ミクロン単位が重要視され、効率が最優先される精密機械加工の世界、 ストレート・クーラント・ホール×1 カーバイド ロッド がゲームチェンジャーとして登場した。この驚異的なクーラントホールは、その中心を貫く精密にドリル加工されたクーラントホールが特徴で、切削ゾーンに直接クーラントを供給し、より低温で、より高速で、より効率的な加工作業の新時代を切り開きます。
この包括的なガイドでは、1ストレートクーラントホールの超硬ロッドの複雑さを掘り下げ、その設計、利点、用途、そして今日の厳しい製造現場で不可欠なツールとなっている要因を探ります。
1ストレートクーラントホール超硬ロッドとは?
1 ストレートクーラントホール超硬ロッドは、その中心を軸方向に貫通する1つの精密なクーラントホールを持つように設計された特殊な超硬ロッドです。この革新的な設計により、高圧クーラントを切削界面に直接供給することができ、従来のフラッドクーラント方式を上回る多くの利点が得られます。
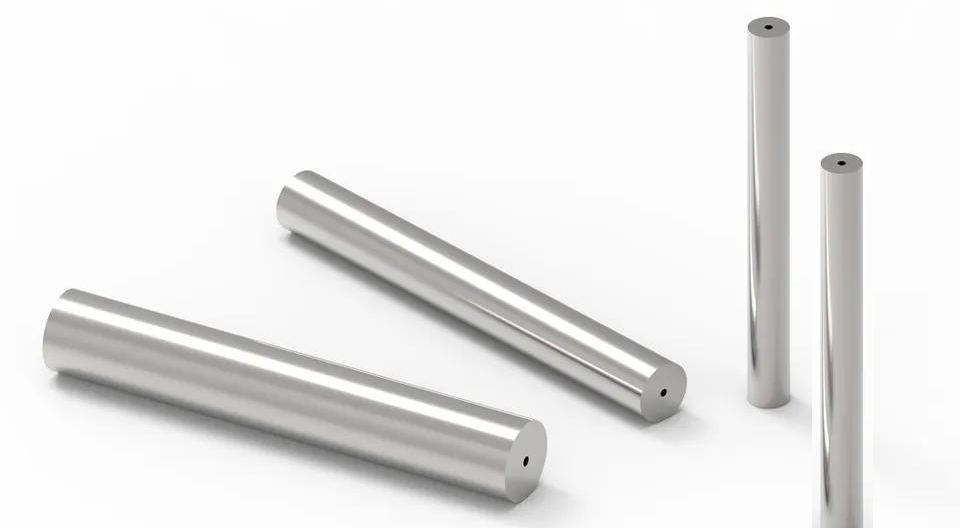
クールを支える科学:クールの仕組み
1ストレートクーラントホールの超硬ロッドの魔法は、加工中の発熱と切り屑排出の課題に対処する能力にあります:
- 狙いを定めたクーラント供給: 内部のクーラントホールは、クーラントが最も必要な場所、つまり切削ゾーンに集中的にクーラントを供給します。この的を絞ったアプローチは、冷却効率を最大化すると同時に、フラッドクーラント方式と比較してクーラント消費量を最小限に抑えます。
- チップ避難の強化: ロッド内を流れる高圧クーラントジェットは、切削領域から切り屑を効果的に洗い流し、切り屑の再切削を防ぎ、仕上げ面精度を向上させ、工具寿命を延ばします。
- 熱影響ゾーンの縮小: 切削ゾーンを低温に保つことで、これらのロッドはワークの熱影響部を最小限に抑え、歪み、反り、冶金的変化のリスクを低減する。
製造と材料に関する考慮事項
1ストレートクーラントホールの超硬ロッドを製造するには、特殊な製造技術と高品質の超硬グレードが必要です:
- 素材の選択: ロッドは通常、K10、K20、または要求の厳しい用途向けの特殊な微小結晶粒グレードなど、高い靭性と耐摩耗性を持つ微粒炭化物グレードから製造されます。
- 精密ドリル: クーラントホールは、放電加工(EDM)やレーザードリルなどの特殊な装置を使って、必要な直径、真直度、表面仕上げを達成するために開けられる。
- 品質管理: クーラント・ホールの完全性、寸法精度、ロッド全体の品質を保証するため、製造工程全体で厳格な品質管理措置が採用されています。
クーラントホール超硬ロッドの分類
1ストレートのクーラントホールの超硬ロッドが広く使用されていますが、特定の加工ニーズに対応するためのバリエーションも存在します:
- クーラントホールの数 2つ、3つ、またはそれ以上のクーラントホールを持つロッドも利用可能で、異なるクーラントフローパターンと切屑排出特性を提供します。
- クーラントホールの形状: クーラントホールの形状とサイズは、特定の用途に合わせてクーラントの流れと圧力分布を最適化するように調整することができます。
- 超硬グレードとコーティング: 超硬材種とコーティングの選択は、加工材料、切削パラメータ、希望する工具寿命によって決まる。
