When it comes to high-performance cutting tools, carbide rods are an industry staple. But have you ever wondered how these small but mighty materials come to life? In this article, we’ll take a deep dive into the fascinating carbide rod manufacturing process. From preparing raw materials to quality inspection, we’ll break down each stage in a conversational tone that’s easy to follow and loaded with insights. So, let’s get started!
Preparation of Raw Materials for the Carbide Rod Manufacturing Process
Think of carbide rods as the superheroes of machining tools—strong, durable, and capable of performing under extreme conditions. But even superheroes need the right foundation. This journey begins with the careful preparation of raw materials.
The primary ingredients are 炭化タングステン(WC) powder and a metallic binder, typically cobalt. Tungsten carbide is prized for its hardness and wear resistance, while cobalt binds the particles together. Both are meticulously sourced to meet strict quality requirements because, as they say, garbage in, garbage out.
- Mixing the Ingredients:
The tungsten carbide and cobalt powders are mixed to create a homogeneous blend. This step often involves ball milling—a process where the powders are tumbled with hard balls in a rotating drum to ensure uniformity. Picture kneading dough for bread but on an industrial scale. - Particle Size Control:
The particle size of tungsten carbide is crucial. Smaller grains lead to harder materials, while larger grains enhance toughness. Balancing these properties is like fine-tuning a guitar—precision is key. - Binder Distribution:
The cobalt must evenly coat the tungsten carbide particles for optimal bonding. Specialized additives and processes ensure this critical step is spot on.
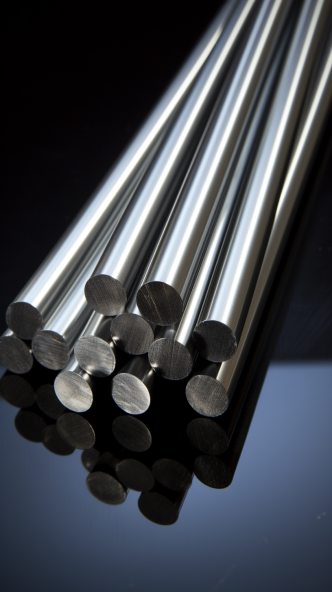
Pre-Sintering in the 超硬棒製造工程
Pre-sintering is like baking a cake halfway—it prepares the “dough” for the final sintering process. Here’s a detailed breakdown:
パラメータ | 説明 |
---|---|
目的 | Removes excess moisture and partially bonds the particles. |
Temperature Range | 400°C to 800°C, depending on the material composition. |
Duration | Typically 1-2 hours, ensuring sufficient material densification. |
Atmosphere | Performed in a controlled environment, often using an inert gas like argon to prevent oxidation. |
Pre-sintering enhances the structural integrity of the material, making it easier to handle during subsequent processes. Imagine building a sandcastle—you want the sand to stick together but not harden completely just yet.
Pressing or Extrusion in the Carbide Rod Manufacturing Process
Once the materials are ready, it’s time to shape them into rods. This stage involves either pressing または extrusion.
- プレス:
Powdered material is placed into a die and compressed under high pressure. This method is excellent for achieving consistent density across the rod. - 押出:
The powder mix is first converted into a slurry and then forced through a die to create long, continuous rods. This process is like squeezing toothpaste out of a tube—smooth, efficient, and ideal for larger production runs.
Key Factors in Shaping:
ファクター | プレス | 押出 |
---|---|---|
Output Shape | Limited to simpler designs. | Capable of complex and variable designs. |
Tool Wear | Minimal due to dry pressing. | Higher due to the slurry’s abrasiveness. |
生産量 | Suitable for small to medium volumes. | Preferred for large-scale production. |
Sintering of Carbide Rods
Sintering is the grand finale where all the magic happens. The material is heated to near-melting temperatures, causing the tungsten carbide and cobalt to fuse into a dense, solid structure.
パラメータ | 詳細 |
---|---|
Temperature Range | 1,300°C to 1,600°C |
Atmosphere | Often performed in a vacuum or with hydrogen to prevent contamination. |
Duration | Can last from several hours to a full day, depending on rod size and composition. |
Outcome | Achieves maximum density, hardness, and wear resistance. |
This process is like forging a sword—it requires extreme heat, precise control, and expert timing.
