В мире обработки, где главенствуют точность и эффективность, выбор правильного материала для режущего инструмента может иметь огромное значение. Хотя существуют различные варианты, твёрдый сплав вставки стали бесспорными чемпионами, совершив революцию в процессах обработки во многих отраслях промышленности.
Но что именно делает твердосплавные пластины лучше других материалов для режущего инструмента? Эта статья в блоге посвящена 7 неоспоримых преимуществ которые вывели твердосплавные пластины на передовые позиции в современном производстве.
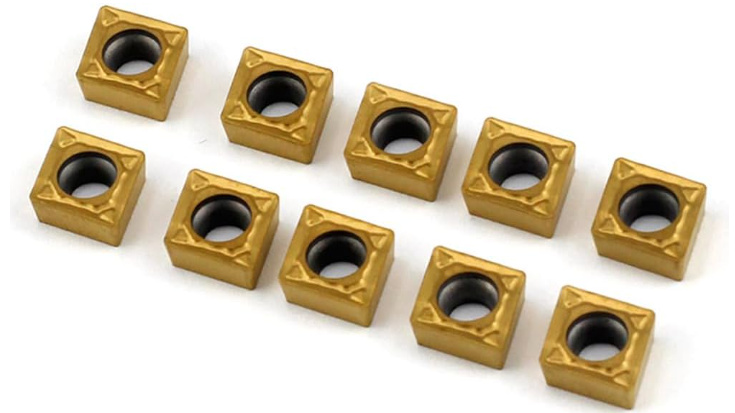
1. Непревзойденная твердость: Покоряя самые прочные материалы
Твердосплавные пластины, состоящие в основном из карбида вольфрама, обладают исключительной твердостью, значительно превосходящей твердость традиционных инструментальных сталей и быстрорежущих сталей (HSS). Эта замечательная твердость позволяет твердосплавным пластинам без труда обрабатывать широкий спектр материалов, включая:
- Закаленные стали: Твердосплавные вставки могут работать с закаленными сталями, которые быстро затупляются или повреждают инструменты из быстрорежущей стали, расширяя возможности обработки и позволяя создавать более прочные детали.
- Экзотические сплавы: В аэрокосмической и других высокопроизводительных отраслях промышленности используются экзотические сплавы с исключительным соотношением прочности и веса. Твердосплавные пластины отлично справляются с обработкой этих сложных материалов, способствуя достижениям в аэрокосмической, медицинской и других сложных областях.
- Абразивные материалы: Такие материалы, как чугун, стекловолокно и композиты из углеродного волокна, известные своими абразивными свойствами, могут быстро изнашивать традиционные режущие инструменты. Твердосплавные пластины, обладающие превосходной твердостью, противостоят износу и сохраняют режущую кромку в течение длительного времени, даже при обработке таких абразивных материалов.
2. Исключительная износостойкость: Минимизация времени простоя, максимальная производительность
Одно из самых значительных преимуществ пластин из твердого сплава заключается в их исключительной износостойкости. По сравнению с другими материалами для режущего инструмента твердосплавные пластины сохраняют остроту режущих кромок значительно дольше. Это означает:
- Уменьшение количества смен инструментов: Меньшее количество смен инструмента означает меньшее время простоя и более высокую загрузку станка, что напрямую влияет на производительность и рентабельность.
- Снижение затрат на оснастку: Хотя твердосплавные пластины могут иметь более высокую первоначальную стоимость, их увеличенный срок службы часто приводит к снижению общих расходов на инструмент с течением времени.
- Улучшенная согласованность деталей: Постоянный износ инструмента обеспечивает большую точность размеров и постоянство качества поверхности на протяжении всего производственного цикла, снижая количество брака и повышая общее качество деталей.
3. Высокоскоростная обработка: Ускорение производства, повышение эффективности
Твердосплавные пластины разработаны таким образом, чтобы выдерживать экстремальные температуры и усилия, возникающие при высокоскоростной обработке. Это позволяет:
- Повышенная скорость резки: Твердосплавные пластины могут работать на значительно более высоких скоростях резания, чем инструменты из быстрорежущей стали, что значительно сокращает время обработки и повышает производительность.
- Улучшенная отделка поверхности: Более высокие скорости резания в сочетании с присущими твердосплавным пластинам свойствами часто приводят к получению более гладких поверхностей, что снижает или устраняет необходимость в дополнительных операциях чистовой обработки.
- Усовершенствованный контроль чипов: Твердосплавные пластины с острыми режущими кромками и оптимизированной геометрией способствуют эффективному образованию и отводу стружки, что крайне важно для поддержания стабильной производительности резания и предотвращения скопления стружки, которая может повредить заготовку или инструмент.
4. Универсальность в применении: Инструмент для любой задачи
Твердосплавные вставки невероятно универсальны и выпускаются в огромном количестве марок, геометрий и покрытий, предназначенных для конкретных операций обработки и материалов. Благодаря такому широкому выбору твердосплавные пластины идеально подходят практически для любой задачи обработки, включая:
- Поворот: Твердосплавные пластины отлично справляются с обточкой внешних и внутренних диаметров, созданием канавок и разделением деталей - от черновой до чистовой обработки.
