最先端:超硬エンドミルが材料除去に革命を起こすまで
カーバイド エンドミルs は、現代製造業の主力製品として、幅広い産業分野で精密かつ効率的な材料除去を可能にしています。航空宇宙、自動車から医療、金型製造に至るまで、非常に硬い超硬合金をチップに使用したこの万能切削工具は、卓越した性能、寿命、費用対効果を発揮します。この包括的なガイドでは、超硬エンドミルの構造、用途、利点、および最適な結果を得るために考慮すべき重要な要素を掘り下げ、超硬エンドミルの複雑さを探求します。
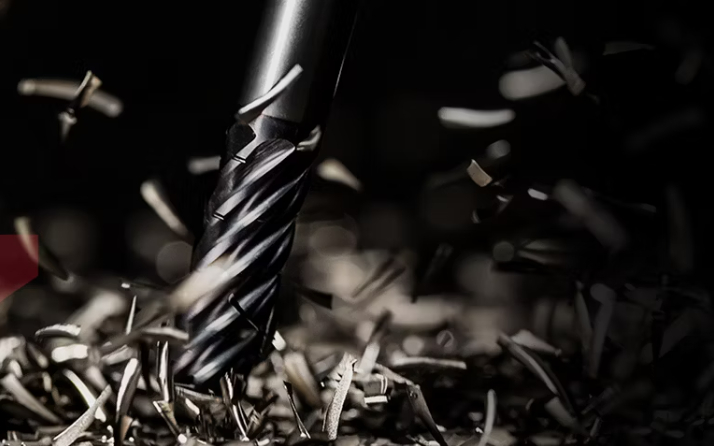
鋼を超える:超硬エンドミルの構造を理解する
コンポーネントとコンフィギュレーション構造を詳しく見る
- カッティングエッジ: 工具のビジネスエンドで、材料を剪断する複数のフルート(切れ刃)を特徴とする。フルートは直線状、ヘリカル状、または特定の用途に合わせた複雑な形状がある。
- シャンク: フライス盤でツールホルダーによって保持される円筒状の部分。ウェルドン、ホイッスルノッチ、ストレートシャンクなどがある。
- 基質: 切れ刃は一般的に超硬合金製だが、工具本体(基板)は高速度鋼(HSS)、超硬ソリッド、超硬チップ付きHSSなどの材料で作ることができ、コストと性能の組み合わせはさまざまである。
- コーティング: 耐摩耗性、硬度、潤滑性をさらに高めるため、超硬エンドミルには窒化チタン(TiN)、炭窒化チタン(TiCN)、窒化アルミニウムチタン(AlTiN)などの特殊コーティングが施されることが多い。
混乱を切り開くエンドミルの種類と用途
荒削りから仕上げまで:作業に適した工具の選択
エンドミル・タイプ | 特徴 | アプリケーション |
---|---|---|
スクエアエンドミル | - フラットカット・エンド、90度コーナー<br> - 四角いショルダーとスロットの作成に使用 | 汎用フライス加工、溝加工、ポケット加工 |
ボールエンドミル | - 半球状の刃先<br> - 丸みを帯びたエッジと輪郭 | 金型製作、ダイシンキング、3D輪郭加工 |
コーナーラジアスエンドミル | - 指定した半径で角を丸くする<br> - スクエアエンドミルとボールエンドミルの特徴を併せ持つ | 面取り、R付け、表面のブレンド |
ラフィングエンドミル | - アグレッシブな材料除去のための少なく深いフルート<br> - 高い金属除去率を実現する設計 | 大量の材料を素早く除去する粗加工 |
仕上げ用エンドミル | - 繊細な表面仕上げのための、より浅いフルート<br> - 軽切削と精密な公差用に設計 | 滑らかな表面と厳しい公差を実現する仕上げ作業 |
超硬エンドミル市場:精密さへの需要の高まり
世界の超硬エンドミル市場は、次のような要因によって大きな成長を遂げている:
- 自動化の進展: CNC加工とオートメーションの台頭は、高性能の切削工具を要求する。
- 航空宇宙の拡大 成長する航空宇宙産業は、軽量で高強度な素材の精密加工を必要としている。
- 医療機器の小型化: 医療機器の小型化、複雑化の傾向に伴い、微細加工能力が必要とされている。
TRUER: 精密加工ソリューションのパートナー
超硬切削工具のグローバルリーダー:比較分析
サプライヤー | 所在地 | 価格帯(1個あたり) | 特産品 |
---|---|---|---|
TRUER | 中国 | $15 – $150+ | カスタム設計の超硬ソリューション、幅広いコーティングと形状、用途に特化した専門知識 |
サンドビック・コロマント | スウェーデン | $20 – $200+ | 高性能超硬材種、革新的な工具設計、持続可能性の重視 |
ケナメタル | アメリカ | $18 – $180+ | 豊富な製品ポートフォリオ、多様なコーティングオプション、業界固有のソリューション |