表1:クーラントホール超硬ロッドのバリエーションを垣間見る
特徴 | 説明 |
---|---|
クーラントホールの数 | 1、2、3、またはそれ以上 |
クーラントホール形状 | ストレート、ヘリカル、シェイプ |
超硬グレード | K10、K20、マイクロ・グレインなど。 |
コーティング | TiN、TiAlN、DLCなど。 |
用途クーラントホール超硬ロッドの利点
1 ストレートクーラントホールの超硬ロッドは、様々な加工、特に加工に関わる加工に革命をもたらした:
深穴掘削:
- 航空宇宙部品: 燃料ライン、油圧システム、構造部品用に、チタンやニッケル合金などの航空宇宙材料に深く正確な穴を開ける。
- 金型製作: プラスチック射出成形やダイカスト用の金型に、複雑な冷却溝や深い空洞を作る。
高速加工:
- 自動車産業: エンジンブロック、シリンダーヘッド、トランスミッション部品を高精度で効率的に加工。
- 医療機器製造: 医療用インプラント、手術器具、その他の医療機器用の小さく複雑な部品を製造。
機械加工が困難な材料:
- チタンとニッケル合金: これらのロッドの強化された冷却と切屑排出能力は、これらの高温合金の効率的な加工を可能にする。
- 硬化鋼: 高硬度鋼の加工では、工具の摩耗やワークの損傷を防ぐために、切削ゾーンを低温に保つことが重要です。
超硬棒サプライヤーの比較:市場概要
サプライヤー | 所在地 | 価格帯(1個あたり、概算) | 特産品 |
---|---|---|---|
TRUER | 中国 | $15 – $600 | 特注クーラント 穴あき超硬棒幅広いグレードと形状、競争力のある価格設定 |
サンドビック・コロマント | スウェーデン | $25 – $700 | 高性能切削工具、ツーリングシステム、金属切削におけるグローバルな専門知識 |
ケナメタル | アメリカ | $20 – $650 | 高度な材料科学、要求の厳しい用途向けの金型ソリューション、技術革新への注力 |
京セラ | 日本 | $22 – $680 | 精密工具、セラミック切削工具、品質と信頼性へのこだわり |
ギュリング | ドイツ | $28 – $750 | ドリルおよびフライス工具、深穴加工の専門知識、高精度ソリューション |
表2:超硬ロッド・サプライヤーの状況をナビゲートする
ご注意ください: 価格は概算であり、グレード、寸法、クーラントホールの仕様、数量、市況などの要因によって大きく変動する可能性があります。正確で最新の価格情報については、常にサプライヤーに直接問い合わせることをお勧めします。
利点と限界:バランスの取れた見方
メリット
- 冷却効率の向上: ターゲットクーラント供給は、切削領域での熱蓄積を大幅に低減し、工具寿命、ワーク品質、および全体的な加工効率を改善します。
- チップ避難の改善: 高圧クーラントは、切削領域から切り屑を効果的に除去し、切り屑の再切削を防ぎ、仕上げ面精度を向上させ、工具摩耗を低減します。
- 切削速度と送り速度の向上: 冷却された切削温度と効率的な切り屑排出により、より高い切削速度と送り速度が可能になり、生産性が向上します。
- 工具摩耗の低減: 切削温度の低下と切りくず排出性の向上は、工具寿命の延長につながり、工具コストとダウンタイムを削減します。
制限:
