現場での効率化:優れたパフォーマンスを実現する2つのキー超硬ボタン設計
重要なエネルギー源としての石炭の絶え間ない需要には、堅牢で効率的な採掘作業が必要である。この厳しい産業の中心には 産炭 カーバイド ボタンこのガイドでは、地下および地表の石炭採掘の過酷な条件に耐えるように設計された、2つの主要なボタン設計に焦点を当てています。このガイドでは、次の2つの主要なボタン設計に焦点を当てています。円錐形 そして きのこ型-そのユニークな利点と、石炭採掘アプリケーションにおける生産性の最大化とダウンタイムの最小化にどのように貢献するかを紹介する。
炭鉱で超硬ボタンが欠かせない理由
普通のウェアパーツを超えて:価値提案を理解する
- 比類なき硬度: このボタンの芯材である炭化タングステンは、ほとんどの金属を凌駕し、石炭や周辺の岩盤の硬度を大幅に上回る、並外れた硬度を持つ。
- 優れた耐摩耗性: この固有の硬度は卓越した耐摩耗性につながり、超硬製ボタンが石炭採掘中に遭遇する研磨力に耐え、工具寿命を延ばし、メンテナンスコストを削減します。
- 耐衝撃性: 石炭採掘作業には、大きな衝撃と衝撃荷重が伴います。超硬製ボタンは、これらの力を吸収するように設計されており、早期故障を防ぎ、安定した性能を保証します。
円錐型とキノコ型:デザインの違いを読み解く
形状が機能を決定する:形状がパフォーマンスに与える影響
1.円錐形のボタン:
- 特徴 このボタンは先が尖った円錐形をしており、攻撃的な貫通のために設計されている。
- メリット 硬い石炭層や岩盤の切断・破壊に優れ、高い掘削速度と効率的な材料除去を実現。
- こんな人に最適 回転ドリル用途、連続坑夫用カッティングピック、および集中的なカッティングアクションを必要とするその他のツール。
2.キノコ型のボタン:
- 特徴 このボタンは、ドーム型またはマッシュルームのような特徴的な形をしており、上面は広く平らになっている。
- メリット 浸透性と耐摩耗性のバランスがとれており、切断と破砕の両方の作用を伴う用途に適している。また、表面積が広いため、摩耗を均一に分散させることができます。
- こんな人に最適 ロードヘッダ、剪断機、および切断、削り取り、破砕の組み合わせが必要なその他の石炭抽出装置。
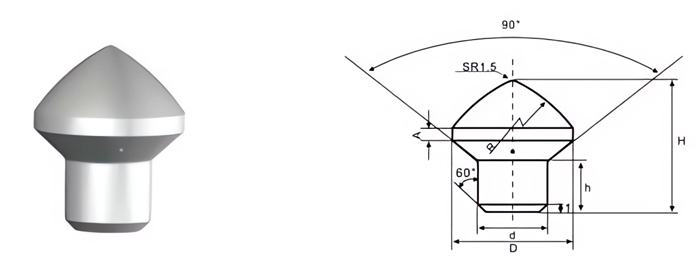
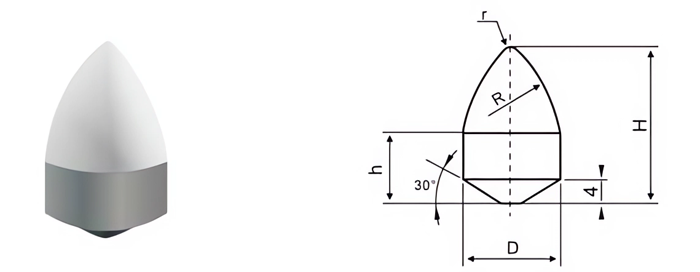
技術仕様:ボタンの特性の比較
コンポジションからスタンダードへ:主要データ
特徴 | 円錐形のボタン | きのこ型ボタン |
---|---|---|
タイプ | 円錐形 | マッシュルーム型 |
構成 | コバルト(Co)またはニッケル(Ni)バインダー付き炭化タングステン(WC) | コバルト(Co)またはニッケル(Ni)バインダー付き炭化タングステン(WC) |
硬度(HV30) | 1500 – 1900 | 1450 – 1850 |
横方向の破断強度 (N/mm²) | 1900 – 2600 | 1850 – 2550 |
耐衝撃性 | 非常に良い | グッド |
耐摩耗性 | ペネトレーションとカッティングの用途に非常に優れている。 | 耐摩耗性と耐貫通性のバランスが良い |
サイズと形状 | 様々な直径と先端角度をご用意 | 様々な直径とドームの高さをご用意 |
グレードと基準 | ISO、ASTM、その他の関連業界標準に準拠 | ISO、ASTM、その他の関連業界標準に準拠 |
石炭採掘でのアプリケーション:それぞれのボタンタイプが得意とするところ
抽出からマテリアルハンドリングまで:さまざまな使用例
- 地下石炭採掘:
- 連続採掘者: 円錐形のボタンは、石炭層での積極的な切断能力のため、連続採掘機の回転ドラムによく使用される。
- ロードヘッダー キノコ型のボタンは、耐摩耗性と耐貫通性のバランスから、石炭を切削しながら同時に装入するロードヘッダーで好んで使用されることが多い。
- ロングウォール採鉱: 円錐形とマッシュルーム形の両方のボタンがロングウォール・シェアラーに使用されており、特定の地質条件と切断要件によって選択される。
- 地表炭鉱:
- 掘削と発破: 円錐形のボタンは、その効率的な貫通能力により、地表鉱山での発破孔掘削用のドリル・ビットに使用されている。
- ドラッグラインのバケット きのこ型のボタンは、石炭をすくい上げ積み込む際の研磨力に耐えるため、ドラッグラインのバケットの歯や刃先によく組み込まれている。
比較分析:TRUERと業界リーダーとの比較
市場をナビゲートする横並び比較
サプライヤー | 所在地 | 国名 | 価格帯(1個あたり) | 特産品 |
---|---|---|---|---|
TRUER | 中国、上海 | 中国 | $10 – $50+ | カスタム設計ソリューション、迅速なプロトタイピング、卓越したカスタマーサポート |
エレメント・シックス | グローバル本社英国、ロンドン | 英国 | $16 – $65+ | 先端材料科学、極限摩耗用途向け高性能超硬合金グレード |
ケナメタル | グローバル本社ペンシルベニア州ピッツバーグ | アメリカ | $13 – $55+ | 幅広い標準ボタンとカスタムボタンのデザイン、豊富な業界経験 |
サンドビック・コロマント | グローバル本社サンドビケン、スウェーデン | スウェーデン | $15 – $70+ | 革新的な金型ソリューション、持続可能性と性能の最適化に注力 |
注: 価格は概算であり、ボタンのサイズ、形状、等級、数量、その他の要因によって大きく異なる場合があります。手頃な価格で耐食性、耐久性のある超硬ボタンを購入したい場合は、クリックしてください。 これ.
