はじめに
機械加工と製造の世界では、切削工具の材料の選択は、作業の効率、精度、および全体的な成功を決定する上で重要な役割を果たします。様々な材料がある中で カーバイド ブレージングチップは、そのユニークな利点により際立っています。このブログでは、超硬ブレージングチップが他の切削工具材料よりも好まれる説得力のある理由を掘り下げ、その優れた性能、耐久性、汎用性に焦点を当てます。詳細な説明、比較、実用的な洞察を通じて、超硬ブレージングチップが多くの産業で選ばれる理由を包括的に理解することを目指します。
超硬ろう付けチップを理解する
超硬ブレージングチップとは?
超硬ろう付けチップ は、超硬チップを工具本体にろう付けした切削工具で、通常はより軟らかい金属でできている。ろう付けプロセスでは、超硬チップと工具本体の間に強力な結合を形成するために金属フィラーを使用します。この組み合わせにより、超硬合金の硬度と耐摩耗性、工具本体材料の靭性と柔軟性が活用され、非常に効果的な切削工具が得られます。
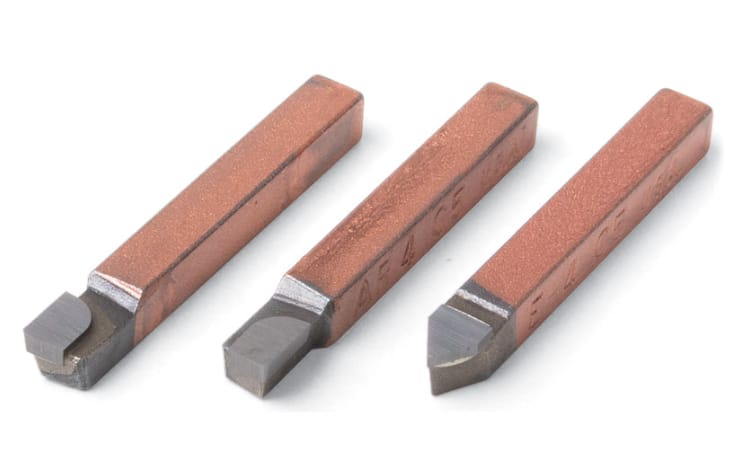
どのように作られているのか?
超硬ろう付けチップの製造工程には、いくつかの重要なステップがあります:
- 超硬チップの準備: 炭化タングステンのチップは、炭化タングステン粒子とコバルトなどの金属バインダーを混合し、プレスと焼結を行う粉末冶金法で製造され、所望の形状と硬度を形成します。
- ろう付けプロセス: 超硬チップは、次に金属フィラーを使って工具本体にろう付けされる。この工程では、溶加材が溶けて接合部に流れ込む温度まで部品を加熱し、強力で耐久性のある接合を実現します。
- 仕上げと品質管理: ろう付けされた工具は精密な寸法に仕上げられ、要求される仕様と性能基準を満たすために厳しい品質管理が行われる。
超硬ろう付けチップの主な利点
1.卓越した硬度と耐摩耗性
超硬ろう付けチップは、一般的に85~92HRA (ロックウェルAスケール) という非常に高い硬度で知られています。この硬度は優れた耐摩耗性につながり、超硬ブレージングチップは、硬い材料や研磨材を加工する場合でも、切れ味と切削効率を長期間維持することができます。
2.切削性能の向上
超硬ブレージングチップは、高い硬度と鋭利な切れ味により、変形や表面粗さを最小限に抑えながら正確なカットを行うことができます。その結果、完成品の品質が向上し、追加の機械加工工程の必要性が減少するため、時間とコストを節約できます。
3.高い熱安定性
炭化タングステンは熱安定性に優れているため、超硬ろう付けチップは高温でも硬度と構造的完全性を維持することができます。この特性は、切削工具の発熱が大きい高速加工において特に有利です。
4.素材を問わない汎用性
超硬ブレージングチップは汎用性が高く、以下のようなさまざまな材料を効果的に加工できます:
- スチールおよびステンレススチール: 高速度鋼の切断および仕上げ作業に最適。
- 非鉄金属: アルミニウム、真鍮、銅、その他の非鉄材料に適しています。
- 硬質合金: 航空宇宙産業や自動車産業で使用される硬質合金や超合金の加工が可能。
- プラスチックと複合材料: プラスチック、複合材料、その他の合成材料の切断と成形に効果的。
5.長い工具寿命
超硬ブレージングチップは、その優れた硬度と耐摩耗性により、高速度鋼(HSS)やコバルトなどの他の切削工具材料と比較して、工具寿命が大幅に長くなっています。そのため、工具交換やメンテナンスの頻度が減り、生産性の向上と運用コストの削減につながります。
6.耐腐食性と耐酸化性
超硬ろう付けチップは、優れた耐腐食性と耐酸化性を発揮し、過酷な作業環境でも安定した性能と長寿命を保証します。このため、腐食性物質にさらされることが多い石油やガスなどの産業での用途に適しています。
7.長期的な費用対効果
超硬ろう付けチップの初期コストは他の切削工具材料よりも高いかもしれませんが、寿命が長く、性能が優れているため、長期的には全体的なコストを抑えることができます。交換やメンテナンスの必要性が減少し、生産性が向上するため、超硬ブレージングチップは長期的に費用対効果の高いソリューションとなります。