- Фрезерование: Твердосплавные пластины широко используются для фрезерования, эффективно снимая материал при торцевом, плечевом и пазовом фрезеровании.
- Бурение: Сверла с твердосплавными напайками обеспечивают превосходную производительность при сверлении, особенно при сверлении твердых материалов или при необходимости получения высокоточных отверстий.
- Скучно: Твердосплавные пластины также используются в расточных инструментах, позволяя получать точные внутренние диаметры и гладкие поверхности отверстий.
5. Повышенная точность и аккуратность: Удовлетворение требований жестких допусков
Современное производство часто требует невероятно жестких допусков, особенно в таких отраслях, как аэрокосмическая, медицинская и электронная. Твердосплавные пластины, благодаря своей способности сохранять остроту режущих кромок и сопротивляться прогибу под действием высоких сил резания, отлично справляются с этими жесткими требованиями:
- Замысловатые геометрии: Твердосплавные вставки могут создавать сложные формы и элементы с исключительной точностью, что очень важно для деталей с замысловатым дизайном или жесткими требованиями к допускам.
- Снижение вибрации: Присущая твердосплавным пластинам жесткость сводит к минимуму вибрацию при обработке, способствуя улучшению качества поверхности и повышению точности размеров.
- Тонкая отделка поверхности: Твердосплавные вставки позволяют добиться очень тонкой обработки поверхности, что часто устраняет необходимость в дополнительных операциях по обработке, таких как шлифовка или полировка.
6. Экономическая эффективность в долгосрочной перспективе: Максимизация возврата инвестиций
Хотя твердосплавные пластины могут иметь более высокую начальную стоимость по сравнению с некоторыми традиционными инструментальными материалами, их долгосрочная экономическая эффективность неоспорима.
Учитывайте эти факторы:
- Увеличенный срок службы инструмента: Твердосплавные вставки служат значительно дольше, чем инструменты из быстрорежущей стали, что сокращает частоту замены инструмента и снижает общие затраты на оснастку.
- Повышенная производительность: Более высокая скорость резания и сокращение времени простоя при замене инструмента приводят к увеличению объема производства, что позволяет максимально увеличить отдачу от инвестиций.
- Улучшенное качество деталей: Постоянный износ инструмента и повышенная точность позволяют получать детали более высокого качества, снижая количество брака и минимизируя отходы материала.
7. Совместимость с передовыми технологиями обработки
Твердосплавные вставки совместимы с широким спектром передовых технологий обработки, что еще больше повышает их возможности и расширяет сферу применения:
- Обработка с ЧПУ: Твердосплавные вставки идеально подходят для использования в обрабатывающих центрах с числовым программным управлением (ЧПУ), где точность и повторяемость имеют первостепенное значение.
- Системы охлаждения высокого давления: Использование систем СОЖ высокого давления в сочетании с твердосплавными пластинами оптимизирует отвод стружки, улучшает теплоотвод и продлевает срок службы инструмента, особенно при сложных операциях обработки.
- Сухая обработка: Некоторые марки твердосплавных пластин специально разработаны для сухой обработки, что исключает необходимость использования смазочно-охлаждающих жидкостей и способствует экологически безопасным производственным процессам.
Твердосплавные пластины в сравнении с другими материалами для режущего инструмента: Сравнительный обзор
Материал | Твердость | Износостойкость | Скорость резки | Стоимость | Преимущества | Недостатки |
---|---|---|---|---|---|---|
Твердосплавная вставка | Крайне высокий | Отличный | Высокая | Высокая | Исключительная твердость, износостойкость, возможность работы на высоких скоростях, универсальность, точность | Более высокая первоначальная стоимость |
Высокоскоростная сталь (HSS) | Высокая | Хороший | Умеренный | Умеренный | Хороший общий баланс свойств, подходит для широкого спектра материалов | Более низкая твердость и износостойкость по сравнению с твердосплавными вставками |
Кобальтовая сталь | Очень высокий | Очень хорошо | Умеренный | Высокая | Отличная термостойкость, подходит для высокотемпературных применений | Дороже, чем быстрорежущая сталь, ниже твердость, чем у твердосплавных пластин |
Керамика | Крайне высокий | Отличный | Очень высокий | Очень высокий | Исключительная твердость, износостойкость и способность работать на высоких скоростях, подходит для очень твердых материалов | Хрупкие, подвержены сколам и поломкам |
Заключение: Использование преимуществ карбида
Преимущества твердосплавных пластин перед другими материалами для режущего инструмента неоспоримы. Их исключительная твердость, износостойкость, способность работать на высоких скоростях, универсальность и точность произвели революцию в процессах обработки, позволив создавать более качественные, сложные и доступные изделия во многих отраслях промышленности.
По мере развития технологий и ужесточения производственных требований твердосплавные пластины, несомненно, будут оставаться в авангарде технологий производства режущих инструментов, стимулируя инновации и определяя будущее производства.
Хотите купить твердосплавную вставку отличного качества по правильной цене? Нажмите здесь.