カーバイド パンチ・ストリップは、控えめでありながら強力なツールであり、無数の製造工程を支える縁の下の力持ちです。揺るぎない精度で材料を打ち抜き、貫通させ、成形するその能力は、エレクトロニクスから自動車に至るまで、さまざまな産業で欠かせないものとなっています。超硬パンチストリップの魅力に迫り、その組成、用途、厳しい加工作業に欠かせない要因を探ります。
超硬パンチストリップとは?
超硬パンチストリップは、超硬合金の薄くて平らな製品で、非常に高い硬度と耐摩耗性で有名な複合材料です。このストリップは、パンチングや成形作業中に発生する極度の力や摩擦に耐えられるよう、特別に設計されています。その秘密は、独自の組成にあります:
- 炭化タングステン: 主成分である炭化タングステンは、ダイヤモンドに迫る硬度を誇り、摩耗や磨耗に対する比類のない耐性を提供する。
- コバルト・バインダー 金属接着剤の役割を果たすコバルトは、炭化タングステン粒子を結合させ、繰り返しの打ち抜きサイクルに耐えるために必要な靭性と耐衝撃性を提供する。
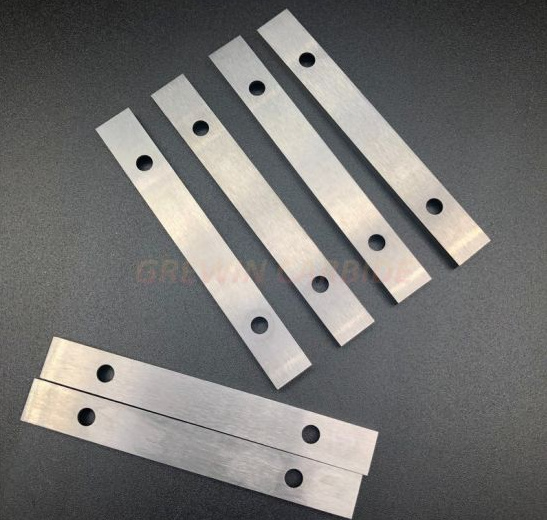
パウダーからパンチへ:超硬パンチストリップ製造の旅
超硬パンチストリップの誕生は、精密工学の賜物である:
- 粉末冶金: 炭化タングステンとコバルトの微粉砕粉末は、パンチング用途に求められる特性を達成するために、特定の比率で細心の注意を払って配合されています。
- プレスと成形: その後、粉末混合物は専用の金型内で大きな圧力をかけられ、ストリップの初期形状が形成される。
- 焼結:強さの融合: プレスされたストリップは、制御された雰囲気の中で高温焼結プロセスを経る。焼結中、コバルト・バインダーが溶けて炭化タングステン粒子を融合させ、強固で驚くほど緻密な素材が形成される。
- 精密研削と仕上げ: 焼結後、超硬ストリップは入念に研削され、パンチング用途に必要な正確な寸法、公差、表面品質を達成するために仕上げられます。
あらゆるパンチ用ストリップ:超硬パンチストリップの種類と特性
超硬パンチストリップは画一的なソリューションではありません。さまざまな等級、サイズ、構成があり、それぞれが特定のパンチング用途や材料に合わせて調整されています。ここでは、その多様性をご紹介します:
超硬パンチストリップ:その特性を読み解く
プロパティ | 説明 | 代表値 |
---|---|---|
硬度(HRA) | 引っかきや圧痕に対する耐性 | 88-95 |
横破断強度(TRS) | 折れることなく曲げ力に耐える能力 | 1500-3000 N/mm² |
圧縮強度 | 圧縮変形に対する耐性 | 4000~6000 N/mm² |
粒度 | 硬度と耐摩耗性に影響する炭化タングステンの粒子径 | 0.5-10 µm |
コバルト含有量 | 靭性と耐摩耗性に影響するコバルトバインダーの割合 | 6-12% |
表1:超硬パンチストリップの主要特性
超硬パンチストリップの用途超硬パンチストリップの用途
超硬パンチストリップは、さまざまな産業で精密パンチ加工の原動力となっています:
1.エレクトロニクスデジタル世界の形成
- プリント基板(PCB): 超硬パンチストリップは、電子部品を取り付けるためにプリント基板に正確な穴と切り欠きを作り、正確な回路接続を保証します。
- 半導体製造: ウェハーのダイシングやパッケージング工程で使用され、デリケートな半導体チップの正確な分離と取り扱いを保証します。
2.自動車あらゆる部品の精度を高める
- 金属プレス: 超硬パンチストリップは、自動車ボディ、フレーム、部品用のシートメタル部品に穴、スロット、その他の特徴を形成します。
- 燃料噴射システム 燃料噴射システムの精密なノズルと部品の製造に使用され、最適な燃料噴霧化とエンジン性能を保証する。
3.組立ラインを越えて
超硬パンチストリップの汎用性は、以下のような他の産業にも幅広く及んでいる:
- 航空宇宙 航空機部品用の軽量素材に穴や溝を開ける。
- メディカルだ: 手術器具や医療機器に精密な開口部や形状を作り出す。
- パッケージング: 包装材料を切断・成形するための金型を製造。
競争優位性:超硬パンチストリップ・サプライヤーの比較
サプライヤー | 所在地 | 価格帯(1個あたり) | 特産品 |
---|---|---|---|
TRUER | グローバル | $10 – $80 | カスタム カーバイド・ソリューション要求の厳しいパンチング用途向けの高性能グレード |
エレメント・シックス | グローバル | $15 – $100 | 幅広い標準および特殊材種、工具寿命延長のための高度なコーティング |
サンドビック・コロマント | スウェーデン | $20 – $120 | 大量打抜きと難度の高い素材に対応する高度な形状とコーティング |
ケナメタル | 米国 | $12 – $90 | 自動車、電子機器など様々な産業向けの高品質超硬パンチストリップ |
表2:超硬パンチストリップ・サプライヤーの比較
注: 価格は概算であり、等級、サイズ、数量、市況によって異なる場合がある。
