何であるか 超硬棒 硬さ?
超硬ロッドは、切削工具、摩耗部品、工業用途に不可欠な部品です。その硬度は、耐久性、耐摩耗性、総合的な性能を決定します。しかし、超硬ロッドの硬度とは一体何なのでしょうか?簡単に言えば、硬度とは材料の変形、ひっかき、貫通に対する抵抗力のことです。超硬ロッドで一般的に使用されるタングステンカーバイドは、タングステンと炭素原子が結合し、緻密な結晶構造を形成するという独自の組成により、高い硬度を実現しています。
超硬ロッドの硬度は、その切削性能、寿命、高ストレス環境に耐える能力に影響を与えます。しかし、硬度だけが要因ではなく、靭性も重要な役割を果たします。硬度と靭性のバランスにより、超硬ロッドは応力下で脆くなりすぎることはありません。
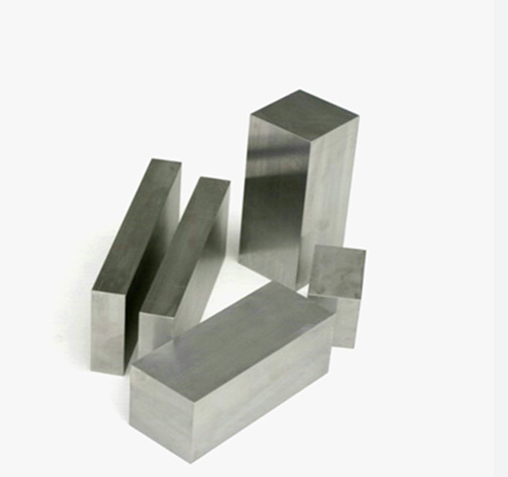
一般的な硬度スケール 超硬棒
超硬合金の硬度は、試験方法によって異なるスケールを使用して測定されます。最も一般的なものは以下の通り:
ロックウェル硬度(HRA、HRB、HRC)
- 主に金属の硬度に使用される。
- HRAはタングステンカーバイドによく使用される。
- HRCは焼き入れ鋼により多く適用される。
ビッカース硬度(HV)
- ダイヤモンドのピラミッドを利用して硬度を測定。
- カーバイドのような微細な材料によく使用される。
モース硬度
- 素材を1(タルク)から10(ダイヤモンド)までランク付け。
- タングステンカーバイドは通常9点前後。
ヌープ硬度(HK)
- 薄い材料の微小硬さ試験に使用。
各スケールには利点があるが、超硬棒の場合、ロックウェル(HRA)とビッカース(HV)が最も適切である。
超硬合金グレードとその硬度
超硬合金の等級は、コバルト含有量、粒度、追加合金元素によって異なります。以下は、一般的な超硬合金の等級とその硬度の内訳です:
超硬グレード | 構成 | ロックウェル硬度(HRA) | ビッカース硬度(HV) | アプリケーション |
---|---|---|---|---|
YG6 | 94% WC、6% Co | 90.5 | 1450 | 汎用加工 |
YG8 | 92% WC、8% Co | 89.5 | 1350 | 頑丈なカッティング |
YG10 | 90% WC、10% Co | 88.5 | 1300 | 耐衝撃アプリケーション |
YG15 | 85% WC、15% Co | 86.0 | 1100 | インパクトの強い用途 |
YL10.2 | 細粒WC、10% Co | 92.5 | 1600 | 高い耐摩耗性 |
K10 | 94% WC、6% Co | 91.0 | 1500 | 精密機械加工 |
K20 | 92% WC、8% Co | 89.5 | 1400 | 汎用切断 |
K30 | 90% WC、10% Co | 88.0 | 1300 | 粗加工 |
G10 | 極細WC、10% Co | 93.0 | 1650 | 高精度工具 |
