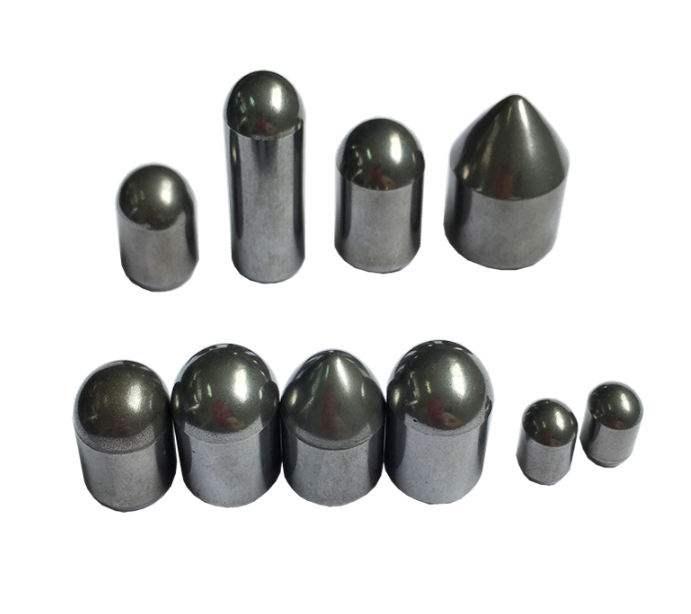
Composition of Carbide Buttons
The composition of carbide buttons is what gives them their exceptional properties. Typically, these components are made of tungsten carbide particles bonded with a metallic binder, such as cobalt or nickel.
Typical Composition of Carbide Buttons
Компонент | Роль |
---|---|
Карбид вольфрама (WC) | The primary component providing hardness and wear resistance. |
Кобальт (Co) | Acts as a binder, holding the tungsten carbide particles together and providing toughness. |
Никель (Ni) | An alternative binder used when corrosion resistance is needed. |
Carbide Powders | May include other carbides like titanium carbide (TiC) or tantalum carbide (TaC) to modify properties like toughness or wear resistance. |
Добавки | Small amounts of other elements may be added to improve specific properties, such as grain growth inhibitors or corrosion-resistant elements. |
By tweaking the composition, manufacturers can tailor the properties of carbide buttons to meet the needs of different applications. This customization is crucial in industries where precision and performance are critical.
Hardness, Strength, and Wear Resistance of Carbide Buttons
The combination of hardness, strength, and wear resistance makes carbide buttons a favorite in industries that demand durability and reliability. Let’s delve into these aspects.
Понимание твердости, прочности и износостойкости
Характеристика | Описание |
---|---|
Твердость | Measured on the Rockwell scale, hardness indicates the material’s resistance to deformation. Carbide buttons typically range between 85-95 HRA, ensuring high durability. |
Прочность | Carbide buttons possess high compressive strength, which is crucial for drilling and cutting in tough materials. |
Износостойкость | Their ability to resist wear and tear ensures long service life, reducing the frequency of replacements and downtime. |
These characteristics make carbide buttons a top choice for heavy-duty applications. However, selecting the right balance of these properties is key to optimizing performance in your specific application.
Specifications, Sizes, Shapes, and Standards for Твердосплавные кнопки
Carbide buttons come in a variety of sizes, shapes, and specifications to meet the diverse needs of different industries. Standardization ensures compatibility and performance.
Common Specifications, Sizes, and Shapes
Спецификация | Подробности |
---|---|
Размеры | Carbide buttons range in size depending on the application, from a few millimeters in diameter for small cutting tools to several centimeters for industrial drill bits. |
Формы | Common shapes include spherical, conical, flat-top, parabolic, chisel, hemispherical, trapezoidal, pyramid, bullet-shaped, and domed. |
Стандарты | International standards such as ISO and ANSI ensure consistency in quality and performance across different manufacturers. |
Допуски | Precision is key, with tight tolerances often required, particularly in high-stakes industries like aerospace or automotive manufacturing. |
Choosing the right size, shape, and specification is essential for ensuring optimal performance and longevity in your specific application.