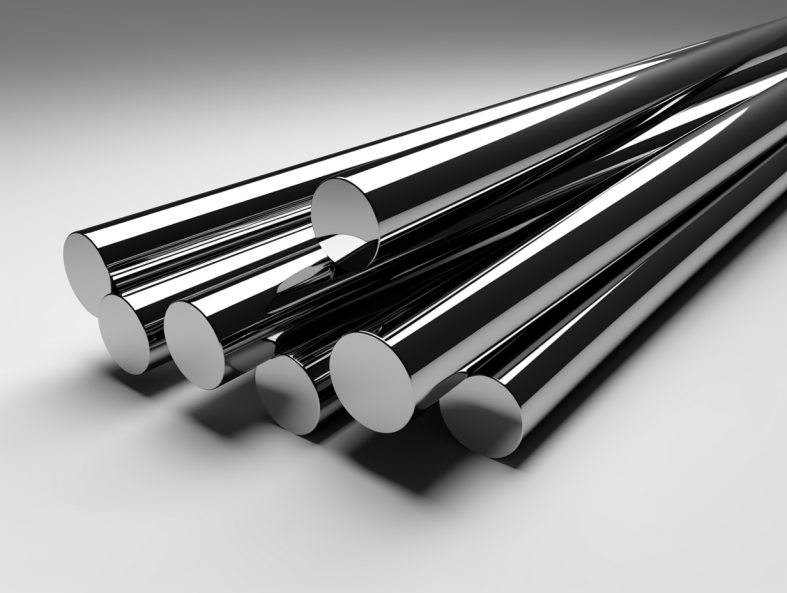
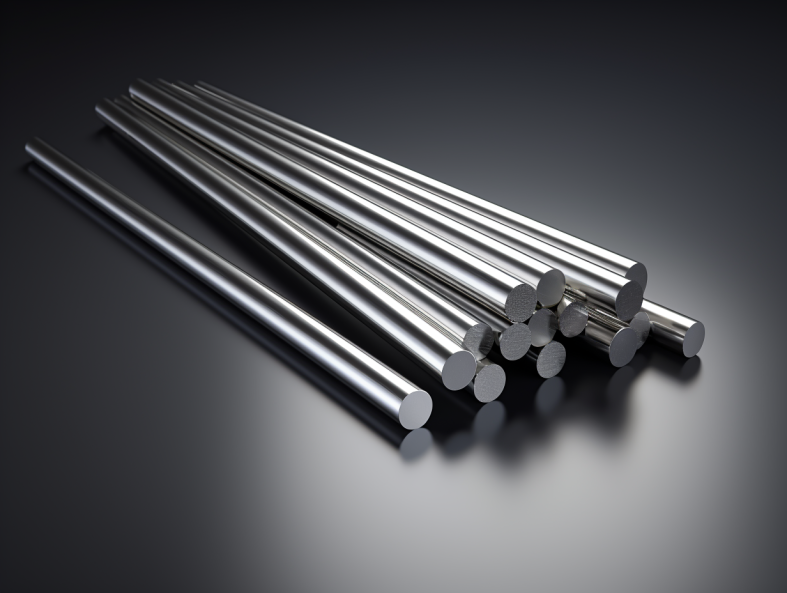
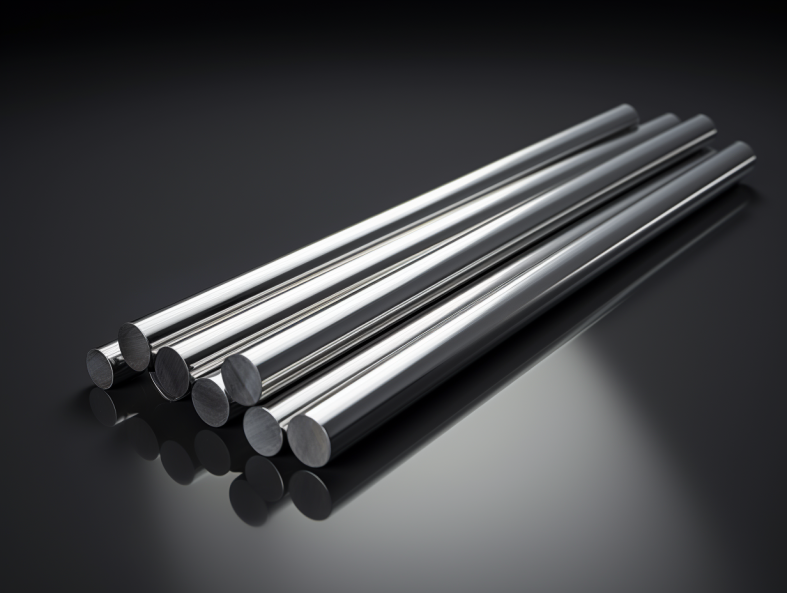
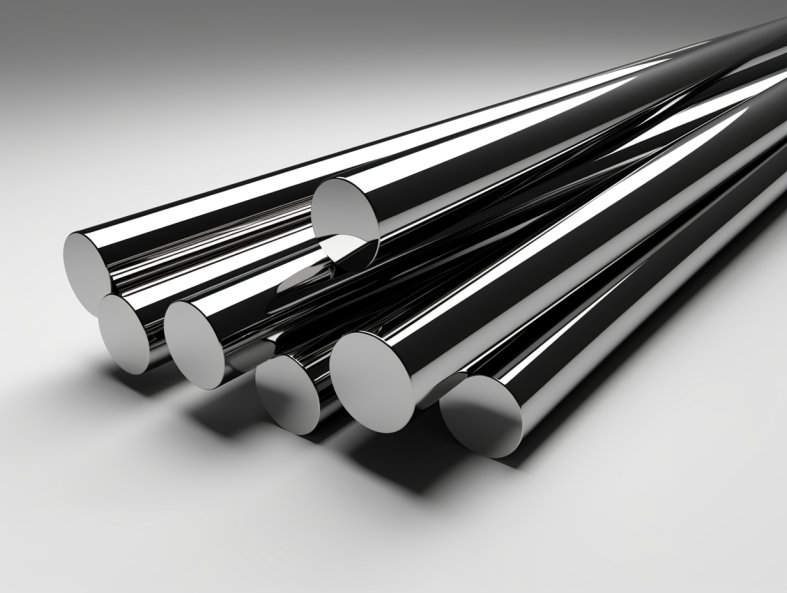
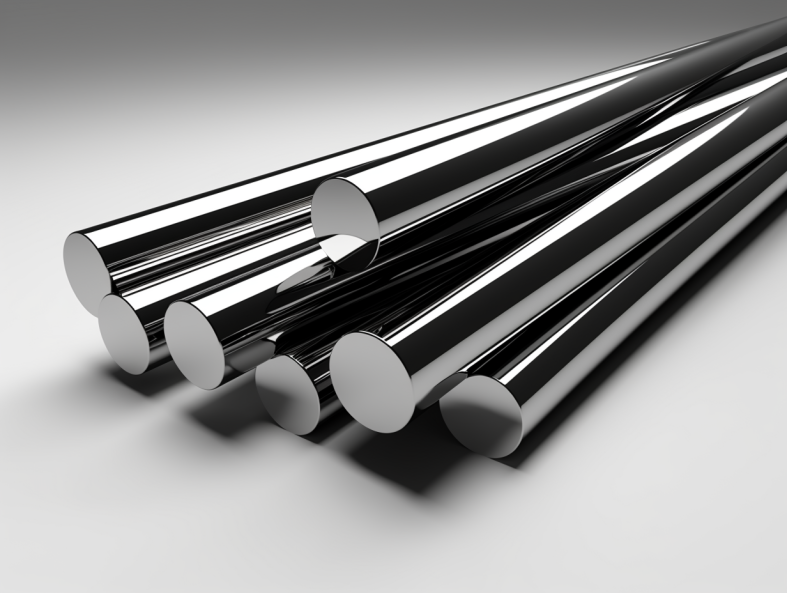