C2 | 93% WC、7% Co | 90.0 | 1450 | 耐摩耗部品 |
コバルト含有量が低ければ硬度が増し、高ければ靭性が増す。
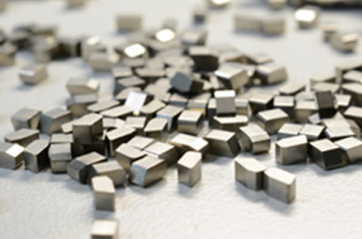
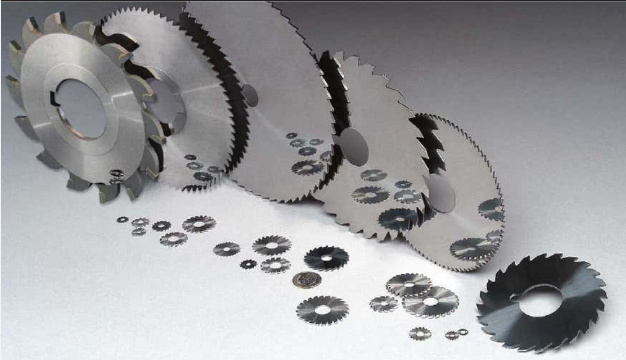
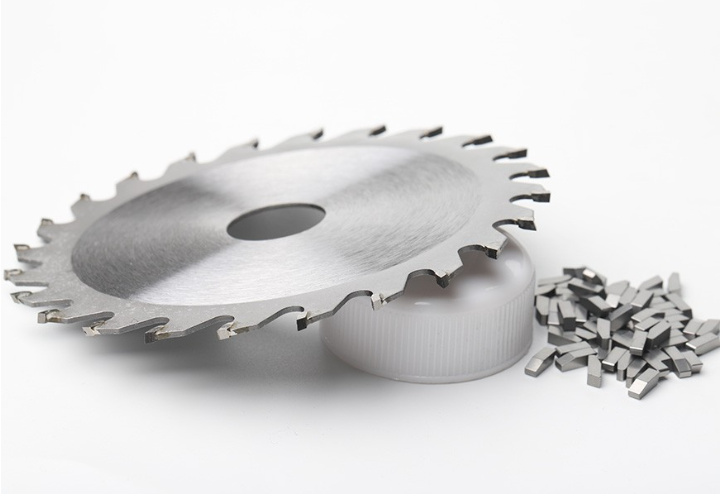
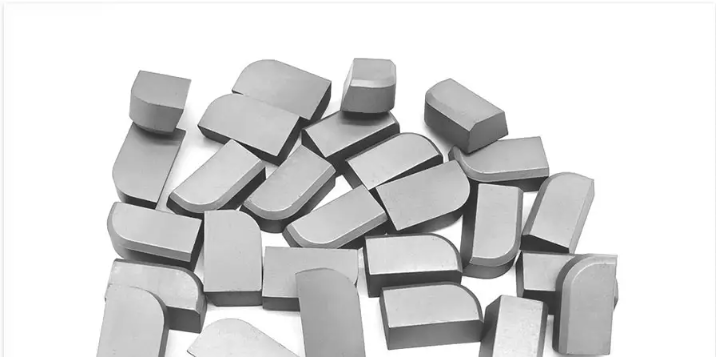
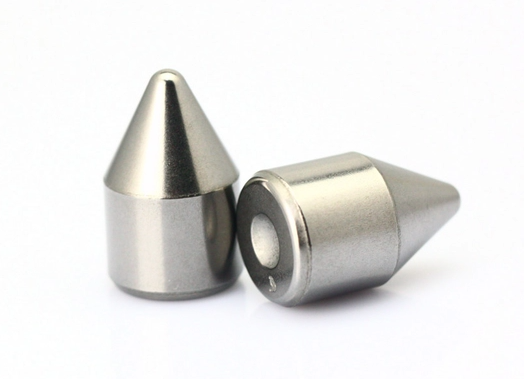
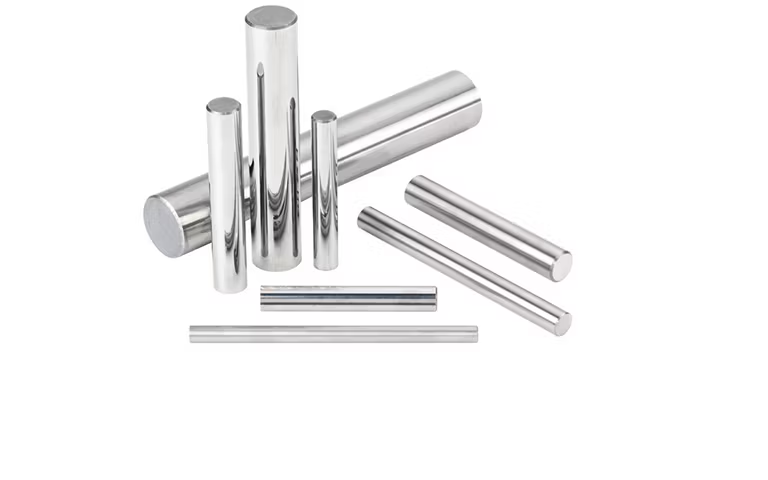
硬さとタフネス:どちらが重要か?
ファクター | 高硬度 | 高い靭性 |
---|---|---|
耐摩耗性 | 素晴らしい | 中程度 |
耐衝撃性 | 低い | 高い |
最先端のリテンション | スーペリア | 中程度 |
耐破壊性 | 低い | 素晴らしい |
代表的なアプリケーション | 精密機械加工 | ヘビーデューティー用途 |
高硬度の超硬ロッドは、摩耗が激しい用途では長持ちするが、衝撃で欠けることがある。逆に、靭性の高いロッドは折れにくいが、摩耗が早い場合がある。
正しい選び方 超硬棒 硬さに基づくか?
適切な超硬ロッドの選択は、用途のニーズによって異なります。以下を参考にしてください:
申し込み | 推奨硬度 | 最高の超硬材種 |
---|---|---|
高速切断 | 90歳以上のHRA | YG6、K10、G10 |
重切削加工 | 88-90 HRA | YG8、YG10、K20 |
耐衝撃工具 | 85-88 HRA | YG15, K30 |
精密工具 | 92+ HRA | YL10.2, G10 |
耐摩耗部品 | 90-93 HRA | C2, YG6, K10 |
硬度が高いほど耐摩耗性に優れ、硬度が低いほど衝撃用途に適した靭性が得られる。

よくあるご質問
質問 | 回答 |
---|---|
最も硬い超硬棒は? | 通常、G10やYL10.2のような超微粒子超硬ロッドの硬度が最も高い。 |
超硬合金の硬度は鋼と比較してどうですか? | 超硬合金は鋼鉄よりもかなり硬く、HRC 65を超えることが多い。 |
硬度が高ければ性能も良いのか? | 硬度が高いほど耐摩耗性は向上するが、衝撃強度は低下する。 |
超硬棒の硬度はどのように測定できますか? | ロックウェル試験(HRA)またはビッカース試験(HV)が一般的に用いられる。 |
何が超硬合金の硬度に影響するのか? | 粒径、コバルト含有量、焼結プロセスはすべて硬度に影響する。 |
高衝撃用途に最適な超硬材種は? | YG15とK30は、耐衝撃性により高い靭性を提供する。 |
超硬ロッドは削れますか? | はい、しかし特殊なダイヤモンド研磨が必要です。 |