超硬棒 は、工具、金型、さまざまなエンジニアリング用途の主要部品として、多くの産業で基本的な役割を果たしている。しかし、その性能は、表面に施される仕上げ加工に大きく左右されます。なぜこれが重要なのか?表面仕上げは、ロッドの耐久性、耐摩耗性、および全体的な機能性を最適化します。これは、航空宇宙、自動車、医療機器製造などの精密主導型産業にとって不可欠な特性です。
この記事では、超硬ロッドの表面仕上げの複雑さを詳細に分けながら掘り下げていきます。これらの工程がどのように超硬ロッドを高性能部品に磨き上げるのかを明らかにしましょう!
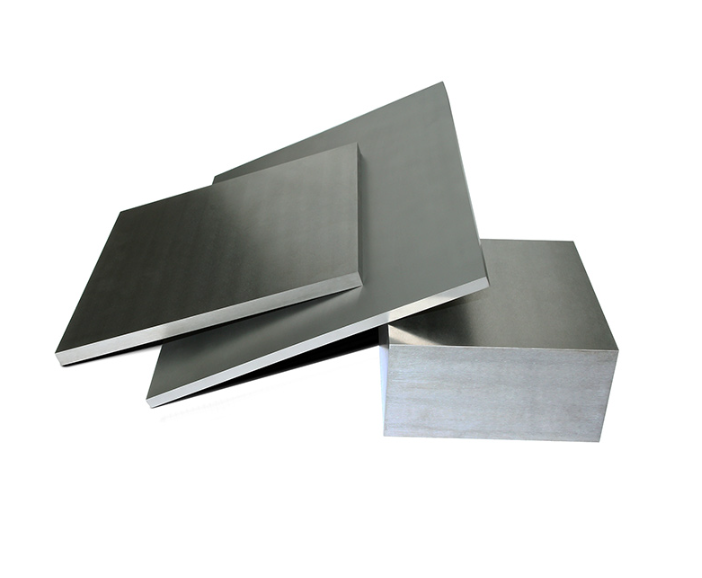
超硬棒の表面仕上げとは?
超硬ロッドの表面仕上げは、超硬材料の表面特性を向上させるために使用される一連のプロセスを指します。単なる研磨にとどまらず、硬度を向上させ、摩擦を減らし、指定されたテクスチャーや光沢レベルを達成する技術が含まれます。普通の超硬棒を、精度と耐久性に最適化された工具に変えるのです。
表面仕上げにはいくつかの目的がある:
- 耐久性の向上:耐摩耗性を高め、部品の寿命を延ばす。
- 摩擦の低減:より滑らかな表面は、エネルギー損失を最小限に抑え、工具をより効率的にする。
- 美観の向上:注目度の高い環境で使用されるツールには、完璧な仕上げがプロフェッショナリズムを演出します。
- 接着性の向上:コーティングのような用途では、よく準備された表面がより良い密着性と性能を保証する。
しかし、これらのプロセスはどのように機能するのだろうか?それは、表面仕上げに採用されている技術に行き着く。
共通 超硬棒 表面処理技術
超硬ロッドの表面仕上げにはさまざまな方法があり、それぞれが特定の要件を満たすように調整されています。ここでは、最も一般的な技術の概要を説明します:
1.研磨
研削は基礎技術のひとつである。研磨砥石を使用し、この工程で材料を除去することで、望ましい寸法と滑らかさを実現します。精密工具で完璧を削り出すようなものだ。
- 長所:高精度で複雑な形状に有効。
- 短所:大規模なオペレーションには時間とコストがかかる。
2.研磨
研磨は研削をさらに一歩進めたものです。微細な砥粒を使用することで、鏡のような仕上がりを実現し、表面の粗さを最小限に抑えます。超平滑な表面を必要とする用途では、最高の仕上げとなります。
- アプリケーション:精密工具、手術器具
- メリット:美観の向上と摩擦の低減。
3.サンドブラスト
この技法は、研磨材の高速ストリームを使用して、表面のクリーニングやテクスチャー加工を行う。不完全な部分を均等にする、マイクロスケールの浸食プロセスと考えてください。
- 主な利点:コーティング前処理に有効。
4.化学エッチング
制御された化学的プロセスであるエッチングは、性能を向上させるために超硬合金の表面を変化させる。これは、素材の能力を向上させるために化学的な改造を施すようなものである。
- メリット:精密なコントロール、複雑なパターンに最適。
- 欠点:化学物質の取り扱いに注意が必要。
5.電気めっき
電気メッキは、超硬ロッドに金属コーティングを施し、耐食性と耐久性を高めます。工具の装甲のアップグレードとお考えください。
- 使用金属:用途に応じて、ニッケル、クロム、金。
6.ダイヤモンド・コーティング
この高度な技術により、表面にダイヤモンド粒子の薄い層が形成され、硬度と耐摩耗性が飛躍的に向上します。文字通り、工具のエッジをダイヤモンドで固めるようなものです!
