超硬スクエアブランク タングステンカーバイドとは、様々な切削工具や摩耗部品を製造するための出発材料となる、正方形状の炭化タングステン片を指します。炭化タングステンのユニークな特性は、それが高い耐摩耗性のアプリケーションのための理想的な材料になります。
このガイドでは、超硬スクエアブランクの詳細な概要、その組成、製造工程、サイズ、公差、用途、選択上の考慮事項、サプライヤー、コスト、代替品との比較について説明します。
超硬スクエアブランクスの紹介
超硬スクエアブランクには、次のような主な特徴があります:
- タングステンカーバイド素材の四角形片
- 異なる標準サイズで利用可能
- 切削工具製造用ブランクとして使用
- 非常に高い耐摩耗性を提供
- HSSのような他の工具材料よりも硬い
- 炭化タングステン粉末の焼結により製造
タングステンカーバイドブランクは、標準化された出発原料として機能し、アプリケーションの要件に基づいて、チップ、ダイ、フォームカッターなどの最終的な工具製品に研削および成形することができます。
超硬ブランクの組成と特性
タングステンカーバイトブランクスの組成と特性は、次のとおりです:
- コバルトマトリックスで結合された炭化タングステン粒でできています。
- 85-95%タングステンカーバイドと5-15%コバルトバインダーを含有
- 少量のその他の炭化物および添加物
- 極めて硬い - HV 1300-1600 kg/mm2
- 密度14.5~15.1g/cc
- 6.5GPaまでの圧縮強度
- 高い剛性と熱伝導性
- 優れた耐摩耗性と耐侵食性
炭化タングステンのユニークな特性は、他の工具材料よりも優れた耐摩耗性を提供します。コバルトバインダーは、破壊靭性を与えます。超硬合金の粒径とコバルト含有量は、用途に応じて調整されます。
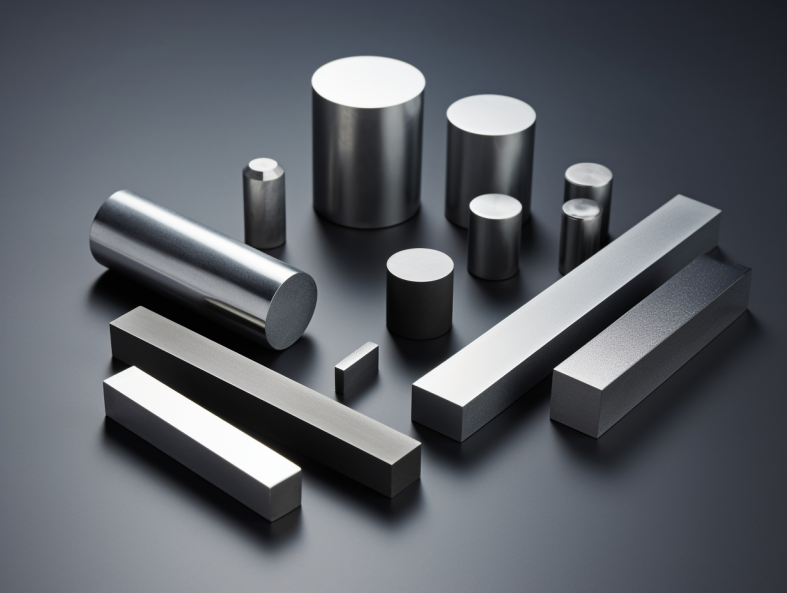
超硬ブランクの製造工程
超硬スクエアブランク が製造している:
パウダー加工
- 炭化タングステン、コバルト、その他の粉末添加剤のブレンド
- 粉体をボールミルして均一な混合物を得る
コンパクション
- 粉砕した粉末を金型に入れて高圧でプレスする。
- 複雑な形状に使用される冷間静水圧プレス
- グリーン」な小型部品を生産
焼結
- 制御された雰囲気中で小型部品を1400~1500℃に加熱する。
- 粒子の緻密化と結合を引き起こす
- 焼結時の20%以上の収縮
仕上げ
- 寸法公差を達成するためのブランクの研削
- ラッピング、ホーニング、ポリッシングで必要な表面仕上げを行う。
- ±0.025mmの緊密な寸法管理
制御されたプレス工程と焼結工程により、ブランクの一貫した特性と寸法が保証される。
超硬ブランクのサイズと公差
タングステンカーバイトブランクは、標準化された正方形サイズで製造されます:
一般的な標準サイズ
- 10 x 10 mm
- 12 x 12 mm
- 16 x 16 mm
- 20 x 20 mm
- 25 x 25 mm
厚さ範囲
- 2 mm~10 mm
サイズ公差
- ±0.025 mm
さまざまな切削工具の要件に合わせて、さまざまな寸法のブランクを製造しています。ブランクを厚くすることで、より長い工具を製造し、剛性を高めることができます。正確な寸法管理により、最終工具を製作する際に必要な研削代を最小限に抑えます。
