はじめに摩耗に打ち勝ち、耐久性を実現
摩耗、衝撃、極限状態が日常的な課題である産業では、耐摩耗性が求められます。 カーバイドプレート ブランクは、縁の下の力持ちとして登場しました。超硬合金から丹念に設計されたこれらの頑丈なプレートは、重要なコンポーネントに卓越した保護を提供し、その寿命を延ばし、コストのかかるダウンタイムを最小限に抑えます。
この包括的なガイドでは、耐摩耗性超硬プレートブランクの世界を掘り下げ、その特性、製造工程、多様な用途、そしてTRUERのような信頼できるサプライヤーと提携する利点についてご紹介します。
耐摩耗超硬プレートブランク:摩耗に対する盾
超硬合金のパワーを理解する
耐摩耗性カーバイドプレートブランクは、主に炭化タングステン(WC)粒子で構成された予備焼結または完全焼結プレートで、その卓越した硬度で有名であり、金属バインダー、通常はコバルト(Co)によって結合されています。このユニークな組成は、これらのプレートに比類のない耐摩耗性を付与し、表面が一定の摩擦、摩耗、または衝撃にさらされる用途に最適です。
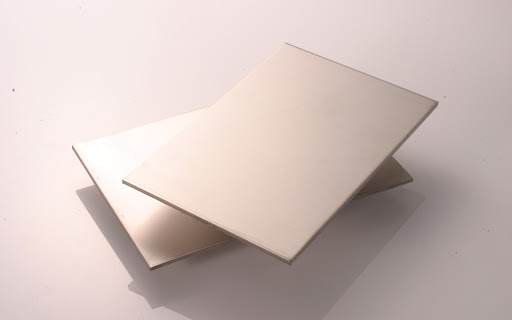
耐摩耗性チャンピオンの誕生
パウダーからプレートへ:製造工程
耐摩耗性超硬プレートブランクの製造には、注意深く管理された複数の工程が必要です:
- パウダーの調製: 炭化タングステン(WC)粉末とバインダー金属粉末、通常はコバルト(Co)を特定の比率で精密に混合し、所望の材料特性を実現します。タンタル(Ta)、ニオブ(Nb)、チタン(Ti)などの他の元素を加えて、耐摩耗性や耐食性などの特定の特性を高めることもできる。
- プレスする: 混合粉末は次に、高圧金型を使って目的の板形状にプレスされる。加圧により粉末が圧縮され、ハンドリングに十分な強度を持つ「グリーン」(未焼結)プレートが形成される。
- プリシンター(オプション): メーカーによっては、グリーン・プレートを炉で制御された加熱工程にかける焼結前工程を採用している。これにより、グリーン・プレートの強度が増し、最終的な焼結の準備が整う。
- 焼結: プレ焼結またはグリーン・プレートは、制御された雰囲気炉で超高温(通常1350℃~1500℃)にさらされる。液相焼結として知られるこのプロセスは、WC粒子を溶融バインダー相を通して融合させ、高密度で信じられないほど硬い材料を生み出す。
- 仕上げ: 焼結後、板は、所望の寸法、表面仕上げ、平坦度を達成するために、研削、ラッピング、研磨などの様々な仕上げ加工を受けることができる。
特性を読み解く:超硬合金の耐摩耗性とは?
表1:耐摩耗性超硬プレートブランクの代表的特性
プロパティ | 説明 | 代表値 |
---|---|---|
硬度(HRA) | 凹みと引っかきに対する耐性 | 88-95 |
横破断強度(TRS) | 曲げ力に耐える能力 | 1200 - 2500 MPa |
圧縮強度 | 破砕力に対する耐性 | 4000 - 6000 MPa |
密度 | 単位体積当たりの質量 | 13.5 - 15.0 g/cm³ |
摩擦係数 | 他の素材との摺動抵抗 | 0.1~0.3(相手材による) |
耐食性 | 化学的攻撃に耐える能力 | ほとんどの環境で優れている |
アプリケーション耐摩耗性が支配する場所
鉱業から製造業まで、アプリケーションの世界
超硬プレートブランクの卓越した耐摩耗性は、幅広い産業と用途で不可欠なものとなっています:
- 鉱業と建設業 超硬プレートは、シュート、ホッパー、バケット、カッティングエッジなどの採掘装置の重要な部品を、岩石、鉱石、その他の過酷な材料の研磨力から保護します。
- 石油・ガス 石油やガスの探査や生産で遭遇する過酷な圧力や研磨環境では、耐摩耗性の部品が要求されます。超硬プレートは、掘削装置、バルブ、ポンプ、その他の重要な部品に使用され、長寿命と信頼性を保証します。
- 発電: 耐摩耗性カーバイドプレートは発電所では不可欠で、石炭粉砕機、灰処理システム、その他研磨粒子による摩耗が発生しやすい場所の部品を保護しています。
- 金属加工と成形: 超硬プレートブランクは、金属成形作業におけるダイ、パンチ、摩耗プレートの作成に使用され、精密な公差と工具寿命の延長を保証します。
- リサイクルと廃棄物管理: シュレッダー、クラッシャー、その他のリサイクル機器のコンポーネントを保護するために、耐摩耗性カーバイドプレートが不可欠です。
超硬プレートブランクサプライヤーの比較:グローバルな視点
表2:耐摩耗性超硬プレートブランクサプライヤーの比較