イスカー | イスラエル | $16 – $170+ | 切りくず排出を最適化する先進の形状、高効率加工ソリューション |
注: 価格は概算であり、エンドミルのサイズ、タイプ、材質、コーティング、数量、その他の要因によって大きく異なる場合があります。
利点を天秤にかける:超硬エンドミルの利点と限界
情報に基づいた機械加工の決定:長所と短所
特徴 | メリット | 制限事項 |
---|---|---|
硬度と耐摩耗性 | - 卓越した硬度により、高硬度材の加工が可能<br> - 高い耐摩耗性により工具寿命を延長 | - 脆く、強い衝撃を受けると欠けたり割れたりすることがある。 |
切削速度と送り速度 | - ハイス工具に比べ、大幅な高速切削が可能<br> - 材料除去率の向上により生産性が向上 | - 振動を最小限に抑えるため、強固なセットアップとマシンが必要 |
精度と表面仕上げ | - 厳しい公差と微細な表面仕上げが可能<br> - 二次的な仕上げ作業の必要性を削減または排除する。 | - イニシャルコストはハイス工具より高くなる可能性がある |
刃先を越えて: エンドミルの性能に影響を与える要因
加工作業の最適化:主な検討事項
- 素材の互換性: 加工する材料に応じて適切な超硬材種とコーティングを選択することは、工具の寿命と性能にとって極めて重要です。
- 切断パラメータ: 効率的で効果的な加工には、工具と材料の特性に基づいて切削速度、送り速度、切り込み深さを最適化することが不可欠です。
- クーラントの選択: 適切なクーラント塗布は、熱を制御し、切削ゾーンを潤滑し、切屑排出を改善するのに役立つ。
- マシンの剛性: エンドミル、特に超硬ソリッドタイプは、工具のたわみや破損を防ぐため、振動を最小限に抑えた剛性の高い機械で最高の性能を発揮します。
TRUERを選ぶ理由
- 妥協のない品質: 当社では最高級の超硬素材を調達し、製造工程全体で厳格な品質管理措置を採用しています。
- アプリケーションの専門知識: 当社のエンジニアチームは、お客様の加工ニーズに最適なエンドミルを選択するための専門的なガイダンスを提供します。
- カスタマイズ能力: 特殊な形状、コーティング、サイズなど、ユニークなアプリケーション要件を満たすカスタム設計ソリューションを提供します。
- カスタマー・サクセスへのコミットメント: お客様との永続的なパートナーシップの構築に努め、卓越したサポートと技術支援を提供します。
よくある質問機械加工に関するお問い合わせ
1.用途に合った超硬エンドミルの選び方は?
加工する材料、要求される公差、表面仕上げ、希望する金属除去率、利用可能な機械能力を考慮してください。当社のテクニカルエキスパートにご相談いただければ、個別のご提案をさせていただきます。
2.エンドミルの摩耗の典型的な兆候と、工具寿命を最大限に延ばす方法は?
摩耗の兆候には、切削抵抗の増加、仕上げ面の劣化、切りくずの溶着などがある。切削パラメータを最適化し、クーラントを適切に塗布し、工具の過度な張り出しを避けることで、工具寿命を延ばすことができる。
3.特注形状やコーティングの超硬エンドミルはできますか?
はい、カスタムメイドのソリューションを専門としています。エンドミルの形状、コーティング、サイズなど、お客様のご要望にお応えします。
4.特注の超硬エンドミルをTRUERに注文する場合、納期はどのくらいかかりますか?
リードタイムは、デザインの複雑さ、注文数量、現在の生産能力によって異なります。当社の営業チームが、個別にリードタイムのお見積もりをいたします。
5.TRUERは、超硬エンドミルの選定や最適化に関する技術サポートやコンサルティングサービスを提供していますか?
もちろんです!当社の経験豊富なエンジニアチームが、材料選択のガイダンス、切削パラメータの最適化、トラブルシューティングの支援など、包括的な技術サポートを提供します。