超硬ブランクスの用途と使用法
超硬スクエアブランクの主な用途は以下の通り:
- 切削工具 - チップ、ドリル、エンドミル、成形工具
- 絞りおよび押し出しダイス
- 伸線ダイス
- ペレタイジングプレス
- スタンピングおよびコイニング金型
- ベアリングとシール
- 鉱業・建設工具
超硬ブランクは、非常に高い硬度、強度、耐摩耗性を必要とする摩耗部品の製造に理想的な出発材料です。研削されたブランクは、ろう付けされるか、ツールホルダーにクランプされます。
超硬ブランクスの利点と利点
を使用する主な利点 超硬スクエアブランク:
- 極めて高い硬度と耐摩耗性
- 高い圧縮強度と曲げ強度
- 高温下でも強度を維持
- 耐熱衝撃性と耐腐食性
- 管理された製造による一貫した特性
- 工具設計を容易にする標準寸法
- カスタム焼結部品より安価
- 特注ブランクサイズより短納期
- 最終工具形状への加工が容易
タングステンカーバイドのユニークな特性と標準化されたスクエアブランクの組み合わせにより、高磨耗工具用途に理想的でコスト効率の高い選択肢となります。
工具材料としての超硬合金の限界
タングステンカーバイドの限界として考慮すべき点がいくつかある:
- 破壊靭性が低く脆い
- 衝撃荷重で欠けやすい
- ダイヤモンド研削を必要とする加工は困難
- 他の工具材料より重い
- ハイス工具より高価
- 正方形のブランクは工具形状のオプションを制限する
- 剛性の低いホルダーには適さない
- 一部の合金との化学的不適合性
- 再研磨はブランクの精度を変える
この制限のために、特定の用途要件に基づいて超硬工具を適切に設計する必要がある。
超硬ブランクの価格とコスト
超硬スクエアブランクの価格帯は以下の通りです:
タングステンカーバイトブランクスの価格
サイズ | 厚さ | 価格帯 |
---|---|---|
10 x 10 mm | 3 mm | $8 – $12 |
16 x 16 mm | 5 mm | $15 – $22 |
20 x 20 mm | 6 mm | $25 – $35 |
25 x 25 mm | 8 mm | $45 – $60 |
- 価格は、サイズ、等級、厚さ、注文数量によって異なります。
- 粒度の細かいグレードはより高価
- 厚いブランクは高価
- 小口注文は1個あたりのコストが高い
タングステンカーバイドは、他の工具材料よりも高価ですが、極端な摩耗条件下ではるかに長い寿命を提供します。そのため、特定の用途では経済的です。
超硬ブランクの選び方
超硬ブランクの主な選択基準:
- 申し込み - 予想摩耗率、負荷、速度、温度などのパラメータ
- ツールサイズ - 完成工具寸法に最も近い標準ブランクサイズを選択
- 厚さ - 剛性を必要とする長尺工具用の厚いブランク
- 公差 - 精密磨耗部品の厳しい公差
- 表面仕上げ - より優れたパフォーマンスを実現する、より微細な表面仕上げ
- グレード - 硬度、強度、靭性のバランス
- コーティング - 潤滑性、耐摩耗性を向上させるあらゆるポストコーティング
- メーカー - 安定した品質を保証する定評あるメーカー
