はじめに腕力しかないとき
巨大なワークと過酷な材料が工具技術の限界を試す過酷な重切削加工の世界では、最もタフな工具だけが生き残ります。参入 タイプD カーバイド ロー付けチップ比類なきパワーと反発力で、最も困難な切削条件を克服するために設計された、機械加工の世界の主力製品です。
この記事では、タイプDの超硬ろう付けチップの領域について掘り下げ、そのユニークな特性や利点、そして最大限の切り屑処理と揺るぎない信頼性が譲れない場合に最適な選択である理由を探ります。
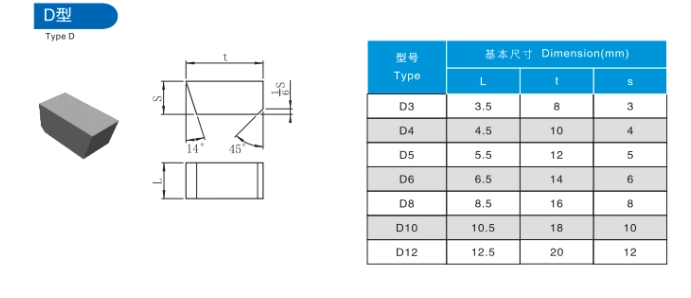
機械加工の重鎮たち:最も困難なアプリケーションに挑む
他のツールは失敗しても、タイプDのチップは勝てる
頑丈な機械加工:
- 高い材料除去率: 大量の材料を迅速かつ効率的に除去。
- 機械加工が困難な材料: 従来の工具がすぐに摩耗してしまうような、靭性の高い、研磨性の高い、または高温の合金の作業。
- 極端な切断力: 大きな切削力を発生させるため、堅牢な工具と機械のセットアップが必要です。
このような厳しい条件下では、卓越した超硬ろう付けチップが必要になります:
- 強さとタフネス: 重切削時に発生する莫大な力と応力に耐える。
- 耐摩耗性: 研磨材を加工する際、切れ刃の完全性と工具寿命を維持する。
- 熱安定性: 高速加工時に発生する高温での変形に耐え、切れ味を維持する。
タイプD超硬ろう付けチップ:最大限の金属除去
強さと耐久性のシンフォニー
Dタイプ超硬ろう付けチップは、重切削加工用に開発されたもので、その特徴により区別されます:
- ニュートラルまたはややポジティブなレーキアングル: このすくい角は、刃先の強さと切れ味のバランスをとり、切れ味を提供する:
- 頑丈な刃先: 重切削加工で一般的な高い衝撃荷重と断続切削に耐える。
- 効率的なチップフロー: 大量の材料除去時に発生する大きな切りくずの除去を容易にする。
- 大きなノーズ半径: タイプDのチップは、ノーズ半径が大きい:
- 刃先強度の向上: 切削力を広範囲に分散し、チッピングや破損のリスクを低減。
- 高送り速度での表面仕上げの向上: 主に仕上げ加工用として知られているわけではないが、ノーズ半径が大きいため、重切削加工で一般的な高い送り速度でも許容できる仕上げ面が得られる。
- タフな超硬グレード: タイプDのチップには、コバルト(Co)含有量の高い超硬合金や、タンタル(Ta)やニオブ(Nb)などの他の元素を添加した超硬合金がよく使用されます。これらの鋼種には、以下の特長があります:
- 並外れた強さとタフネス: 重切削加工で遭遇する極端な力を処理する。
- 高い耐摩耗性: 研磨材加工時の工具寿命の延長。
- 熱安定性: 高温下でも切れ刃の完全性を維持。
重切削加工におけるD型超硬ろう付けチップの利点
最も過酷なカットを乗り切る
D型超硬ろう付けチップの堅牢な設計と材料特性は、いくつかの重要な利点につながります:
- 高い材料除去率: その強度と靭性は、積極的な切削パラメータを可能にし、生産性を最大化し、加工時間を短縮する。
- 困難な材料における工具寿命の延長: その耐摩耗性により、研磨材や高温合金の加工でも工具寿命が延びる。
- 信頼性と予測可能性: その堅牢な構造は、予期せぬ工具の故障のリスクを最小限に抑え、一貫した性能と予測可能な結果を保証します。
- ヘビーデューティ用途での汎用性: D型チップは、フライス加工、旋削加工、中ぐり加工、溝入れ加工など、幅広い重切削加工に適している。
