概要
超硬チップソー は、鋸刃の効率、精度、耐久性を決定づける切削工具の重要な部品です。これらのチップの形状と設計は、切削性能と耐摩耗性に重要な役割を果たします。このブログでは、超硬チップソーの設計の複雑な詳細を掘り下げ、さまざまな幾何学的要因がその機能性にどのように影響するかを探ります。木工、金属加工、または精密切削を必要とするその他の業界を問わず、これらの要因を理解することで、工具の性能と寿命を大幅に向上させることができます。
詳細紹介
超硬チップソーとは?
超硬チップソーは、鋸刃の歯に取り付けられる小さくて硬い部品です。硬度と耐摩耗性で知られる炭化タングステンから作られています。これらのチップは、鋸刃が高精度と最小限の摩耗で様々な材料を切断することができます。これらのチップの設計と形状は、性能を最適化するために細心の注意を払って設計されています。
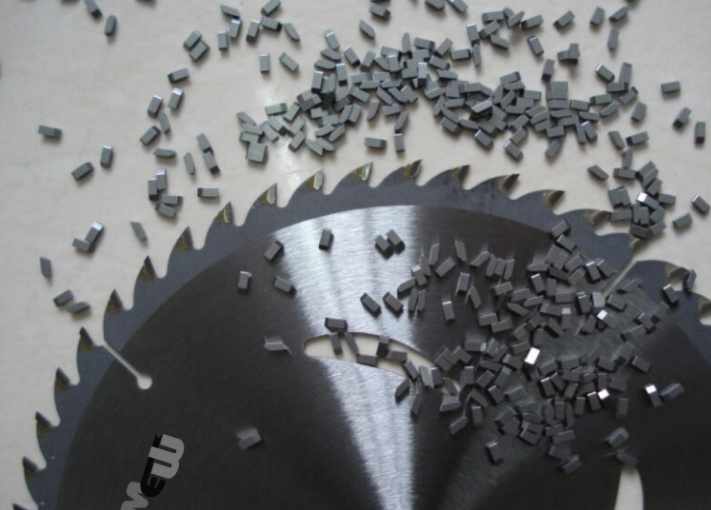
ジオメトリーは切削性能にどう影響するか?
超硬チップソーの形状には、形状、角度、刃先の構成が含まれます。これらの要素を総合的に判断することで、チップの切断効率が決まります。主な幾何学的側面は以下の通りです:
- 先端形状:チップの全体的な形状は、材料との相互作用に影響する。一般的な形状には、平らなチップ、台形のチップ、丸いチップなどがあり、それぞれ異なる切断特性を提供します。
- レーキ角度:すくい角とは、刃先と被削材のなす角度のこと。正のすくい角は、切断を容易にし、より小さな力で済みますが、負のすくい角は、より大きな強度と耐久性をもたらします。
- クリアランス・アングル:ティップの背面と素材との間の角度で、ティップが素材と擦れるのを防ぎ、摩擦と発熱を軽減します。
- エッジ半径:刃先の鋭さは半径で定義され、切りやすさと仕上げの質に影響する。刃先が鋭いほど切れ味は良くなりますが、磨耗が早くなります。
幾何学的要因とその影響
先端形状とプロファイル
超硬チップソーの形状とプロファイルは、その切断効率と達成できる切断の種類を決定します。ここでは、一般的な形状とその影響について説明します:
- フラットチップ:滑らかで連続的な切れ味を提供し、繊細な仕上げに最適。
- 台形チップ:切れ味と耐久性のバランスが良く、一般的な切断に適しています。
- ラウンドチップ:チップの強度と耐久性を高め、より硬い材料の切断に最適。
レーキ角度
すくい角は、切りやすさと工具寿命に大きく影響する:
- ポジティブ・レーキ・アングル:切削力とエネルギー消費量を削減し、切削効率を向上させます。木材やプラスチックのような柔らかい素材に適しています。
- ネガティブ・レーキ角:先端の強度と耐久性が向上し、金属のような硬い研磨材の切断に最適。
クリアランス・アングル
クリアランス角は、摩擦と熱の蓄積を減らすのに役立つ:
- 大きなクリアランスアングル:摩擦と熱を最小限に抑え、工具寿命を延ばします。高速切削用途に有効です。
- 小さなクリアランス:刃先をより強くサポートし、耐久性を高めるが、摩擦や熱を増加させる可能性がある。
エッジ半径
刃先半径は、切れ味と耐摩耗性に影響する:
- シャープ・エッジ:きれいで正確なカットができるが、消耗が早い。
- ブラント・エッジ:耐久性と耐摩耗性が向上し、粗切削用途に適しています。
耐摩耗設計を最適化するには?