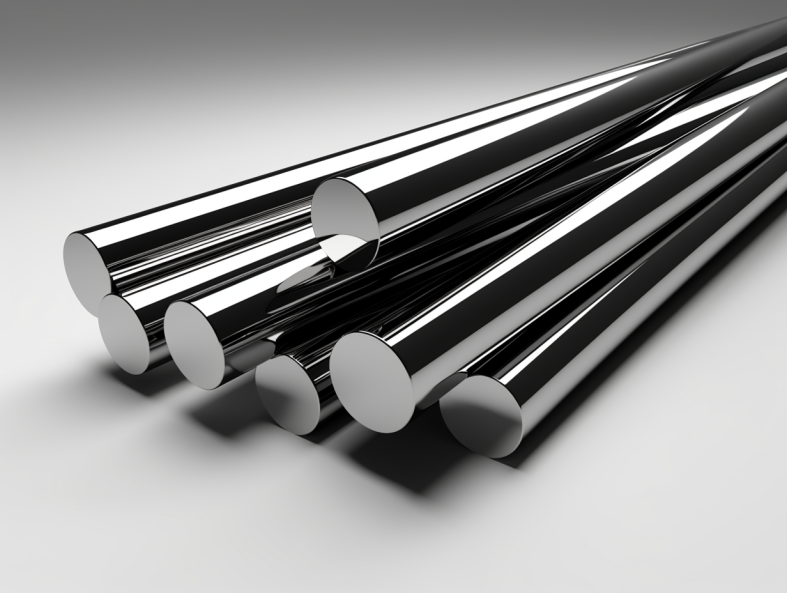
Continuing Processing After the 超硬棒製造工程
After sintering, the carbide rods are far from ready for end use. Continuing processing ensures they meet exacting specifications.
