Carbide plates are integral components in a variety of industrial applications, ranging from cutting tools to wear-resistant surfaces. Producing these plates is a meticulous process involving a series of well-defined steps to ensure optimal performance and durability. In this detailed guide, we’ll explore the entire process of carbide plate production, breaking it down step by step.
Preparation of Raw Materials for Carbide Plate Production
The foundation of any high-quality carbide plate lies in its raw materials. The primary constituents are tungsten carbide powder and a metallic binder, typically cobalt or nickel. The purity, particle size, and distribution of these materials play a significant role in the final product’s properties.
Why is preparation critical?
Imagine trying to bake a cake with poorly sifted flour—it just wouldn’t rise evenly! Similarly, for carbide plates, the raw materials need to be meticulously processed to achieve uniformity and consistency.
- Selection of Tungsten Carbide: Raw tungsten carbide is sourced from ores or recycled carbide materials. It’s refined to ensure it meets stringent purity requirements.
- Binder Metal: High-purity cobalt or nickel is chosen based on the desired application. Cobalt enhances toughness, while nickel provides better corrosion resistance.
- 添加物: Minor elements may be added to tailor specific properties like wear resistance or thermal stability.
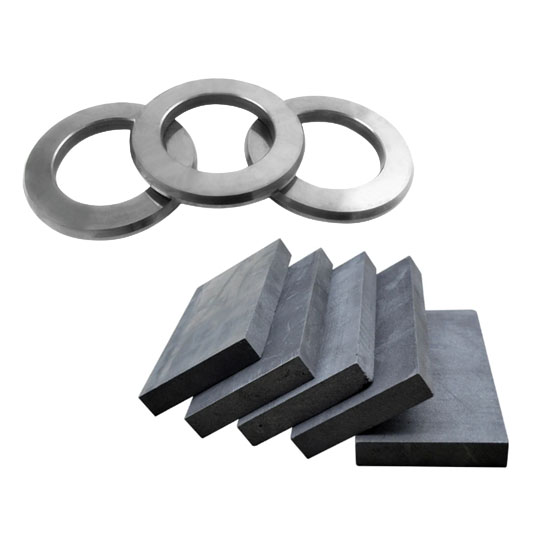
Mixing and Granulation of Carbide Plate Production
Once the raw materials are ready, they are mixed and granulated to create a homogenous blend that ensures consistency in the final product.
ステップ | 説明 |
---|---|
Blending | Tungsten carbide and binder metal powders are blended using ball mills or attritors. This ensures uniform particle dispersion. |
Wet Milling | A liquid medium (e.g., ethanol) is added to prevent clumping and improve mixing. |
Granulation | The wet mixture is spray-dried to form granules of uniform size. These granules have better flow characteristics, making them suitable for the next step, compression molding. |
Compression Molding of Carbide Plate Production
The granulated mixture is now ready to be compressed into a green compact—a shape that resembles the final product but is much weaker.
The Compression Process
Compression molding is akin to pressing cookie dough into a mold. It gives the material its preliminary shape.
- Tooling Design: Molds are customized to the desired dimensions of the carbide plates.
- 高圧: Hydraulic presses apply pressures of up to several tons to compact the granules. The pressure ensures the granules stick together and eliminates voids.
- Green Strength: After molding, the compact has enough strength to be handled but is still fragile and needs further processing.
Sintering of Carbide Plate Production
Sintering is the most critical stage, where the green compact is transformed into a dense, hard carbide plate.
パラメータ | 説明 |
---|---|
Temperature Range | Typically between 1,300°C and 1,600°C. |
Atmosphere | Conducted in a vacuum or controlled environment to prevent oxidation. |
Duration | Sintering times vary based on plate size but often range from several hours to a full day. |
Liquid Phase Formation | During sintering, the binder metal melts and fills the voids, creating a dense, solid structure. |
What happens during sintering?
Think of sintering like firing pottery in a kiln. The high temperatures not only harden the material but also bond the particles on a molecular level. In carbide plate production, this step also aligns the material’s grain structure, enhancing its strength and wear resistance.