超硬チップソーを長持ちさせるには、耐摩耗性が重要です。設計を最適化するには、切れ味と耐久性のバランスを取る必要があります。主な検討事項は以下の通りです:
- 素材構成:高品質のタングステンカーバイドと適切なバインダー材を使用し、耐摩耗性を向上。
- コーティング:窒化チタン(TiN)やダイヤモンドライクカーボン(DLC)のような高度なコーティングを施すことで、摩耗を減らし、工具の寿命を延ばします。
- 先端形状:被削材や切削条件に応じて適切なすくい角、逃げ角、刃先半径を選択することで、最適な耐摩耗性を実現します。
製造工程と形状への影響
超硬チップソーの製造工程も、その形状や性能に影響を与えます。主な工程は以下の通りです:
- 粉体混合:炭化タングステン粉末は、金属バインダー(通常はコバルト)と混合される。
- プレス:混合物は高圧金型を使ってプレスされ、先端の形状が決定される。
- 焼結:プレスされた形状は、焼結炉で高温に加熱され、炭化物粒子同士が結合される。
- 研磨:焼結チップは、精密な寸法に研磨され、エッジ半径と全体的な形状に影響を与えながら研がれます。
- ろう付け:完成したチップは鋸刃の本体にろう付けされ、確実で耐久性のある取り付けを保証します。
表:幾何学的要因と切削性能への影響
幾何学的係数 | 説明 | 切削性能への影響 | 耐摩耗性への影響 |
---|---|---|---|
先端形状 | 先端の全体的な形状 | 切断特性と効率を決定する | 材料の硬度による耐久性への影響 |
レーキ角度 | 先端面と素材との角度 | 正の角度は切断力を低減し、負の角度は強度を高める | 正の角度は摩耗を早め、負の角度は耐久性を高める。 |
クリアランス・アングル | チップバックと素材の間の角度 | 大きな角度が摩擦と熱を低減 | 小さなアングルでエッジをサポート |
エッジ半径 | 刃先の鋭さ | よりシャープなエッジが、よりクリーンなカットを実現 | 鈍いエッジが耐摩耗性を高める |
説明:この表は、超硬チップソーの幾何学的要因とその説明、および切削性能と耐摩耗性への影響をまとめたものです。これらの要因を理解することは、特定の用途に適したチップ設計を選択するのに役立ちます。
アプリケーション
超硬チップソーは、さまざまな産業や用途で使用されており、それぞれに特有の形状設計が役立っています。主な用途をいくつかご紹介します:
- 木工:
- 広葉樹と針葉樹の伐採。
- 精密な建具とキャビネット
- 木材の表面に繊細な仕上げを施す。
- 金属加工:
- アルミニウムや銅などの非鉄金属の切断。
- ステンレス鋼のような硬い金属の加工。
- 金属部品や構造物の製作
- プラスチック切断:
- プラスチックシートや部品の切断、成形。
- 精密な寸法のプラスチック製品を製造。
- 建設:
- コンクリート、石工、その他の建築資材の切断。
- 建築部品の製造。
- 自動車産業:
- 自動車部品製造。
- 金属およびプラスチック部品の切削加工。
- 航空宇宙:
- 航空宇宙材料の精密切断
- 航空機部品の製造
- 家具製造:
- 木製および金属製の家具部品の切断と成形。
- 家具の表面を美しく仕上げる。
長所と短所の表
表:さまざまな幾何学的設計の利点と限界
アスペクト | フラットチップ | 台形チップ | ラウンドチップ |
---|---|---|---|
切断効率 | スムーズで連続的なカットを可能にする高さ | 汎用切断用バランス | 中程度、硬い素材に適している |
耐久性 | 中程度 | 高い | 非常に高い |
精密 | 非常に高い | 高い | 中程度 |
耐摩耗性 | 中程度 | 高い | 非常に高い |
申し込み | 木工と仕上げ | 汎用切断 | 硬い素材や研磨材の切断 |
説明:この表は、さまざまな形状の超硬チップソーの利点と制限を比較したものです。各設計には独自の利点があり、特定の用途や材料に適しています。
よくある質問超硬チップソーの形状に関するお問い合わせ
1.広葉樹のカットに最適なすくい角は?
広葉樹の場合、切削性能と耐摩耗性のバランスをとるため、すくい角はややマイナス(-5~-10度程度)にするのが一般的です。
2.ガレットデザインは切り屑排出にどのような影響を与えますか?
より広く、より深いガレットは、切り屑を除去するためのより広いスペースを提供し、針葉樹やプラスチックのような大きな切り屑を生成する材料を切断する際に不可欠です。
3.チップブレーカーの目的は何ですか?
チップブレーカーは、切りくずを細かく砕くことで、切りくずがガレットに詰まるのを防ぎ、熱の蓄積を抑えて工具の寿命を延ばします。
4.コーティングはどのように超硬チップソーの性能を向上させるのか?
TiNやAlTiNのようなコーティングは、硬度を高め、摩擦を減らし、耐熱性を向上させ、工具寿命の延長と切削性能の向上につながる。
5.鋸刃の超硬チップの形状に関する情報はどこで入手できますか?
TRUER は、すくい角、逃げ角、その他の特徴など、先端の形状に関する詳細情報を提供します。この情報は、ブレードのパッケージまたは製品詳細ページに記載されています。
超硬チップソーを安く買いたいですか?クリックしてください これ.