ステップ | 目的 |
---|---|
研磨 | Refines dimensions and surface finishes, ensuring rods meet tight tolerances. |
研磨 | Enhances the surface quality, reducing friction during use. |
コーティング | Often, rods are coated with materials like titanium nitride to boost performance. |
カッティング | Rods may be cut into shorter lengths to suit specific applications. |
Each of these steps is critical. Think of it as turning a rough diamond into a sparkling gem.
Quality Inspection of Carbide Rod Manufacturing Process
Quality control is the backbone of any manufacturing process, and carbide rods are no exception. Every rod undergoes rigorous testing before it’s deemed ready for market.
- 寸法精度:
Tools like micrometers and coordinate measuring machines (CMMs) ensure that rods meet exact size specifications. A deviation as small as a hair’s width could render a rod unusable. - 硬度試験:
Devices like Rockwell or Vickers hardness testers measure the rod’s resistance to deformation. - Defect Detection:
Non-destructive testing methods, such as ultrasonic or X-ray analysis, are used to identify internal flaws without damaging the rod. - Performance Testing:
Sample rods are subjected to real-world conditions to verify their durability and functionality.
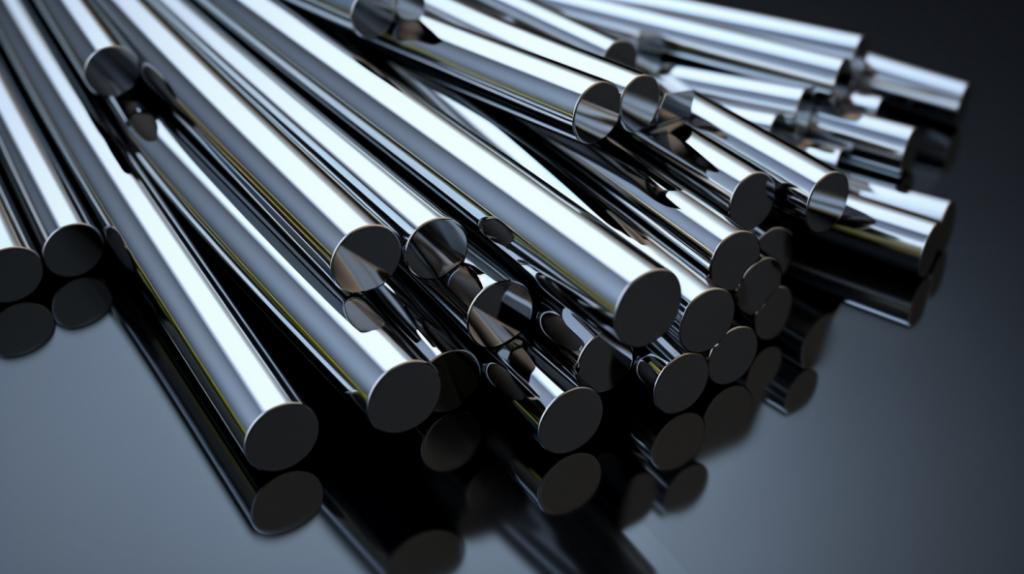
よくあるご質問
質問 | 回答 |
---|---|
超硬棒は何に使うのですか? | They are used to manufacture cutting tools, drills, end mills, and wear-resistant parts. |
How is tungsten carbide powder made? | It’s produced by combining tungsten metal with carbon at high temperatures in a controlled atmosphere. |
What makes carbide rods so durable? | Their unique combination of tungsten carbide and cobalt creates a material that’s both hard and tough. |
超硬ロッドはリサイクルできますか? | Yes, they can be reclaimed and reprocessed, reducing waste and environmental impact. |
How does extrusion compare to pressing? | Extrusion is better for complex shapes and large volumes, while pressing is ideal for simpler designs. |
結論
について carbide rod manufacturing process is a symphony of science, engineering, and craftsmanship. From carefully prepared raw materials to rigorous quality checks, every step contributes to creating a product that’s nothing short of extraordinary. Whether you’re a machinist, engineer, or just a curious mind, understanding this process sheds light on why carbide rods are the unsung heroes of the manufacturing world. So next time you see a cutting tool in action, you’ll know the incredible journey it took to get there.