超硬材料の特性を理解する
取り組むべきこと 超硬加工の課題 を効果的に使用するには、まずカーバイドの特徴を理解する必要がある。炭素とタングステンのような金属元素の化合物である超硬合金は、卓越した硬度、耐摩耗性、熱伝導性を誇ります。しかし、これらの特性をもっと深く掘り下げてみよう:
- 硬度:超硬合金の硬度はロックウェル単位で測定され、90HRAを超えることが多い。そのため、変形しにくいが、加工しにくい。
- 熱安定性:超硬合金は、高温でも強度と硬度を維持するため、高速切削工具に使用されている。
- 耐摩耗性:超硬部品は、その緻密な構造により、研磨条件下で多くの代替品よりも長持ちします。
- 脆さ:超硬合金はその強さにもかかわらず、不均一な応力や衝撃で欠けたり割れたりしやすい。
これらの特性を理解することは、メーカーが特定の用途に適した等級と工具を選択し、無駄を最小限に抑え、効率を高めるのに役立つ。
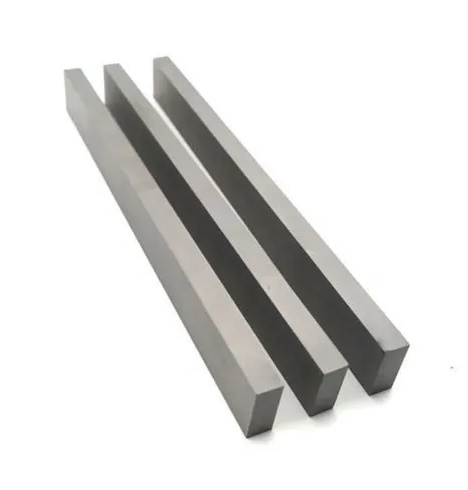
超硬加工における一般的な課題
超硬合金の加工は容易ではありません。超硬合金は非常に硬いため、性能的には優れていますが、工具や加工技術には厳しいという両刃の剣です。最も一般的な課題を探ってみましょう:
1. 工具の摩耗と破損
超硬合金の硬度は、工具の摩耗を早める。切削工具は、たとえ超硬用に設計されたものであっても、すぐに劣化し、頻繁な交換とコスト増につながります。
2. 発熱
超硬合金の加工ではかなりの熱が発生し、精度に影響を与えたり、工具の劣化を引き起こしたりします。放熱の管理は非常に重要です。
3. 表面仕上げの問題
超硬合金は脆いため、滑らかな仕上げを実現するのは難しい。不適切な加工は、表面に亀裂や粗いテクスチャーを生じさせます。
4. チップコントロール
超硬合金はもろいため、切りくずが不均一になったり断片化したりすることが多く、回収や廃棄の際に問題が生じる。
5. 高い設備コスト
超硬加工に必要な特殊な機械や工具は割高である。そのため、中小メーカーはこの技術を採用しにくい。
超硬加工における革新
イノベーション | 説明 | メリット |
---|---|---|
アドバンスト・コーティング | 切削工具にTiAlNやダイヤモンドライクカーボンなどのコーティングを施す。 | 工具寿命の向上、摩耗の低減、耐熱性の向上。 |
高精度研削 | ダイヤモンド砥石の利用。 | 表面仕上げと寸法精度の向上。 |