D型超硬ろう付けチップの用途
パワーと耐久性が支配する場所
D型超硬ろう付けチップは、他の工具では対応できないような重切削加工で威力を発揮します:
- 荒削りな作業: フライス加工や旋盤加工で、大量の材料を素早く除去。
- 高温合金の加工: インコネル、チタン、ステンレス鋼など、切削温度が高くなる材料を扱う。
- 研磨材の切断: 鋳鉄、焼入れ鋼、その他の従来の工具をすぐに摩耗させるような材料の加工。
- 重い中断カット: 工具がワークピースに何度も出入りするフライス加工のような用途で発生する衝撃荷重や変動する力に耐える。
正しいタイプD超硬ブレージングチップの選択:考慮すべき要素
過酷な条件下での工具選択の最適化
最適なタイプDの超硬ろう付けチップを選択するには、慎重に評価する必要があります:
- 工作物の材質: 材料の硬度、研磨性、熱特性は、適切な超硬グレードとコーティングを決定する上で極めて重要な要素です。
- 加工作業: 荒フライス加工、高温合金の旋削加工、大径のボーリング加工など、特殊な重切削加工は、チップの形状とサイズの選択に影響する。
- 切断パラメータ: 希望する切削速度、送り速度、切り込み深さは、切削力と温度に直接影響するため、チップの選択において重要な役割を果たす。
- 工作機械の能力: 工作機械の剛性とパワーは、チップサイズと切削パラメーターの選択を制限することがある。
タイプD超硬ろう付けチップの選択:簡易ガイド
選択プロセスを支援するために、異なるタイプDチップ形状の典型的な用途と考慮点をまとめた表を以下に示す:
タイプD チップ形状 | 代表的なアプリケーション | 主な検討事項 |
---|---|---|
高ポジットのインサート | 高送りフライス加工、荒加工 | 強度とチップフローのバランスが良い。 |
ダブルネガティブ・インサート | 重切削、断続切削 | 最高の強度と耐チッピング性を提供 |
ボタン挿入 | ヘビーデューティーボーリング、深溝加工 | 最大限のサポートと剛性を提供し、大きな切り込み深さに対応 |
D型超硬ろう付けチップに関するよくある質問
Q1: タイプDの超硬ブレージングチップは仕上げ加工に使用できますか?
A1: 繊細な仕上げ面を得るには理想的ではありませんが、タイプDのチップは、仕上げ面の要求がそれほど厳しくない一部の重切削用途の仕上げ切削に使用できます。
Q2: タイプDの超硬ろう付けチップの摩耗の兆候は何ですか?
A2: 一般的な摩耗の兆候には、切れ刃の逃げ面摩耗、すくい面のクレーター、高温による切れ刃の塑性変形などがある。
Q3:重切削加工でタイプDの超硬ブレージングチップの工具寿命を最大限に延ばすにはどうしたらいいですか?
A3: 主な要因としては、アプリケーションに適したチップ形状と材種の選択、切削パラメータの最適化(材料除去速度と工具寿命のバランス)、高圧クーラントシステムの使用、機械のセットアップの厳密化などが挙げられる。
Q4: D型チップのハイポジティブ・インサートとダブルネガティブ・インサートの違いは何ですか?
A4: ハイポジチップは、効率的な切り屑の流れと高送りのフライス加工用に設計されており、ダブルネガティブチップは、高負荷の旋削加工や断続切削加工において、最高の強度と耐チッピング性を発揮します。
Q5: どのような場合にD型チップを選ぶのですか?
A5: ボタンチップは、工具のたわみを防止し、正確な穴径や溝寸法を確保するために、最大限のサポートと剛性が必要とされるヘビーデューティーなボーリング加工や深溝加工に最適です。