- 一般的な使い方:高性能切削工具。
- 制限事項:コストがかかり、専門的な設備が必要。
7.蒸着(PVD/CVD)
物理的気相成長法(PVD)と化学的気相成長法(CVD)では、超硬棒の表面に薄膜を蒸着させる。これらの薄膜は硬度を高め、摩擦を減らし、耐酸化性を向上させます。
- 人気のコーティング:窒化チタン(TiN)、酸化アルミニウム(Al2O3)。
8.ラッピング
精密な表面仕上げ工程であるラッピングは、砥粒のスラリーを使用して極めて厳しい公差を達成する。
- 主なメリット:平面と厳しい寸法精度に最適。
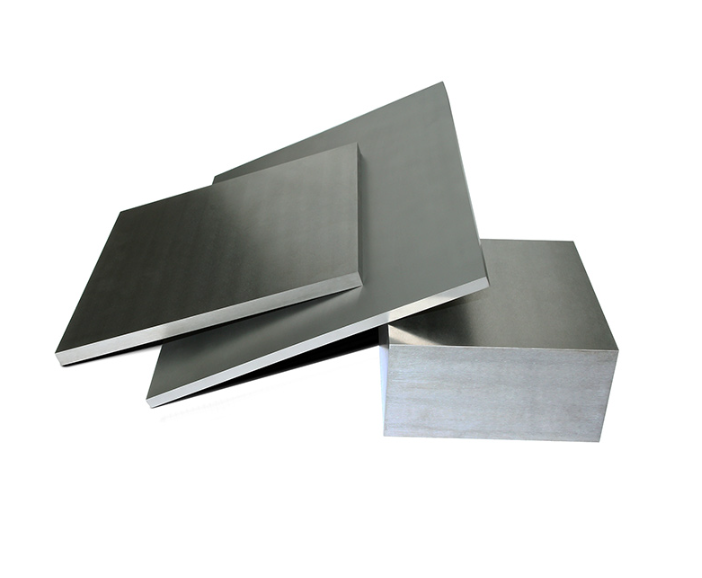
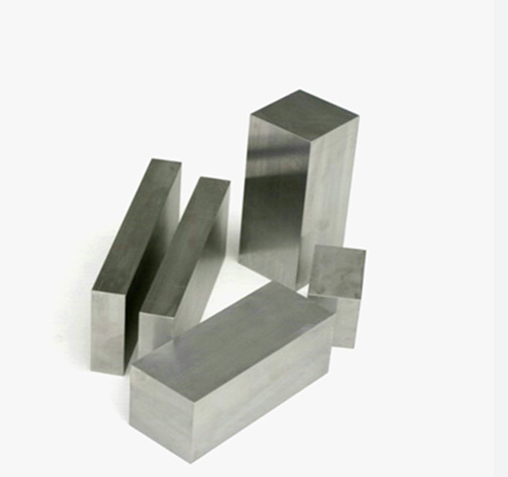
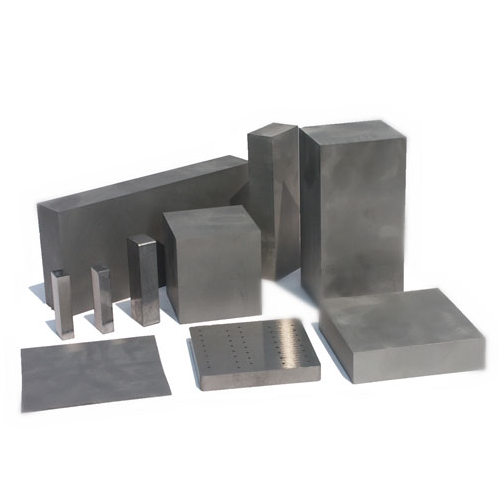
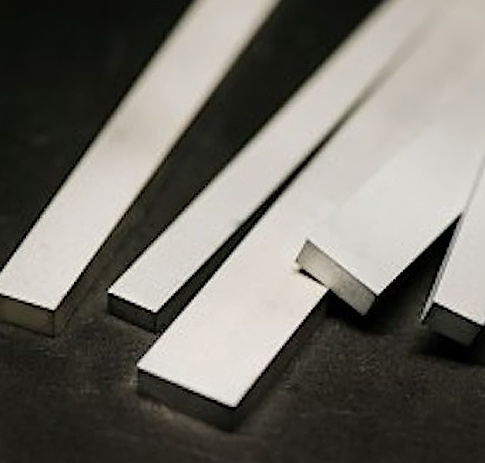
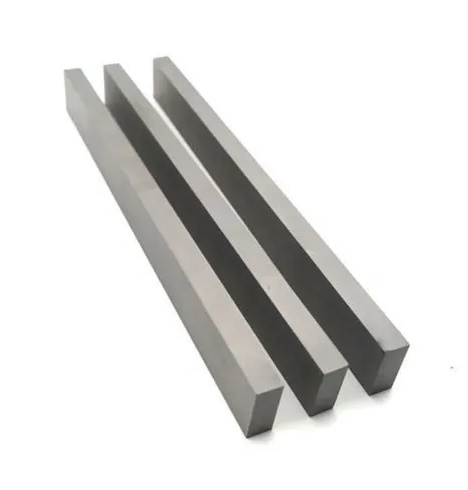
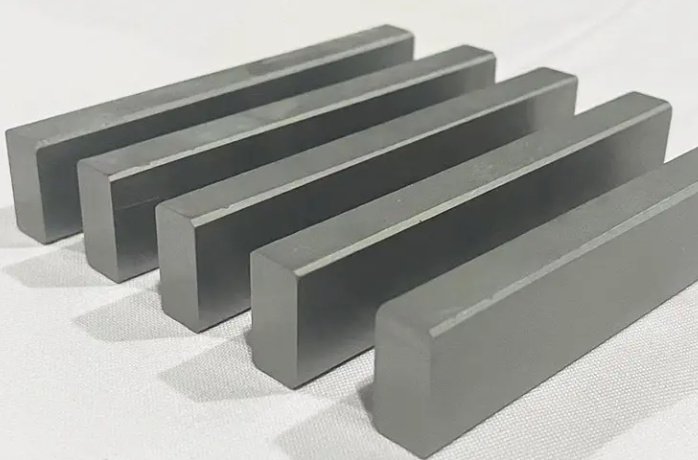
主要な要因 超硬棒 表面仕上げ
表面仕上げの方法を選択する際には、いくつかの要素が絡んできます。以下はその内訳である:
ファクター | 説明 |
---|---|
素材構成 | 超硬合金の種類は、仕上げ方法の選択に影響する。 |
申し込み | 特定の業界(例えば、医療業界と自動車業界)には固有の要件がある。 |
表面粗さ | 摩擦、摩耗、接着特性を測定する。 |