- コストだ: 冷却孔用超硬棒は、冷却孔の穿孔に製造工程が増えるため、一般に超硬ソリッド棒より高価である。
- 目詰まりの可能性: 特に筋状の切りくずが出る材料を加工する場合、クーラントホールが切りくずや破片で詰まることがあります。適切な切りくず処理とクーラント濾過が不可欠です。
- クーラント圧の要件: これらのロッドは通常、効果的なクーラント供給と切屑排出を確保するために、フラッドクーラントシステムよりも高いクーラント圧力を必要とする。
表3:クーラントホール超硬ロッドの長所と短所を比較する
クーラントホール用超硬ロッドのパートナーとしてTRUERを選ぶ理由
TRUERは、高品質のクーラントホールカーバイドロッドの一流プロバイダーとして、以下のような魅力的な組み合わせを提供しています:
- カスタマイズの専門家: 当社は、クーラントホールの直径や形状から超硬合金グレード、コーティング、寸法公差に至るまで、お客様の精密な仕様に合わせたクーラントホール用超硬ロッドソリューションを専門としています。
- 精密製造: 当社の高度な穴あけ能力と厳格な品質管理措置は、冷却孔の完全性と精度を保証し、最適な性能と信頼性を実現します。
- 競争力のある価格設定: 弊社は、品質に妥協することなく、費用対効果の高いソリューションを提供するよう努めており、競争力のある価格設定と、お客様の特定のニーズに応える柔軟な注文数量を提供しています。
- 顧客満足へのコミットメント: 当社の専門チームは、最初のお問い合わせや技術的なご相談から、タイムリーな納品や販売後のサポートに至るまで、お客様の旅を通して卓越したサービスとサポートを提供することをお約束します。
よくある質問クーラントホール超硬ロッドに関するお問い合わせ
1.クーラントホールカーバイドロッドに使用するクーラントの種類は?
水溶性合成クーラントは、潤滑剤と防錆剤が添加されていることが多く、クーラントホールの超硬ロッドで一般的に使用されています。具体的なクーラントの選択は、加工する材料、切削パラメータ、希望する仕上げ面によって異なります。
2.加工中にクーラントホールが詰まらないようにするには?
クーラントホールの目詰まりを防ぐには、高圧クーラントシステムの使用、適切な切り屑処理方法(切り屑ブレーカーなど)の選択、効果的なクーラント濾過が重要です。
3.クーラントホールの超硬ロッドは、荒加工と仕上げ加工の両方に使用できますか?
クーラントホールの超硬ロッドは、深穴加工や高速加工などの要求の厳しい用途に優れていますが、特定の工具形状と切削パラメータに応じて、荒加工と仕上げ加工の両方に使用できます。
4.クーラントホールの詰まりの兆候と対処法は?
詰まりの兆候としては、クーラント流量の減少、切削抵抗の増加、表面仕上げの悪化などがある。詰まりが発生した場合は、工具を注意深く取り外し、圧縮空気、ワイヤーブラシ、または専用のクリーニングツールを使用してクーラントホールを清掃してください。
5.超硬ソリッドロッドと比較して、クーラントホール超硬ロッドの一般的な寿命はどのくらいですか?
様々な要因によりますが、クーラントホールの超硬ロッドは、冷却と切り屑排出が強化されているため、同等の用途ではソリッド超硬ロッドよりも長寿命であることがよくあります。これは、工具コストの削減と生産性の向上につながります。