クーラント統合システム | 高圧クーラント供給システムの使用。 | 効果的な熱管理、熱変形の低減。 |
レーザーアシスト加工 | レーザーによる超硬合金表面の予熱。 | 脆性が減少し、切り屑の除去が容易になった。 |
アディティブ・マニュファクチャリング | 超硬粉末を使った3Dプリンティングツール。 | 工具のカスタマイズ、材料の無駄の削減。 |
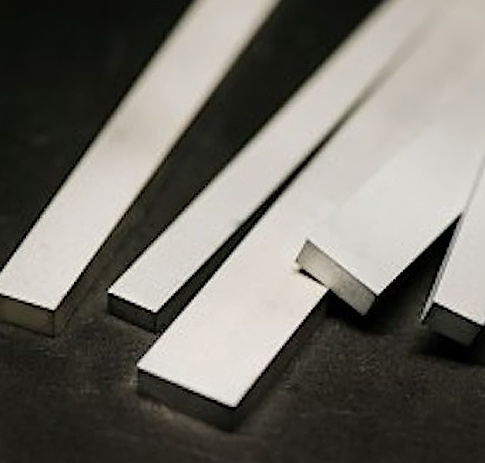
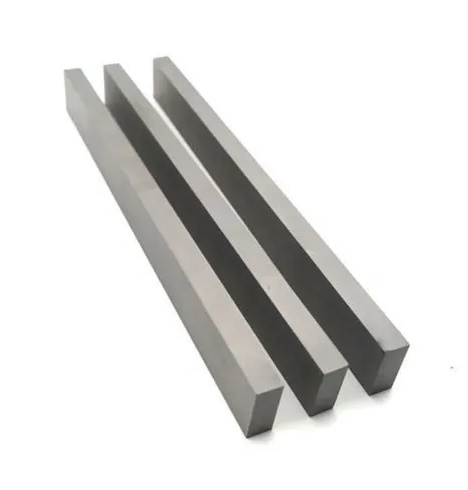
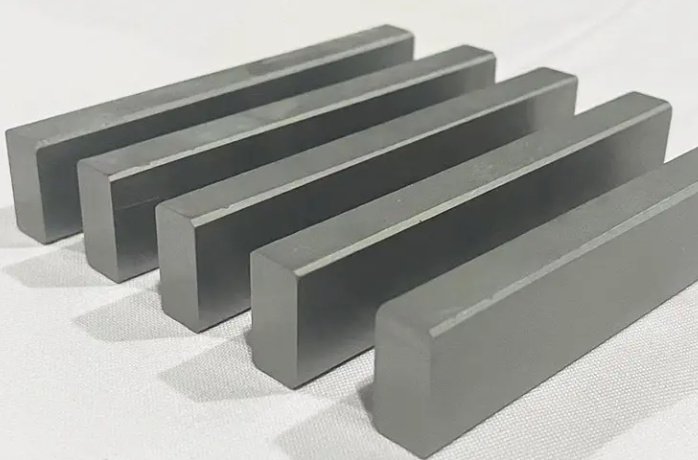
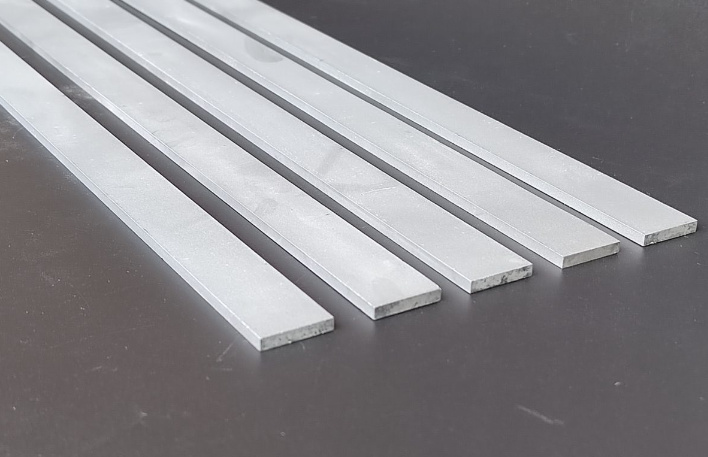
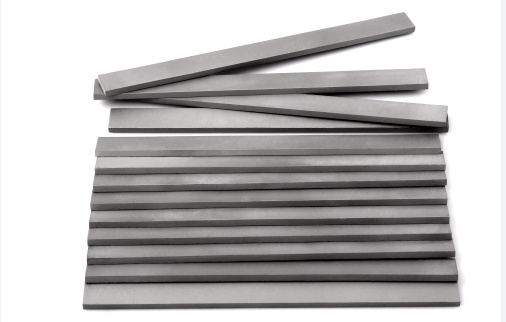
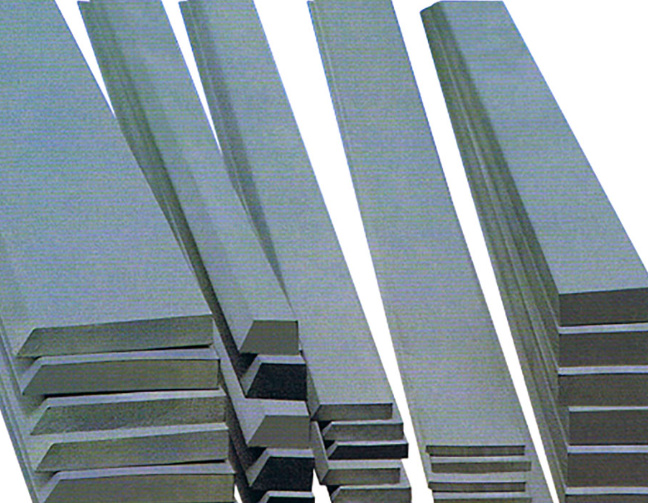
メーカーのための実践的ヒント
1. 適切なツールを選ぶ
ダイヤモンドチップやコーティングされたオプションなど、超硬専用に設計された工具を選ぶ。工具の材種を用途に合わせる-耐摩耗性には硬い材種を、衝撃吸収には柔らかい材種を。
2. 切削パラメータの最適化
工具の摩耗を最小限に抑えるために、速度、送り速度、切り込み深さのバランスをとる。超硬加工では、低速の方がうまくいくことが多い。
3. 適切なクーラントの使用
高性能クーラントは熱を低減し、工具の寿命を延ばします。大規模加工には浸水冷却、精密加工にはミスト冷却をご検討ください。
4. 高品質の機械に投資する
超硬加工には、振動減衰機能を備えた高剛性CNCマシンが不可欠です。精度が重要なので、ここで手を抜いてはいけません。
5. 定期的な工具のメンテナンス
工具は定期的に点検し、研ぎ直してください。工具が鈍っていると、作業効率が低下するだけでなく、超硬部品が損傷する可能性があります。
超硬マシニングの特徴
超硬加工は、そのユニークな特徴で際立っています。以下はその内訳である:
- 耐久性:研磨条件下でも部品が長持ち。
- 精密:厳しい公差を達成することができる。
- 汎用性:工具から航空宇宙まで、幅広い産業に適している。
- 費用対効果:イニシャルコストは高いが、耐久性と性能における長期的な節約はそれを相殺する。
比較 超硬加工の課題 その他の代用品