寸法精度 | 切削工具や金型にとって、精度は極めて重要である。 |
コスト | ダイヤモンド・コーティングのような高度な技術は、製造コストを増加させる可能性がある。 |
スケーラビリティ | 大容量の産業には、効率的で拡張性の高いソリューションが必要です。 |
超硬棒の特性に及ぼす超硬棒表面仕上げの影響
表面仕上げは、炭化タングステンロッドの物理的および化学的特性を大きく変えます。その方法は以下の通りです:
1.耐摩耗性
ダイヤモンド・コーティングのような強化された仕上げ方法は、耐摩耗性を劇的に向上させる。通常のタイヤからヘビーデューティーなオールテレーンタイヤにアップグレードするようなものだ。
2.摩擦低減
研磨と蒸着は摩擦を低減し、これは高速で動作する切削工具にとって非常に重要である。
3.耐食性
電気めっきと化学処理によって保護層が形成され、ロッドは環境劣化から保護される。
4.強化された体力
表面処理により耐荷重性が向上し、重荷重用途に適したロッドとなる。
切削工具、金型、エンジニアリング部品の超硬棒表面仕上げの例
- 切削工具:ダイヤモンドコーティングされた超硬ロッドは、チタンや硬化鋼のような強靭な材料の加工に比類のない精度を提供します。
- 金型:研磨された超硬ロッドは、プラスチックや医療機器などの産業に不可欠な射出成形金型の完璧な仕上げを保証します。
- エンジニアリング・コンポーネント:サンドブラスト処理された超硬ロッドは、航空宇宙および自動車分野の高応力用途に均一な表面を提供します。
異業種における超硬棒表面仕上げの需要
