超硬チップ は、一見シンプルに見えますが、その控えめな外観の下には、複雑な形状と設計の世界があり、各要素は切削性能を最適化するために綿密に設計されています。これらの幾何学的特徴が加工結果にどのような影響を与えるかを理解することは、作業に適した超硬チップを選択し、優れた結果を得るための鍵となります。
このブログでは、次のような魅力的な関係を掘り下げている。 超硬インサート形状 とカッティング・パフォーマンス 7つの重要なデザイン要素 と加工結果への影響について説明した。
1.レーキ角度:切り屑の流れと切削力に影響する
すくい角は、超硬チップのすくい面(切り屑に面する面)と被削材に垂直な線との間で測定され、切り屑の形成と切削力に重要な役割を果たす。
- ポジティブなレーキアングル: 切り屑の流れを促進し、切削抵抗の低減と少ない動力で加工が可能。柔らかい材料の加工や、微細な仕上げ面を得るのに最適。
- 負のレーキ角: 硬い材料の加工や、耐衝撃性が重要な断続切削に適している。しかし、負のすくい角は、より高い切削力を発生させる。
2.クリアランスアングル:摩擦と熱の蓄積を防ぐ
超硬チップの逃げ面(加工面に面する面)と被削材の接線との間に形成される逃げ角は、工具と被削材との間に十分なクリアランスを確保し、擦れや過度の発熱を防ぐ。
- より大きなクリアランスアングル: 摩擦と熱の蓄積を低減し、特に切粉溶着を起こしやすい軟質材や延性材の加工に有効。
- 小さいクリアランス・アングル: 切れ刃のサポートが強化され、高硬度材の加工や重切削時の工具寿命が向上。
3.チップブレーカーの形状チップの形成と排出を制御する
超硬チップのすくい面に組み込まれた溝や段差であるチップブレーカーは、切り屑の形成を制御し、切り屑の流れを切削領域から遠ざけるために非常に重要です。
- ワイドでシャローなチップブレーカー: 短くカールした切りくずの形成を促進し、高切削速度での延性材料の加工に最適。
- 狭く、深いチップブレーカー: より硬い材料の加工や、切りくず処理が重要な荒加工に適しています。
4.刃先の準備:刃先強度と表面仕上げに影響する
超硬チップの刃先は様々な方法で加工でき、それぞれが刃先強度、仕上げ面、工具寿命に影響する。
- ホーンド・エッジ: 非常にシャープな研磨エッジが得られ、精緻な表面仕上げや厳しい公差を実現するのに理想的。しかし、ホーニングエッジはよりデリケートで、欠けやすい。
- 面取りされたエッジ: 切れ刃を強化し、特に研磨材の加工時や断続切削時のチッピングのリスクを低減。
- ラウンドエッジ: 刃先強度と表面仕上げのバランスが良く、幅広い加工用途に適している。
5.コーナーラジアス:強さとシャープさのバランス
コーナR(すくい面と逃げ面の交点にある丸みを帯びたエッジ)は、チップの強度、切れ味、さまざまな切削条件に対応する能力に影響する。
- シャープコーナー(小半径): 最も鋭い切れ刃を提供し、厳しい公差や複雑な形状を実現するのに理想的。ただし、鋭いコーナーはチッピングの影響を受けやすい。
- 角丸(ラージラジアス): 強度と耐チッピング性が向上し、重切削加工や硬い材料の加工に特に有効。
6.インサート厚さ:工具の剛性と安定性の決定
超硬チップの厚さは、その剛性と切削力によるたわみに対する抵抗力に影響する。
