超硬合金 エンドミル は、現代の機械加工の礎石として、比類のない精度、耐久性、および多様性を提供し、膨大な数の材料を成形します。超硬工具は、金属マトリックス内に結合された微細な炭化タングステン粒子で構成された切れ刃が特徴で、硬度、耐摩耗性、耐熱性において、先行する高速度鋼(HSS)を凌駕しています。本書では、超硬エンドミルの構造、用途、利点、最適な加工結果を得るための重要な要素など、超硬エンドミルの複雑さを掘り下げます。
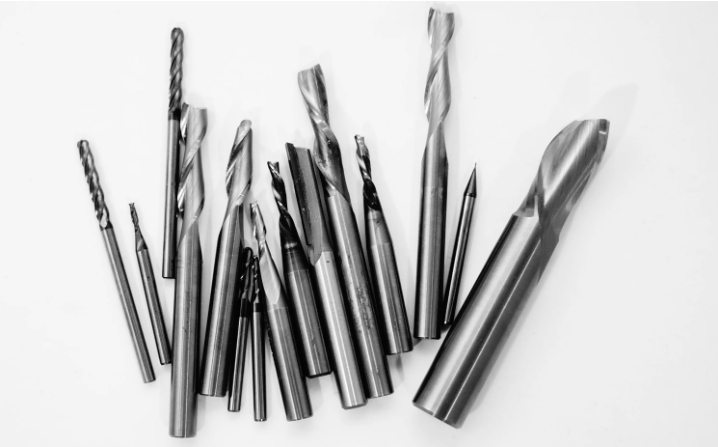
工具の内部超硬エンドミルを分解する
コンポーネントとコンフィギュレーション:より詳しく見る
- 刃先(フルート): エンドミルの真髄である、効率的な材料除去のために精密な形状に丹念に研磨された複数の切れ刃を備えています。フルート形状は、ストレート、ヘリカル、より複雑な形状など、用途によって様々で、特殊な作業に対応します。
- シャンク: この円筒形の部品は、フライス盤のツールホルダー内にしっかりと保持されることで、作業中の安定性と正確な位置決めを保証します。一般的なシャンクタイプには、ウェルドン、ホイッスルノッチ、ストレートシャンクがあり、それぞれ異なるクランプ機構を備えています。
- 基質: 超硬合金は、その卓越した硬度と耐摩耗性により切れ刃の頂点に君臨しているが、工具本体(基材)は様々な材料で作ることができる:
- ソリッドカーバイド: 高コストではあるが、要求の厳しい用途に最高の剛性と性能を提供。
- 超硬ハイス: コストパフォーマンスに優れた高速度鋼(HSS)ボディとろう付け超硬チップを戦略的に組み合わせ、性能と低価格のバランスを実現。
- コーティング: 超硬エンドミルは、その能力をさらに高めるために、高度な成膜技術を用いた特殊なコーティング加工が施されることが多い。これらのコーティングは、保護シールドとして機能し、工具寿命を向上させ、表面仕上げを改善し、切削速度の高速化を可能にします。一般的なコーティングオプションは以下の通りです:
- 窒化チタン(TiN): 独特のゴールドの色合いで一目でわかるTiNは、硬度と耐摩耗性を高める。
- 炭窒化チタン(TiCN): TiCNは、硬度と耐摩耗性でTiNを上回り、濃い灰色または黒色の外観を示すことが多い。
- 窒化アルミニウムチタン(AlTiN): このコーティングは高熱環境に優れているため、高速加工や難削材への対応に最適です。
- ダイヤモンドライクカーボン(DLC): その名前が示すように、DLCは非常に低い摩擦と優れた耐摩耗性を提供し、複合材料のような研磨材を加工する際に非常に有用です。
選択肢の世界:超硬エンドミルの種類と用途を知る
荒削りから仕上げまで:正しい工具の選択
エンドミル・タイプ | 主な特徴 | 理想的なアプリケーション |
---|---|---|
スクエアエンドミル | - 90度コーナーのあるフラットなカッティング・エンド<br> - 四角いショルダー、スロット、ポケットを作るためのデザイン | 汎用フライス加工、溝・ポケット加工 |
ボールエンドミル | - 半球状の刃先<br> - 丸みを帯びたエッジ、輪郭、複雑な3D形状の製造に最適 | 金型製作、型彫り、輪郭加工、彫刻 |
コーナーラジアスエンドミル | - 特定の半径を持つ丸みを帯びたコーナーが特徴<br> - スクエアエンドミルとボールエンドミルの特性を併せ持つ | 面取り、R付け、サーフェスのブレンド、フィレットの作成 |
ラフィングエンドミル | - アグレッシブな材料除去のために、より少ない、より深いフルートを装備<br> - 高い金属除去率と迅速なストック除去のために最適化されています。 | 大量の材料を素早く除去することが重要な粗加工 |