1.航空
航空産業では、高い応力と極端な温度に耐える工具が求められます。 超硬棒 高度な表面仕上げにより、求められる信頼性と精度を提供します。
2.自動車
エンジン部品から製造用切削工具に至るまで、自動車産業は研磨およびコーティングされた超硬ロッドから多大な恩恵を受けています。超硬棒は、自動車製造の舞台裏を支える縁の下の力持ちなのです。
3.医療機器
医療グレードの超硬ロッドは、衛生と精度の基準を満たすために卓越した仕上げが必要です。研磨された表面は手術器具の摩擦を減らし、安全性と効率を確保します。
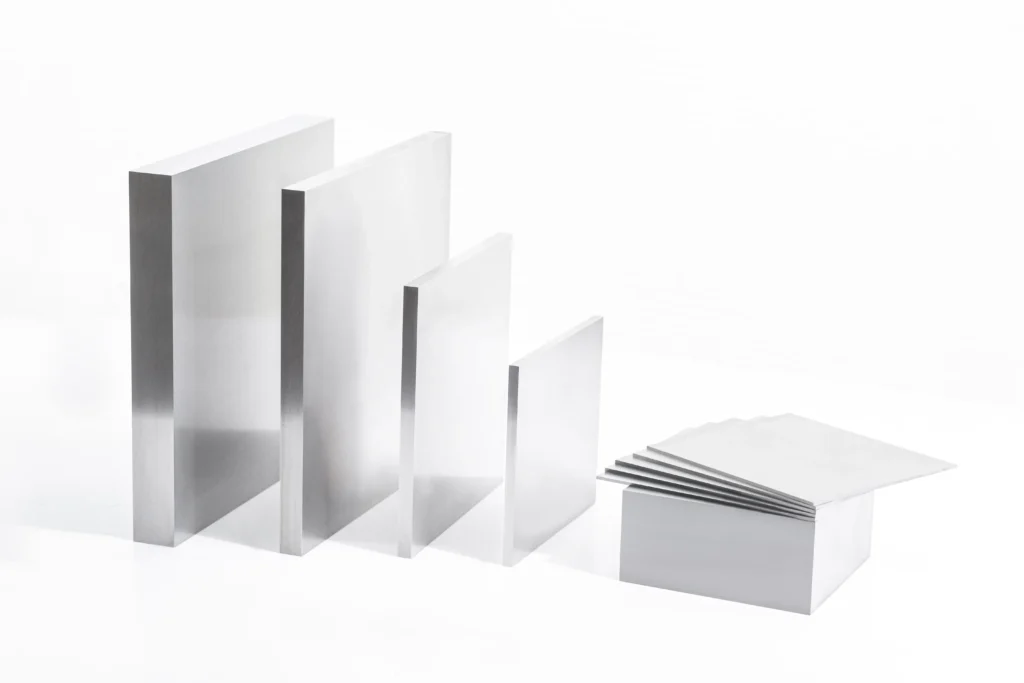
よくあるご質問
質問 | 回答 |
---|---|
表面仕上げの主な目的は何ですか? | 耐久性を向上させ、摩擦を減らし、性能を高める。 |
超硬ロッドが広く使われている産業は? | 航空、自動車、医療機器製造が主なユーザーである。 |
最も耐久性のある表面仕上げ技術とは? | ダイヤモンドコーティングは、比類のない耐摩耗性を提供する。 |
表面仕上げは切削工具にどのような影響を与えますか? | 切れ味を向上させ、摩耗を減らし、切削精度を高める。 |
すべての超硬ロッドに研磨は必要ですか? | アプリケーション固有の要件によります。 |
表面処理は高価ですか? | PVD/CVDのような高度な技術はコストがかかるが、長期的な価値をもたらす。 |
表面仕上げは環境破壊を軽減できるか? | そう、道具の寿命を延ばすことで、廃棄物や資源の消費を最小限に抑えることができる。 |