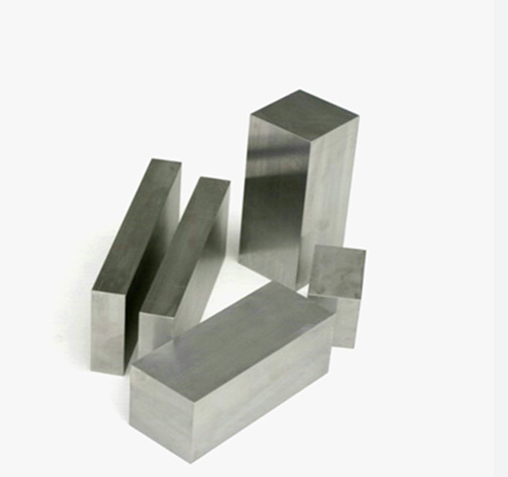
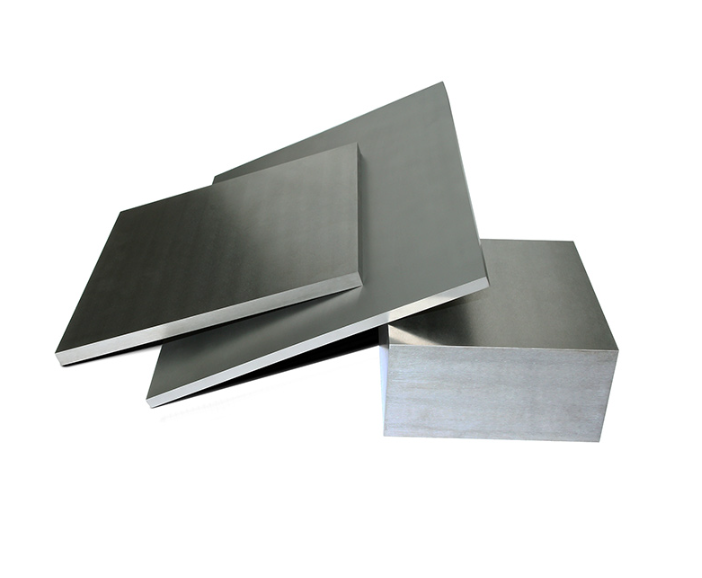
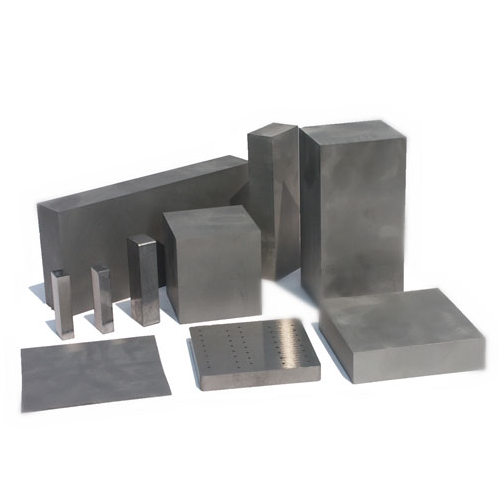
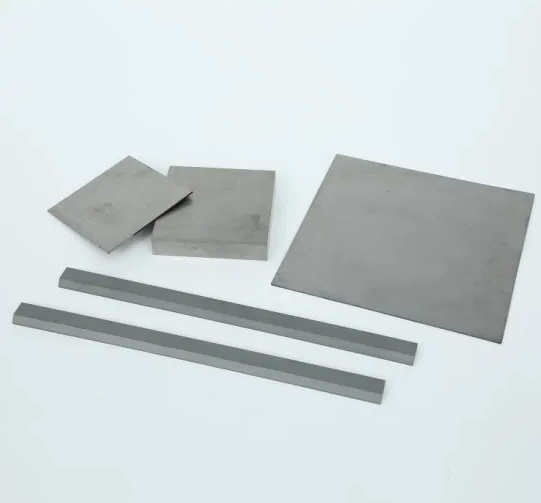
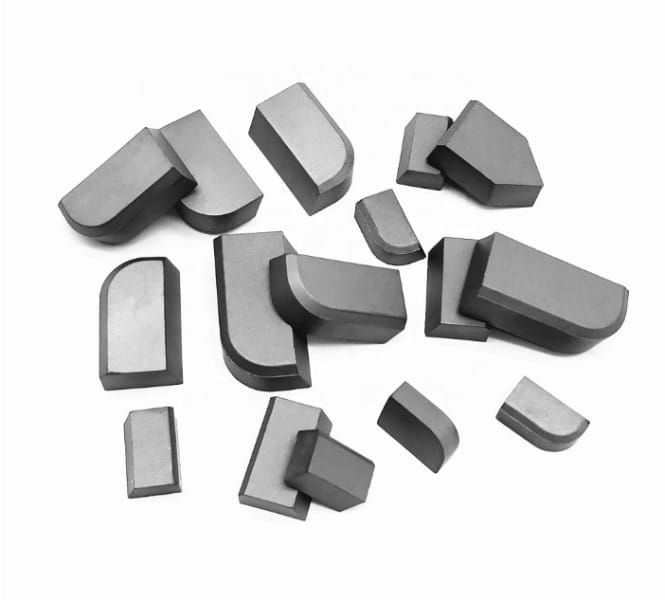
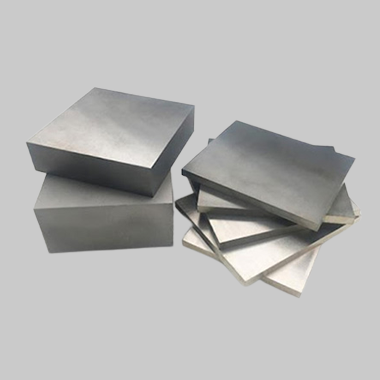
Cooling and Demolding of Carbide Plate Production
After sintering, the carbide plates are cooled and removed from their molds. This step might sound straightforward, but it’s essential for maintaining the integrity of the product.
ステップ | 詳細 |
---|---|
Controlled Cooling | Plates are cooled slowly to prevent thermal shock, which can cause cracking. |
Demolding | Plates are carefully removed from molds to avoid surface damage. |
Residual Stress Relief | In some cases, additional heat treatments are applied to relieve stresses introduced during cooling or sintering. |
Post-Processing of Carbide Plate Production
Once cooled, the carbide plates undergo various post-processing steps to achieve the required dimensions, surface finish, and performance characteristics.
Typical Post-Processing Steps
- 研削と研磨: The plates are ground to precise dimensions and polished for smoothness.
- Coating (if applicable): Some plates receive additional coatings, like PVD (Physical Vapor Deposition), to improve wear resistance.
- Deburring: Any sharp edges or burrs are removed to ensure safe handling and application.
Inspection and Testing of Carbide Plate Production
No production process is complete without thorough quality checks. Inspection ensures that each carbide plate meets stringent industry standards.
