超硬ロッドとは?
超硬棒 は、タングステンと炭素原子が結合してできた化合物である炭化タングステン(WC)を主成分とする円柱状の棒です。これらの棒は、その卓越した硬度と耐摩耗性で有名で、切削工具の製造に理想的です。製造プロセスには粉末冶金が用いられ、炭化タングステン粉末を結合剤(通常はコバルト)と混合し、焼結して高密度の固形ロッドを形成する。この方法は、組成と特性の均一性を保証し、高速加工や切削作業の厳しさに耐えることができる材料になります。
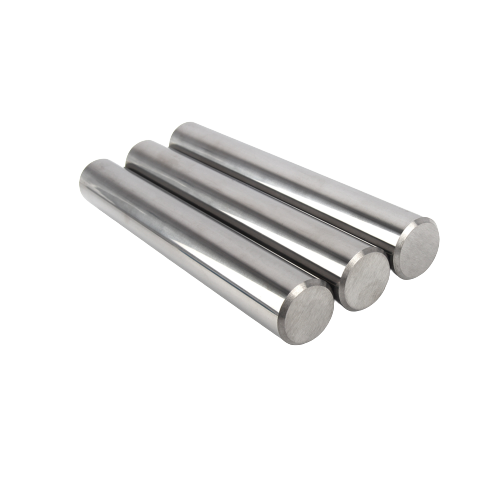
切削工具インサートで材料が重要な理由
切削工具チップの材料の選択は、工具の性能と寿命にとって非常に重要である。超硬ロッドは、その優れた硬度と耐熱性により、他の材料に比べて切削速度と送り速度を上げることができます。これは、機械加工の生産性と効率の向上につながります。さらに、鋭い切れ刃を維持する超硬の能力は、工具交換の頻度を減らし、ダウンタイムと運用コストを最小限に抑えます。
使用するメリット 超硬棒
1.卓越した硬度と耐摩耗性: 超硬ロッドは、ダイヤモンドに次ぐ硬度を示し、硬い材料を容易に切断し、長期間の摩耗に耐える。
2.高い熱安定性: 切削加工中に発生する高温にも硬度を失うことなく耐えることができ、安定した性能を発揮する。
3.表面仕上げの向上: 超硬工具の剛性と切れ味は、加工部品の表面仕上げをより滑らかにし、二次加工の必要性を減らす。
4.汎用性: 鋼鉄、鋳鉄、非鉄金属、超合金など幅広い材料に適している。
5.費用対効果: 初期費用は高くつくが、工具寿命の延長とダウンタイムの短縮により、全体的なコスト削減につながる。

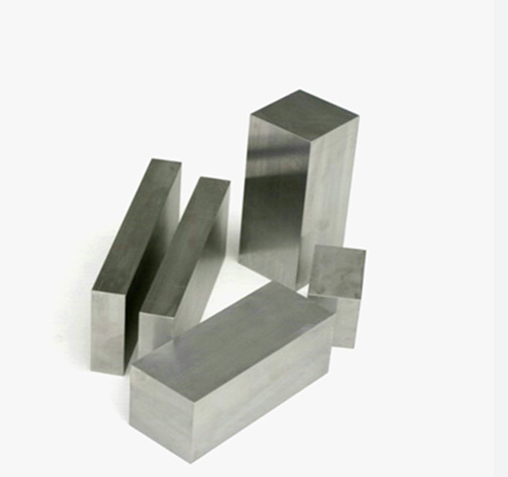