- 配送 - 標準ブランクで短納期を実現
- コスト - 性能と総工具コストのバランス
工具設計者は、各工具の用途に合わせて最適なブランク仕様を選択します。
超硬ブランクと代替品の比較
他の工具材料との比較
パラメータ | 炭化タングステン | 高速度鋼 | セラミックス |
---|---|---|---|
耐摩耗性 | 素晴らしい | 中程度 | 素晴らしい |
タフネス | 中程度 | 非常に良い | 低い |
熱特性 | グッド | 中程度 | 素晴らしい |
耐食性 | 素晴らしい | 中程度 | 素晴らしい |
加工性 | 難しい | 簡単 | 難しい |
コスト | 高い | 低い | 高い |
カスタム焼結部品に対する利点
- 大幅なコスト削減
- 標準サイズの納期短縮
- 工具設計の制約を削減
- 在庫管理の簡素化
タングステンカーバイトブランクは、特に標準サイズが要件を満たす場合、ほとんどの磨耗部品用途に特性とコストの理想的なバランスを提供します。
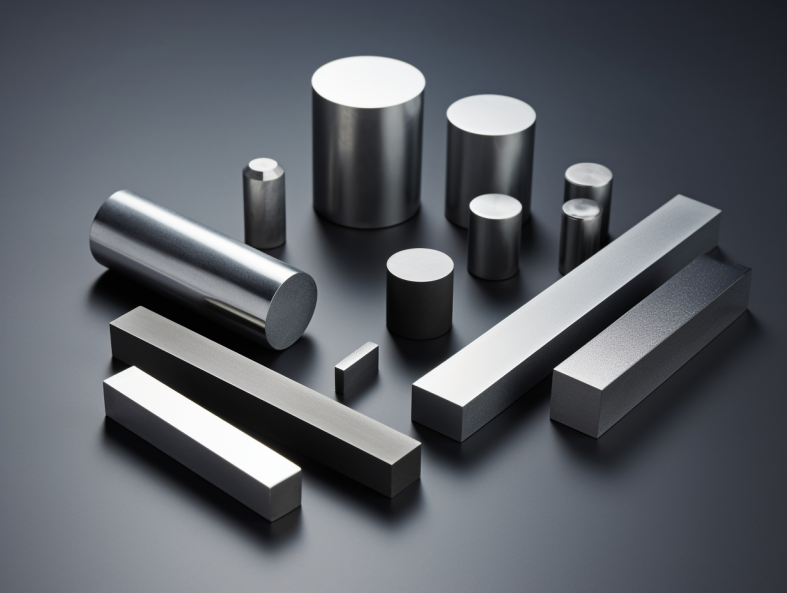
よくあるご質問
炭化タングステンのブランクは何に使われるのですか?
炭化タングステンブランクは、高い耐摩耗性が要求される各種切削工具、金型、ベアリング、摩耗部品などの製造の出発原料として使用されます。
炭化タングステンのブランクはどのように製造されるのですか?
TCブランクは、炭化タングステンとコバルトの粉末を圧縮し、高温で焼結して高密度の材料を製造する。焼結された部品は、形状に合わせて研磨されます。
炭化タングステンの主な特性は?
炭化タングステンは、非常に高い硬度と圧縮強度、優れた耐摩耗性と耐侵食性、高い熱伝導性、優れた耐食性を持っています。
カスタム焼結部品とTCブランクを使用する利点は何ですか?
標準化されたブランク・サイズを使用することで、コスト削減、納期短縮、柔軟性の向上といったメリットが得られます。これにより、在庫と生産が簡素化されます。
超硬ブランクのサイズとグレードを正しく選択するには?
工具のサイズ、必要な剛性、公差、表面仕上げ、生産量、使用条件、および工具の総コストを考慮してください。評判の良いメーカーを選ぶ。
タングステンカーバイドブランクスの公差は?
一般的な寸法公差は±0.025mmです。精密な用途では±0.01mmのような微細な公差も可能ですが、コストが高くなります。
炭化タングステンのブランクは、どのように研ぎ直されるのですか?
TCブランクは、損傷を最小限に抑えるために適切な砥石を選択し、ダイヤモンド研削によって研がれます。研ぎを繰り返すと、ブランクの精度が損なわれ、交換が必要になることがあります。
工具材料として超硬合金を使用することの限界は何ですか?
他の材料に比べ靭性が低い、機械加工が難しい、部品が重い、基本コストが高いなどの制限がある。適切な設計とアプリケーション・エンジニアリングが重要である。
超硬ブランクにはどのようなコーティングが施されていますか?
一般的なコーティングには、窒化チタンアルミニウム(TiAlN)、窒化チタン(TiN)、炭窒化チタン(TiCN)などがあります。これにより、特定の用途における摩耗性能と工具寿命が向上します。