特徴 | 超硬加工 | スチール加工 | セラミック加工 |
---|---|---|---|
硬度 | スーペリア | 中程度 | 高い |
工具摩耗率 | 高い | 中程度 | 低い |
耐熱性 | 素晴らしい | グッド | 素晴らしい |
コスト | 前払い金が高い | 先行投資額を抑える | 高い |
脆さ | 欠けやすい | もろくなりにくい | 非常に脆い |
表面仕上げ精度 | 高精度を実現 | 中程度の精度 | 優れた精度 |
超硬切削工具を購入する際の注意点
超硬切削工具を購入する際には、次のことを考慮する:
- 素材グレード:お客様の用途との適合性をご確認ください。コバルトバインダー付き超硬合金は汎用性があります。
- 工具コーティング:コーティングされた工具は長持ちし、性能も向上する。
- サプライヤーの評判:ケナメタル、サンドビック、セラチジットのような信頼できるブランドにこだわる。
- カスタマイズ性:ユニークな用途には、オーダーメイドの工具設計をご検討ください。
- 価格対性能:高品質な道具は初期費用は高いが、長期的には節約になる。
の利点と限界 超硬加工の課題
アスペクト | メリット | 制限事項 |
---|---|---|
硬度 | 高い耐摩耗性と耐変形性 | 非常に硬いため機械加工が難しい |
熱安定性 | 高温でも特性を維持 | 高度な冷却ソリューションが必要 |
長寿 | 研磨条件下での耐久性 | 高額な設備投資 |
精密 | 厳しい公差と優れた表面仕上げ | 脆く、ストレスで欠けやすい。 |
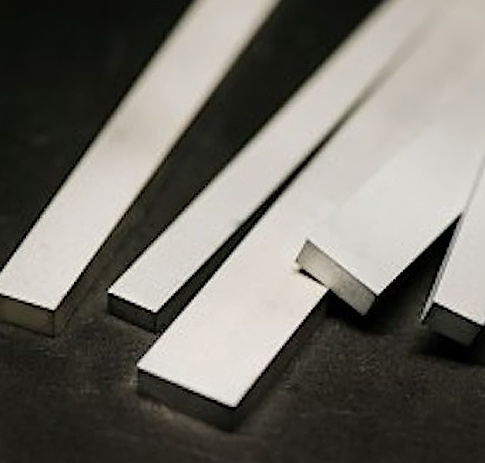
よくあるご質問
質問 | 回答 |
---|---|
超硬合金は機械加工で何に使われるのか? | 超硬合金は、その硬度と熱安定性により、切削工具、金型、耐摩耗部品に使用される。 |
なぜ超硬加工は難しいのか? | 非常に硬く、脆いため、工具には厳しく、特殊な器具が必要となる。 |
超硬工具の寿命を延ばすには? | 適切なコーティングの使用、切削パラメータの最適化、効果的な冷却技術の採用。 |
どのような産業で超硬合金が役立っているのか? | 航空宇宙、自動車、工具、鉱業などでは、その耐久性と精度の高さから超硬合金が頻繁に使用されている。 |
超硬加工は費用対効果が高いのか? | 初期費用は高いが、その耐久性と性能は長期的には大きな節約になる。 |