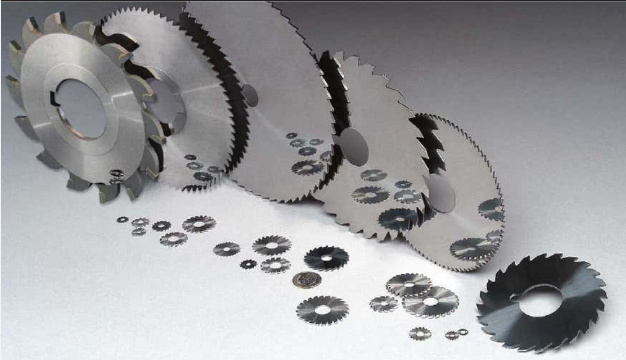
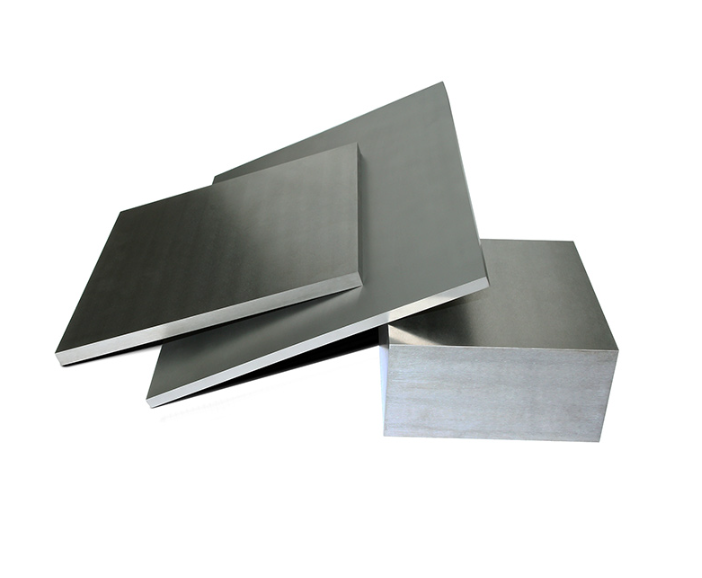
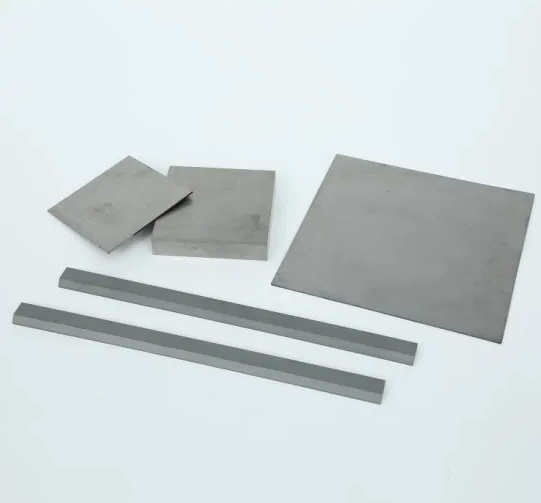
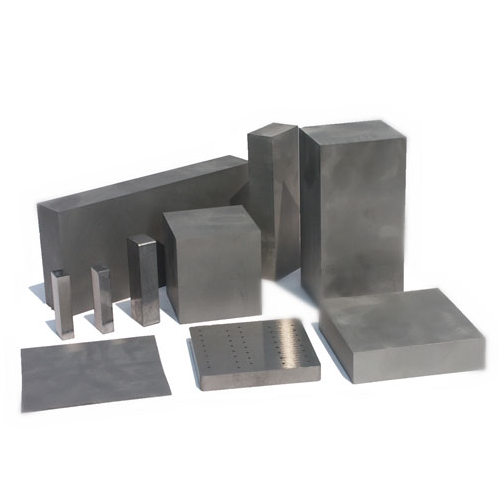
他の素材との比較
プロパティ | 超硬棒 | 高速度鋼(HSS) | セラミックス | サーメット |
---|---|---|---|---|
硬度 | 非常に高い | 中程度 | 高い | 高い |
タフネス | 中程度 | 高い | 低い | 中程度 |
耐摩耗性 | 素晴らしい | グッド | 素晴らしい | 非常に良い |
熱抵抗 | 高い | 中程度 | 非常に高い | 高い |
コスト | より高い | より低い | 高い | 中程度 |
アプリケーション | 一般機械加工、硬質材料 | 汎用、より柔らかい素材 | 高速仕上げ | 仕上げ、軽い荒削り |
超硬インサートの一般的な用途
超硬チップは、その耐久性と効率性により、さまざまな産業で利用されています:
- 自動車産業: エンジン部品、トランスミッション部品、その他精密さと耐摩耗性が要求される重要部品の加工用。
- 航空宇宙産業: タービンブレード、構造部品、その他難削材部品の製造に使用。
- 金属加工: さまざまな金属の旋盤加工、フライス加工、ドリル加工、ねじ切り加工に最適。
- 木工: 木製品の成形や仕上げ用の切削工具に使用される。
- 医療機器製造: 高い精度と生体適合性が要求される手術器具やインプラントの製造に。
超硬インサートとハイスインサートの違いは?