バランスのとれた視点:超硬パンチストリップの利点と限界
超硬パンチストリップ:長所と短所の比較
メリット | 制限事項 |
---|---|
優れた硬度と耐摩耗性により、長い工具寿命を実現 | 比較的脆く、極端な衝撃や側面荷重がかかると欠けたり割れたりしやすい。 |
高い寸法精度と精密さにより、複雑な部品の作成が可能。 | 特に複雑な形状の場合、他の工具材料に比べて高価になる可能性がある。 |
薄い箔から厚板まで、幅広い素材のパンチングが可能 | 機械加工や研ぎ出しには、専用の設備と専門知識が必要 |
高温・高圧への耐性があり、要求の厳しい用途に適している。 | 特に、非常に大きな穴や不規則な形状の穴を伴う用途には適さない場合があります。 |
表3:超硬パンチストリップの利点と限界
パンチプレスを超えて:超硬合金についての興味深い事実
- 鉱業から製造業へ: 炭化タングステンの主成分であるタングステンは、スウェーデン語で "重い石 "を意味する "tung sten "に由来する。タングステンは当初、その非常に硬い性質から採掘工具に使用されていた。
- 極限の素材: 炭化タングステンはすべての金属の中で最も融点が高く、摂氏3,422度(華氏6,192度)に達する。
- 持続可能な選択 タングステンカーバイドは非常に耐久性のある素材であり、そこから作られた工具は何度も研ぎ直すことができるため、廃棄物を減らし、持続可能性を促進する。
超硬パンチストリップのニーズにTRUERを選ぶ理由
TRUERは、お客様が卓越したパンチング性能を達成できるような超硬ソリューションを提供することに専念しています。TRUERが際立つ理由はここにあります:
- 妥協のない品質: 当社では、最高品質のタングステンカーバイド材料を調達し、製造工程全体で厳格な品質管理措置を採用しています。
- カスタムソリューション: 弊社は、グレードや形状からサイズや仕上げに至るまで、お客様独自の仕様に合わせた超硬パンチストリップの製造を専門としています。
- 技術的専門知識: 当社の超硬専門家チームは、専門的なガイダンスとサポートを提供し、お客様のパンチングアプリケーションに最適な超硬ソリューションを選択するお手伝いをします。
- グローバルなリーチ グローバルな事業展開により、世界中どこにいてもタイムリーな配送と迅速なカスタマーサービスを提供します。
よくある質問超硬パンチストリップに関するお問い合わせ
1.超硬パンチストリップの寿命に影響する要因は何ですか?
超硬パンチストリップの寿命は、以下のようないくつかの要因に左右される:
– 超硬グレード: グレードの高い超硬ストリップは、一般に工具寿命が長い。
– パンチされる素材: 研磨材や高強度材のパンチングは、工具寿命を縮める可能性がある。
– パンチングの条件 パンチング速度、潤滑、材料の厚みが摩耗率に影響する。
– メンテナンス 適切に研ぎ、洗浄し、保管することで、超硬パンチストリップの寿命を大幅に延ばすことができます。
2.超硬パンチストリップはコーティングできますか?
はい、超硬パンチストリップは、その性能を高めるために様々な材料でコーティングすることができます。一般的なコーティングは以下の通りです:
– 窒化チタン(TiN): 硬度を高め、摩擦を減らし、耐摩耗性を向上させる。
– 炭窒化チタン(TiCN): TiNよりもさらに高い硬度と耐摩耗性を提供。
– ダイヤモンドライクカーボン(DLC): 優れた潤滑性と耐摩耗性を発揮し、特に研磨材の打ち抜きに最適。
3.超硬ストリップを使用したパンチとダイのセットを設計する際の主な考慮事項は何ですか?
超硬ストリップを使用した効果的なパンチとダイセットの設計には、次のような要素を考慮する必要があります:
– クリアランス パンチとダイの間のスペースで、材料の流れを制御し、損傷を防ぐために重要である。
– 剥離力: 打ち抜かれた材料をダイから取り外すのに必要な力で、パンチとダイの設計に影響する。
– 素材の厚みと特性: 打ち抜かれる材料の種類と厚さは、パンチとダイの形状に影響を与える。
4.パンチング用途に適した超硬材種はどのように選べばよいですか?
適切な超硬材種を選択するには、以下のような要素を考慮する必要がある:
– パンチされる素材: 異なる超硬グレードは、特定の材料(スチール、アルミニウム、銅など)の打ち抜き用に最適化されています。
– パンチ力とスピード: より高い荷重と回転数には、より強靭な超硬材種が必要になる場合がある。
– 必要な工具の寿命: 長い工具寿命を必要とする用途では、より高いグレードの超硬ストリップが役立ちます。
5.超硬パンチストリップの取り扱いと使用に関する安全上の注意点は?
超硬パンチストリップは非常に硬く、チッピングの可能性があるため、取り扱いには十分注意してください:
– 安全眼鏡を着用すること: 飛散する切り屑や破片から目を守る。
– 手袋を使用する: 鋭利な刃物による切り傷を防ぐ。
– 取り扱い注意: 欠けや破損を防ぐため、ストリップを落としたり衝撃を与えたりしないでください。