- 厚めのインサート: より高い剛性と安定性を提供し、重切削作業や、たわみが精度に影響する大型ワークの加工に不可欠。
- より薄いインサート: 切削抵抗が少なく、消費電力を削減できるため、繊細な部品の加工や、小型でパワーの弱い機械の使用に適している。
7.コーティング技術:耐摩耗性と性能の向上
超硬チップは、耐摩耗性を高め、摩擦を減らし、全体的な切削性能を向上させるために、しばしば薄い硬質材料でコーティングされる。
- 窒化チタン(TiN): 硬度を高め、摩擦を低減し、耐酸化性を向上させる汎用性の高いコーティングで、幅広い加工用途に適している。
- 炭窒化チタン(TiCN): TiNよりもさらに高い硬度と耐摩耗性を持ち、研磨材の加工や高速加工に特に有効。
- 酸化アルミニウム(Al2O3): 耐熱性と耐摩耗性に優れ、高温合金の加工やドライ加工に最適。
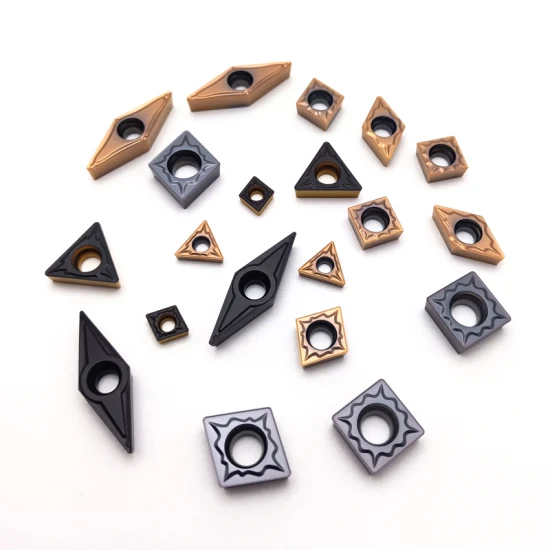
超硬インサート形状:クイックリファレンスガイド
特徴 | 説明 | 切断性能への影響 |
---|---|---|
レーキ角度 | すくい面と垂線の角度 | 切りくずの流れ、切削力、仕上げ面に影響 |
クリアランス・アングル | フランク面とワーク接線との角度 | 摩擦を防ぎ、熱の蓄積を抑制 |
チップブレーカー | レーキ面の溝や段差 | 切り屑の形成と排出をコントロール |
最先端の準備 | 本磨き、面取り、または丸め加工 | 刃先強度、表面仕上げ、工具寿命に影響 |
コーナー半径 | すくい面と側面が交差するエッジは丸みを帯びている。 | 強さと切れ味のバランス |
インサート厚さ | インサート全体の厚さ | 工具の剛性と安定性を決定する |
コーティング | 表面に塗布された薄くて硬い素材 | 耐摩耗性の向上、摩擦の低減、性能の向上 |
よくある質問超硬インサート形状に関するご質問
1.自分の用途に適したすくい角を選ぶには?
適切なすくい角を選択するかどうかは、加工する材料と希望する切削条件によって決まる。柔らかい素材や仕上げ加工では、一般的に正のすくい角が有効ですが、硬い素材や荒加工では負のすくい角が必要になることがよくあります。
2.機械加工における切りくず処理の重要性とは?
効果的な切りくず処理は、安定した切削性能を維持し、ワークや工具を損傷させる切りくずの堆積を防ぎ、作業者の安全を確保するために極めて重要です。適切に設計されたチップブレーカは、切屑の流れを切削領域から遠ざける重要な役割を果たします。
3.どのような場合に、角の丸いインサートと鋭角のインサートを使い分けるべきですか?
シャープコーナーチップは、厳しい公差や複雑な形状を実現するのに理想的ですが、チッピングの影響を受けやすくなります。角丸チップは強度が増し、重切削加工や硬い材料の加工に適しています。
4.コーティングされた超硬チップを使用する利点は何ですか?
コーティング 超硬インサート は、耐摩耗性の向上、摩擦の低減、耐熱性の改善、切削性能の向上など、数多くの利点を提供します。さまざまなコーティングは、特定の加工用途や材料に合わせて調整されます。
5.チップの厚みは工具剛性にどのように影響しますか?
厚いチップは剛性が高く、切削力によるたわみに対する耐性が高いが、薄いチップは切削抵抗が低い。適切なチップ厚さの選択は、加工作業、ワークサイズ、機械の能力によって異なる。