はじめに正確さが支配する場所
1000分の1インチが部品の機能を左右する複雑な機械加工の世界では、精度が最も重要です。入 タイプF カーバイド ロー付けチップ機械加工界の縁の下の力持ちであり、要求の厳しい仕上げ加工や中仕上げ加工において、卓越した精度と仕上げ面粗さを実現するために綿密に設計されています。
この記事では、タイプFの超硬ブレージングチップの領域について掘り下げ、そのユニークな特性、利点、そして厳しい公差と完璧な表面を達成することが譲れない場合に最適な選択である理由を探ります。
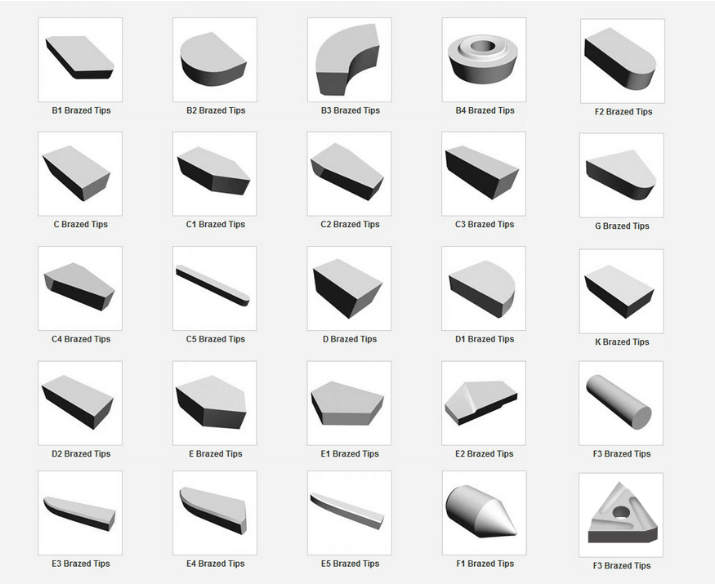
完璧の追求:仕上げと半仕上げの役割
荒削りから洗練へ:機械加工の段階
機械加工は通常、荒加工から仕上げ加工へと進む:
- ラフィング 初期段階では、ワークピースのおおよその形状と寸法を達成するために、大量の材料を素早く除去することに重点を置く。
- 準仕上げ: 荒加工と仕上げ加工のギャップを埋める中間段階で、ワークピースの形状と表面品質をさらに洗練させる。
- 仕上げ: 最終段階で、望ましい寸法精度、表面仕上げ、完成部品の全体的な品質を達成することに専念する。
タイプFの超硬ブレージングチップは、仕上げや中仕上げの領域で優れています:
- 厳しい公差: 1000分の1インチ以内の寸法精度を維持することは、部品の適切な適合、機能、組み立てにとって極めて重要です。
- 優れた表面仕上げ: 滑らかで欠陥のない表面を実現することは、美観を損なわず、摩擦や摩耗を減らし、耐食性を高めるために不可欠です。
タイプF超硬ろう付けチップ:精密設計による完璧な仕上がり
精度と表面忠実度の解剖学
タイプFの超硬ろう付けチップは、仕上げおよび中仕上げ作業用に綿密に設計されており、その特徴は次のとおりです:
- 鋭い刃先: 多くの場合、プラスとマイナスのすくい角の組み合わせを特徴とするタイプFのチップは、鋭い切れ刃を優先することで、切削力を最小限に抑え、滑らかで正確なカットを実現し、卓越した仕上げ面をもたらします。
- 小さな鼻の半径: タイプFのチップはノーズ半径が小さいので、これが可能になる:
- 細かい表面のディテール: デリケートな形状を正確に加工し、ワークピースにタイトなRを実現します。
- スキャロップの最小化: 特に直径の大きな工具を使用する場合、輪郭のある表面に発生する可能性のある、目に見えるスカラップや隆起を減らす。
- 細粒超硬合金: タイプFのチップは、一般的に高硬度で耐摩耗性に優れた細粒超硬合金を使用しています。これらの材種は
- 鋭い刃先を維持する: 仕上げ工程全体で一貫した精度と表面仕上げを達成するために不可欠。
- 刃先の摩耗を最小限に抑える: 頻繁な工具交換の必要性を減らし、予測可能な高品質の結果を保証します。
仕上げ・中仕上げにおけるF型超硬ろう付けチップの利点
精度と表面の卓越性の追求
F型超硬ろう付けチップの綿密な設計と材料特性は、いくつかの重要な利点につながります:
- 卓越した寸法精度: 鋭利な切れ刃ときめの細かい超硬合金は、厳しい公差を実現し、部品が厳しい寸法要件を満たすことを保証します。
- 優れた表面仕上げ: シャープな切削形状、微細な超硬合金、最小限の切削力の組み合わせにより、非常に滑らかで欠陥のない表面が得られます。
- 仕上げ加工における工具寿命の延長: 荒加工用チップのように大きな切削力を受けることはありませんが、タイプFのチップは耐摩耗性の高い超硬材種を使用しているため、特に切削パラメータが中程度の仕上げ加工において、工具寿命の延長を実現します。
- 精密加工における多様性: タイプFのチップは、微細なフライス加工、輪郭加工、プロファイル加工、仕上げ旋盤加工など、幅広い仕上げ・中仕上げ加工に適しています。
F型超硬ろう付けチップの用途
精度と表面品質を重視する場所
タイプFの超硬ろう付けチップは、厳しい公差と優れた表面仕上げを達成することが重要な用途に優れています:
- 金型製作: プラスチック部品、ゴム部品、金属鋳物の製造に使用される金型やダイの複雑なキャビティ、中子、エジェクターピン穴の加工。
- 航空宇宙製造: 空気力学的性能、燃費、構造的完全性に不可欠な、厳しい公差と滑らかな表面を持つ重要な部品を製造。
- 医療機器製造: 生体適合性と表面品質が重要な医療用インプラント、手術器具、その他の精密医療機器に、複雑な形状や滑らかな仕上げを施す。
- 光学部品: レンズ、ミラー、その他の光学部品を、非常に厳しい公差と滑らかな表面で加工し、適切な光の透過と反射を確保する。
正しいタイプF超硬ろう付けチップの選択:考慮すべき要素
精密仕上げのための工具選択の微調整
最適なF型超硬ろう付けチップを選択するには、慎重に評価する必要があります:
- 工作物の材質: 材料の硬度、研磨性、熱特性は、適切な超硬グレードとコーティングを決定する上で極めて重要な要素です。
- 表面仕上げの要件: Ra(平均粗さ)またはRz(平均ピーク・ツー・バレー粗さ)で指定されることが多い所望の表面仕上げは、チップ選択の主な要因です。
- 公差要件: 要求される寸法公差は、チップ形状の選択と刃先の準備に影響します。
- 加工作業: 微細フライス加工、輪郭加工、仕上げ旋盤加工など、特定の仕上げ加工または中仕上げ加工は、チップの形状とサイズの選択に影響を与える。
- 工作機械の能力: 工作機械の剛性と精度は、達成可能な表面仕上げと公差に影響を与えます。
タイプF超硬ろう付けチップの選択:簡易ガイド
選択プロセスを支援するために、異なるタイプFチップ形状の典型的な用途と考慮点をまとめた表を以下に示す:
タイプF チップ形状 | 代表的なアプリケーション | 主な検討事項 |
---|---|---|
小ノーズラウンドインサート | 汎用仕上げ、輪郭加工、プロファイリング | 切れ味と強度のバランスが良く、幅広い用途に対応。 |
シャープなコーナーのスクエアインサート | 平らな面の仕上げ、肩のフライス加工 | 正確な90度ショルダーと平らな面のためのシャープなコーナーを提供します。 |
シャープポイント付きダイヤモンドインサート | 彫刻、微細加工、複雑な金型加工 | 繊細なディテールと最も狭い半径のための卓越したシャープネスを提供します。 |
タイプF超硬ろう付けチップに関するよくある質問
Q1:可能ですか? タイプF超硬ろう付けチップ 荒削りに使えるか?
A1: タイプFのチップは荒加工用に設計されておらず、そのような用途での使用は推奨されません。鋭利な切れ刃と細粒の超硬合金は、仕上げ加工と精密加工に最適化されており、重切削には適していません。
Q2: タイプFの超硬ろう付けチップの摩耗の兆候は何ですか?
A2: 一般的な摩耗の兆候には、切れ刃の丸み、すくい面または逃げ面の摩耗、切れ刃のビルドアップエッジ(BUE)の形成などがある。仕上げ加工では、摩耗は表面仕上げの悪化や寸法精度の低下として現れることがある。
Q3: タイプFの超硬合金製ろう付けチップで、最高の仕上げ面を得るにはどうすればよいですか?
A3: 重要な要素には、用途に適したチップ形状と材種の選択、切削パラメータの最適化(低送りおよび低切り込みの使用)、適切な切削油剤の塗布の確保、機械のセットアップの厳格な維持などがある。
Q4: 丸型チップと角型チップの違いは何ですか?
A4: 小さなノーズ半径を持つ丸いチップは、一般的な仕上げや輪郭加工に適した切れ味と強度のバランスを提供し、鋭いコーナーを持つ四角いチップは、平らな面の仕上げや正確な90度ショルダーの作成に最適です。
Q5: どのような場合にダイヤモンドインサート・タイプFのチップを選ぶのでしょうか?
A5: 鋭利な先端を持つダイヤモンドチップは、彫刻、微細加工、複雑な金型加工など、細部まで精巧に仕上げることが最も重要な加工において、卓越した切れ味を発揮します。