はじめに獣を飼いならす鋳鉄の精密加工
鋳鉄は、その優れた強度と費用対効果により、数え切れないほどの産業用アプリケーションの頂点に君臨しています。しかし、この頑丈な材料を加工するには、その研磨性と硬く不連続な切り屑を形成する傾向から、独特の課題があります。参入 タイプG カーバイド ロー付けチップ鋳鉄加工の複雑さを克服するために設計された専用工具は、卓越した性能、工具寿命、仕上げ面粗さを実現します。
この記事では、タイプG超硬ブレージングチップの世界を掘り下げ、そのユニークな特性や利点、鋳鉄部品の加工で精度と効率を達成するための最適な選択肢である理由を探ります。
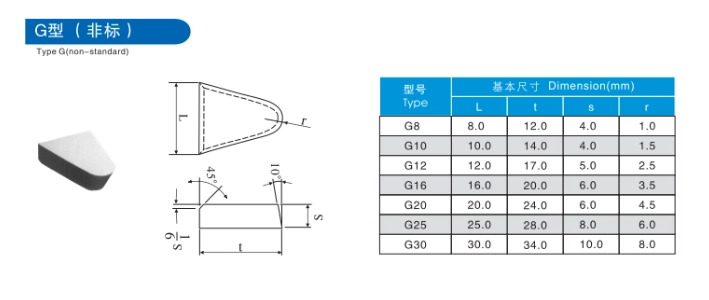
鋳鉄の課題:摩耗、熱、切り屑の形成
タフな機械加工の地形をナビゲートする:
鋳鉄の加工には、従来の切削工具を急速に劣化させる可能性のある3つの課題があります:
- 高い耐摩耗性: 鋳鉄マトリックス内にグラファイトフレークが存在すると、本質的に研磨材となり、工具の摩耗を促進し、刃先の切れ味を低下させる。
- 発熱: 鋳鉄は研磨性が高いため、加工中に大きな熱が発生し、工具の摩耗を助長し、寸法精度に影響を与える可能性があります。
- 不連続なチップ形成: 鋳鉄は脆いため、小さな不連続な切り屑が形成され、切削ゾーンに捕捉される可能性があり、摩擦の増加、熱の蓄積、潜在的な工具の損傷につながる。
タイプG超硬ろう付けチップ:鋳鉄用
耐摩耗性とチップコントロールの解剖学:
タイプGの超硬ろう付けチップは、鋳鉄加工の課題に対処するために特別に設計されており、次のような特徴があります:
- タフな超硬グレード: タイプGのチップは、靭性と耐摩耗性を強化した超硬材種を採用しており、鋳鉄の過酷な切削環境にも耐えることができます。
- 鋭い刃先: 鋭い切れ刃を維持することは、効率的な切りくず形成と鋳鉄加工での発熱を最小限に抑えるために極めて重要です。タイプGのチップは、きれいな剪断作用を促進するために、鋭くポジティブなすくい角を特徴としていることがよくあります。
- チップコントロール機能: 多くのType Gチップには、鋳鉄で発生しやすい長くて筋状の切りくずを分断するように設計されたチップブレーカーや切りくず制御形状が組み込まれています。これらの機能は、効率的な切り屑排出を促進し、熱の蓄積を抑え、切り屑の溶着を防ぎます。
タイプG超硬ブレージングチップが鋳鉄加工で威力を発揮する7つの理由
自信を持って困難に打ち勝つ:
タイプGの超硬ろう付けチップの特殊な設計と材料特性は、いくつかの重要な利点につながります:
- 卓越した耐摩耗性: その強靭な超硬材種と鋭い切れ刃は、鋳鉄の加工時に発生する高研磨摩耗に耐えることができ、工具寿命を大幅に延ばすことができます。
- 効率的なチップ制御: チップブレーカの形状とポジティブなすくい角は、効率的な切り屑の形成と排出を促進し、熱の蓄積を抑え、切り屑の溶着を防ぎ、仕上げ面粗さを向上させます。
- 表面仕上げの向上: 鋭利な切れ刃、効率的な切りくず処理、切削抵抗の低減の組み合わせにより、G型チップは鋳鉄で驚くほど良好な仕上げ面を実現し、多くの場合、二次的な仕上げ加工が不要になります。
- 切断力の低減: 鋭い切れ刃とポジティブなすくい角は、切削力を最小限に抑え、工具、工作機械、被削材へのストレスを軽減する。
- 生産性の向上: 工具寿命の延長、ダウンタイムの削減、より高い切削速度と送りを達成する能力は、生産性の向上とサイクルタイムの短縮に貢献します。
- 要求の厳しいアプリケーションにおける費用対効果: タイプGチップによる工具寿命の延長と生産性の向上は、特に大量の鋳鉄加工において、大幅なコスト削減につながります。
- 鋳鉄加工の多様性: タイプGのチップは、荒加工、仕上げ加工、旋削加工、フライス加工、ドリル加工、ボーリング加工など、幅広い鋳鉄加工に適しています。
タイプG超硬ろう付けチップの用途
