Introduction: The Unsung Heroes of Demanding Environments
In industries where harsh chemicals, abrasive materials, and extreme temperatures are the norm, conventional materials simply don’t stand a chance. Enter corrosion-resistant carbide tube blanks – the unsung heroes engineered to withstand the toughest challenges and deliver uncompromising performance. These specialized materials, crafted from tungsten carbide, offer exceptional hardness, wear resistance, and corrosion resistance, making them indispensable for a wide range of critical applications.
What are Corrosion-Resistant Carbide Tube Blanks?
The Foundation of Durable Tubular Components
Corrosion-resistant carbide tube blanks are essentially semi-finished tubular components, typically cylindrical in shape, manufactured from a composite material known as cemented carbide. Cemented carbide, often referred to simply as carbide, is a composite material composed of extremely hard tungsten carbide particles (WC) held together by a metallic binder, typically cobalt (Co). The unique properties of carbide arise from the synergistic combination of these two components:
- Карбид вольфрама (WC): Provides exceptional hardness, wear resistance, and high-temperature strength.
- Cobalt Binder (Co): Imparts toughness, allowing the carbide to withstand impact and shock loads.
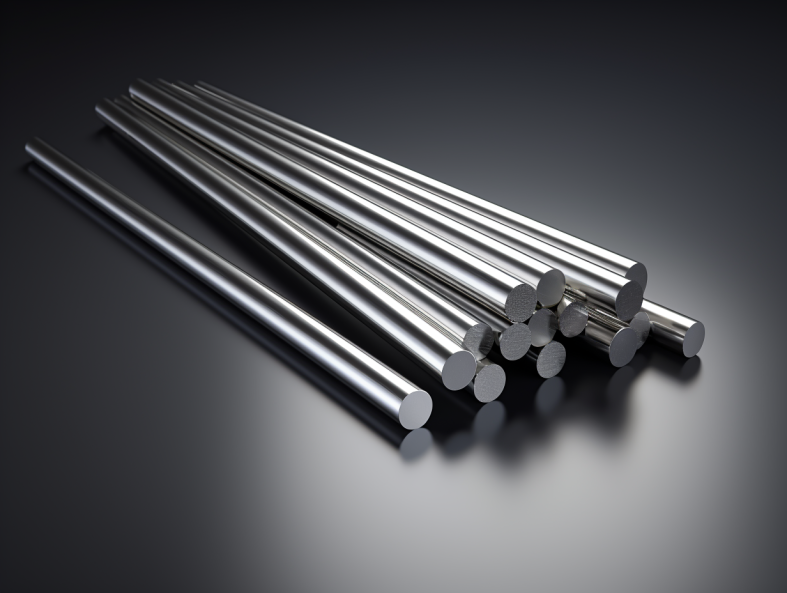
How are Corrosion-Resistant Carbide Tube Blanks Made?
From Powder to Precision: A Multi-Step Process
The manufacturing of corrosion-resistant carbide tube blanks involves a series of carefully controlled steps:
- Приготовление порошка: Finely powdered tungsten carbide and cobalt are precisely blended in specific ratios to achieve the desired properties.
- Forming: The blended powder is then compacted into the desired shape using a process called pressing. TRUER, for example, utilizes advanced electric direct drive automatic presses for high precision and stability in the forming process.
- Спекание: The pressed blanks are then subjected to high temperatures in a controlled atmosphere furnace. This process, known as sintering, fuses the carbide particles together, creating a solid, dense material.
- Отделка: After sintering, the blanks undergo various finishing operations, such as grinding, honing, or polishing, to achieve the required dimensions, surface finish, and tolerances.
Corrosion-Resistant Carbide Tube Blank Materials: A Closer Look
Table 1: Unveiling the Properties of TRUER’s Corrosion-Resistant Carbide Tube Blanks
Недвижимость | Типичное значение | Описание |
---|---|---|
Плотность (г/см³) | 14.2 – 14.8 | High density contributes to the material’s wear resistance and ability to withstand high pressures. |
Твердость (HRA) | 88 – 92 | Exceptional hardness allows the blanks to resist abrasion and maintain their shape under extreme conditions. |
Прочность при поперечном разрыве (Н/мм²) | 1800 – 2200 | Measures the material’s ability to withstand bending forces without fracturing. |
Compressive Strength (N/mm²) | 5500 – 6500 | Indicates the material’s resistance to deformation under compressive loads. |
Thermal Expansion Coefficient (10⁻⁶/K) | 4.9 – 5.5 | Describes how much the material expands or contracts with temperature changes. |
Коррозионная стойкость | Отличный | Highly resistant to a wide range of corrosive chemicals, acids, and alkalis. |
Примечание: Specific properties may vary depending on the exact carbide grade and manufacturing process.