Selecting the Right Carbide Button
Choosing the right carbide button isn’t just about picking the hardest or most wear-resistant option—it’s about matching the button’s properties to your application’s specific needs.
Factors to Consider When Selecting a Carbide Button
Фактор | Описание |
---|---|
Приложение | Consider the specific application—whether it’s drilling, cutting, or wear protection—as different applications require different properties. |
Material to be Worked | The hardness and abrasiveness of the material you’re working on will determine the appropriate carbide button. |
Условия эксплуатации | Temperature, pressure, and environmental conditions should influence your choice. |
Стоимость в сравнении с производительностью | While carbide buttons can be more expensive than other materials, their longevity and performance often justify the cost in demanding applications. |
Репутация производителя | Consider the reputation of the manufacturer, as quality can vary significantly between different suppliers. |
Making the right choice can lead to improved performance, reduced costs, and longer tool life.
Comparing Carbide Buttons: Advantages and Limitations
While carbide buttons offer numerous advantages, they also have some limitations. Understanding these can help you make an informed decision.
Преимущества и ограничения
Аспект | Преимущества | Ограничения |
---|---|---|
Твердость | Superior hardness ensures long-lasting performance in cutting and drilling applications. | High hardness can also make them brittle under certain conditions. |
Износостойкость | Excellent wear resistance reduces downtime and the need for frequent replacements. | Wear resistance may come at the expense of toughness in some compositions. |
Жесткость | Carbide buttons are tough enough to withstand high impact forces. | In very demanding conditions, toughness may be insufficient, leading to chipping or breakage. |
Стоимость | Though more expensive upfront, their durability often leads to cost savings over time. | The higher initial cost can be a barrier, especially for smaller operations or less demanding applications. |
Универсальность | Available in a wide range of shapes, sizes, and compositions to suit different applications. | The variety can make it challenging to choose the right type without proper knowledge or guidance. |
Understanding these factors allows you to weigh the pros and cons and make a more informed choice tailored to your specific needs.
Suppliers and Pricing Details for Carbide Buttons
The market for carbide buttons is vast, with numerous suppliers offering a range of products. Here, we’ll highlight some well-known suppliers and provide an overview of pricing.
Top Suppliers and Pricing Overview
Поставщик | Регион | Ассортимент продукции | Ценообразование |
---|---|---|---|
Kennametal | Глобальная | Offers a wide range of carbide buttons, particularly for mining and drilling applications. | Prices vary depending on size, shape, and composition, generally ranging from $10 to $100 per button. |
Sandvik | Europe, Americas | Renowned for high-quality carbide products, including buttons for rock drilling and metal cutting. | Competitive pricing with a focus on high-performance products, typically $20 to $150 per button. |
Цементированный карбид из Чжучжоу | Азия | A major supplier in China, offering a variety of carbide buttons at lower prices. | More affordable options, often ranging from $5 to $50 per button, depending on specifications. |
Tungsten Heavy Alloy | Северная Америка | Specializes in custom carbide buttons for niche applications, with a focus on quality. | Custom orders can range significantly in price, generally starting at $30 per button. |
Ingersoll Rand | Глобальная | Offers a variety of industrial products, including carbide buttons for heavy machinery. | Premium pricing, often justified by the longevity and performance of their products, with prices ranging from $50 to $200 per button. |
Selecting a supplier involves balancing quality, cost, and service. It’s crucial to consider not just the price but also the reputation and reliability of the supplier.
How to Choose the Right Carbide Button
Selecting the perfect carbide button for your application can feel overwhelming, given the multitude of options available. But fear not, we’ve got some handy tips to help you make the right choice.
