概要 超硬焼結体ブランク
焼結カーバイドブランクとは、タングステンカーバイド粉末を圧縮・焼結した部品のことで、ほぼ完全な高密度で寸法精度の高いものを指します。主な特徴は以下の通りです:
- 高い硬度、耐摩耗性、強度
- 鋭利な刃先は、研削によって付与することができる。
- 鋼体にろう付けして超硬切削工具を製造可能
- 剛性と寸法安定性に優れた機械加工用基板
- シェーピングだけでは不可能な複雑な形状が可能
- 特定の加工用途に合わせたグレードを用意
超硬ブランクは、労働集約的な超硬ソリッドからの加工に比べ、経済的な方法で刃先交換式チップやその他の切削工具を製造することができます。
超硬ブランクの製造工程
超硬ブランクは粉末冶金技術を用いて製造される:
- 粉体をボールミルで粉砕し、均一な小粒径を実現
- 粉末をバインダーとともに顆粒状に噴霧乾燥する。
- 粉末顆粒を高圧で金型に圧縮する
- 1000~1300℃で予備焼結し、ハンドリング強度を付与
- ブランクを正確な寸法と表面仕上げに研削する。
- 1350-1650℃の高温真空焼結で完全密度にする。
- ブランクをスチール工具本体にろう付け
- 研削刃のプロファイルと特徴
各生産工程を正確に管理することで 超硬焼結ブランク 均一性に優れ、経済的に製造できる。
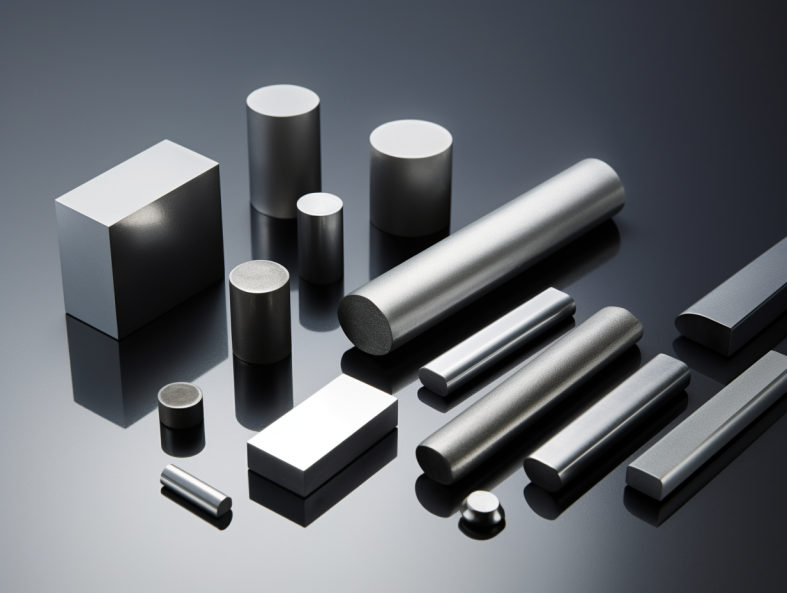
超硬ブランク材種
さまざまな加工用途に合わせて、さまざまなグレードが用意されています:
グレード | 説明 | 主要物件 | 代表的な用途 |
---|---|---|---|
C1-C3 | ストレート・タングステン・カーバイド | タフネス | 低摩耗、アルミニウム、真鍮 |
C5-C6 | コバルトタングステン炭化物 | 耐摩耗性 | 鋼、焼き入れ材 |
C7-C8 | 微粒炭化物 | 赤の硬度、強度 | 高速度鋼、チタン |
C9-C10 | 粗粒炭化物 | 耐破壊性 | 荒加工と断続加工 |
サーメット | 炭窒化チタン合金 | 高温強度 | 高速で硬い素材 |
工具の性能と寿命を最大化するには、被削材と加工に適した材種を適切に選択することが重要です。
超硬ブランクの設計原則
超硬ブランクを設計する際には、いくつかの要素が重要である:
- 硬度と品位は用途に適合していなければならない。
- 均一で微細な炭化物粒径が性能を向上
- 余裕のあるフィレット半径で応力を最小化
- 応力を集中させる鋭い角がない
- 適切なクリアランス・アングル、エッジ・プレップ、チップ・ブレーカー
- 適切な衝撃靭性と破壊靭性を持つこと
- 焼結時の収縮の考慮
- 工具本体への取り付けを可能にするブレーズ機能
- 研削の寸法公差の指定
高度なシミュレーションツールにより、仮想設計の最適化とプロセスのモデリングが可能になり、ブランクの品質が向上します。
超硬ブランクの寸法と公差
超硬ブランクは、寸法公差が厳しく、幅広い標準サイズおよびカスタムサイズと形状で製造されます:
- 直径3 mm~150 mm以上
- 厚さ1 mm~50 mm+
- 長さ: 300 mmまで
- 形状:丸型、正方形、長方形、各種インデックス
- 寸法公差最大±0.025 mm
- 平坦度<0.025 mm
- 表面仕上げ最大Ra 0.2 μm
高精度の公差を維持することで、最終研削時の取り代を最小限に抑え、優れた仕上がりを実現します。規格外のブランクも特注で製作可能です。
超硬焼結体ブランクの用途
超硬ブランクは、以下の分野で幅広く使用されています:
- 切削工具 - ターニング、フライス、ドリル、溝加工、ねじ切り
- 金属成形 - パンチ、ブランキングダイ
- 鉱業 - コールピック、ドリルビット
- 木工 - カッター、鋸刃、ルータービット
- 複合材料 - 切削工具およびフライス工具
- バイオメディカル - 歯科用バリ、ドリル、整形外科用工具