利点と限界:トレードオフを天秤にかける
情報に基づいた決断を:各ボタンの種類をバランスよく見る
ボタンタイプ | メリット | 制限事項 |
---|---|---|
円錐形 | - 硬い石炭や岩石に理想的な高い浸透率<br> - 効率的な材料除去により、穴あけや切断の高速化を実現 | - 極端な横荷重がかかると破損しやすい。<br> - 大きな擦過や破砕を伴う用途では、マッシュルーム型ボタンよりも高い摩耗率 |
マッシュルーム型 | - 浸透性と耐摩耗性のバランスが良い<br> - より広い表面積が摩耗をより均一に分散<br> - カッティング、スクレイピング、クラッシュアクションの組み合わせに適している。 | - 円錐形ボタンと比較して貫通率が低い<br> - 非常に硬い地層での積極的な切断を必要とする用途には適していません。 |
基本を超えて:ボタンの性能と寿命に影響を与える要因
ROIの最大化:主な検討事項
- 超硬グレードの選択: 炭化タングステンの適切なグレードを選択することは、石炭や岩石の硬度、耐衝撃性の要件、研磨鉱物の存在などの要因を考慮する上で非常に重要です。
- ボタンの取り付け方法: ボタンと採掘工具を確実に接合し、ボタンの早期脱落を防ぐには、適切なろう付けまたは溶接技術が不可欠です。
- 動作パラメータ: 切削速度、切込み深さ、切削油剤の使用などの要因は、ボタンの摩耗率や全体的な性能に大きく影響します。
TRUERを選ぶ理由
石炭採掘の効率化におけるパートナー
TRUERは、単なるカーバイドボタンにとどまらず、お客様の石炭採掘作業を最適化するためのソリューションを提供することをお約束します。業界のリーダーたちがTRUERを選ぶ理由はここにあります:
- 揺るぎない品質: 当社では、最高グレードのタングステンカーバイドのみを調達し、製造工程全体にわたって厳格な品質管理措置を遵守しています。
- カスタマイズの専門家: 当社のエンジニアチームは、お客様の石炭採掘に関する特定の課題に対応するカスタムボタンソリューションの設計と製造に優れています。
- ラピッドプロトタイピングと生産: 当社は、鉱業におけるダウンタイムを最小限に抑えることの重要性を理解しています。当社の合理化されたプロセスにより、プロトタイプや生産ランを効率的に提供することができます。
- 卓越したカスタマーサポート: お客様の成功のために、専門家による技術指導とサポートを提供します。
よくある質問炭鉱ボタンに関するお問い合わせ
1.特定の石炭採掘用途に適した超硬ボタンの種類とグレードを選ぶには?
最適なボタンの種類と等級は、石炭層の硬度、使用する採掘機器の種類、浸透性と耐摩耗性の望ましいバランスなどの要因によって異なります。個別のガイダンスについては、当社の技術専門家にご相談されることをお勧めします。
2.円錐形やマッシュルーム形のボタンに見られる典型的な摩耗パターンにはどのようなものがありますか?
摩耗のパターンはボタンの種類と使用条件によって異なります。一般的な摩耗の兆候としては、円錐形のボタンでは先端の鈍化や欠け、マッシュルーム型のボタンでは上面の平坦化や溝が挙げられます。定期的な点検と、確立された摩耗限界に基づく交換が重要です。
3.TRUERは、厳しい炭鉱環境で耐摩耗性や耐腐食性を高める特殊コーティングを施した超硬ボタンを提供できますか?
はい、研磨鉱物や腐食剤、その他の厳しい条件下で、ボタンの性能と寿命をさらに向上させるさまざまな表面処理とコーティングを提供しています。
4.TRUERに特注の超硬ボタンを注文する場合の一般的なリードタイムはどのくらいですか?
カスタムオーダーのリードタイムは、デザインの複雑さや必要な数量によって異なります。個別のお見積もりとリードタイムのお見積もりについては、営業チームにお問い合わせください。
5.TRUERは、石炭採掘用途でのカーバイドボタンの使用とメンテナンスに関して、現場での技術サポートやトレーニングを提供していますか?
当社は、お客様が当社製品を最大限に活用し、石炭採掘作業を最適化できるよう、現場でのコンサルティング、トレーニングプログラム、トラブルシューティング支援など、包括的な技術サポートを提供しています。