Test Type | 目的 |
---|---|
寸法精度 | Verifies the plate’s dimensions align with design specifications. |
硬度試験 | Measures resistance to deformation, often using the Rockwell or Vickers scale. |
Density Check | Ensures no voids or porosity are present. |
耐摩耗性 | Simulates real-world conditions to test durability. |
Ultrasonic Testing | Detects internal defects or cracks. |
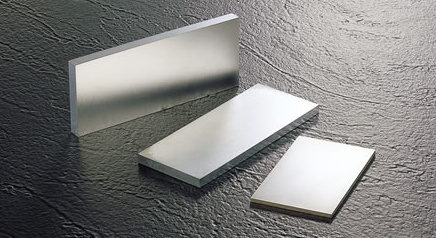
よくあるご質問
質問 | 回答 |
---|---|
What materials are used in carbide plates? | Tungsten carbide powder and a metallic binder like cobalt or nickel are the primary components. |
Why is sintering so important? | Sintering solidifies the plate, eliminates voids, and bonds particles, giving the material its final strength and durability. |
How are carbide plates inspected for quality? | Through tests like dimensional checks, hardness measurements, and ultrasonic inspections to detect internal defects. |
超硬プレートはカスタマイズできますか? | Yes, they can be tailored in size, thickness, and even material composition based on specific applications. |
超硬合金はどのような産業で使用されていますか? | Common applications include cutting tools, wear-resistant surfaces, mining equipment, and high-pressure dies. |
By understanding each step of carbide plate production, you can appreciate the craftsmanship and precision that goes into these industrial workhorses. Whether you’re selecting carbide plates for a project or simply curious about their manufacturing, this guide provides the knowledge to make informed decisions.