- ジュエリー - ダイヤモンドスカイフ、エングレービングツール
- セラミックス - 切削工具およびスライス工具
- ガラス - カッター、ドリル
超硬ブランクは、精密刃先交換式チップや幅広い回転切削工具の経済的な生産を可能にします。
使用するメリット 超硬焼結体ブランク
超硬ブランクの主な利点
- さまざまなサイズでコスト効率の高い生産
- 優れた寸法精度と再現性
- 機械加工では得られない均一な微細炭化物粒度
- シャープな刃先と複雑な形状を実現
- パートごとに一貫したパフォーマンス
- 最小限の研磨でネットに近い形状
- 機械加工に比べてリードタイムが短い
- 大量生産の自動化が容易
- ソリッドカーバイドの加工に比べて廃棄物が少ない
- 複雑な形状や壊れやすい形状も製作可能
- 鋳造、研削の超硬部品より優れている
- 革新的な切削工具の設計が可能
- 刃先交換式チップの製造を簡素化
超硬ブランクは、設計の柔軟性とともに、材料費、加工費、製造費の大幅な節約を実現します。
超硬焼結体ブランクの限界
超硬ブランクの使用に伴う欠点もある:
- 超硬グレードと材料の選択肢は限られている
- 複雑な内部形状のない、より単純なブランク形状に限定される。
- 焼結炉の能力によって制限される最大サイズ
- 単一ツールのプロトタイピングや少量生産には適さない。
- プレス金型と工程最適化のための初期費用が高い
- 二次研削はまだ必要
- ろう付けプロセスには専門知識が必要で、コストがかかる
- 脆性的な挙動により、成形や加工の選択肢が制限される
- 設計に必要な高度なシミュレーションスキル
- 超硬ソリッド工具より格下と思われる
しかし、ほとんどの商業用切削工具製造では、その利点が制限を大きく上回ることが多い。
超硬ブランクの品質管理試験
品質を確保するためには、粉末、成形品、焼結ブランク、完成工具の広範なテストが必要である:
- 化学組成 - 適切な炭化物の種類とバインダーの含有量を確認します。
- 粒度分布 - 充填密度に最適なパウダーサイズ
- 密度分析 - ヘリウムピクノメトリーとアルキメデス試験により、98%以上の理論密度を検証。
- 硬度試験 - ロックウェル・スケールで適切なグレードの硬度を確認
- 靭性 - 横方向の破断強度が耐衝撃性を示す。
- 真直度 - 厳しい真直度公差を満たすこと
- 表面仕上げ - SEMおよび光学検査
- 寸法公差 - CMM/光学測定による精度測定
- 微細構造 - 超硬合金の粒度と結合相分析
- 研削性能 - 切削試験による工具刃先と形状の評価
すべての工程を管理することで、高性能で信頼性の高い超硬工具を提供することができます。
超硬ブランクと超硬ソリッドのコスト分析
超硬ブランクと超硬ソリッドを比較する経済性には、以下のようなものがある:
超硬ブランク:
- 部品当たりの材料費を削減
- 製造コストの上昇は生産量で相殺された
- 研削時間と砥石コストの削減
- 製造時のスクラップ・ロスの低減
- 機械加工の体積エネルギーの1/10
ソリッドカーバイド:
- 部品当たりの材料費が高い
- プロトタイプ量産時の製造コスト低減
- 広範な研削にかかる人件費が大きい
- スクラップ・ロスの増加、未使用材料
- 工具ろう付け工程にかかる費用が不要
超硬ブランクは、通常1,000~5,000個を超えるとコスト面で有利になり、ニアネットシェイプ加工により、より経済的な工具設計が可能になる。
超硬ブランクのサプライヤーまたはメーカーの選択
カーバイドブランクサプライヤーの主な選択基準:
- 超硬粉末冶金における実証済みの専門知識
- ご希望の炭化物グレードと粒度を供給する能力
- 要件を満たす寸法精度と公差
- 要求される材料特性を達成する一貫性
- 利用可能なブランクの形状とサイズの範囲
- ユニークな工具設計のためのカスタマイズ機能