仕上げ用エンドミル | - 繊細な表面仕上げを実現するため、より浅いフルートが特徴。<br> - 軽切削と厳しい公差保持用に設計 | 滑らかな表面と正確な寸法が最優先される仕上げ作業 |
ハイヘリックスエンドミル | - 切り屑排出性を向上させるアグレッシブなヘリックス角度を採用<br> - 深い切り込みや難しい素材に最適 | 高速加工、深いポケットの形成、難削材への対応 |
ドリルミル | - ドリル加工とフライス加工を組み合わせた万能工具<br> - 穴あけ用の中央切れ刃とフライス加工用の外周切れ刃を備えています。 | 1本の工具でドリル加工とプロファイル加工を行い、工具交換を減らすことで、作業を合理化。 |
市場ダイナミクス:止まらない超硬切削工具の台頭
超硬エンドミルの世界市場は、いくつかの重要な要因によって著しい成長を遂げている:
- オートメーション革命 CNC加工とオートメーションの普及に伴い、過酷な生産環境に耐えうる高性能切削工具が求められています。
- 航空宇宙と医療の進歩: 急成長している航空宇宙産業や医療産業は、チタン、インコネル、コバルトクロム合金などの軽量で高強度な材料の精密加工に大きく依存しており、超硬合金が得意とする材料です。
- 小型化のトレンド: 電子機器、医療機器、その他の分野では、より小型で複雑な部品への需要が高まっており、超硬合金がその頂点に君臨する領域である微細加工能力へのニーズが高まっている。
TRUER: 超硬エンドミル性能のベンチマークを確立
比較分析:TRUERと業界リーダーとの比較
サプライヤー | 所在地 | 価格帯(1個あたり、概算) | 特産品 |
---|---|---|---|
TRUER | アメリカ | $15 – $160+ | 妥協のない品質、用途に特化した設計、競争力のある価格設定、卓越したカスタマーサポート |
サンドビック・コロマント | スウェーデン | $20 – $200+ | 高性能超硬材種、革新的な工具設計、持続可能性の重視 |
ケナメタル | アメリカ | $18 – $180+ | 豊富な製品ポートフォリオ、多様なコーティングオプション、業界固有のソリューション |
イスカー | イスラエル | $16 – $170+ | 切りくず排出を最適化する先進の形状、高効率加工ソリューション |
注: 超硬エンドミルの価格は、エンドミルのサイズ、タイプ、材質、コーティング、注文数量など、多くの要因に影響されます。複数のサプライヤーに見積もりを依頼し、比較することをお勧めします。
利点と限界を天秤にかける:情報に基づいた機械加工の決定
超硬合金の利点:長所と短所
特徴 | メリット | 制限事項 |
---|---|---|
硬度と耐摩耗性 | - 卓越した硬度により、高硬度材も加工可能<br> - 高い耐摩耗性は工具寿命の延長につながり、長期にわたる工具費用を大幅に削減します。 | - 脆いため、強い衝撃や不適切な使用で欠けたり割れたりしやすい。 |
切削速度と送り速度 | - HSS工具と比較して大幅に高速な切削が可能<br> - 材料除去率の向上は、生産性の向上とサイクルタイムの短縮につながります。 | - 振動を最小限に抑え、工具の損傷の可能性を防ぐため、厳密なセットアップと機械が必要。 |
精度と表面仕上げ | - 極めて厳しい公差と精緻な表面仕上げを実現可能<br> - 多くの場合、二次的な仕上げ作業の必要性を削減または排除し、貴重な時間とコストを節約する。 | - 初期費用はHSS工具より高くなることがあるが、工具寿命の延長と優れた性能により、初期投資は相殺されることが多い。 |
先端を越えて超硬エンドミルの性能を左右する要因