Applications: Where Durability Meets Performance
Corrosion-resistant carbide tube blanks serve as the foundation for a wide array of components used in demanding industries:
- Нефть и газ: Nozzles, sleeves, valves, and other downhole tools operating in corrosive environments.
- Химическая обработка: Pumps, valves, seals, and reactor components handling aggressive chemicals.
- Горнодобывающая промышленность и строительство: Drill bits, cutting tools, wear parts, and structural components subjected to abrasion and impact.
- Аэрокосмическая промышленность: Engine components, landing gear parts, and other critical components requiring high strength and wear resistance.
- Медицина: Surgical instruments, implants, and other medical devices demanding biocompatibility and corrosion resistance.
Comparing Suppliers: Navigating the Carbide Landscape
Table 2: A Comparative Analysis of Corrosion-Resistant Carbide Tube Blank Suppliers
Поставщик | Расположение | Price Range (per piece, USD, approximate) | Специальности |
---|---|---|---|
Kennametal | США | $50 – $500+ | Wide range of carbide grades and sizes, custom solutions |
Sandvik Coromant | Швеция | $60 – $650+ | Focus on high-performance grades and specialized geometries |
Элемент шесть | Великобритания, Глобальный | $75 – $800+ | Expertise in advanced materials, including polycrystalline diamond (PCD) |
Ceratizit | Люксембург | $45 – $480+ | Broad portfolio of carbide products, competitive pricing |
TRUER | Китай | $35 – $400+ | Specializes in high-quality blanks, competitive pricing, fast lead times |
Примечание: Prices are highly variable and depend on blank size, material grade, quantity, and other factors.
Преимущества и ограничения: Взвешивание компромиссов
Table 3: A Balanced Perspective on Corrosion-Resistant Carbide Tube Blanks
Преимущества | Ограничения |
---|---|
Exceptional Hardness & Wear Resistance: Outperforms most other materials in abrasive and high-wear applications. | Хрупкая натура: Can be susceptible to chipping or cracking under impact or shock loads. |
High Corrosion Resistance: Withstands exposure to a wide range of corrosive chemicals and environments. | Стоимость: Higher initial cost compared to some alternative materials. |
High-Temperature Strength: Maintains strength and stability at elevated temperatures. | Задачи механической обработки: Requires specialized tooling and expertise for machining and finishing. |
Длительный срок службы: Extended lifespan reduces downtime and replacement costs. | Design Considerations: Careful design is crucial to accommodate the material’s brittleness. |
Beyond the Basics: Interesting Facts about Carbide
- Carbide’s Origins: While tungsten carbide was first synthesized in the 18th century, it wasn’t until the early 20th century that it found widespread industrial use.
- Hardness on the Mohs Scale: Tungsten carbide boasts a hardness of 8.5-9 on the Mohs scale, making it one of the hardest materials known to man, second only to diamond.
- Переработка карбида: Due to the value of tungsten, carbide is a highly recyclable material. Recycling processes can recover both the tungsten carbide and the cobalt binder for reuse.
FAQs: Addressing Your Key Questions
1. What types of corrosion can carbide resist?
Carbide exhibits excellent resistance to a wide range of corrosive agents, including acids (e.g., sulfuric acid, hydrochloric acid), alkalis (e.g., sodium hydroxide), salt solutions, and many organic solvents.
2. Can carbide be used in high-pressure applications?
Yes, carbide’s high density and compressive strength make it well-suited for high-pressure applications, such as those found in the oil & gas and chemical processing industries.
3. What are the key factors to consider when selecting a carbide grade?
The primary factors include the specific application requirements, such as wear resistance, corrosion resistance, toughness, and cost. Consulting with a carbide supplier or tooling expert is recommended.
4. How do I know if carbide is the right material for my application?
Consider the operating environment, including the presence of corrosive agents, abrasive materials, high temperatures, or extreme pressures. If these factors are present, carbide may be an ideal choice.
5. What is the typical lead time for carbide tube blanks?
Lead times can vary significantly depending on the supplier, blank size, material grade, and quantity. However, TRUER prides itself on offering competitive lead times to meet our customers’ demanding production schedules.