- 品質認証 - ISO 9001およびISO 14001
- コンプライアンス文書を提供する検査報告書
- アプリケーションと材料選択の技術的専門知識
- 競争力のある安定した価格と迅速な見積もり
- リードタイムを短縮するための標準サイズの在庫状況
- 試作品やサンプルのリクエストへの対応
- 大量生産の管理能力
認定された品質システムを持つ確立されたメーカーは、精密超硬ブランクに対する顧客のニーズを最も満足させる傾向がある。
超硬ブランクと代替品の長所と短所
超硬ブランクの利点
- 生産量における大幅なコスト削減
- より高い寸法精度と再現性
- 優れた表面仕上げとエッジの鋭さ
- ニアネットシェイプ製造による機械加工の削減
- より微細で均一な炭化物粒度
- より小さく、より薄い形状が可能
- 複雑な刃先交換式チップの加工がより簡単に
- 革新的な切削工具の設計が可能
- 鋳造合金では不可能な最適グレード組成
超硬ブランクの欠点:
- 初期プロセス開発および金型コストが高い
- フィーチャーとカッティング・エッジの研削がまだ必要
- 複雑な内部形状を持たない、より単純なブランクフォームに限定される。
- 超硬合金のろう付けと研削に必要な特殊工程
- 超硬ソリッド工具より格下と思われる
- 機械加工ほど材料の範囲は広くない
ほとんどの場合、商業用切削工具の生産において、経済的および性能的な利点が制限を大幅に上回る。
超硬ブランクと3Dプリント超硬の比較
パラメータ | 超硬ブランク | 3Dプリント超硬合金 |
---|---|---|
製造工程 | 粉末冶金成形と焼結 | バインダージェット印刷またはレーザー/電子ビームPBF |
材料 | コバルト・タングステングレード | 混合酸化物+バインダーまたは純タングステン |
部品サイズ | 300mmまでの寸法 | プリンタービルドチャンバーに限定 |
精度 | 非常に高い、±0.025 mm | 中程度、±0.2mm |
表面仕上げ | 素晴らしい | 可もなく不可もなく、後処理が必要 |
コスト経済学 | 中量から大量を好む | 試作品や少量生産に最適 |
生産量 | 年間最大10万人 | < 年間5,000ドル未満 |
リードタイムズ | プロセス開発期間が長い | 単発は早いがバッチは遅い |
設備投資 | 設備投資の減少 | 3Dプリンターの高コスト |
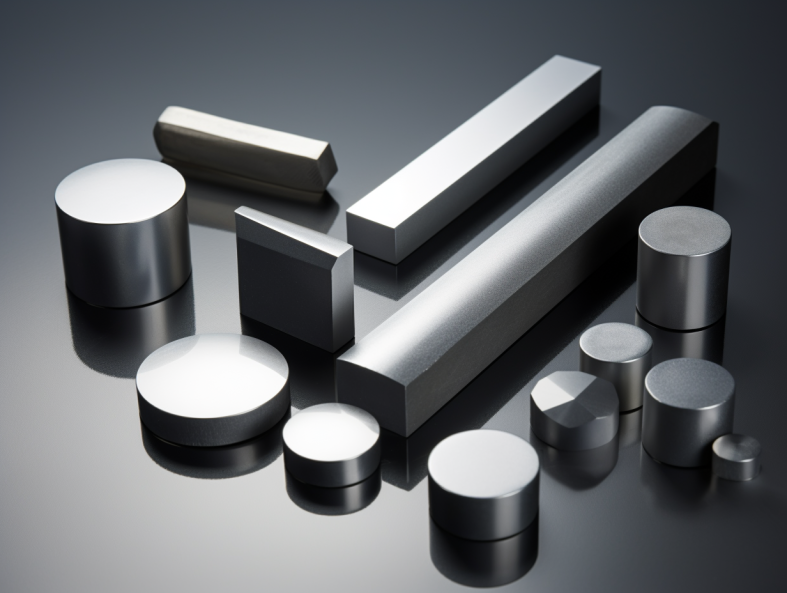
よくあるご質問
焼結カーバイドブランクの一般的な公差はどのくらいですか?
超硬ブランクは、日常的に±0.025 mm、複雑な形状では±0.05 mmまでの寸法精度を達成することができます。0.01mm以下の公差も可能ですが、より厳しい工程管理が必要となります。
超硬焼結ブランクのエッジ・チッピングのような欠陥の原因は何ですか?
過度に粗い炭化物粒子に起因する不十分な衝撃靭性と不適切なブランク研削が、その後の機械加工で超硬焼結体ブランクのエッジ欠陥が発生する最も一般的な原因である。
未完成の超硬ブランクはどのように扱い、保管すべきですか?
焼結炭化物ブランクは脆いので、衝撃や衝撃を避けるために慎重な取り扱いが必要である。ブランクのエッジを保護し、清潔で乾燥した環境で保管する必要があります。
超硬合金ブランクの最大サイズを制限するものは何ですか?
均一な加熱と焼結により、超硬ブランクの最大寸法は通常300×300×50mm程度に制限される。より大型のプレス機と炉を使用すれば、より大きなブランクを製造することができます。
超硬焼結ブランクのコストは、超硬ソリッドからの加工と比べてどうですか?
超硬ブランクが超硬ソリッドに対して費用対効果を発揮するのは、通常1000個を超えるような中・大量生産時のみです。ネットシェイプに近い均一な特性は、スケールアップ時に大きな経済的メリットをもたらします。