サプライヤー | 所在地 | 価格帯(kgあたり、米ドル) | 特産品 |
---|---|---|---|
ケナメタル | アメリカ | $80 – $250+ | 幅広い超硬材種、大きな板サイズ、精密研削能力 |
サンドビック・コロマント | スウェーデン | $90 – $280+ | 高度な超硬グレード、極限摩耗用途の特殊コーティング |
エレメント・シックス | イギリス, グローバル | $100 – $300+ | 過酷な摩耗に対する多結晶ダイヤモンド(PCD)と炭化タングステンのソリューションの専門知識 |
セラティジット | ルクセンブルク | $70 – $220+ | 費用対効果の高いソリューション、標準およびカスタム超硬グレード、グローバルな製造拠点 |
タンガロイ | 日本 | $85 – $260+ | 高性能カーバイド材種、厳しい公差、精密加工の専門知識 |
TRUER | 中国 | $65 – $200+ | 高品質、コスト効率 超硬プレートブランク地質鉱業製品における専門知識;優れた密度と耐摩耗性を実現する高度なプレス・焼結技術による垂直統合製造 |
注: 価格は概算であり、板サイズ、等級、数量、公差、表面仕上げの要件、およびその他の要因によって大幅に異なる場合があります。
利点と限界:トレードオフを天秤にかける
表3:耐摩耗超硬プレートブランクの利点と限界
メリット | 制限事項 |
---|---|
卓越した耐摩耗性: 摩耗、侵食、衝撃を受ける部品の寿命を大幅に延ばし、ダウンタイムとメンテナンスコストを削減 | 脆い性質: 超硬合金は硬度が高いため本質的に脆く、衝撃や衝撃荷重が大きいと欠けたり割れたりしやすい。 |
高い硬度と強度: 過酷な圧力や研磨条件下でも、構造的完全性と寸法精度を維持します。 | コストだ: 超硬プレートブランクは通常、耐摩耗鋼や他の材料に比べて初期コストが高い。 |
汎用性がある: 多様な用途に対応するため、さまざまなグレード、サイズ、形状を用意 | 機械加工の課題: 超硬合金の加工には、その硬度と研磨性のために特殊な設備、工具、専門知識が必要です。 |
TRUERの違い:なぜTRUERを選ぶのか?
- 妥協のない品質: TRUERでは、品質第一をモットーとしています。すべての耐摩耗性超硬プレートブランクがお客様のご期待に沿う、あるいはご期待を上回ることを保証するために、製造工程全体にわたって厳格な品質管理手段を維持しています。
- 垂直統合: パウダー加工から最終仕上げまで、垂直統合された製造工程により、製造のあらゆる側面を管理することができ、一貫した品質と競争力のある価格を実現しています。
- 技術的専門知識: 当社の経験豊富なエンジニアチームは、超硬材料と用途に関する深い知識を有しています。お客様との緊密な連携により、お客様の具体的なニーズを理解し、用途に最適な超硬合金グレードとプレート設計を推奨します。
- 顧客中心のアプローチ: 私たちは、卓越したカスタマーサービスとサポートを提供することをお約束します。私たちの専門チームは、いつでもお客様のご質問にお答えし、技術的なサポートを提供し、お客様にご満足いただけるよう努めます。
よくある質問(FAQ)
摩耗に関する懸念への対応
1.耐摩耗性超硬プレートブランクの一般的な寿命を教えてください。
超硬プレートブランクの寿命は、用途の厳しさ、扱う材料、使用環境など、さまざまな要因に左右されます。しかし、超硬プレートは通常、同等の用途で耐摩耗鋼の5~10倍長持ちします。
2.製造可能な最大の超硬プレートサイズは?
当社では、最大1500mm x 600mm、厚さ3mmから50mmまでの超硬プレートの製造が可能です。
3.特注の形状や穴パターンの超硬プレートは提供できますか?
はい。お客様独自のアプリケーション要件を満たすために、特定の形状、穴パターン、その他の特徴を持つ超硬プレートを作成するカスタム加工サービスを提供しています。
4.超硬プレートを部品に取り付ける最良の方法は?
超硬プレートは、ろう付け、溶接、機械的固定、接着剤による接着など、さまざまな方法で取り付けることができます。最適な方法は、特定の用途と関係する材料によって異なります。
5.摩耗用途に適した超硬材種を選ぶには?
最適な性能と寿命を得るためには、適切な超硬材種を選択することが極めて重要です。考慮すべき要素には、摩耗の種類と程度、使用温度、耐衝撃性の要件、耐腐食性のニーズなどがあります。当社のエンジニアリング・チームは、特定の用途に最適な材種を選択するお手伝いをいたします。