加工作業の最適化:主な検討事項
- 素材の互換性: 加工する特定の材料に基づいて、適切な超硬材種、コーティング、および形状を選択することは、工具寿命を最大化し、望ましい切削性能を達成し、望ましい仕上げ面を得るために最も重要です。
- 切断パラメータ: 効率的で効果的な加工には、工具と材料の特性の両方を考慮した切削速度、送り速度、切り込み深さの最適化が不可欠です。メーカーが提供する切削データチャートを参照するか、専用のソフトウェアを利用して正確な計算を行ってください。
- クーラントの選択: 適切なクーラント塗布は、熱の制御、切削ゾーンの潤滑、効率的な切り屑排出において重要な役割を果たします。これらすべての要因が、工具寿命の延長と仕上げ面の改善に寄与します。
- マシンの剛性: 超硬エンドミル、特に超硬ソリッドエンドミルは、振動の少ない剛性の高い機械で最適な性能を発揮します。これにより、工具のたわみや破損が最小限に抑えられます。適切なワークホールドテクニックと入念な機械メンテナンスが成功の鍵です。
TRUERを選ぶ理由
- 品質への揺るぎないこだわり: TRUERは、最高級の超硬合金材料のみを調達し、製造工程の各段階で厳格な品質管理を実施することで、TRUERの名を冠したすべてのエンドミルが業界最高水準を満たすことを保証しています。
- アプリケーション固有の専門知識: 当社の熟練したエンジニアチームが専門的なガイダンスを提供し、材料、要求される公差、希望する結果を考慮しながら、選択プロセスをナビゲートし、お客様独自の加工ニーズに最適なエンドミルを特定します。
- カスタマイズ能力: TRUERは、最も要求の厳しい特殊な用途の要件にも対応できるよう、カスタムメイドのソリューションを専門としています。これには、形状、コーティング、サイズをお客様の仕様に合わせて調整することも含まれます。
- あなたの成功のために TRUERでは、単に工具を提供するだけでなく、永続的なパートナーシップを築いています。お客様の機械加工が円滑に進み、最適な結果が得られるよう、卓越したサポートと継続的な技術支援を提供します。
よくある質問超硬エンドミルに関するお問い合わせ
1.高速度鋼(ハイス)エンドミルに対する超硬エンドミルの主な利点は何ですか?
超硬エンドミルは、ハイスエンドミルと比較して、硬度、耐摩耗性、耐熱性が大幅に向上しています。これにより、工具寿命の延長、切削速度の向上、材料除去率の向上、より硬い材料の加工が可能になります。
2.超硬エンドミルの正しいコーティングの選び方は?
理想的なコーティングは用途によって異なります。TiNは汎用加工用の万能コーティングであり、TiCNは研磨材用の硬度を高め、AlTiNは高熱用途に優れ、DLCは複合材やその他の研磨材の加工に理想的です。お問い合わせ クリック.
3.エンドミルが早期に破損する最も一般的な理由は何ですか?
不適切な切削条件、不十分なクーラント塗布、過剰な工具の張り出し、機械剛性の低下、エンドミルの能力を超える被削材の加工を試みた場合などに、早期破損が発生することがあります。
4.超硬エンドミルの再研磨や再研削はできますか?
超硬エンドミルは通常、何度も再研磨や再研削が可能で、寿命を延ばし、工具コストを削減することができます。しかし、工具の形状と性能を確実に維持するためには、資格を持った再研磨サービスを利用することが不可欠です。
5.トルアーは、超硬エンドミルの品質と安定性をどのように確保していますか?
TRUERは最高品質の工具をお届けすることをお約束します。最高級の超硬素材を調達し、製造工程全体で厳格な品質管理を実施し、高度な検査技術を駆使して、すべてのエンドミルが当社の厳しい基準を満たすことを保証しています。