Steps to Choosing the Right Carbide Button
Шаг | Описание |
---|---|
Identify the Application | Start by clearly understanding the specific application and the demands it places on the carbide button. |
Assess the Material | Consider the hardness and abrasiveness of the material you’ll be working with, as this will influence the type of carbide button you need. |
Consider the Conditions | Evaluate the operating conditions, such as temperature, pressure, and environmental factors, which can affect the performance of the carbide button. |
Consult with Experts | Don’t hesitate to consult with suppliers or industry experts who can offer advice based on their experience and knowledge of the products. |
Test Before Committing | If possible, test a small batch of carbide buttons in your application before committing to a large purchase. This can prevent costly mistakes down the line. |
Evaluate Cost vs. Longevity | Weigh the initial cost of the carbide button against its expected longevity and performance. Sometimes, a more expensive option can save money in the long run. |
By following these steps, you can ensure that you select a carbide button that not only meets your needs but also offers the best value for your investment.
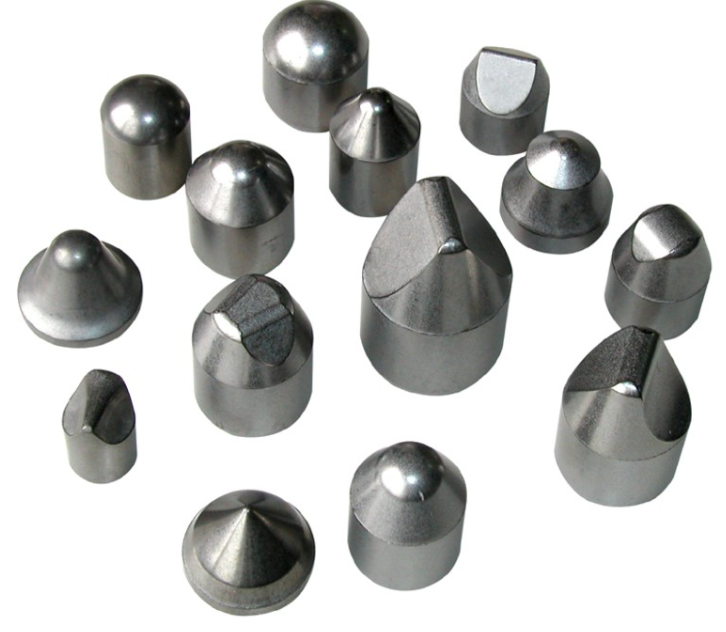
ЧАСТО ЗАДАВАЕМЫЕ ВОПРОСЫ
Вопрос | Ответить |
---|---|
What are carbide buttons made of? | Carbide buttons are typically made of tungsten carbide particles bonded with a metallic binder, such as cobalt or nickel. |
Why are carbide buttons used in drilling? | Their exceptional hardness and wear resistance make carbide buttons ideal for penetrating tough rock formations without wearing out quickly. |
Как правильно выбрать твердосплавную кнопку? | Consider the application, material, operating conditions, and consult with experts to find the best match for your needs. |
Are carbide buttons expensive? | While they can be more expensive upfront, their durability often leads to cost savings over time, especially in demanding applications. |
Can carbide buttons be used in metal cutting? | Yes, carbide buttons are commonly used in metal cutting tools due to their ability to maintain a sharp edge and resist wear. |
Каков срок службы твердосплавных кнопок? | The lifespan of a carbide button depends on the application and conditions, but they generally last much longer than other materials in similar roles. |
What shapes do carbide buttons come in? | They come in various shapes, including spherical, conical, flat-top, parabolic, chisel, hemispherical, trapezoidal, pyramid, bullet-shaped, and domed. |
Do different compositions affect performance? | Yes, the composition of the carbide button, including the type of binder and additives, can significantly affect its performance in different applications. |
Can carbide buttons resist corrosion? | Depending on the composition, some carbide buttons, especially those with nickel binders, offer good corrosion resistance. |
Где можно купить твердосплавные кнопки? | Carbide buttons can be purchased from various suppliers globally, including major companies like Kennametal, Sandvik, and Zhuzhou Cemented Carbide. |
Заключение
Твердосплавные кнопки are a crucial component in industries that require tools capable of withstanding extreme conditions. Whether you’re drilling through rock or cutting through metal, choosing the right carbide button can significantly impact the efficiency, cost-effectiveness, and success of your operation. By understanding the different types, material properties, and factors that influence their performance, you can make informed decisions that will benefit your work in the long run.