他の切削工具材料との比較
1.高速度鋼(HSS)
高速度鋼は、その靭性と耐衝撃性で知られ、広く使用されている切削工具材料である。しかし、超硬ブレージングチップと比較すると、いくつかの点で不十分です:
プロパティ | 超硬ろう付けチップ | 高速度鋼(HSS) |
---|---|---|
硬度(HRA) | 85-92 | 60-70 |
耐摩耗性 | 高い | 中程度 |
熱安定性 | 素晴らしい | グッド |
工具寿命 | ロング | ショーター |
費用対効果 | 高い | 中程度 |
表1:超硬ろう付けチップと高速度鋼の比較
2.コバルト工具
コバルト工具は、高温に耐える能力と靭性で知られている。しかし、超硬ろう付けチップほどの硬度や耐摩耗性はありません:
プロパティ | 超硬ろう付けチップ | コバルト工具 |
---|---|---|
硬度(HRA) | 85-92 | 65-75 |
耐摩耗性 | 高い | 中程度 |
熱安定性 | 素晴らしい | 非常に良い |
工具寿命 | ロング | ショーター |
費用対効果 | 高い | 中程度 |
表2 超硬ブレージングチップとコバルト工具の比較
3.セラミックツール
セラミック工具は高い硬度と耐熱性を持つが、超硬ろう付けチップに比べて脆い:
プロパティ | 超硬ろう付けチップ | セラミックツール |
---|---|---|
硬度(HRA) | 85-92 | 90-95 |
耐摩耗性 | 高い | 非常に高い |
熱安定性 | 素晴らしい | 素晴らしい |
工具寿命 | ロング | ロング |
費用対効果 | 高い | 高い |
脆さ | 低い | 高い |
表3:超硬ブレージングチップとセラミック工具の比較
超硬ろう付けチップの用途
超硬ブレージングチップの汎用性と優れた性能は、幅広い用途に適しています。ここでは、超硬ろう付けチップが優れている主な分野をご紹介します:
- 自動車産業: エンジン部品、歯車、その他の重要部品の加工。
- 航空宇宙産業: 航空機製造に使用される高強度合金や複合材の切断と成形。
- 金型製作: 精密金型、金型、切削工具の製作。
- 医療機器製造: 高精度の手術器具やインプラントを製造。
- 石油・ガス産業 過酷な環境にさらされる部品の穴あけや機械加工。
- 金属加工: 旋盤加工、フライス加工、ドリル加工を含む一般的な機械加工作業。
- 木工: 木材や木質系材料の切断と成形。
- エレクトロニクス産業: 電子機器や電子回路の部品加工。
リスト1:超硬ブレージングチップの用途
他の材料ではなく超硬ブレージングチップを選ぶ理由
1.性能と精度
超硬ろう付けチップは、比類のない性能と精度を提供し、高品質の仕上げと正確な寸法を保証します。これは、航空宇宙や医療機器製造など、精度が最も重要な産業において極めて重要です。
2.耐久性と寿命
超硬ろう付けチップの卓越した硬度と耐摩耗性は、工具寿命の延長につながり、ダウンタイムとメンテナンスコストを削減します。この耐久性は、特に大量生産環境において有益です。
3.コスト効率
初期コストは高いものの、超硬ろう付けチップの長寿命と優れた性能により、全体的なコストは低くなります。そのため、長期的な使用に適した費用対効果の高いソリューションとなっている。
4.多用途性
超硬ろう付けチップは汎用性が高く、さまざまな材料や用途に対応できます。この適応性により、工具在庫の合理化を目指すメーカーにとって理想的な選択肢となります。
5.高速加工
超硬ブレージングチップの熱安定性と硬度は、高速加工に適しており、生産性の向上とサイクルタイムの短縮を実現します。
結論
超硬ろう付けチップは、他の切削工具材料と比較して多くの利点があり、多くの産業で好まれています。その卓越した硬度、耐摩耗性、熱安定性、および汎用性は、優れた性能、工具寿命の延長、およびコスト効率につながります。高強度合金、非鉄金属、プラスチック、複合材料の加工のいずれにおいても、超硬ブレージングチップは、最適な結果を得るために必要な精度と信頼性を提供します。超硬ブレージングチップを選択することで、メーカーは作業効率を高め、ダウンタイムを削減し、最終的に高品質な製品を実現することができます。