鋳鉄加工における精度と効率が出会う場所:
タイプGの超硬ブレージングチップは、幅広い鋳鉄加工用途に最適です:
- 自動車産業: エンジンブロック、シリンダーヘッド、トランスミッションケースなど、鋳鉄の強度とコスト効率が高く評価される部品の加工。
- 重機製造: 建設機械、農業機械、鉱山機械のギア、ハウジング、その他重要部品を製造。
- ポンプとバルブの製造 ポンプハウジング、バルブボディ、その他流体の流れや圧力の封じ込めが重要な部品に、複雑な形状や滑らかな表面を作ります。
正しいタイプG超硬ブレージングチップの選択:考慮すべき要素
鋳鉄を極めるための工具選択の最適化:
最適なタイプGの超硬ろう付けチップを選択するには、いくつかの要素を慎重に検討する必要があります:
- 鋳鉄の種類: 鋳鉄の等級によって、硬度、強度、切削性が異なるため、超硬合金等級とコーティングの選択に影響を与えます。
- 加工作業: 荒加工、仕上げ加工、旋削加工、フライス加工、ドリル加工、ボーリング加工など、特定の加工作業は、チップの形状、サイズ、チップブレーカの設計の選択に影響を与えます。
- 切断条件: 希望する切削速度、送り、切り込み深さ、断続切削の有無は、チップの選択に影響する。
- 工作機械の能力: 工作機械の剛性とパワーは、達成可能な切削パラメータや、適切なチップサイズと形状の選択に影響を与える可能性がある。
タイプG超硬ろう付けチップの選択:簡易ガイド
選択プロセスを支援するために、タイプGの先端形状別の典型的な用途と考慮点をまとめた表を以下に示す:
タイプG 先端形状 | 代表的なアプリケーション | 主な検討事項 |
---|---|---|
チップブレーカー付きラウンドインサート | 汎用旋削、フェーシング、ボーリング | 良好な切りくず処理と、切れ味と強度のバランスを提供する。 |
チップブレーカー付きスクエアインサート | フライス加工、ショルダーフライス加工、溝加工 | 強力な切れ刃と良好な切りくず排出性で、断続切削に対応 |
ポジティブ・レーキ付き三角形インサート | プランジフライス、ランピング、面取り | アグレッシブなカッティングやプランジング作業に強力な切れ刃を提供します。 |
タイプG超硬ろう付けチップに関するよくある質問
Q1:缶タイプG 超硬ブレージングチップ 鋳鉄以外の材料の加工に使えますか?
A1: タイプGチップは鋳鉄用に特別に設計されていますが、他の材料、特にダクタイル鋳鉄や圧縮黒鉛鋳鉄のような類似した特性を持つ材料の加工にも使用できます。しかし、その性能は特定の材料や切削条件によって異なる場合があります。
Q2: タイプGの超硬ろう付けチップの摩耗の兆候は何ですか?
A2: 一般的な摩耗の兆候には、切れ刃の逃げ面摩耗、すくい面のクレーター摩耗、切れ刃のチッピングや丸みなどがある。鋳鉄の加工では、摩耗は表面仕上げの悪化、切削抵抗の増加、切りくずの形成の変化として現れます。
Q3: タイプGの超硬ブレージングチップを使用して鋳鉄を加工する場合、工具寿命を最大限に延ばすにはどうすればよいですか?
A3: 重要な要素には、用途に適したチップ形状と材種の選択、切削パラメータの最適化(鋳鉄の材種と工作機械の能力を考慮)、適切な切削油剤の塗布の確保、機械のセットアップの厳密な維持などがある。
Q4: タイプGの超硬ブレージングチップにおけるチップブレーカーの役割は何ですか?
A4: チップブレーカーは、鋳鉄で発生しやすい長くて筋状の切屑を分断するように設計されており、効率的な切屑排出を促進し、熱の蓄積を抑え、工具とワークの両方に損傷を与える切屑の溶着を防ぎます。
Q5: 鋳鉄の加工で、丸チップと角チップのG型チップを選択するのはどのような場合ですか?
A5: 鋳鉄の汎用旋削加工、フェーシング加工、ボーリング加工には、チップブレーカ付き丸形チップがよく使用され、断続切削が多いフライス加工、ショルダーフライス加工、溝入れ加工には、チップブレーカ付き角形チップが適している。