超硬インサート:
- 硬度: HSSよりもかなり硬いため、高速切削が可能。
- 耐摩耗性: 優れた耐摩耗性により、工具寿命が延びる。
- 熱抵抗: 硬度を失うことなく高温に耐えることができる。
- コストだ: 初期コストは高いが、耐久性に優れ、長期的には費用対効果が高い。
HSSインサート:
- タフネス: 延性が高く、断続的な切断でも欠けにくい。
- エッジの鋭さ: よりシャープなエッジに研磨でき、特定の用途に有効。
- コストだ: イニシャルコストが低く、少量生産やそれほど要求の高くない業務に適している。
- 汎用性がある: 再研磨が容易で、カスタム・アプリケーション用に修正しやすい。
特定の金属粉末モデル 超硬棒
適切な金属粉末モデルを選択することは、超硬ロッドにおいて望ましい性能特性を達成するために極めて重要である。以下は具体的なモデルのリストです:
- YG6だ: 6%コバルトを含有し、優れた硬度と耐摩耗性を提供。一般加工に最適。
- YG8だ: 8%のコバルトを使用し、硬度と靭性のバランスが取れており、採掘や掘削用途に適している。
- YG10: 10%コバルトを含有し、靭性を向上。高精度を要求される切削工具に使用される。
- YG15: 15%コバルトを使用し、靭性と耐久性を向上。重切削や摩耗部品に最適。
- YW1: 炭化タングステンとコバルトを配合した万能材種で、優れた耐摩耗性と靭性を発揮。
- YW2だ: YW1に似ているが、コバルト含有量がやや高く、靭性が向上している。
- K10: 精密機械加工や切削工具に最適な微粒タングステンカーバイド。
- C2: 汎用用途で知られ、耐摩耗性と衝撃強度に優れている。
- C3: C2に似ているが耐摩耗性が高く、非鉄および非金属材料に使用される。
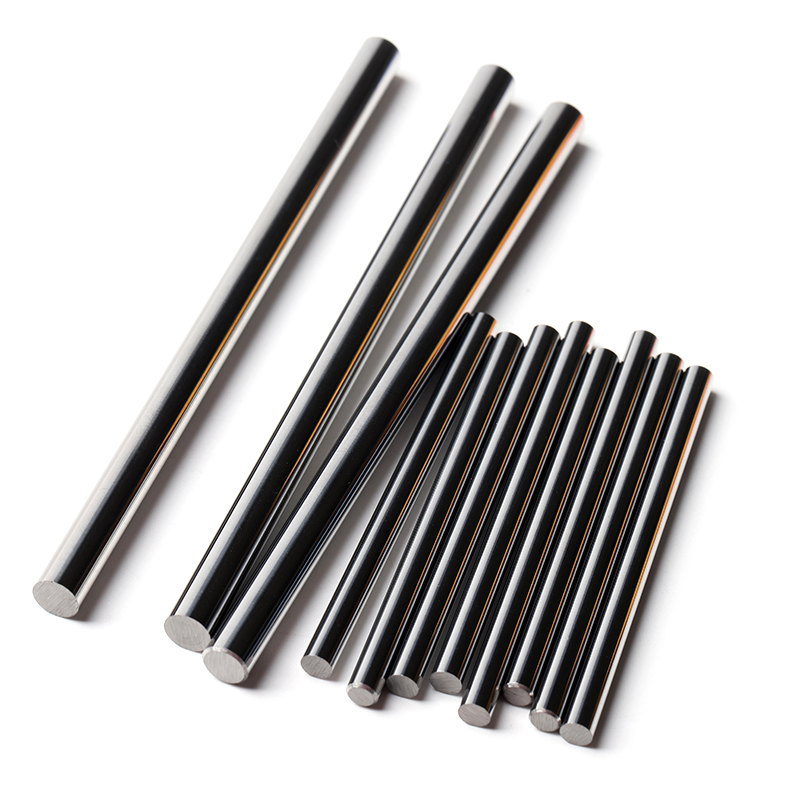
よくあるご質問
質問 | 回答 |
---|---|
超硬ロッドが切削工具インサートとして優れている理由は何ですか? | その卓越した硬度、耐摩耗性、熱安定性により、切削速度の高速化と工具寿命の延長が可能になります。 |
超硬ロッドは費用対効果が高いのか? | そう、初期コストは高いものの、耐久性が高いため交換頻度が減り、長期的な節約につながるのだ。 |
超硬ロッドはすべての材料に使用できますか? | 硬質金属や複合材など、幅広い素材に対応する汎用性の高い製品だ。 |
超硬ロッドの性能はハイスと比較してどうですか? | 超硬ロッドは硬度と耐摩耗性が高く、より高速な加工と優れた表面仕上げが可能です。 |
超硬ロッドを使うことの限界は何ですか? | ハイスよりも脆く、特定の条件下では欠けやすくなる。 |
超硬工具の再研磨は可能ですか? | そうだが、硬いので専用の器具が必要だ。 |
どのような産業が超硬棒の恩恵を最も受けているか? | 自動車、航空宇宙、金属加工、医療機器製造などの業界では、超硬工具が広く使用されている。 |
超硬ロッドは特別な取り扱いが必要ですか? | そうですね、脆いので、欠けたり割れたりしないように慎重に扱う必要があります。 |
超硬ロッドには等級がありますか? | そう、YG6、YG8、K10といったさまざまなグレードが、特定の用途や性能要件に対応している。 |
バインダーの含有量は超硬棒の特性にどのような影響を与えますか? | コバルト含有量が高いほど靭性は向上するが、硬度が低下し、耐摩耗性に影響する可能性がある。 |